- お役立ち記事
- Uncovering Japan’s Printing Secrets: How Japanese Manufacturing Optimizes Dot Gain Management
月間77,185名の
製造業ご担当者様が閲覧しています*
*2025年2月28日現在のGoogle Analyticsのデータより
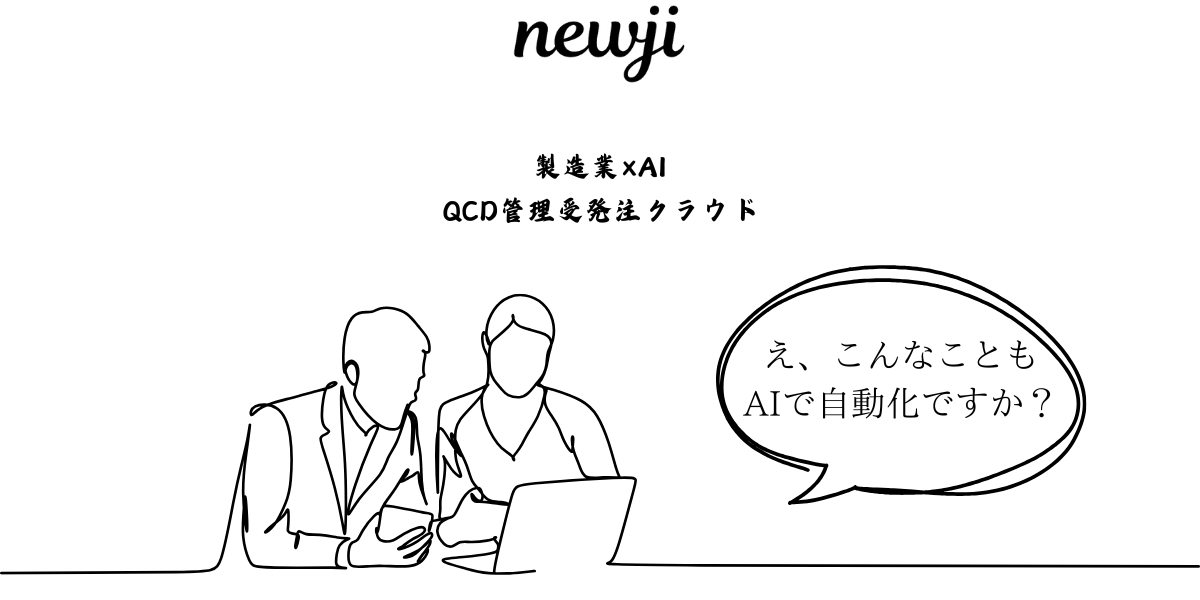
Uncovering Japan’s Printing Secrets: How Japanese Manufacturing Optimizes Dot Gain Management
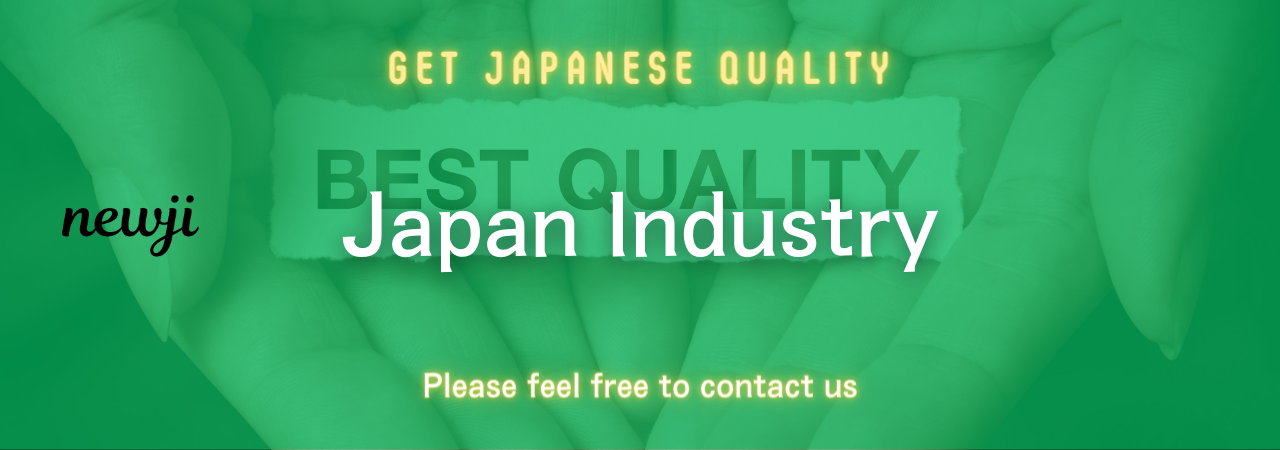
目次
Introduction to Dot Gain Management in Japanese Printing
Dot gain management is a crucial aspect of the printing process, ensuring that the final output matches the intended design. Japanese manufacturing has long been recognized for its precision and efficiency in various industries, including printing. By optimizing dot gain management, Japanese manufacturers achieve superior quality and consistency in their printed products. This article delves into the strategies and techniques employed by Japanese manufacturers to master dot gain management, offering valuable insights for procurement and purchasing professionals.
