- お役立ち記事
- Revolutionizing Japanese Manufacturing with Motor Efficiency Analysis Mapping Software: Boosting Productivity and Sustainability
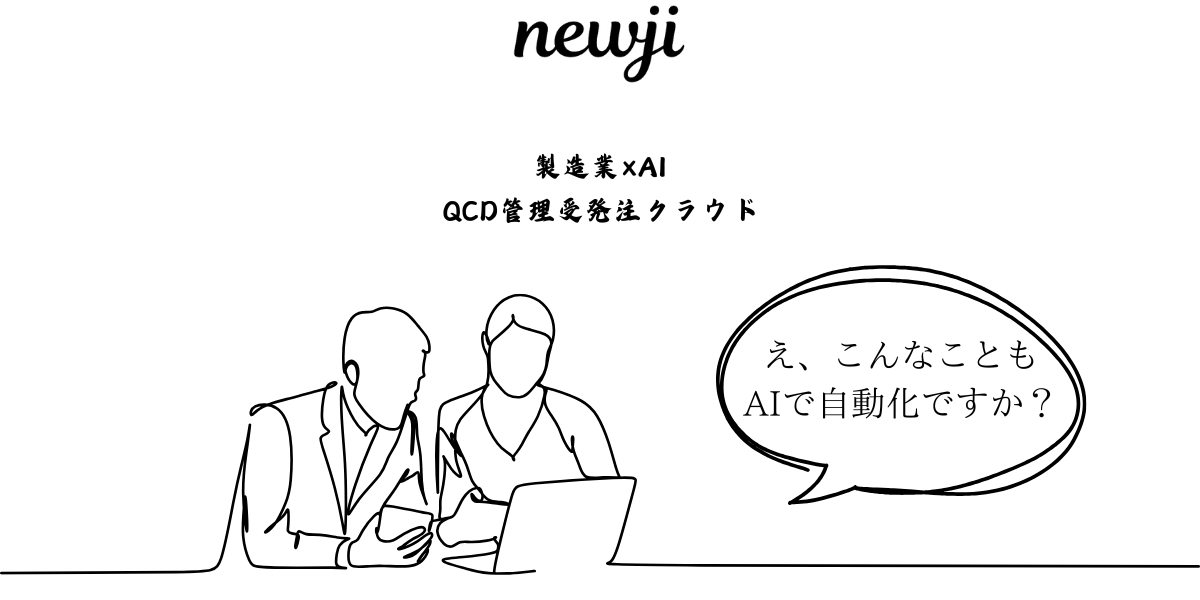
Revolutionizing Japanese Manufacturing with Motor Efficiency Analysis Mapping Software: Boosting Productivity and Sustainability
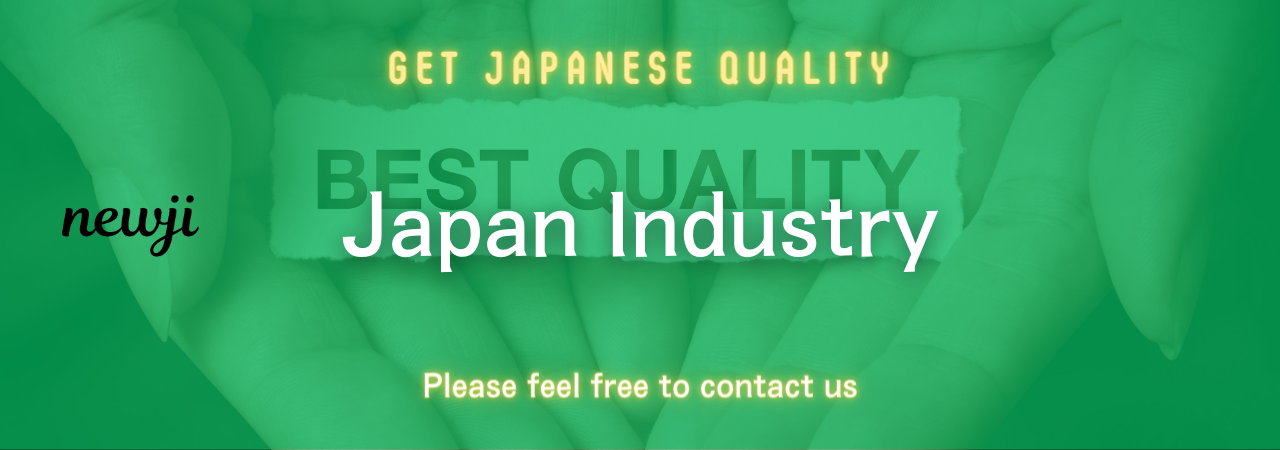
目次
Introduction
In the competitive landscape of global manufacturing, efficiency and sustainability have become paramount. Japanese manufacturing, renowned for its precision and reliability, continuously seeks innovative solutions to maintain its edge. One such innovation is Motor Efficiency Analysis Mapping Software, a technological advancement poised to revolutionize manufacturing processes. This software facilitates a comprehensive analysis of motor performance, identifying inefficiencies and enabling manufacturers to optimize operations. By integrating this software, Japanese manufacturers can significantly boost productivity while adhering to sustainable practices, ensuring long-term operational success and environmental responsibility.
