- お役立ち記事
- Efficient data collection of FA system using PLC and application to IoT system
月間77,185名の
製造業ご担当者様が閲覧しています*
*2025年2月28日現在のGoogle Analyticsのデータより
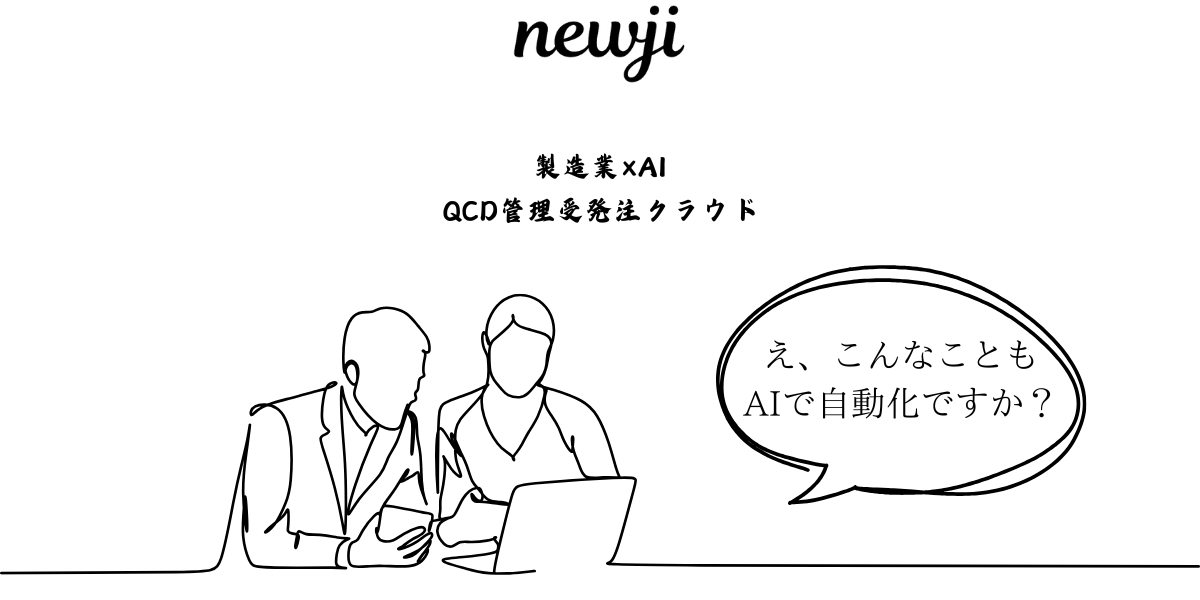
Efficient data collection of FA system using PLC and application to IoT system
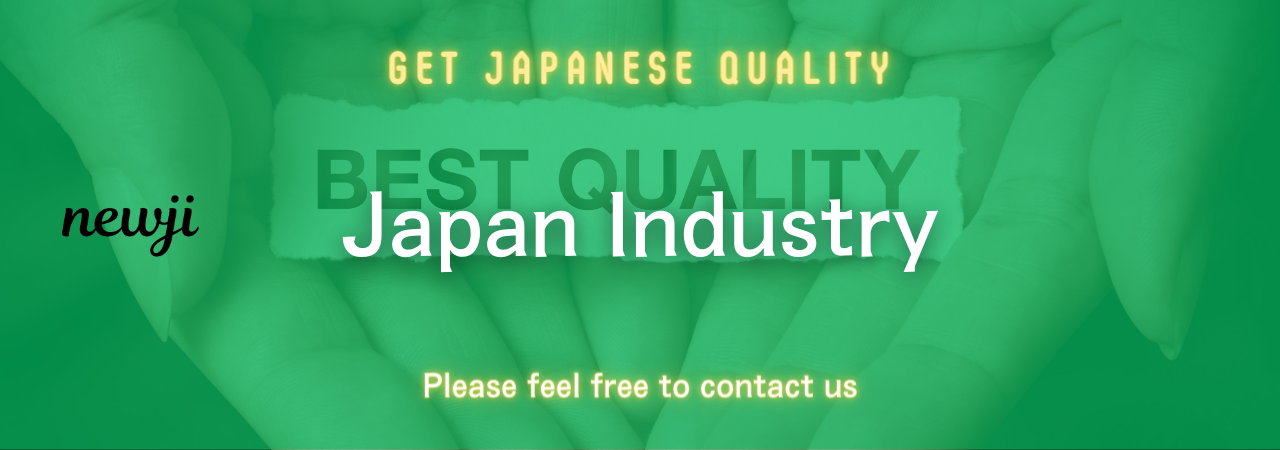
目次
Understanding PLCs in FA Systems
Programmable Logic Controllers (PLCs) are pivotal components in modern Factory Automation (FA) systems.
These reliable and flexible devices are designed to control complex industrial processes and machinery.
They are integral to operational efficiency, minimizing errors, and ensuring consistent production quality.
PLCs operate by using a programmable memory to store instructions and execute specific functions like timing, counting, and data processing.
They are highly adaptable to various tasks and industries, providing the control logic for everything from assembly lines to robotics.
In an FA system, PLCs collect real-time data from sensors and actuators, process this data, and make decisions based on predefined parameters.
This automation streamlines processes and effectively minimizes human intervention, reducing the likelihood of errors while improving safety and productivity.
