- お役立ち記事
- Important points in prototyping tools for friction stir welding and how to select prototype workers
月間77,185名の
製造業ご担当者様が閲覧しています*
*2025年2月28日現在のGoogle Analyticsのデータより
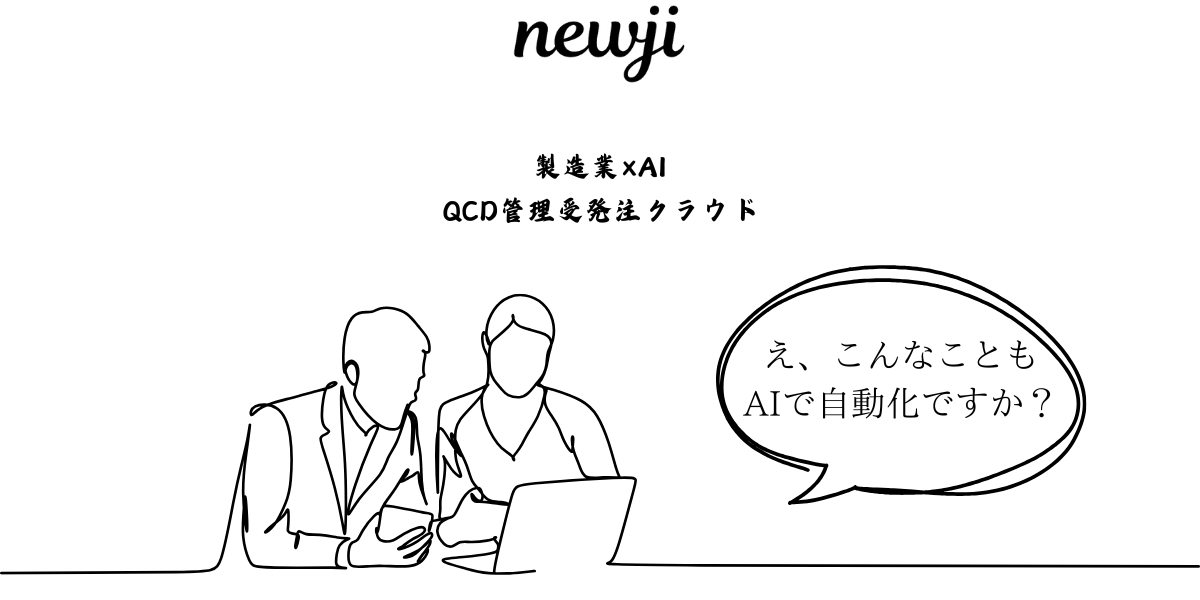
Important points in prototyping tools for friction stir welding and how to select prototype workers
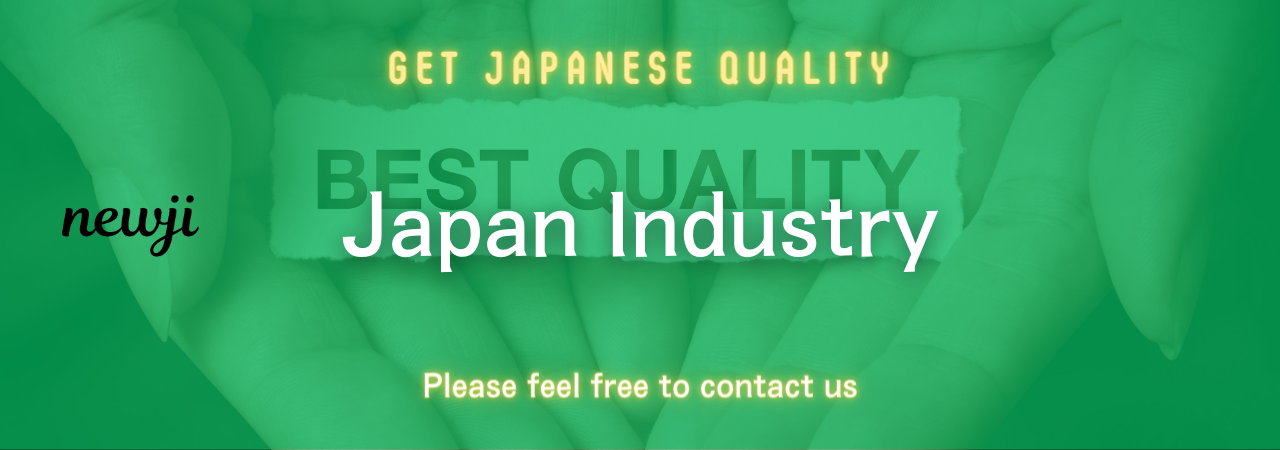
目次
Understanding Friction Stir Welding
Friction stir welding (FSW) is a solid-state joining process that is used to join two facing workpieces without melting the material.