Importance of Motor Efficiency in Manufacturing
Motor efficiency plays a critical role in manufacturing operations, directly impacting both operational costs and environmental footprint. Electric motors are the backbone of numerous manufacturing processes, driving machinery, conveyors, and various automated systems. Inefficient motors consume more electricity, leading to higher energy bills and increased greenhouse gas emissions. Additionally, inefficient motors tend to have shorter lifespans, resulting in more frequent replacements and higher maintenance costs. By focusing on motor efficiency, manufacturers can achieve cost savings, reduce their environmental impact, and enhance the overall reliability of their production systems. This emphasis aligns with global trends toward energy conservation and sustainability, making motor efficiency a key component of modern manufacturing strategies.
Overview of Motor Efficiency Analysis Mapping Software
Motor Efficiency Analysis Mapping Software is a specialized tool designed to assess and optimize the performance of electric motors within manufacturing systems. This software utilizes advanced algorithms and real-time data collection to map motor efficiency across various parameters, such as load, speed, and operating conditions. By providing detailed insights into motor performance, the software identifies inefficiencies, suggests corrective actions, and monitors improvements over time. Features typically include energy consumption tracking, predictive maintenance alerts, and automated reporting. The software integrates seamlessly with existing manufacturing systems, offering a user-friendly interface that allows engineers and managers to make informed decisions based on accurate and actionable data. This integration empowers manufacturers to enhance motor performance, reduce energy usage, and extend the lifespan of their motors, thereby driving both productivity and sustainability.
Advantages of Implementing the Software in Japanese Manufacturing
Implementing Motor Efficiency Analysis Mapping Software offers numerous advantages tailored to the strengths and needs of Japanese manufacturing. Firstly, the software enhances precision in monitoring motor performance, aligning with Japan’s emphasis on quality and accuracy. Secondly, it facilitates proactive maintenance strategies, minimizing downtime and ensuring continuous production flows, which is crucial for maintaining high productivity levels. Additionally, the software supports sustainability initiatives by identifying energy-saving opportunities, helping companies meet regulatory requirements and corporate social responsibility goals. The integration of this software also fosters a culture of continuous improvement, a cornerstone of Japanese manufacturing philosophy, by providing data-driven insights that inform strategic decisions. Furthermore, the ability to benchmark motor efficiency across different facilities enables standardized practices and knowledge sharing, reinforcing the competitive advantage of Japanese manufacturers in the global market.
Boosting Productivity through Enhanced Motor Efficiency
Enhanced motor efficiency directly translates to increased productivity in manufacturing settings. Efficient motors ensure that machinery operates at optimal performance levels, reducing energy wastage and minimizing the risk of mechanical failures. This reliability leads to fewer production interruptions, allowing for smoother and more consistent manufacturing processes. Additionally, efficient motors consume less power, which can be redirected to other critical areas of production, further boosting overall productivity. The software’s ability to pinpoint specific inefficiencies enables targeted improvements, ensuring that resources are allocated effectively to areas that will yield the highest returns. By streamlining motor performance, manufacturers can achieve higher output rates, shorten production cycles, and enhance the overall throughput of their manufacturing operations, thereby maintaining competitiveness in a demanding market.
