- お役立ち記事
- Revolutionizing Japanese Manufacturing: The Role of Wet Etching Process OEMs in Precision Engineering
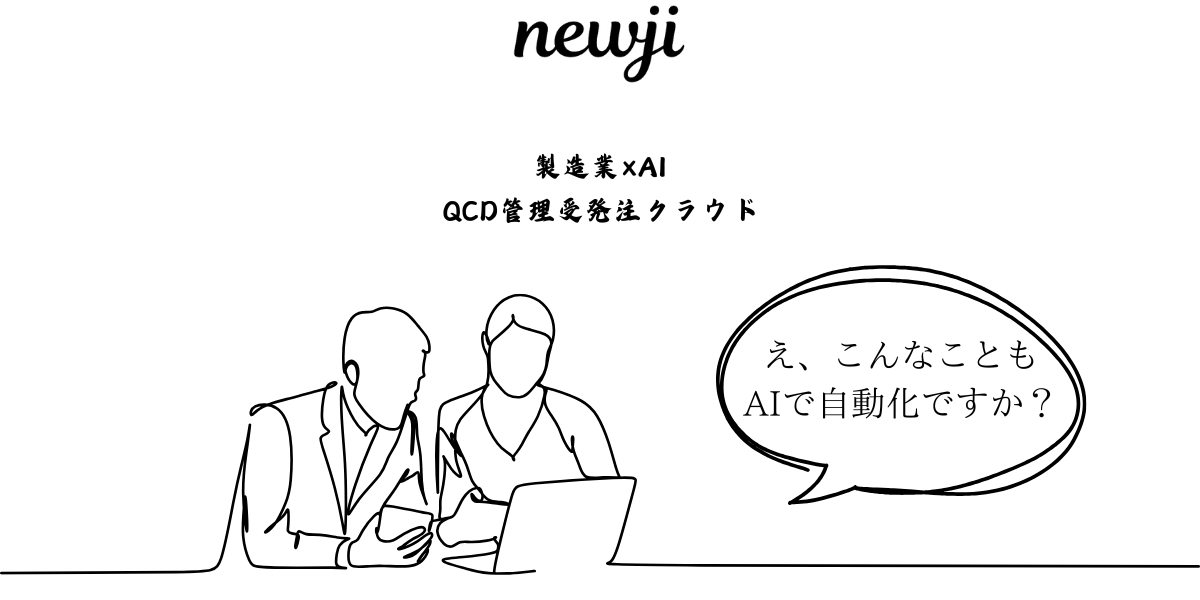
Revolutionizing Japanese Manufacturing: The Role of Wet Etching Process OEMs in Precision Engineering
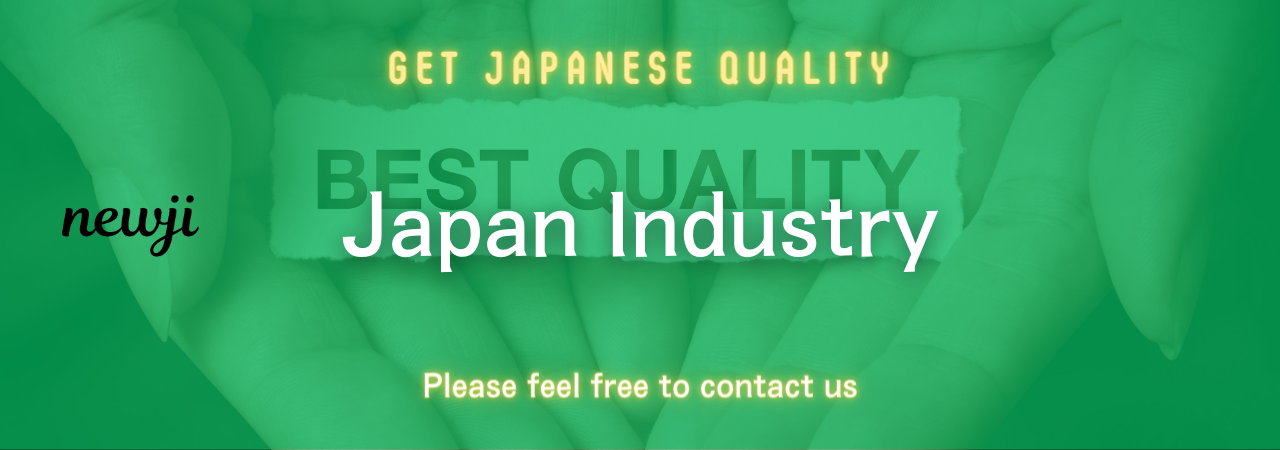
目次
Introduction to Wet Etching in Japanese Manufacturing
Wet etching is a critical process in the realm of precision engineering, particularly within Japanese manufacturing sectors. This chemical-based technique involves the removal of material from a wafer or substrate through liquid chemical solutions. The precision and control offered by wet etching make it indispensable for producing intricate components used in electronics, automotive parts, and various high-tech applications. Japanese manufacturers have long been pioneers in refining wet etching processes, contributing significantly to their reputation for excellence and innovation in the global market.
