- お役立ち記事
- Evolution of processing technology that connects prototyping and mass production
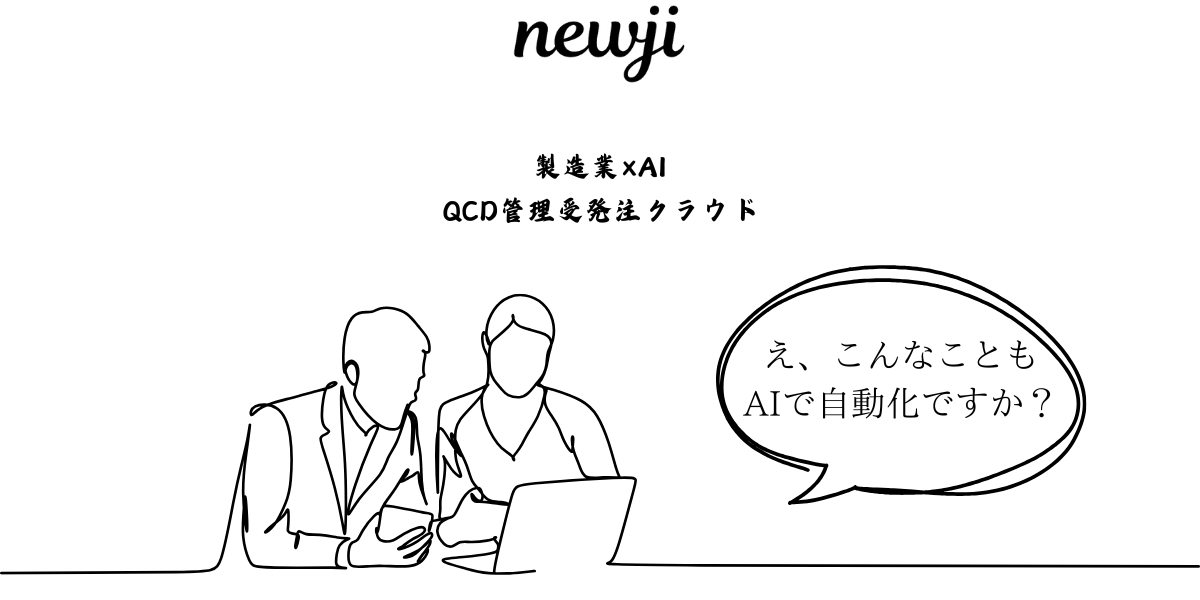
Evolution of processing technology that connects prototyping and mass production
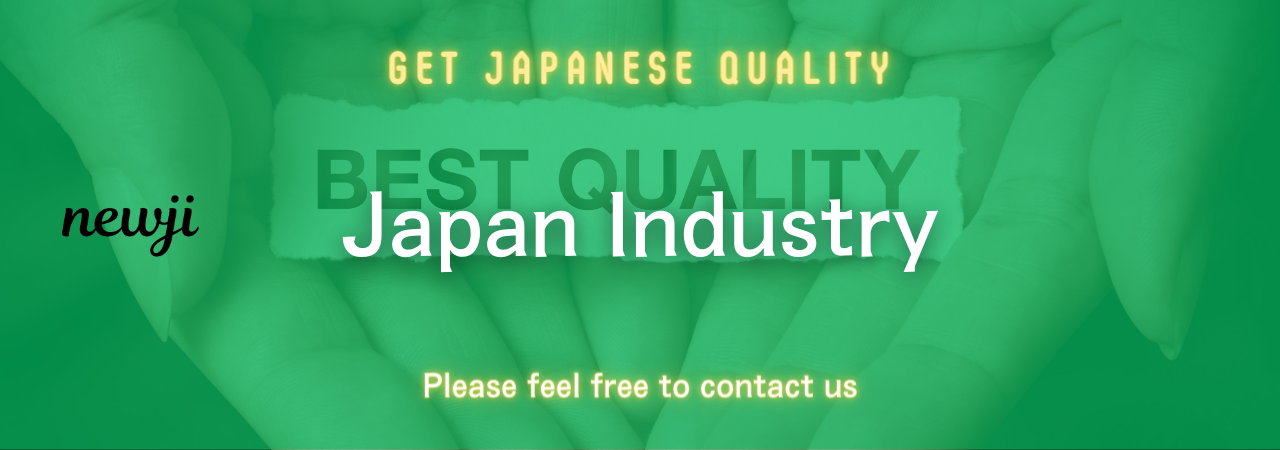
目次
Introduction to Processing Technology
Processing technology has evolved significantly over the past few decades.
This evolution has played a crucial role in bridging the gap between the initial stages of prototyping and the final steps of mass production.
Prototyping is often seen as the playground for product innovation, where an idea is turned into a tangible form.
However, an equally important aspect is transitioning this prototype into a product that can be mass-produced efficiently and cost-effectively.
In today’s rapidly advancing technological landscape, processing technologies enable this transition seamlessly, reducing time, cost, and risks.
The Historical Perspective
Historically, the world of prototyping and mass production were distinct.
The traditional methods of crafting a prototype involved manual labor and time-consuming techniques.
Prototypes were custom-made, piece-by-piece, each requiring meticulous attention to detail.
Mass production, on the other hand, required a shift to completely different techniques and machinery, often leading to discrepancies between the prototype and the final product.
