- お役立ち記事
- Key points of machining technology for large ring machining for the aerospace industry
月間77,185名の
製造業ご担当者様が閲覧しています*
*2025年2月28日現在のGoogle Analyticsのデータより
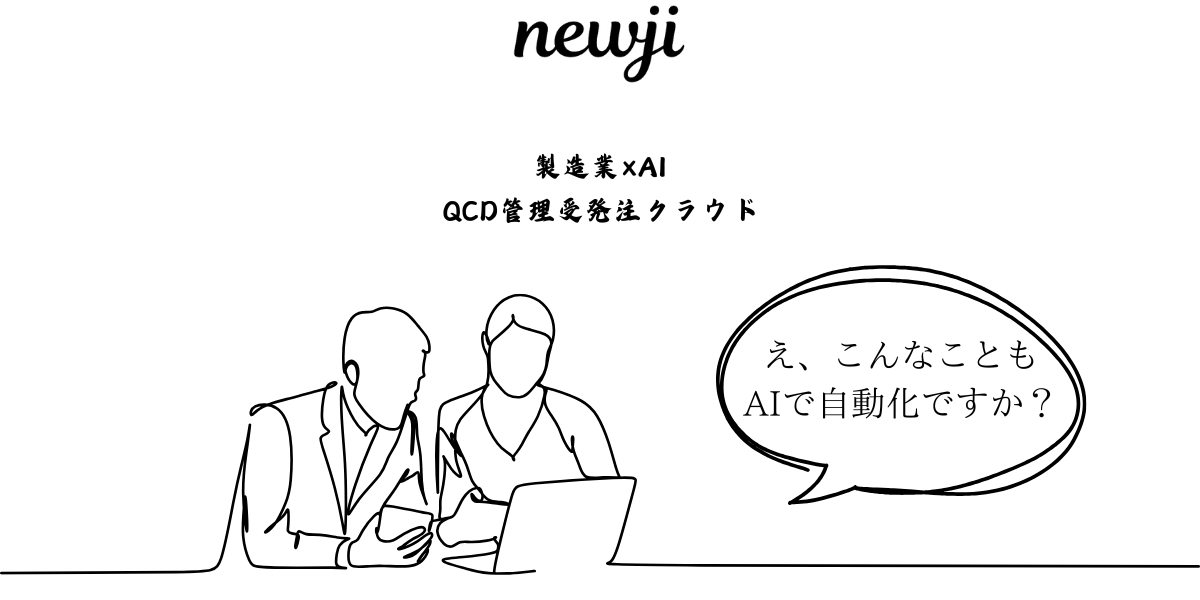
Key points of machining technology for large ring machining for the aerospace industry
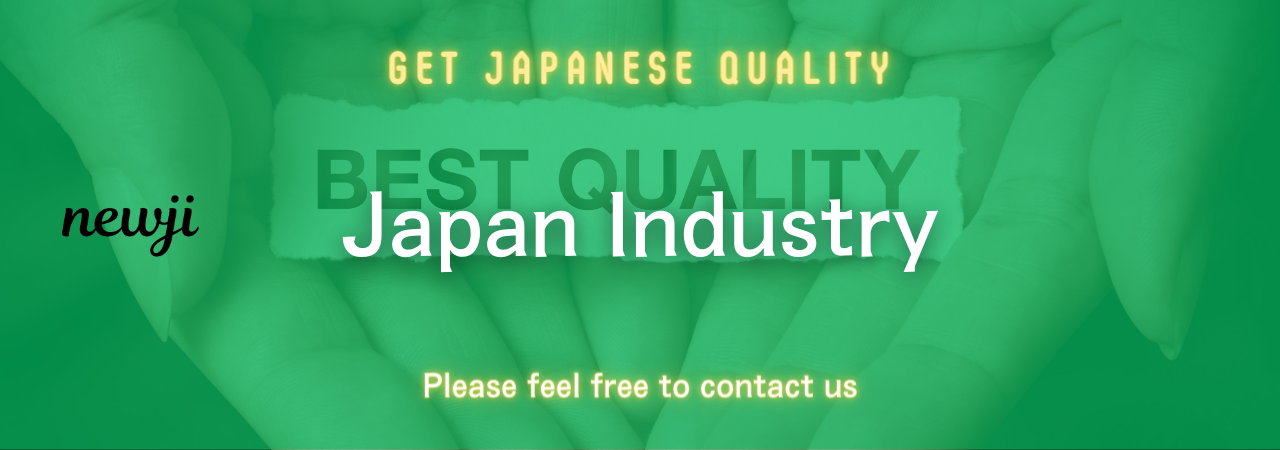
目次
Introduction to Machining Technology in Aerospace
The aerospace industry is a cornerstone of modern technological advancement.
Within this sector, machining technology plays a pivotal role, particularly when it comes to manufacturing large rings.
These components are integral to the structure and efficiency of various aerospace machines, from aircraft engines to satellite systems.
Machining these large rings requires precision, expertise, and advanced technology to meet the stringent demands for performance and safety.
Understanding Large Ring Machining
Large ring machining involves crafting circular components with precise specifications and tolerances.
These rings must withstand extreme conditions, such as high temperatures and pressures, which are frequently encountered in aerospace applications.
These demanding conditions necessitate the use of state-of-the-art materials and machining techniques.
The primary challenge in large ring machining is maintaining accuracy while handling materials like titanium, stainless steel, and aluminum alloys.