The Significance of OEMs in Wet Etching
Original Equipment Manufacturers (OEMs) play a pivotal role in the wet etching landscape. These companies specialize in producing etching equipment and processes tailored to the specific needs of their clients. By collaborating closely with OEMs, manufacturers can leverage cutting-edge technology and expertise to enhance their precision engineering capabilities. In Japan, OEMs are renowned for their meticulous attention to detail, reliability, and ability to integrate seamlessly with existing manufacturing systems.
Advantages of Partnering with Japanese OEMs
Partnering with Japanese OEMs offers several advantages:
– **High Precision and Quality:** Japanese OEMs are known for their stringent quality control measures, ensuring that the wet etching processes meet the highest standards.
– **Advanced Technology:** Continuous investment in research and development allows OEMs to provide state-of-the-art etching solutions.
– **Customization:** OEMs offer tailored solutions that can be adapted to the specific requirements of different manufacturing processes.
– **Reliability and Support:** Japanese companies often provide exceptional after-sales support and maintenance services, ensuring minimal downtime.
Disadvantages of Relying on Japanese OEMs
Despite the benefits, there are some drawbacks:
– **Higher Costs:** Advanced technology and superior quality often come at a premium price.
– **Longer Lead Times:** Due to the high demand and meticulous manufacturing processes, lead times may be longer compared to other regions.
– **Cultural and Language Barriers:** Communication challenges can arise, potentially affecting project timelines and outcomes.
Procurement and Purchasing Strategies for Wet Etching OEMs
Effective procurement and purchasing strategies are essential for maximizing the benefits of engaging with Japanese wet etching OEMs. These strategies encompass supplier selection, negotiation tactics, and risk management to ensure a seamless supply chain.
Supplier Selection
Selecting the right OEM is critical. Factors to consider include:
– **Technical Expertise:** Assess the OEM’s capability to meet specific technical requirements.
– **Reputation and Track Record:** Research the OEM’s history of delivering reliable and high-quality solutions.
– **Financial Stability:** Ensure the OEM has a stable financial standing to support long-term partnerships.
– **Compliance and Certifications:** Verify that the OEM adheres to relevant industry standards and holds necessary certifications.
Negotiation Techniques
Negotiating with Japanese OEMs requires a nuanced approach, respecting cultural norms and business practices:
– **Building Relationships:** Establishing trust and a strong working relationship is fundamental in Japanese business culture.
– **Clear Communication:** Articulate your requirements and expectations clearly to avoid misunderstandings.
– **Value Proposition:** Highlight the mutual benefits of the partnership, focusing on long-term collaboration rather than short-term gains.
– **Flexibility:** Be prepared to accommodate the OEM’s processes and timelines, demonstrating respect for their operational methods.
Risk Management in Procurement
Managing risks is vital to maintain a stable supply chain:
– **Diversification:** Avoid dependence on a single OEM by diversifying your supplier base.
– **Contingency Planning:** Develop backup plans to address potential disruptions, such as delays or quality issues.
– **Quality Assurance:** Implement rigorous quality control measures to detect and address defects early in the process.
– **Continuous Monitoring:** Regularly assess the performance and reliability of OEMs to identify and mitigate risks proactively.
Market Conditions Influencing Wet Etching OEMs
Understanding the market dynamics is essential for strategic decision-making in procurement and purchasing. Several factors influence the wet etching OEM market:
Technological Advancements
The rapid pace of technological innovation drives OEMs to continuously enhance their wet etching processes. Advances in materials science, automation, and precision control contribute to improved performance and efficiency.