Enhancing Sustainability with Motor Efficiency Analysis
Sustainability is a key consideration for modern manufacturers, and motor efficiency analysis plays a vital role in achieving environmental goals. Electric motors account for a significant portion of energy consumption in manufacturing facilities, and optimizing their efficiency reduces overall energy usage. This reduction not only lowers operational costs but also diminishes the carbon footprint associated with manufacturing activities. The software facilitates the identification of energy-saving opportunities, such as upgrading to more efficient motor models or adjusting operational parameters to match demand. Furthermore, by extending the lifespan of motors through proactive maintenance, manufacturers can decrease waste and reduce the need for frequent component replacements. These sustainability efforts contribute to a greener manufacturing process, enhancing the company’s reputation and compliance with environmental regulations. Ultimately, the integration of motor efficiency analysis supports long-term sustainability initiatives, ensuring responsible resource management and environmental stewardship.
Integration with Existing Manufacturing Systems
Successful implementation of Motor Efficiency Analysis Mapping Software requires seamless integration with existing manufacturing systems. Japanese manufacturers often utilize sophisticated production management and automation systems, making compatibility a critical factor. The software must be capable of interfacing with various data sources, including SCADA systems, PLCs, and IoT devices, to gather real-time motor performance data. Additionally, it should support standardized communication protocols to ensure interoperability with different hardware and software platforms. Effective integration minimizes disruptions during deployment and allows for the smooth transition of data flows. Training and support are essential components of the integration process, ensuring that personnel can effectively use the software and interpret its outputs. By aligning with existing infrastructure, the software enhances operational capabilities without necessitating significant overhauls, thereby providing a cost-effective solution for improving motor efficiency and overall manufacturing performance.
Supplier Negotiation Techniques for Software Implementation
Negotiating with software suppliers is a critical step in the successful implementation of Motor Efficiency Analysis Mapping Software. Japanese manufacturers can leverage their strong negotiation skills to secure favorable terms and ensure the software meets their specific needs. Key negotiation techniques include thoroughly understanding the software’s features and capabilities, allowing for informed discussions about pricing and customization options. Establishing clear requirements and expectations upfront can help in negotiating service level agreements (SLAs) that guarantee performance standards and support response times. Additionally, exploring volume discounts or long-term licensing agreements can result in cost savings. Building a collaborative relationship with the supplier is essential, fostering open communication and flexibility in addressing issues that may arise during implementation. Manufacturers should also consider negotiating training and support packages to maximize the software’s effectiveness and ensure a smooth adoption process. By applying strategic negotiation techniques, Japanese manufacturers can ensure that they obtain the best value and functionality from their Motor Efficiency Analysis Mapping Software investments.
Market Conditions and Trends in Motor Efficiency Software
The market for Motor Efficiency Analysis Mapping Software is experiencing significant growth, driven by increasing demand for energy efficiency and sustainability in manufacturing. Technological advancements have led to the development of more sophisticated and user-friendly software solutions, integrating features such as artificial intelligence and machine learning for predictive analytics. There is a growing trend towards cloud-based platforms, offering greater scalability, remote accessibility, and cost-effectiveness compared to traditional on-premises solutions. Additionally, the rise of the Internet of Things (IoT) has enhanced data collection capabilities, providing more granular insights into motor performance. Market competition is intensifying, with software providers focusing on differentiation through advanced analytics, customization options, and superior customer support. Japanese manufacturers are particularly influenced by these trends, seeking solutions that align with their high standards for quality and precision. Staying abreast of market conditions and emerging technologies enables manufacturers to make informed decisions and adopt the most effective motor efficiency tools available.
Best Practices for Adopting Motor Efficiency Analysis Mapping Software
Adopting Motor Efficiency Analysis Mapping Software requires a strategic approach to ensure successful implementation and optimal outcomes. Best practices include conducting a thorough needs assessment to identify specific motor efficiency challenges and objectives within the manufacturing facility. Selecting the right software involves evaluating different providers based on functionality, compatibility, ease of use, and support services. Engaging stakeholders from various departments, such as engineering, maintenance, and procurement, ensures that the software addresses diverse needs and gains organizational buy-in. Comprehensive training programs are essential to equip users with the necessary skills to operate the software effectively and interpret its data accurately. Establishing clear metrics and KPIs helps in tracking progress and measuring the software’s impact on motor efficiency and overall productivity. Regular reviews and updates are necessary to adapt to changing operational conditions and incorporate new features or upgrades. By following these best practices, manufacturers can maximize the benefits of Motor Efficiency Analysis Mapping Software, leading to sustained improvements in efficiency, productivity, and sustainability.
