- お役立ち記事
- Fundamentals of powder and points to improve fluidity and filling properties
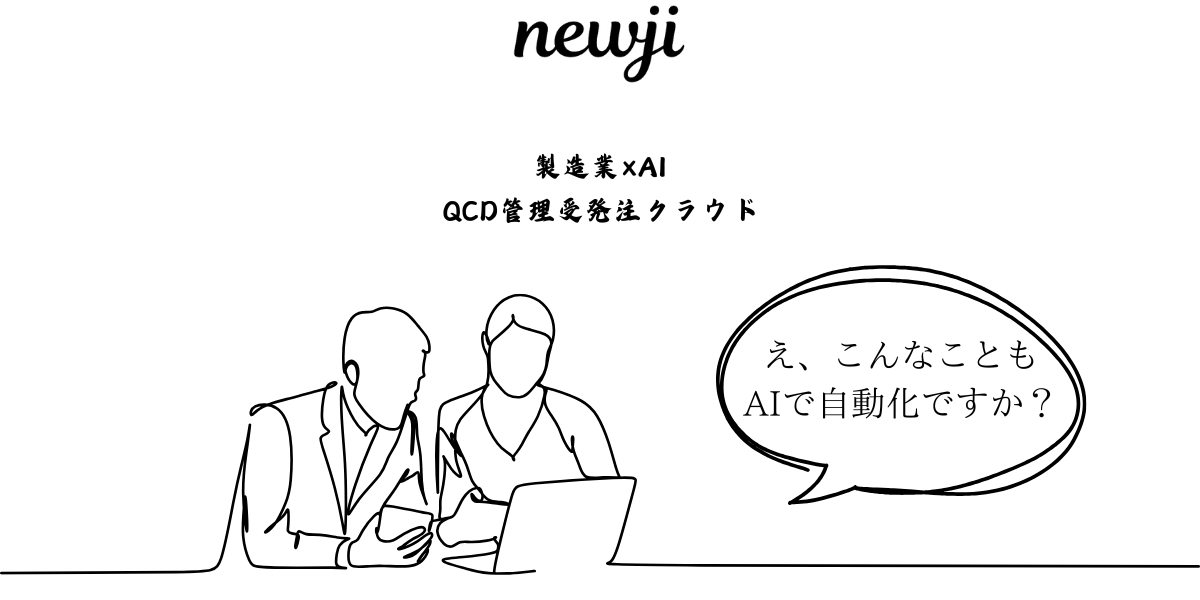
Fundamentals of powder and points to improve fluidity and filling properties
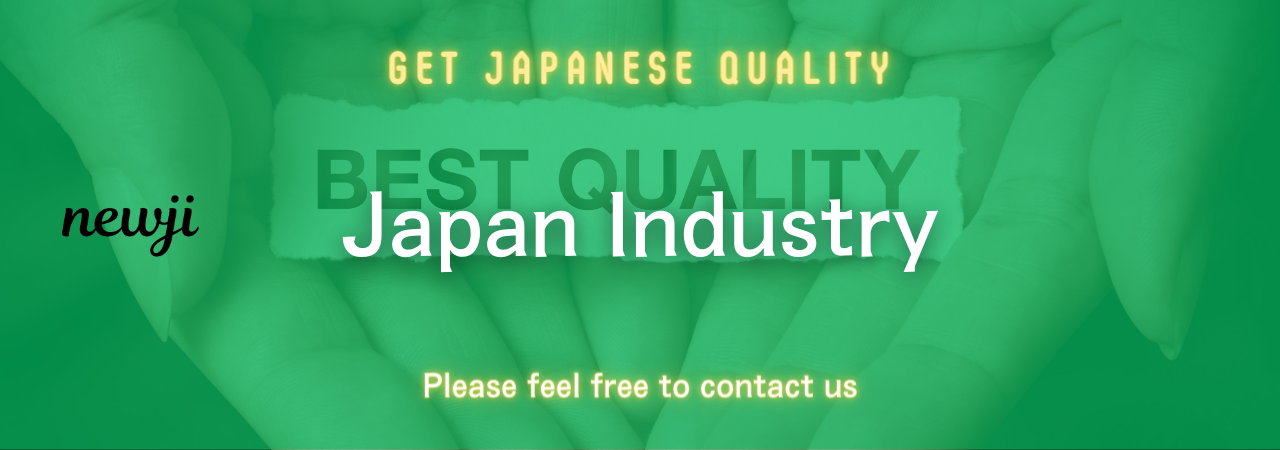
目次
Understanding the Basics of Powder
Powder, seemingly simple in appearance, plays a crucial role in various industries, including pharmaceuticals, food production, and manufacturing.
Understanding the fundamentals of powder is essential for improving its fluidity and filling properties, which can significantly affect the efficiency and quality of a final product.
In essence, powder consists of fine particles that exhibit both the properties of solids and fluids.