Global Supply Chain Dynamics
Global events, such as trade disputes or pandemics, can significantly impact supply chains. Japanese OEMs often navigate these challenges with robust logistics and strong international networks, but disruptions can still affect lead times and costs.
Demand Fluctuations
The demand for precision-engineered components in industries like electronics, automotive, and aerospace influences the wet etching market. Economic cycles and sector-specific trends can lead to fluctuations in OEM demand.
Competitive Landscape
The presence of both domestic and international competitors shapes the market. Japanese OEMs often compete on quality and reliability, while other regions may offer cost advantages or specialized technologies.
Best Practices in Collaborating with Japanese Wet Etching OEMs
Adopting best practices ensures a productive and harmonious partnership with Japanese OEMs.
Cultural Understanding and Respect
Appreciating and respecting Japanese business culture fosters trust and cooperation. Understanding customs, business etiquette, and communication styles can enhance interactions and prevent misunderstandings.
Clear and Detailed Specifications
Providing comprehensive and precise specifications helps OEMs deliver products that meet your exact requirements. Detailed documentation reduces the risk of errors and ensures alignment between parties.
Regular Communication and Feedback
Maintaining open lines of communication facilitates the prompt resolution of issues and continuous improvement. Regular meetings and feedback sessions can help identify areas for enhancement and reinforce the partnership.
Long-Term Partnership Focus
Emphasizing long-term collaboration over short-term gains encourages mutual investment in success. Building a stable, ongoing relationship with OEMs can lead to better terms, preferential treatment, and greater innovation.
Advantages of Wet Etching in Precision Engineering
Wet etching offers several benefits in precision engineering, particularly for high-accuracy applications.
High Precision and Control
Wet etching allows for precise material removal, critical for applications requiring tight tolerances. The process can be finely tuned to achieve specific patterns and depths.
Cost-Effectiveness
Compared to other etching methods, wet etching can be more cost-effective, especially for large-scale production. The simplicity of the process reduces equipment and operational costs.
Versatility
Wet etching is compatible with a wide range of materials, including metals, semiconductors, and polymers. This versatility makes it suitable for diverse applications across various industries.
Scalability
The process is easily scalable, allowing manufacturers to adjust production volumes based on demand. This flexibility is advantageous for both small and large-scale operations.
Challenges in Wet Etching and OEM Collaboration
Despite its advantages, wet etching presents several challenges that manufacturers must navigate.
Environmental and Safety Concerns
Wet etching involves the use of hazardous chemicals, necessitating strict environmental and safety protocols. Compliance with regulations and proper waste management are essential to mitigate risks.
Process Variability
Achieving consistent results can be challenging due to factors like chemical concentration, temperature, and agitation. Manufacturers must implement robust process controls to ensure uniformity.
Material Limitations
Not all materials are equally amenable to wet etching. Some substrates may require specialized chemicals or alternative etching methods, limiting applicability.
Integration with Other Processes
Wet etching must often be integrated with other manufacturing processes, such as deposition or lithography. Ensuring seamless integration can be complex and requires careful planning and coordination.
Technological Innovations Enhancing Wet Etching
Technological advancements continue to refine and expand the capabilities of wet etching in precision engineering.
Automation and Process Control
Automation technologies enhance process precision and repeatability. Advanced sensors and control systems enable real-time monitoring and adjustments, improving overall efficiency and quality.
Advanced Chemical Formulations
Innovations in chemical formulations enhance etch rates, selectivity, and material compatibility. Tailored chemistries allow for more precise and efficient etching processes.
Nano-Scale Etching
Advances in nano-scale etching techniques enable the production of highly intricate and minuscule features. This capability is crucial for the development of cutting-edge electronic devices and components.
Environmentally Friendly Processes
There is a growing emphasis on developing eco-friendly etching processes. Innovations focus on reducing chemical usage, recycling etchants, and minimizing environmental impact.
Case Studies: Successful Collaborations with Japanese OEMs
Examining successful collaborations provides valuable insights into best practices and effective strategies.
Automotive Industry Partnership
A leading automotive manufacturer partnered with a Japanese OEM to develop a wet etching process for precision engine components. Through meticulous collaboration, they achieved enhanced component accuracy and reduced production costs. The partnership’s success was attributed to clear communication, mutual trust, and a shared commitment to quality.
