- お役立ち記事
- Introduction and practical examples of digital twin in the prototyping process
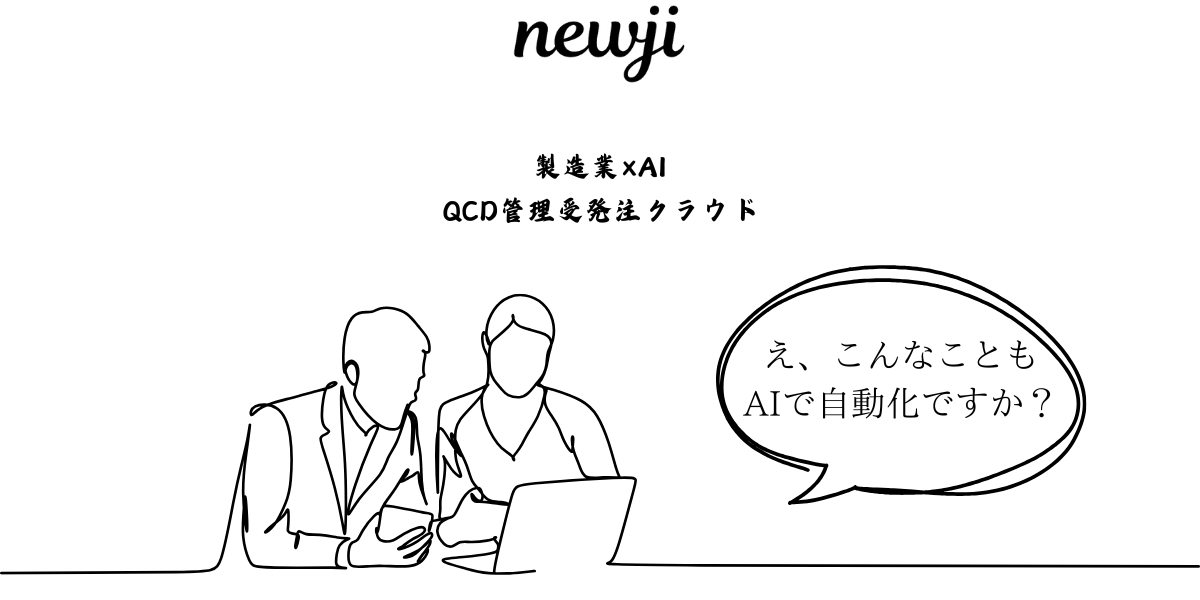
Introduction and practical examples of digital twin in the prototyping process
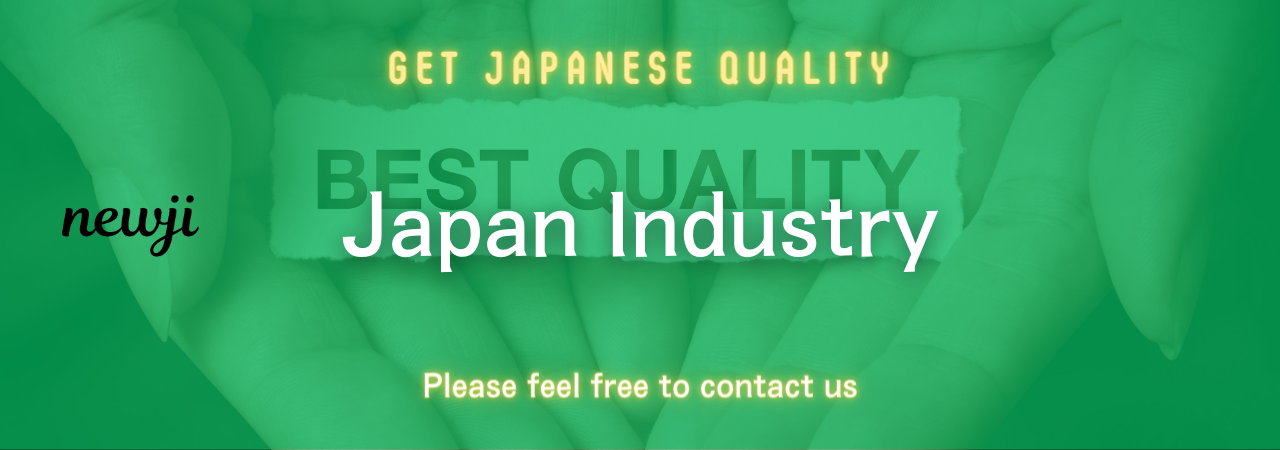
目次
Understanding Digital Twin Technology
Digital twin technology is a fascinating concept that’s transforming how industries approach design and manufacturing processes.
Simply put, a digital twin is a virtual replica of a physical object or system, created to simulate, analyze, and improve its real-world counterpart.
This technology is invaluable in the prototyping stage, where it allows engineers and designers to visualize a product’s lifecycle and optimize performance before physical manufacturing begins.
