- お役立ち記事
- Fundamentals of PID control, limiting pole placement method, and application to digital control
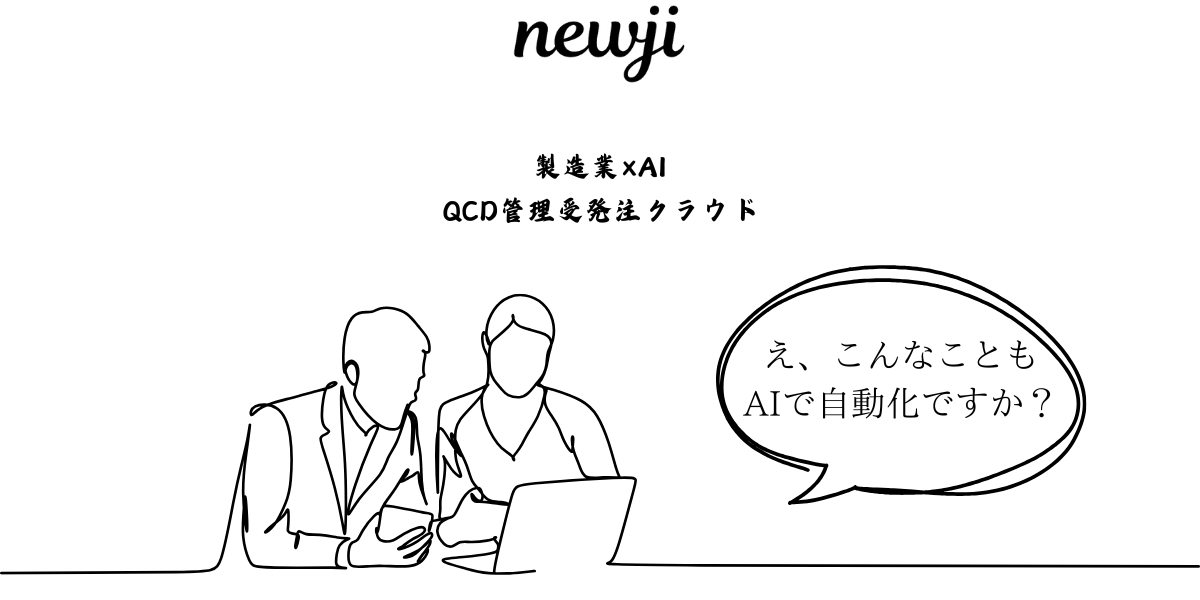
Fundamentals of PID control, limiting pole placement method, and application to digital control
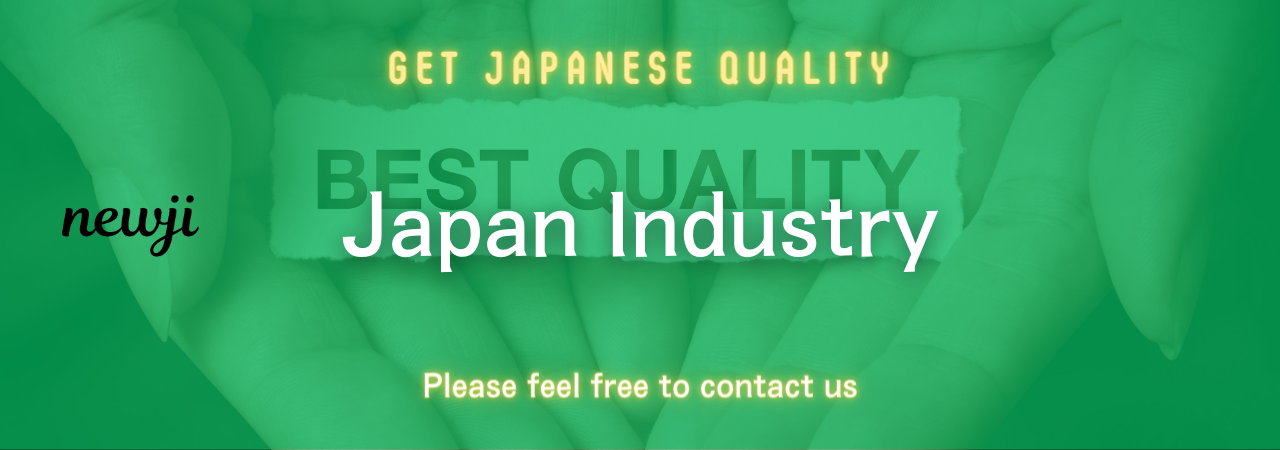
目次
Understanding the Basics of PID Control
PID control stands for Proportional, Integral, and Derivative control, which are the three main components that constitute this control system.
These controllers are fundamental in industrial control systems, enabling machines and processes to maintain desired levels of output.
Understanding how these components work together is essential for mastering control system implementations.
The **Proportional** component of the PID control is responsible for providing a control output that is directly proportional to the error signal.
The error signal is simply the difference between the desired setpoint and the actual process variable.