The Importance of Dot Gain in Printing
Dot gain refers to the phenomenon where printed dots appear larger than intended, affecting the overall image quality. Understanding and controlling dot gain is essential for maintaining color accuracy and sharpness in printed materials. Excessive dot gain can lead to muddiness in images, loss of detail, and color shifts, which are detrimental to the quality of the final product.
Impact on Color Accuracy
Color accuracy is paramount in the printing industry, especially for brands that rely on precise color matching. Uncontrolled dot gain can alter the intended hues, making it difficult to achieve consistency across different print runs and materials.
Quality Control and Customer Satisfaction
Maintaining strict control over dot gain is a key factor in ensuring high-quality prints. Consistent quality enhances customer satisfaction and builds trust in the manufacturer’s capabilities. Japanese manufacturers prioritize dot gain management to uphold their reputation for delivering exceptional products.
Strategies Employed by Japanese Manufacturers
Japanese manufacturers utilize a combination of advanced technologies and meticulous processes to optimize dot gain management. These strategies encompass various aspects of production, from equipment calibration to material selection and process monitoring.
Advanced Printing Technologies
The adoption of cutting-edge printing technologies plays a significant role in minimizing dot gain. Japanese manufacturers invest in state-of-the-art printing machines equipped with precise control systems that regulate ink deposition and drying processes. These technologies enable finer dot placement and reduce the risk of excess ink spread.
Precision Calibration and Maintenance
Regular calibration and maintenance of printing equipment are essential for consistent performance. Japanese manufacturers adhere to stringent maintenance schedules, ensuring that printers operate within optimal parameters. Precision calibration helps in achieving accurate dot placement, thereby controlling dot gain effectively.
High-Quality Inks and Substrates
The choice of inks and substrates significantly influences dot gain. Japanese manufacturers select high-quality, fast-drying inks that minimize ink spread during the printing process. Additionally, the selection of appropriate substrates with specific absorbency characteristics helps in controlling dot gain from the outset.
Data-Driven Process Monitoring
Implementing data-driven approaches allows for real-time monitoring and adjustments during the printing process. Japanese manufacturers utilize sophisticated software systems to track dot gain metrics continuously. This data-driven methodology facilitates prompt decision-making and ensures that any deviations are corrected immediately.
Advantages of Japanese Dot Gain Management Techniques
The meticulous dot gain management practices of Japanese manufacturers offer several advantages, both operational and strategic, to companies engaged in procurement and purchasing.
Consistent High-Quality Output
One of the primary benefits is the consistent high quality of printed materials. By controlling dot gain effectively, Japanese manufacturers ensure that every print batch meets the desired standards, reducing the likelihood of defects and reprints.
Enhanced Color Fidelity
Achieving accurate color reproduction is crucial for brand integrity. Japanese manufacturers’ expertise in dot gain management ensures that colors remain true to the original design, enhancing the overall visual appeal of printed products.
Improved Efficiency and Reduced Waste
Efficient dot gain management leads to fewer production errors and less material waste. This efficiency not only lowers production costs but also supports sustainable manufacturing practices, aligning with global environmental standards.
Strong Supplier Relationships
Japanese manufacturers’ reliability in delivering high-quality prints fosters strong, long-term relationships with their clients. For procurement and purchasing departments, this reliability translates into dependable supply chains and predictable product quality.
Challenges in Dot Gain Management
Despite the advanced techniques and technologies, managing dot gain presents several challenges that Japanese manufacturers continuously strive to overcome.
Variability in Materials
Different substrates and inks can behave unpredictably, making it challenging to maintain consistent dot gain across various projects. Manufacturers must tailor their approaches to accommodate these variations, requiring a deep understanding of material properties.
Technological Limitations
While Japanese manufacturers invest heavily in advanced technologies, there are inherent limitations in current printing equipment and materials that can impact dot gain control. Ongoing research and development are essential to address these limitations and push the boundaries of what is achievable.
Increasing Demand for Faster Turnaround
The global market’s demand for faster production cycles can pressure manufacturers to speed up their processes. Balancing speed with the precision required for effective dot gain management is a persistent challenge that requires innovative solutions.
Environmental Regulations
Stricter environmental regulations necessitate the use of eco-friendly inks and materials, which may have different dot gain characteristics. Manufacturers must adapt their dot gain management strategies to accommodate these changes while maintaining quality.
Supplier Negotiation Techniques for Dot Gain Management
Effective supplier negotiation is critical for ensuring that procurement and purchasing departments can secure the best terms and quality in dot gain management. Japanese manufacturers are known for their collaborative approach, which can be leveraged to achieve mutual benefits.