Challenges and Considerations
While Motor Efficiency Analysis Mapping Software offers substantial benefits, its implementation is not without challenges. One major consideration is the initial investment required for software acquisition and system integration, which can be significant, particularly for smaller manufacturers. Ensuring compatibility with existing systems and hardware may necessitate additional modifications or upgrades, adding to the overall cost and complexity. Data security is another critical issue, as the software must handle sensitive operational data, requiring robust cybersecurity measures to prevent unauthorized access and data breaches. Additionally, there may be resistance to change within the organization, with employees hesitant to adopt new technologies or alter established workflows. Overcoming this resistance requires effective change management strategies, including clear communication of the software’s benefits and comprehensive training programs. Another challenge is maintaining data accuracy and integrity, as unreliable or incomplete data can lead to incorrect analyses and suboptimal decision-making. Manufacturers must establish rigorous data management practices to ensure the reliability of the software’s outputs. Addressing these challenges proactively can facilitate a smoother implementation process and enhance the likelihood of achieving desired outcomes.
Future Prospects of Motor Efficiency Analysis in Manufacturing
The future of Motor Efficiency Analysis Mapping Software in manufacturing is poised for continued growth and innovation. Advancements in artificial intelligence and machine learning are expected to enhance the software’s predictive capabilities, enabling more accurate forecasting of motor performance and maintenance needs. Integration with emerging technologies such as augmented reality (AR) could provide interactive visualizations of motor systems, aiding in troubleshooting and optimization efforts. The increasing emphasis on sustainability is likely to drive further developments in energy-efficient software solutions, supporting manufacturers in achieving their environmental targets. Additionally, the global push towards Industry 4.0 will see greater connectivity and data exchange between different manufacturing systems, with Motor Efficiency Analysis Mapping Software playing a central role in this interconnected ecosystem. As manufacturers continue to prioritize efficiency and sustainability, the demand for sophisticated motor analysis tools will grow, leading to more competitive software offerings and broader adoption across the manufacturing sector. Embracing these future developments will enable manufacturers to stay ahead of industry trends and maintain their competitive advantage.
Conclusion
Motor Efficiency Analysis Mapping Software represents a transformative tool for Japanese manufacturing, offering significant enhancements in productivity and sustainability. By providing detailed insights into motor performance, the software enables manufacturers to optimize operations, reduce energy consumption, and extend the lifespan of critical equipment. The integration of this technology aligns with Japan’s commitment to quality, precision, and continuous improvement, reinforcing its position as a leader in global manufacturing. While challenges such as initial costs and data security must be carefully managed, the long-term benefits far outweigh the obstacles. As the manufacturing sector continues to evolve, embracing advanced motor efficiency analysis will be essential for staying competitive and achieving sustainable growth. By adopting best practices and staying attuned to market trends, Japanese manufacturers can fully leverage the potential of Motor Efficiency Analysis Mapping Software, driving innovation and excellence in their operations.
資料ダウンロード
QCD調達購買管理クラウド「newji」は、調達購買部門で必要なQCD管理全てを備えた、現場特化型兼クラウド型の今世紀最高の購買管理システムとなります。
ユーザー登録
調達購買業務の効率化だけでなく、システムを導入することで、コスト削減や製品・資材のステータス可視化のほか、属人化していた購買情報の共有化による内部不正防止や統制にも役立ちます。
NEWJI DX
製造業に特化したデジタルトランスフォーメーション(DX)の実現を目指す請負開発型のコンサルティングサービスです。AI、iPaaS、および先端の技術を駆使して、製造プロセスの効率化、業務効率化、チームワーク強化、コスト削減、品質向上を実現します。このサービスは、製造業の課題を深く理解し、それに対する最適なデジタルソリューションを提供することで、企業が持続的な成長とイノベーションを達成できるようサポートします。
オンライン講座
製造業、主に購買・調達部門にお勤めの方々に向けた情報を配信しております。
新任の方やベテランの方、管理職を対象とした幅広いコンテンツをご用意しております。
お問い合わせ
コストダウンが利益に直結する術だと理解していても、なかなか前に進めることができない状況。そんな時は、newjiのコストダウン自動化機能で大きく利益貢献しよう!
(Β版非公開)