- お役立ち記事
- Precision prototyping process made with CNC machining
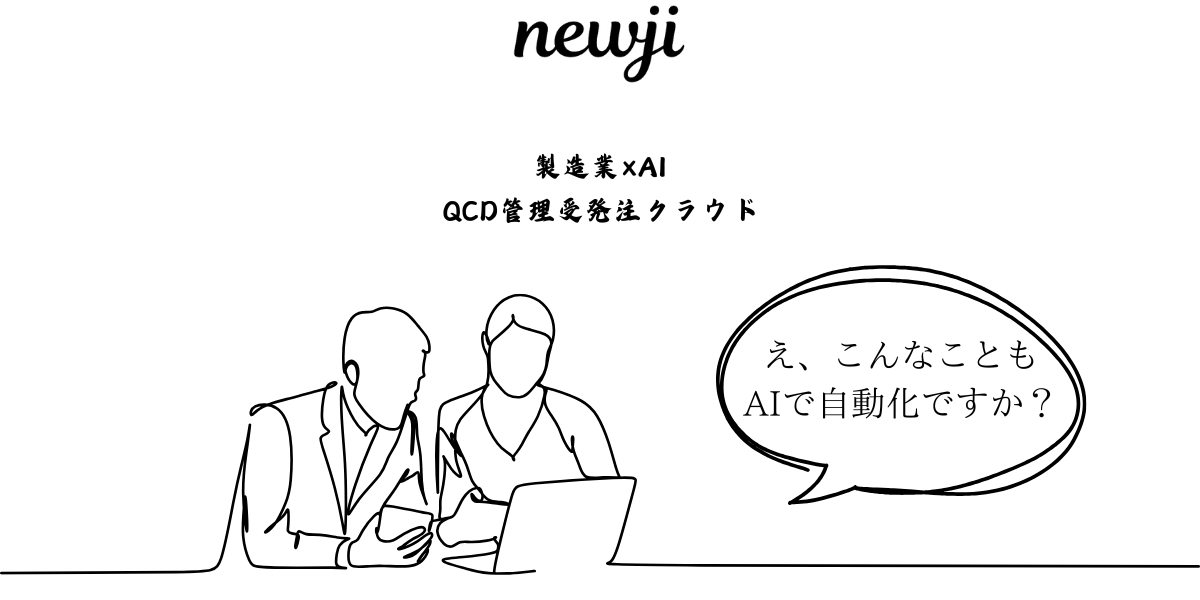
Precision prototyping process made with CNC machining
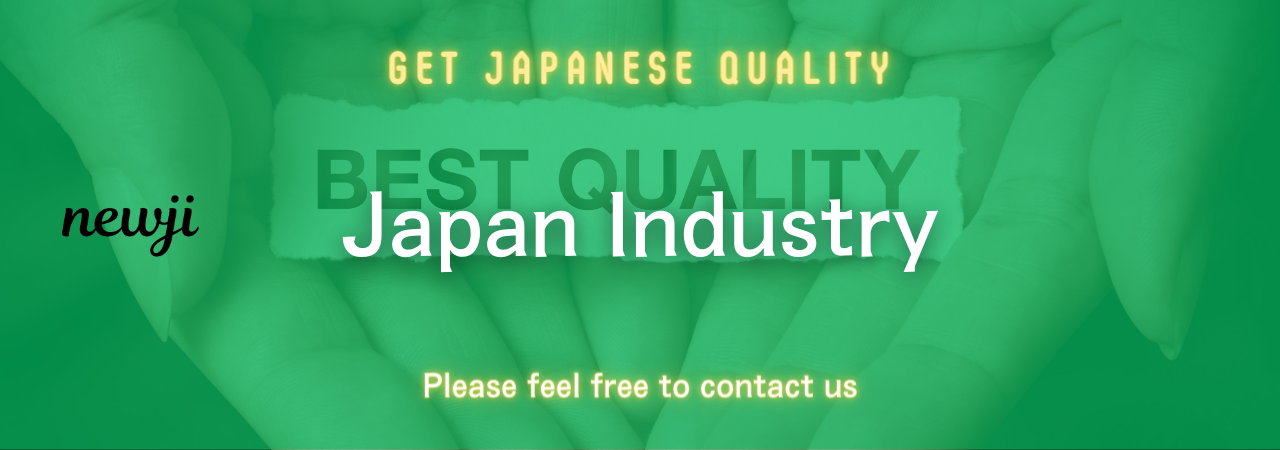
目次
Understanding CNC Machining
CNC machining stands for Computer Numerical Control machining.
It is a process where pre-programmed computer software dictates the movement of factory tools and machinery.
This technology is used to control a range of complex machinery, from grinders and lathes to mills and routers.
With CNC machining, you can achieve high precision and accuracy, which is critical in the prototyping phase of product development.
Why Choose CNC Machining for Prototyping?
The importance of prototyping cannot be understated.
It allows designers and engineers to test the functionality, durability, and overall look of a product before it goes into mass production.