The characteristics of powder are largely determined by factors such as particle size, shape, and distribution.
When looking at powders from a manufacturing perspective, one must consider their behavior during transportation, mixing, and packing.
The two major characteristics that are of primary concern are fluidity and filling properties.
Fluidity refers to the ease with which powder particles move and slide past one another.
Improving fluidity can enhance processes like mixing and filling, leading to better control and precision.
Filling properties are related to how effectively powder can occupy a given space.
Understanding these properties ensures that the product being produced is consistent in terms of volume and weight.
Factors Affecting Powder Fluidity
Several factors influence the fluidity of powder.
One is the size of the particles.
Generally, smaller particles tend to have lower fluidity because they have a larger surface area relative to their volume, which leads to increased friction between particles.
Particle shape also plays a vital role.
Irregularly shaped particles can interlock, reducing fluidity, whereas smooth, spherical particles can move more freely.
Moisture content is another critical factor.
Excess moisture can cause particles to clump together, negatively affecting fluidity.
Conversely, a controlled amount of moisture can sometimes enhance fluidity by reducing static electricity and friction.
Finally, the interaction between particles must be considered.
This includes forces such as van der Waals forces and electrostatic charges, both of which can impede fluid movement.
Improving Powder Fluidity
To enhance powder fluidity, start by selecting or adjusting particle size and shape.
Using granulation or milling techniques can help achieve a more desirable particle size distribution.
Additives are often used to improve fluidity.
Anti-caking agents, for example, can prevent clumping, while lubricants can decrease friction between particles.
Controlling moisture content is essential.
Implementing drying techniques or moisture control systems can ensure that the powder remains in an optimal state for fluidity.
Electrostatic charges can also be managed.
In some cases, using ionizers or grounding equipment can reduce unwanted interactions that hinder fluidity.
Understanding Filling Properties
Filling properties of powder are just as critical as fluidity, as they determine how well a powder can occupy a given space within a container or mold.
One important aspect of filling is the bulk density, which indicates how much space a given mass of powder occupies.
Loose bulk density refers to the space occupied when the powder is poured freely, while tapped bulk density is measured after the powder has been compacted, such as through tapping.
Another factor is compressibility, which refers to the ability of powder to decrease in volume under pressure.
Powders with poor compressibility may lead to complications during the packing process.
The flowability of powder impacts its filling efficiency.
Better flowability ensures consistent and uniform filling, which is crucial for products that require precise dosages or tight packaging.
Improving Filling Properties
To improve filling properties, it is advisable to first evaluate and control the bulk density of the powder.
This can involve modifying the particle size and shape to achieve a more uniform distribution.
Using compaction aids or binder materials during the powder processing can enhance compressibility.
These materials help hold the powder together, allowing it to fill spaces more effectively without gaps or inconsistencies.
Optimizing the flowability also improves fill efficiency.
Adjusting the formulation by incorporating additives designed to boost flow can prevent issues during packing.
Regular testing and monitoring of filling properties during production are pivotal.
Implementing quality control measures will ensure that any variations in filling properties are detected and rectified promptly.
Conclusion
The fundamentals of powder, including understanding its fluidity and filling properties, are vital for optimizing manufacturing processes and ensuring product quality.
By considering particle size, shape, moisture content, and interparticle interactions, businesses can improve these properties to their advantage.
Enhancing fluidity and filling properties through strategic adjustments and the use of additives can lead to significant benefits in production efficiency and final product consistency.
Continual monitoring and evaluation of powder characteristics will enable ongoing improvements and maintain high standards within any industry that relies on powders.
資料ダウンロード
QCD調達購買管理クラウド「newji」は、調達購買部門で必要なQCD管理全てを備えた、現場特化型兼クラウド型の今世紀最高の購買管理システムとなります。
ユーザー登録
調達購買業務の効率化だけでなく、システムを導入することで、コスト削減や製品・資材のステータス可視化のほか、属人化していた購買情報の共有化による内部不正防止や統制にも役立ちます。
NEWJI DX
製造業に特化したデジタルトランスフォーメーション(DX)の実現を目指す請負開発型のコンサルティングサービスです。AI、iPaaS、および先端の技術を駆使して、製造プロセスの効率化、業務効率化、チームワーク強化、コスト削減、品質向上を実現します。このサービスは、製造業の課題を深く理解し、それに対する最適なデジタルソリューションを提供することで、企業が持続的な成長とイノベーションを達成できるようサポートします。
オンライン講座
製造業、主に購買・調達部門にお勤めの方々に向けた情報を配信しております。
新任の方やベテランの方、管理職を対象とした幅広いコンテンツをご用意しております。
お問い合わせ
コストダウンが利益に直結する術だと理解していても、なかなか前に進めることができない状況。そんな時は、newjiのコストダウン自動化機能で大きく利益貢献しよう!
(Β版非公開)