Instead, it uses a non-consumable tool to generate frictional heat, causing the components to soften and be mixed at the joint site, forming a strong bond as the material cools.
FSW is commonly used in the aerospace, automotive, and shipbuilding industries due to its ability to produce high-quality welds with minimal distortion.
Importance of Prototyping in FSW
Prototyping is a crucial step in the friction stir welding process.
It allows engineers and designers to test and refine their FSW techniques before full-scale production begins.
By creating prototypes, potential issues can be identified and corrected early on, saving time and resources in the long run.
Prototyping helps ensure that the FSW process is optimized for the materials and joint configurations being used.
It provides valuable insights into the performance of the weld and its ability to withstand the intended loads.
Key Tools for FSW Prototyping
When it comes to prototyping for friction stir welding, choosing the right tools is essential for achieving the best results.
Here are some important points to consider when selecting prototyping tools for FSW:
Tool Material
The material of the welding tool is crucial for its performance and lifespan.
Common materials used for FSW tools include tool steel, tungsten carbide, and polycrystalline cubic boron nitride (PCBN).
Each material has its own benefits and is suited to different applications, so it’s important to choose the right one based on the specific requirements of the project.
Tool Geometry
The geometry of the FSW tool, including the shoulder and pin profiles, plays a significant role in determining the quality of the weld.
The tool’s design can affect the heat generation, material flow, and final surface finish of the weld.
It’s important to select a tool with the appropriate geometry for the materials and joint design being used in the prototype.
Tool Size
The size of the tool is another critical factor to consider.
The size must be compatible with the thickness and type of the materials being joined.
Using an appropriately sized tool ensures consistent heat distribution and effective material mixing, resulting in a defect-free weld.
Selecting Prototype Workers for FSW
The success of the FSW prototyping process also depends heavily on the expertise of the workers involved.
Here are some tips for selecting the right prototype workers for FSW:
Experience
Experience is key when it comes to selecting workers for FSW prototyping.
Look for individuals who have a proven track record in working with FSW processes and materials.
Experienced workers are more likely to understand the nuances of the process and be able to troubleshoot any issues that arise.
Technical Knowledge
Workers involved in FSW prototyping should have a strong technical understanding of the welding process and the materials being used.
This includes knowledge of tool selection, parameter settings, and potential weld defects.
A good grasp of these technical elements can help ensure the success of the prototyping process.
Problem-Solving Skills
Prototyping is an iterative process that often involves testing, evaluation, and refinement.
Workers with strong problem-solving skills are essential for identifying issues quickly and proposing effective solutions.
Their ability to adapt and make informed decisions will contribute to a more efficient and successful prototyping phase.
The Role of Technology in FSW Prototyping
In addition to skilled workers and proper tool selection, the use of technology can significantly enhance the FSW prototyping process.
Advanced simulation software can be used to model the welding process, predict outcomes, and optimize parameters before actual testing takes place.
This reduces the number of physical prototypes needed and helps improve the efficiency of the process.
Furthermore, modern FSW equipment often comes with features like real-time monitoring and data logging, which can provide valuable insights into the process and highlight areas for improvement.
Conclusion
Prototyping is a vital step in the friction stir welding process, allowing for thorough testing and optimization before full-scale production.
Choosing the right tools and engaging skilled workers are essential for a successful prototype.
Additionally, leveraging technology can further enhance the prototyping process by providing accurate insights and reducing trial and error.
As industries continue to rely on FSW for its strength and efficiency, effective prototyping will remain a cornerstone of successful welding projects.
By focusing on the key aspects outlined above, companies can ensure their FSW processes meet the highest standards of quality and performance.
資料ダウンロード
QCD管理受発注クラウド「newji」は、受発注部門で必要なQCD管理全てを備えた、現場特化型兼クラウド型の今世紀最高の受発注管理システムとなります。
ユーザー登録
受発注業務の効率化だけでなく、システムを導入することで、コスト削減や製品・資材のステータス可視化のほか、属人化していた受発注情報の共有化による内部不正防止や統制にも役立ちます。
NEWJI DX
製造業に特化したデジタルトランスフォーメーション(DX)の実現を目指す請負開発型のコンサルティングサービスです。AI、iPaaS、および先端の技術を駆使して、製造プロセスの効率化、業務効率化、チームワーク強化、コスト削減、品質向上を実現します。このサービスは、製造業の課題を深く理解し、それに対する最適なデジタルソリューションを提供することで、企業が持続的な成長とイノベーションを達成できるようサポートします。
製造業ニュース解説
製造業、主に購買・調達部門にお勤めの方々に向けた情報を配信しております。
新任の方やベテランの方、管理職を対象とした幅広いコンテンツをご用意しております。
お問い合わせ
コストダウンが利益に直結する術だと理解していても、なかなか前に進めることができない状況。そんな時は、newjiのコストダウン自動化機能で大きく利益貢献しよう!
(β版非公開)