- お役立ち記事
- Points of on-site problem solving and quality assurance in the Toyota method
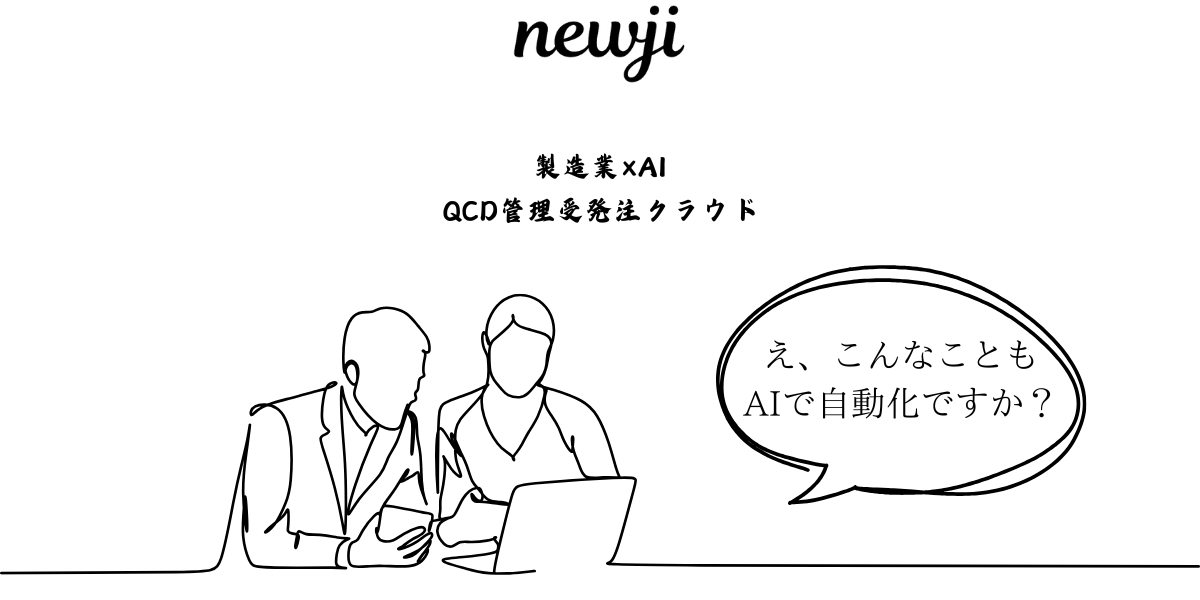
Points of on-site problem solving and quality assurance in the Toyota method
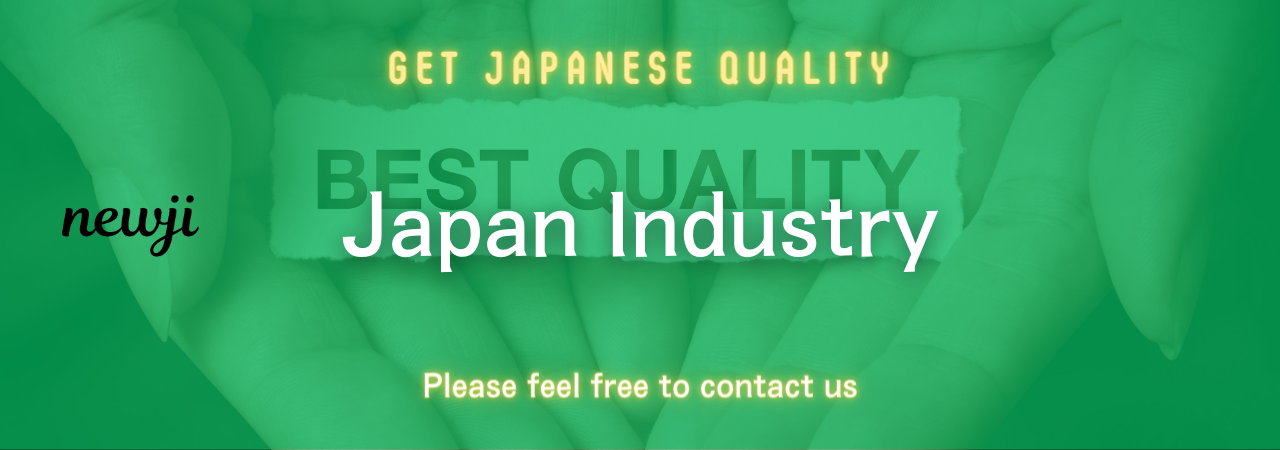
目次
Understanding the Toyota Production System
The Toyota Production System (TPS) is renowned worldwide for its efficiency and effectiveness in manufacturing.
This system focuses on eliminating waste, improving processes, and ensuring quality assurance.
In the TPS, problem-solving is not just an activity, but a core philosophy embedded into every process.
Through continuous improvement, Toyota aims to produce high-quality products consistently.
The Role of On-Site Problem Solving
The heart of the Toyota Production System lies in its approach to on-site problem solving.
Often referred to as “Genchi Genbutsu” or “go and see,” it emphasizes the importance of visiting the actual place where work is done to understand the problem thoroughly.