Electronics Sector Innovation
In the electronics sector, a company collaborated with a Japanese OEM to innovate a wet etching technique for semiconductor fabrication. The collaboration led to the development of a high-precision etching process that significantly improved device performance and reliability. Regular feedback and joint problem-solving were key factors in the partnership’s effectiveness.
Aerospace Engineering Breakthrough
An aerospace engineering firm worked with a Japanese OEM to refine wet etching processes for specialized aerospace components. The collaboration resulted in the creation of lightweight, high-strength parts that met stringent aerospace standards. The success was driven by the OEM’s technical expertise and the manufacturer’s clear specification requirements.
Future Trends in Wet Etching and OEM Partnerships
Looking ahead, several trends are poised to shape the future of wet etching and OEM collaborations.
Integration with Additive Manufacturing
The convergence of wet etching with additive manufacturing (3D printing) presents new opportunities for complex part fabrication. Combining these technologies can lead to innovative manufacturing solutions with enhanced precision and flexibility.
Increased Focus on Sustainability
Sustainability will continue to be a driving force, with OEMs developing greener etching processes. Renewable energy integration, waste reduction, and eco-friendly chemicals will be prioritized to meet environmental standards and consumer expectations.
Advanced Data Analytics
The use of data analytics in process optimization will grow, enabling OEMs to leverage big data for predictive maintenance, quality control, and process improvements. Data-driven insights will enhance efficiency and reduce operational costs.
Global Expansion and Localization
Japanese OEMs may expand their global footprint, establishing localized operations to better serve international markets. This trend can lead to reduced lead times, improved customer service, and increased market responsiveness.
Strategic Recommendations for Manufacturers
To excel in utilizing wet etching processes through Japanese OEM partnerships, manufacturers should consider the following strategies:
Invest in Relationship Building
Develop strong, trust-based relationships with OEMs. Invest time in understanding their culture, business practices, and technical capabilities to foster a collaborative and productive partnership.
Emphasize Continuous Improvement
Adopt a mindset of continuous improvement, working with OEMs to refine processes, enhance quality, and innovate. Regularly review and optimize workflows to stay competitive.
Leverage Technology and Innovation
Stay abreast of the latest technological advancements in wet etching. Invest in training and development to ensure your team can effectively utilize new tools and techniques provided by OEMs.
Implement Robust Quality Control
Establish comprehensive quality control measures to monitor and maintain process consistency. Collaborate with OEMs to develop and enforce quality standards that align with your manufacturing goals.
Optimize Supply Chain Management
Enhance supply chain resilience by diversifying suppliers, implementing effective risk management practices, and leveraging technology for better visibility and control over the supply chain.
Conclusion
Wet etching remains a cornerstone of precision engineering, and Japanese OEMs continue to drive innovation and excellence in this field. By strategically partnering with these OEMs, manufacturers can unlock significant advantages in quality, efficiency, and technological capability. However, to fully realize these benefits, it is essential to adopt effective procurement and purchasing strategies, foster strong relationships, and stay attuned to market and technological trends. Embracing best practices and navigating challenges with informed strategies will position manufacturers to thrive in the competitive landscape of precision engineering.
資料ダウンロード
QCD調達購買管理クラウド「newji」は、調達購買部門で必要なQCD管理全てを備えた、現場特化型兼クラウド型の今世紀最高の購買管理システムとなります。
ユーザー登録
調達購買業務の効率化だけでなく、システムを導入することで、コスト削減や製品・資材のステータス可視化のほか、属人化していた購買情報の共有化による内部不正防止や統制にも役立ちます。
NEWJI DX
製造業に特化したデジタルトランスフォーメーション(DX)の実現を目指す請負開発型のコンサルティングサービスです。AI、iPaaS、および先端の技術を駆使して、製造プロセスの効率化、業務効率化、チームワーク強化、コスト削減、品質向上を実現します。このサービスは、製造業の課題を深く理解し、それに対する最適なデジタルソリューションを提供することで、企業が持続的な成長とイノベーションを達成できるようサポートします。
オンライン講座
製造業、主に購買・調達部門にお勤めの方々に向けた情報を配信しております。
新任の方やベテランの方、管理職を対象とした幅広いコンテンツをご用意しております。
お問い合わせ
コストダウンが利益に直結する術だと理解していても、なかなか前に進めることができない状況。そんな時は、newjiのコストダウン自動化機能で大きく利益貢献しよう!
(Β版非公開)