The Role of Data Collection in FA Systems
Data collection is crucial in FA systems as it provides insight into system performance, machine health, and production efficiency.
Analyzing this data allows factory managers to make informed decisions, optimize processes, and plan maintenance more effectively.
Local data collection via PLCs is efficient and reliable, facilitating real-time monitoring and control.
These controllers can be connected to a wide range of sensors that measure variables such as temperature, pressure, and speed.
By continuously collecting data these convening devices can detect anomalies or deviations from normal patterns, ensuring timely intervention to prevent downtime or damage.
Furthermore, by logging historical data, PLCs help track performance trends over time.
This enables predictive maintenance planning, thereby ensuring machinery is serviced only when necessary, rather than at scheduled intervals, which might not align with actual wear and tear.
Integrating FA Systems with IoT
The Internet of Things (IoT) offers an expansive platform that connects machines and systems to the internet, allowing them to exchange data freely.
This connectivity transforms traditional FA systems by facilitating remote monitoring, advanced analytics, and cross-device communication.
Integrating IoT with PLC-controlled FA systems involves the digitalization of machine data to enable higher-level insights.
This transition enhances factory operations by fostering more intelligent, data-driven decision-making processes.
An IoT-enabled FA system utilizes sensors that gather extensive data, which is then transmitted via IoT networks for further analysis.
IoT platforms can process large data volumes, providing real-time insights and actionable intelligence to stakeholders both within and outside the production facility.
The data collected from these IoT-enabled devices can be used to optimize production lines, reduce energy consumption, and improve equipment utilization.
By leveraging IoT, factories can transition towards smarter manufacturing processes, enhancing overall efficiency and adaptability.
Benefits of Integrating IoT with FA Systems
The integration of IoT technologies with FA systems offers many advantages, transforming traditional manufacturing environments into smart factories.
The key benefits include:
– **Enhanced Data Quality and Accessibility**: IoT platforms enable the seamless management and accessibility of vast datasets.
Decision-makers can access precise, real-time data from any location, facilitating quick and informed decisions.
– **Predictive Maintenance**: IoT integration helps in implementing predictive maintenance strategies, allowing for the early identification of potential machinery failures.
This reduces downtime and maintenance costs while extending the life cycle of equipment.
– **Operational Efficiency**: By automating data collection and analysis, IoT can boost operational efficiency.
Automated processes lower labor costs, while optimal equipment performance reduces waste and energy usage.
– **Improved Product Quality**: Real-time monitoring and adjustments ensure that products are manufactured to the highest quality standards.
This leads to better customer satisfaction and competitive advantage in the market.
Implementing IoT Solutions in FA Systems
Implementing IoT solutions within FA systems involves several steps to ensure a cohesive, secure, and efficient integration.
Here are some vital considerations:
Identify Integration Points
Analyzing the existing FA system architecture helps identify key integration points where IoT technologies can be applied.
This includes evaluating machines, PLCs, sensors, and networking infrastructure to ensure compatibility.
Select Appropriate IoT Technology
Selecting the right IoT platform and technologies is crucial for a successful integration.
Factors such as scalability, security, cost, and ease of use should be considered when choosing the platform.
Ensuring that the IoT technology can handle the data processing requirements and provide compatible connectivity solutions is essential.
Data Security and Privacy
With increased data flow between devices and networks, ensuring data security is paramount.
Implementing robust security measures such as encryption, authentication protocols, and regular security audits helps prevent unauthorized access and data breaches.
Employee Training and Change Management
As technology evolves, it’s essential to equip the workforce with the necessary skills to operate and manage IoT-integrated systems effectively.
Technical training and change management strategies are crucial to enabling employees to adapt to new technologies and processes.
Conclusion
The integration of PLCs in FA systems with IoT technologies marks a significant advancement in manufacturing automation.
This powerful combination enhances data collection, providing deeper insights, efficient monitoring, and optimized production processes.
By leveraging these innovations, businesses can achieve higher levels of efficiency, competitiveness, and sustainability in their operations.
As the manufacturing sector continues to evolve, embracing IoT solutions will be critical to maintaining a cutting-edge advantage, ensuring factories remain adaptable, resilient, and profitable in the digital age.
資料ダウンロード
QCD管理受発注クラウド「newji」は、受発注部門で必要なQCD管理全てを備えた、現場特化型兼クラウド型の今世紀最高の受発注管理システムとなります。
ユーザー登録
受発注業務の効率化だけでなく、システムを導入することで、コスト削減や製品・資材のステータス可視化のほか、属人化していた受発注情報の共有化による内部不正防止や統制にも役立ちます。
NEWJI DX
製造業に特化したデジタルトランスフォーメーション(DX)の実現を目指す請負開発型のコンサルティングサービスです。AI、iPaaS、および先端の技術を駆使して、製造プロセスの効率化、業務効率化、チームワーク強化、コスト削減、品質向上を実現します。このサービスは、製造業の課題を深く理解し、それに対する最適なデジタルソリューションを提供することで、企業が持続的な成長とイノベーションを達成できるようサポートします。
製造業ニュース解説
製造業、主に購買・調達部門にお勤めの方々に向けた情報を配信しております。
新任の方やベテランの方、管理職を対象とした幅広いコンテンツをご用意しております。
お問い合わせ
コストダウンが利益に直結する術だと理解していても、なかなか前に進めることができない状況。そんな時は、newjiのコストダウン自動化機能で大きく利益貢献しよう!
(β版非公開)