Building Strong Relationships
Cultivating strong, trust-based relationships with suppliers is fundamental. Japanese business culture emphasizes long-term partnerships, which can lead to better cooperation and shared goals in managing dot gain effectively.
Setting Clear Expectations
Clearly communicating quality standards and expectations regarding dot gain management helps suppliers understand their roles and responsibilities. Detailed specifications and regular feedback ensure that both parties are aligned in their objectives.
Collaborative Problem-Solving
Adopting a collaborative approach to problem-solving encourages open dialogue and mutual assistance when challenges in dot gain management arise. This teamwork fosters innovation and continuous improvement in processes.
Leveraging Technology Sharing
Sharing technological advancements and best practices can enhance a supplier’s capability in dot gain management. Japanese manufacturers are often willing to share proprietary technologies or methodologies to strengthen their supply chain.
Market Conditions Impacting Dot Gain Management
Understanding the broader market conditions is essential for effective dot gain management. Various economic, technological, and competitive factors influence how Japanese manufacturers approach this aspect of printing.
Economic Fluctuations
Economic conditions can affect material costs, investment in new technologies, and overall production capacity. Manufacturers must adapt their dot gain management strategies to remain cost-effective without compromising quality during economic downturns or booms.
Technological Advancements
Rapid advancements in printing technology continually reshape the capabilities for dot gain management. Staying abreast of the latest innovations allows manufacturers to integrate new tools and techniques that enhance their control over dot gain.
Global Competition
The global marketplace is highly competitive, with manufacturers from various countries striving for excellence in printing quality. Japanese manufacturers leverage their expertise in dot gain management to differentiate themselves and maintain a competitive edge.
Sustainability Trends
Increasing emphasis on sustainability prompts manufacturers to adopt eco-friendly practices, which can impact dot gain management. Developing sustainable inks and substrates that perform well in terms of dot gain is an ongoing area of focus.
Best Practices for Optimizing Dot Gain Management
Implementing best practices is essential for achieving optimal dot gain management. Japanese manufacturers exemplify these practices, which can serve as a guide for procurement and purchasing professionals.
Comprehensive Training Programs
Investing in training programs ensures that all personnel involved in the printing process understand the importance of dot gain and how to manage it effectively. Skilled operators can make informed adjustments that enhance print quality.
Standardized Processes
Establishing standardized workflows and procedures minimizes variability and ensures consistency in dot gain management. Standardization facilitates repeatability and reliability in production outcomes.
Continuous Quality Improvement
Adopting a mindset of continuous improvement encourages ongoing evaluation and enhancement of dot gain management practices. Regular audits and performance reviews help identify areas for improvement and implement necessary changes.
Leveraging Data Analytics
Utilizing data analytics tools to monitor and analyze dot gain metrics provides valuable insights into process performance. Data-driven decision-making enables proactive adjustments that maintain optimal dot gain levels.
Supplier Integration
Integrating suppliers into the dot gain management process ensures that all components, from materials to final prints, align with quality standards. Close collaboration and communication with suppliers enhance overall process control.
Conclusion
Dot gain management is a critical element of the printing process that significantly impacts the quality and consistency of printed materials. Japanese manufacturers set a benchmark in this field through their advanced technologies, meticulous processes, and strategic supplier relationships. For procurement and purchasing professionals, understanding and applying these Japanese techniques can lead to improved product quality, enhanced efficiency, and stronger supply chain partnerships. By adopting best practices and staying attuned to market conditions, companies can leverage the expertise of Japanese manufacturing to optimize their own dot gain management strategies and achieve superior printing outcomes.
資料ダウンロード
QCD管理受発注クラウド「newji」は、受発注部門で必要なQCD管理全てを備えた、現場特化型兼クラウド型の今世紀最高の受発注管理システムとなります。
ユーザー登録
受発注業務の効率化だけでなく、システムを導入することで、コスト削減や製品・資材のステータス可視化のほか、属人化していた受発注情報の共有化による内部不正防止や統制にも役立ちます。
NEWJI DX
製造業に特化したデジタルトランスフォーメーション(DX)の実現を目指す請負開発型のコンサルティングサービスです。AI、iPaaS、および先端の技術を駆使して、製造プロセスの効率化、業務効率化、チームワーク強化、コスト削減、品質向上を実現します。このサービスは、製造業の課題を深く理解し、それに対する最適なデジタルソリューションを提供することで、企業が持続的な成長とイノベーションを達成できるようサポートします。
製造業ニュース解説
製造業、主に購買・調達部門にお勤めの方々に向けた情報を配信しております。
新任の方やベテランの方、管理職を対象とした幅広いコンテンツをご用意しております。
お問い合わせ
コストダウンが利益に直結する術だと理解していても、なかなか前に進めることができない状況。そんな時は、newjiのコストダウン自動化機能で大きく利益貢献しよう!
(β版非公開)