With the advent of new processing technologies, the line between prototyping and mass production began to blur.
Innovative methods such as Computer Numerical Control (CNC) and digital modeling paved the way for more consistency between prototype and production.
This bridge allowed manufacturers to visualize potential issues early in the process, offering a clearer pathway to mass production.
Innovations in Processing Technology
The 21st century has introduced revolutionary innovations in processing technology, facilitating a seamless transition from prototypes to production.
Additive manufacturing, commonly known as 3D printing, has been one of the major breakthroughs.
It allows for the creation of complex geometries that were previously impossible or too costly to produce with traditional techniques.
3D printing not only accelerates the prototyping phase but also enables cost-effective small-scale production runs.
This flexibility is crucial for testing and iterating designs quickly, ensuring that any issues are addressed long before mass production begins.
Another significant advancement is the use of artificial intelligence and machine learning in processing technology.
These technologies optimize production processes by predicting potential failures, enhancing machine efficiency, and ensuring consistent quality control across production runs.
By incorporating real-time data analytics, manufacturers can adjust the production process to improve both speed and output quality.
Closed-Loop Manufacturing Systems
A noteworthy evolution in processing technology is the development of closed-loop manufacturing systems.
These systems continuously monitor, adjust, and improve the production process through feedback loops.
They involve sophisticated software and sensors that track everything from raw material usage to final product quality.
By enabling real-time adjustments, these systems reduce waste, improve efficiency, and maintain high standards of quality.
Closed-loop systems are pivotal in industries where precision and reliability are paramount, like automotive and aerospace.
Bridging the Gap with Advanced Materials
The evolution of processing technology is not limited to machinery and software.
Advancements in material science have also played a critical role in closing the gap between prototyping and mass production.
High-performance materials such as composites and alloys are now accessible in the prototyping phase.
These materials ensure that the prototype closely mirrors the final product in terms of functionality and durability.
Moreover, new developments in eco-friendly materials strive to make both prototyping and mass production sustainable, reducing environmental impact without compromising on quality.
Digital Prototyping and Virtual Reality
Digital prototyping and virtual reality (VR) are transforming how prototypes are developed and tested.
These technologies provide a comprehensive view of the product in a simulated environment before physical creation.
Digital twins – a dynamic, real-time replica of the product – allow for extensive testing and modifications without the expense or time of physical prototypes.
Virtual reality provides an immersive experience, offering designers and engineers the chance to ‘feel’ the product and make intuitive adjustments.
These tools ultimately streamline the transition from digital concept to physical prototype, minimizing barriers to mass production.
The Role of Cloud Computing
Cloud computing has become indispensable in the realm of processing technology.
It offers vast storage, enables collaborative platforms, and provides computational power critical for processing large datasets.
Cloud solutions ensure that teams across the globe can collaborate seamlessly on a single project, enhancing innovation and speeding up the timeline from idea to product.
Manufacturers leverage cloud computing to manage supply chains, perform real-time data analytics, and ensure smooth production runs, thus aligning prototyping closely with mass production.
Challenges and Future Prospects
Despite these advancements, challenges such as high initial investments in technology, skilled labor shortages, and cybersecurity threats persist.
However, the trajectory of processing technology is firmly set toward further innovation.
Future prospects include advancements in IoT integration, which will allow machines to communicate and coordinate with one another autonomously.
This enhanced connectivity could result in unprecedented levels of efficiency and customization in both prototyping and mass production.
Moreover, the continuous push towards sustainability will likely drive innovations aimed at reducing energy consumption and waste, making processing technology a key player in achieving global environmental goals.
Conclusion
In conclusion, the evolution of processing technology has fundamentally transformed the manufacturing landscape, effectively connecting prototyping with mass production.
Through innovations in 3D printing, AI, closed-loop systems, and advanced materials, manufacturers can ensure higher efficiency, consistency, and quality in their products.
As this evolution continues, it promises a future where ideas rapidly transition from the drawing board to market-ready products, all while maintaining sustainability and reducing cost implications.
This synergy between prototyping and production not only benefits manufacturers but also encourages a wave of innovation and creativity across industries.
資料ダウンロード
QCD調達購買管理クラウド「newji」は、調達購買部門で必要なQCD管理全てを備えた、現場特化型兼クラウド型の今世紀最高の購買管理システムとなります。
ユーザー登録
調達購買業務の効率化だけでなく、システムを導入することで、コスト削減や製品・資材のステータス可視化のほか、属人化していた購買情報の共有化による内部不正防止や統制にも役立ちます。
NEWJI DX
製造業に特化したデジタルトランスフォーメーション(DX)の実現を目指す請負開発型のコンサルティングサービスです。AI、iPaaS、および先端の技術を駆使して、製造プロセスの効率化、業務効率化、チームワーク強化、コスト削減、品質向上を実現します。このサービスは、製造業の課題を深く理解し、それに対する最適なデジタルソリューションを提供することで、企業が持続的な成長とイノベーションを達成できるようサポートします。
オンライン講座
製造業、主に購買・調達部門にお勤めの方々に向けた情報を配信しております。
新任の方やベテランの方、管理職を対象とした幅広いコンテンツをご用意しております。
お問い合わせ
コストダウンが利益に直結する術だと理解していても、なかなか前に進めることができない状況。そんな時は、newjiのコストダウン自動化機能で大きく利益貢献しよう!
(Β版非公開)