CNC machining stands out for prototyping because it offers unparalleled precision.
By using a computer program, the machine can replicate complex designs within a tight tolerance range, ensuring every prototype is an exact match to the design specifications.
Moreover, CNC machining is versatile and can work with a variety of materials, such as metal, plastic, wood, and foam.
This adaptability makes it a favorable choice for industries ranging from aerospace to consumer electronics.
Steps in CNC Machining of Prototypes
1. Design Creation
The first step in the CNC machining process is designing the prototype.
Designs are usually created using CAD (Computer-Aided Design) software.
These designs hold all the necessary specifications, dimensions, and details that the CNC machine needs to follow.
It is crucial to have a detailed design, as it will directly impact the precision and functionality of the final prototype.
2. Conversion to CNC Code
After the design is completed, it is translated into a format that the CNC machine can understand.
This format is known as G-code.
G-code is a programming language that contains instructions for the machine regarding where and how to move.
These instructions tell the machine the specific path, speed, and depth required to craft each part of the prototype.
3. Setup and Calibration
Before the actual machining begins, the CNC machine must be set up and calibrated.
This involves selecting the appropriate tools, setting the machine to the correct parameters, and securely positioning the material.
Proper setup is essential to ensure the machine runs correctly and safely, minimizing the risk of errors or accidents.
4. Machining Process
Once everything is set, the machine executes the G-code by precisely cutting or shaping the material according to the design specifications.
This stage involves various processes such as milling, drilling, and turning, depending on the prototype’s design requirements.
The machine meticulously follows each command, resulting in a detailed prototype.
Post-Machining Procedures
Finishing and Inspection
After the machining process, the prototype undergoes finishing and inspection.
Finishing involves cleaning, polishing, or coating the prototype to improve its appearance or functionality.
The prototype is then examined to ensure it meets all design specifications and quality standards.
Any necessary adjustments or corrections can be made at this stage.
Testing and Validation
Once the prototype passes the initial inspection, it undergoes rigorous testing.
This testing phase is crucial to validate the prototype’s functionality and reliability.
Depending on the intended use of the prototype, it may be subjected to stress tests, environmental tests, or performance evaluations.
Successful testing ensures that the prototype can proceed to the next stage of product development.
Advantages of CNC Machining for Prototyping
High Precision and Consistency
CNC machining offers unmatched precision and consistency.
The accuracy of CNC machines allows for the creation of complex geometries with minimal errors, which is pivotal for testing designs.
Once the machine is programmed, it can produce large numbers of identical prototypes, maintaining the same high quality for each one.
Time and Cost Efficiency
Although initial setup and programming of CNC machines require time, they save time in the long run.
Their speed and efficiency help reduce overall production time compared to manual machining techniques.
Additionally, CNC machines can reduce labor costs as they can operate with minimal supervision.
Versatility in Material Use
CNC machines can handle a diverse range of materials, allowing for flexibility in choosing the material best for the prototype.
This versatility is advantageous for designers and engineers who want to explore various options to optimize the prototype’s performance.
Future of Precision Prototyping with CNC Machining
As technology continues to evolve, CNC machining will likely become even more integral to precision prototyping.
Advancements in software and machine capabilities are expected to further increase accuracy, reduce production times, and lower costs.
Moreover, the integration of AI and machine learning could lead to more autonomous and intuitive prototyping processes.
In conclusion, CNC machining is a cornerstone of precision prototyping, offering unparalleled accuracy, consistency, and efficiency.
Its ability to handle various materials and produce intricate designs makes it an invaluable tool in modern manufacturing, ensuring that prototypes meet the highest standards before moving to mass production.
資料ダウンロード
QCD調達購買管理クラウド「newji」は、調達購買部門で必要なQCD管理全てを備えた、現場特化型兼クラウド型の今世紀最高の購買管理システムとなります。
ユーザー登録
調達購買業務の効率化だけでなく、システムを導入することで、コスト削減や製品・資材のステータス可視化のほか、属人化していた購買情報の共有化による内部不正防止や統制にも役立ちます。
NEWJI DX
製造業に特化したデジタルトランスフォーメーション(DX)の実現を目指す請負開発型のコンサルティングサービスです。AI、iPaaS、および先端の技術を駆使して、製造プロセスの効率化、業務効率化、チームワーク強化、コスト削減、品質向上を実現します。このサービスは、製造業の課題を深く理解し、それに対する最適なデジタルソリューションを提供することで、企業が持続的な成長とイノベーションを達成できるようサポートします。
オンライン講座
製造業、主に購買・調達部門にお勤めの方々に向けた情報を配信しております。
新任の方やベテランの方、管理職を対象とした幅広いコンテンツをご用意しております。
お問い合わせ
コストダウンが利益に直結する術だと理解していても、なかなか前に進めることができない状況。そんな時は、newjiのコストダウン自動化機能で大きく利益貢献しよう!
(Β版非公開)