These metals provide the strength and durability necessary for aerospace applications, but they also pose machining challenges due to their hardness and toughness.
Materials Used in Large Ring Machining
Material selection is crucial in aerospace manufacturing due to the complex requirements for durability, weight, and thermal properties.
Each material presents unique challenges and benefits:
– **Titanium** is favored for its strength-to-weight ratio and corrosion resistance.
However, its hardness requires advanced cutting tools and techniques.
– **Stainless steel** is known for its toughness and resistance to wear and corrosion, making it suitable for high-stress environments.
– **Aluminum alloys** are lightweight and easy to machine, but they must be carefully selected and treated to meet the specific mechanical demands.
Advanced Techniques in Large Ring Machining
With technological advancements, several techniques have emerged to enhance the manufacturing process of large rings for aerospace applications:
Computer Numerical Control (CNC) Machining
CNC machining has revolutionized precision engineering with its ability to automatically control machine tools through pre-programmed software.
This level of control ensures that each large ring adheres to rigid specifications, helping maintain consistency and quality throughout production.
CNC machines can produce complex geometries with minimal human intervention, reducing errors and speeding up the manufacturing process.
5-Axis Machining
5-axis machining allows for greater flexibility by moving the workpiece along five different axes.
This capability is particularly beneficial for crafting complex components like large rings, where intricate designs and deep channels are necessary.
The increased range of motion in 5-axis machining provides more precision and reduces the need for multiple setups, conserving time and resources.
Electrochemical Machining (ECM)
ECM is a non-conventional machining process that removes metal by an electrochemical reaction.
It’s used for hard-to-machine materials or precise and complex shapes that are difficult to achieve through traditional machining methods.
In ECM, there is no mechanical contact between the tool and the workpiece, which eliminates tool wear and allows for excellent surface finishes and dimensional accuracy.
Challenges in Large Ring Machining for Aerospace
Machining large rings for the aerospace industry involves a multitude of challenges, each of which must be addressed with precision and expertise:
Maintaining Tolerances
One of the most significant challenges in machining large rings is maintaining tight tolerances.
Even small deviations can result in performance issues or failures, which is unacceptable given the high stakes involved in aerospace applications.
Advanced measuring tools and real-time monitoring systems are employed to ensure that every piece meets the predetermined standards.
Material Challenges
As previously mentioned, working with aerospace-grade materials such as titanium and stainless steel can be tough.
These materials require specific cutting techniques and equipment to avoid deformation or damage, increasing the complexity and cost of the machining process.
High Cost and Time Requirements
The development and production of large rings involve significant investment in both time and resources.
From procuring the right raw materials to employing skilled workers and maintaining high-tech machinery, the entire process is costly.
Furthermore, any errors or inefficiencies can lead to increased expenditure and extended deadlines.
Future of Large Ring Machining in Aerospace
The future of large ring machining in aerospace is promising, fueled by technology and innovation.
As the demand for more efficient and lighter components grows, so does the need for advanced machining technologies.
Automation and Artificial Intelligence (AI)
Automation is increasingly integrated into manufacturing processes, including large ring machining.
AI and machine learning algorithms can optimize machining operations, improve accuracy, and predict maintenance needs before failures occur, thus reducing downtime.
Innovative Materials
Research continues into developing new materials that meet the elusive balance of strength, weight, and machinability.
Future advancements may see composite materials that provide even better performance than current titanium and aluminum options.
Sustainability Considerations
With a heightened focus on sustainability, future machining processes will prioritize minimizing waste and energy consumption.
This shift will not only enhance the environmental footprint of aerospace manufacturing but also drive cost efficiencies.
Conclusion
Machining technology for large rings in the aerospace industry is a complex but essential component of modern engineering.
It requires an intricate balance of advanced technologies, robust materials, and meticulous processes to meet the industry’s rigorous demands.
As technology continues to evolve, we can anticipate greater efficiency, innovation, and sustainability in the field of large ring machining.
The ongoing advancements in this domain will continue to fuel the growth and success of the aerospace industry, leading to safer and more efficient aerospace machines.
資料ダウンロード
QCD管理受発注クラウド「newji」は、受発注部門で必要なQCD管理全てを備えた、現場特化型兼クラウド型の今世紀最高の受発注管理システムとなります。
ユーザー登録
受発注業務の効率化だけでなく、システムを導入することで、コスト削減や製品・資材のステータス可視化のほか、属人化していた受発注情報の共有化による内部不正防止や統制にも役立ちます。
NEWJI DX
製造業に特化したデジタルトランスフォーメーション(DX)の実現を目指す請負開発型のコンサルティングサービスです。AI、iPaaS、および先端の技術を駆使して、製造プロセスの効率化、業務効率化、チームワーク強化、コスト削減、品質向上を実現します。このサービスは、製造業の課題を深く理解し、それに対する最適なデジタルソリューションを提供することで、企業が持続的な成長とイノベーションを達成できるようサポートします。
製造業ニュース解説
製造業、主に購買・調達部門にお勤めの方々に向けた情報を配信しております。
新任の方やベテランの方、管理職を対象とした幅広いコンテンツをご用意しております。
お問い合わせ
コストダウンが利益に直結する術だと理解していても、なかなか前に進めることができない状況。そんな時は、newjiのコストダウン自動化機能で大きく利益貢献しよう!
(β版非公開)