By observing the reality of the situation, employees can gather accurate data, understand the problem’s context, and propose realistic solutions.
On-site problem-solving is not about imposing quick fixes.
Instead, it focuses on uncovering root causes and eliminating them to prevent recurrence.
This method promotes a culture where workers are encouraged to voice issues and contribute insights for improving processes.
The Five Whys Technique
One of the key tools used within the Toyota method for problem-solving is the “Five Whys” technique.
This involves asking “why” repeatedly to drill down to the root cause of a problem.
The simplicity of this technique allows teams to cut through complicated layers of symptoms and pinpoint the fundamental issue that needs addressing.
By systematically questioning each layer, teams can develop long-term solutions rather than stopgap measures.
For instance, if a machine fails, the process might look like this:
1. Why did the machine stop? – It overheated.
2. Why did it overheat? – The cooling system malfunctioned.
3. Why did the cooling system malfunction? – The coolant was leaking.
4. Why was the coolant leaking? – There was a crack in the hose.
5. Why was there a crack in the hose? – The hose was not maintained properly.
Addressing the root cause, in this case, would involve establishing a regular maintenance schedule rather than just fixing the hose.
Quality Assurance in the Toyota Method
Quality assurance in Toyota’s approach is an ongoing commitment rather than a one-time task.
The principle of Jidoka, or automation with a human touch, ensures that quality is built into the manufacturing process.
Machines are designed to detect anomalies and halt production automatically, allowing operators to address issues immediately.
By stopping the production line when a defect is detected, Toyota minimizes waste and prevents further defects from being produced.
This is a proactive approach that ensures the integrity of the entire manufacturing process.
Standard Work and Continuous Improvement
Standard work is another cornerstone of quality assurance in the Toyota method.
It ensures that each task is performed uniformly and consistently, which reduces variations that could lead to quality issues.
This standardization not only enhances quality but also improves efficiency, as every worker knows exactly what is expected of them.
Moreover, Toyota encourages Kaizen, or continuous improvement, at all levels of the organization.
Employees are driven to consistently look for ways to enhance their work processes and eliminate waste.
Through small, incremental changes, Toyota can adapt rapidly to changes and maintain high quality.
Empowering Employees for Better Quality
Empowerment forms the backbone of Toyota’s quality assurance strategy.
Workers are trained to take ownership of their processes and have the authority to stop the production line if they spot defects.
This responsibility creates a sense of accountability and ownership, leading to a more motivated workforce committed to quality outcomes.
Furthermore, Toyota invests heavily in training and development, ensuring that all employees possess the skills needed to identify and solve problems effectively.
This investment in human resources translates to a highly skilled workforce capable of maintaining high quality standards.
The Long-Term Benefits of the Toyota Method
Implementing on-site problem-solving and rigorous quality assurance has numerous long-term benefits.
Organizations that adopt Toyota’s methodologies can expect improved efficiency, reduced waste, and higher product quality.
These principles foster a culture of continuous improvement, which is integral to staying competitive in today’s fast-paced market.
The Toyota method emphasizes sustainability, with a focus on long-term growth rather than short-term gains.
By solving problems at their root and ensuring consistent processes, companies can build a reputation for delivering defect-free products that meet customer expectations.
Adapting the Toyota Method to Other Industries
The principles of the Toyota Production System, while developed in manufacturing, are applicable across various industries.
From healthcare to information technology, these practices can be tailored to suit different operational needs.
By integrating problem-solving and quality assurance into their operations, organizations in diverse fields can enhance their performance and deliver superior results.
In conclusion, the Toyota method of on-site problem-solving and quality assurance offers a blueprint for operational excellence.
By focusing on the root causes of problems and ensuring adherence to standard work, businesses can achieve sustainable success.
Embracing these principles can lead to a highly efficient, motivated workforce capable of producing high-quality outcomes consistently.
資料ダウンロード
QCD調達購買管理クラウド「newji」は、調達購買部門で必要なQCD管理全てを備えた、現場特化型兼クラウド型の今世紀最高の購買管理システムとなります。
ユーザー登録
調達購買業務の効率化だけでなく、システムを導入することで、コスト削減や製品・資材のステータス可視化のほか、属人化していた購買情報の共有化による内部不正防止や統制にも役立ちます。
NEWJI DX
製造業に特化したデジタルトランスフォーメーション(DX)の実現を目指す請負開発型のコンサルティングサービスです。AI、iPaaS、および先端の技術を駆使して、製造プロセスの効率化、業務効率化、チームワーク強化、コスト削減、品質向上を実現します。このサービスは、製造業の課題を深く理解し、それに対する最適なデジタルソリューションを提供することで、企業が持続的な成長とイノベーションを達成できるようサポートします。
オンライン講座
製造業、主に購買・調達部門にお勤めの方々に向けた情報を配信しております。
新任の方やベテランの方、管理職を対象とした幅広いコンテンツをご用意しております。
お問い合わせ
コストダウンが利益に直結する術だと理解していても、なかなか前に進めることができない状況。そんな時は、newjiのコストダウン自動化機能で大きく利益貢献しよう!
(Β版非公開)