A high proportional gain results in a larger change in the output for a given error.
However, excessive proportional gain can lead to system instability.
The **Integral** component focuses on accumulating the error over time.
This function corrects any offset that the proportional component might leave unaddressed.
By integrating over the past errors, the controller adjusts the system to bring the steady-state error to zero.
This feature is especially useful in eliminating persistent, small errors that cannot be corrected using only the proportional control.
The **Derivative** component predicts future behavior based on the rate of error change.
This part of the controller provides a dampening effect, reducing overshoot and oscillation.
By anticipating future errors, it works to stabilize the system more swiftly and accurately.
Exploring Limiting Pole Placement Method
The pole placement method is a technique used in control theory for designing controllers that place the system poles in desired locations in the s-plane.
By positioning these poles strategically, one can directly influence the system’s response characteristics.
**Pole placement** is primarily used to achieve specific performance metrics, such as settling time, rise time, and damping ratio.
This is achieved by modifying the controller parameters to move the system’s poles to these predefined locations.
The **limiting pole placement method** extends pole placement by considering constraints on the control system.
These constraints might be due to physical limitations, safety regulations, or efficiency measures.
This method ensures that the designed control system not only meets performance requirements but also adheres to these imposed restrictions.
One of the crucial aspects of limiting pole placement is the balance between performance and robustness.
While it allows for precise control tuning, it also requires careful consideration of how close poles are placed to the stability boundary, as poles near this boundary might make the system susceptible to disturbances and noise.
Applying PID Control to Digital Control Systems
With the advent of digital technology, the application of PID control systems has evolved significantly.
Unlike traditional analog systems, digital control involves discretizing the continuous PID controller equations to work within a digital framework.
Transforming a PID controller into its **digital counterpart** requires discretization techniques, such as the backward difference, forward difference, or trapezoidal method.
Choosing the right discretization method can influence the precision and stability of the digital control system.
Once the PID controller is implemented digitally, it can be integrated into computer-based control systems.
This integration leverages the computing power and flexibility of modern computers, allowing for more sophisticated control algorithms and smoother operation.
Digital PID controllers are frequently employed in areas where rapid changes in system dynamics need to be managed efficiently, such as in automotive systems, robotics, and telecommunications.
Through digital implementation, these controllers gain added benefits like ease of tuning, adaptability, and enhanced data processing capabilities.
Challenges in Digital PID Control
Despite the advantages, digital PID control faces several challenges.
Sampling rates are critical in the accurate conversion of continuous signals to digital.
Inadequate sampling rates can lead to aliasing, where high-frequency components of the signal interfere with the low-frequency components, degrading the control system’s performance.
Moreover, computational delays present another challenge.
Since digital control systems are often realized in software, latency introduced by computations can affect the responsiveness of the PID controller.
Careful synchronization and optimization of control algorithms are necessary to minimize these delays.
Finally, digitization can introduce **quantization errors.**
These are errors introduced by mapping a large set of input values to a smaller set of digital values, potentially leading to a loss in precision.
Sophisticated methods, such as higher bit-resolution and advanced filtering techniques, are employed to mitigate these errors.
The Future of PID in Control Systems
As technology continues to advance, the role of PID controllers in control systems is expected to evolve further.
The integration of **machine learning** and artificial intelligence with PID control algorithms is an exciting development.
These methodologies can autonomously tune PID parameters to optimize system performance under varying conditions.
Moreover, the incorporation of **IoT capabilities** is enhancing the reach and application of PID control systems.
With interconnected devices, PID controllers can now tap into extensive data, providing insights that were not possible in older systems.
In essence, while PID control forms the backbone of many control systems, ongoing advancements ensure that these controllers remain robust, adaptable, and ready to meet the demands of modern applications.
資料ダウンロード
QCD調達購買管理クラウド「newji」は、調達購買部門で必要なQCD管理全てを備えた、現場特化型兼クラウド型の今世紀最高の購買管理システムとなります。
ユーザー登録
調達購買業務の効率化だけでなく、システムを導入することで、コスト削減や製品・資材のステータス可視化のほか、属人化していた購買情報の共有化による内部不正防止や統制にも役立ちます。
NEWJI DX
製造業に特化したデジタルトランスフォーメーション(DX)の実現を目指す請負開発型のコンサルティングサービスです。AI、iPaaS、および先端の技術を駆使して、製造プロセスの効率化、業務効率化、チームワーク強化、コスト削減、品質向上を実現します。このサービスは、製造業の課題を深く理解し、それに対する最適なデジタルソリューションを提供することで、企業が持続的な成長とイノベーションを達成できるようサポートします。
オンライン講座
製造業、主に購買・調達部門にお勤めの方々に向けた情報を配信しております。
新任の方やベテランの方、管理職を対象とした幅広いコンテンツをご用意しております。
お問い合わせ
コストダウンが利益に直結する術だと理解していても、なかなか前に進めることができない状況。そんな時は、newjiのコストダウン自動化機能で大きく利益貢献しよう!
(Β版非公開)