The digital twin operates by integrating information from various real-time data sources.
It uses sensors and IoT (Internet of Things) technologies to continually gather data about the physical object’s performance, which is then fed into the digital model.
This data-driven approach enables businesses to simulate different scenarios, foresee issues, and implement solutions seamlessly.
The Role of Digital Twin in Prototyping
In prototyping, digital twins offer a dynamic way to test and refine new products or systems.
Traditional prototyping methods can be time-consuming and costly, often requiring several iterations of physical models to be manufactured before arriving at a final product.
Digital twins streamline this process significantly by enabling virtual testing and modifications.
By creating a digital twin of a prototype, designers can run simulations to observe how the product will perform under various conditions.
This reduces the need for costly physical prototypes, as potential design flaws can be identified and addressed in the virtual realm.
Moreover, the insights gained from these simulations can accelerate the development cycle, bringing products to market faster and more efficiently.
Advantages of Using Digital Twin in Prototyping
1. **Cost Efficiency**: By reducing the number of physical prototypes needed, digital twins cut down costs associated with materials, labor, and time.
2. **Time Savings**: Virtual testing speeds up the prototyping process, allowing for quicker refinement and iteration.
3. **Improved Design Accuracy**: With access to real-time data and comprehensive simulations, designers can create more precise models that lead to better quality products.
4. **Risk Reduction**: Simulating scenarios helps identify potential issues early, preventing costly mistakes at later stages of production.
Practical Examples of Digital Twin Applications
Let’s explore some practical examples of how digital twins are applied in various industries during the prototyping phase.
Aerospace Industry
In aerospace, creating a digital twin of an aircraft component allows engineers to simulate its performance under different flight conditions and stress factors.
For instance, a digital twin can predict how an engine will perform in extreme weather scenarios or under varying altitude pressures.
This level of analysis ensures that when the component is physically manufactured, it meets the required safety and performance standards.
Automotive Industry
Car manufacturers use digital twins to prototype new vehicle models, simulating driving experiences and safety tests virtually.
These simulations provide critical insights into how a car might behave in real-world conditions, such as crash scenarios or fuel efficiency metrics.
Consequently, this information can inform design improvements that enhance the vehicle’s performance and safety before it hits the production line.
Healthcare
In healthcare, digital twins are used to create detailed simulations of medical devices and even human organs.
This technology aids in the development of precision devices tailored to specific patient needs.
For example, a digital twin of a human heart can be used to design and prototype custom-fit cardiac implants, significantly reducing the risk of complications and improving patient outcomes.
Smart Cities and Infrastructure
Digital twins are instrumental in designing and prototyping urban infrastructure projects.
By creating a digital representation of a building or city planning project, architects and engineers can simulate environmental impacts, energy consumption, and traffic flow.
These insights contribute to the development of smarter, more efficient urban solutions that are better aligned with sustainability goals.
Future Prospects of Digital Twin in Prototyping
The integration of digital twin technology in the prototyping stage is still evolving, and its potential continues to grow with advancements in AI, machine learning, and IoT devices.
As these technologies progress, digital twins will become even more sophisticated, capable of providing deeper insights and greater accuracy.
In the future, we can expect digital twins to facilitate even more groundbreaking innovations across various industries.
For example, they might enable more complex simulations that include human-computer interaction factors, allowing for more intuitive product designs.
Furthermore, the continuous improvement of AI algorithms could automate much of the analysis, offering instant recommendations and optimizations during the prototyping process.
As industries continue to embrace digital twin technology, the prototyping process will evolve to become more efficient, cost-effective, and innovative.
This transformation not only promises to revolutionize how products and systems are designed and tested but also signals a shift towards more sustainable production practices.
In conclusion, digital twins represent a significant leap forward in the digital transformation of manufacturing and design processes.
Their application in prototyping not only reduces time and costs but also enhances the overall quality and safety of the final product.
As technology advances, the digital twin will undoubtedly play an integral role in the future of smart manufacturing and beyond.
資料ダウンロード
QCD調達購買管理クラウド「newji」は、調達購買部門で必要なQCD管理全てを備えた、現場特化型兼クラウド型の今世紀最高の購買管理システムとなります。
ユーザー登録
調達購買業務の効率化だけでなく、システムを導入することで、コスト削減や製品・資材のステータス可視化のほか、属人化していた購買情報の共有化による内部不正防止や統制にも役立ちます。
NEWJI DX
製造業に特化したデジタルトランスフォーメーション(DX)の実現を目指す請負開発型のコンサルティングサービスです。AI、iPaaS、および先端の技術を駆使して、製造プロセスの効率化、業務効率化、チームワーク強化、コスト削減、品質向上を実現します。このサービスは、製造業の課題を深く理解し、それに対する最適なデジタルソリューションを提供することで、企業が持続的な成長とイノベーションを達成できるようサポートします。
オンライン講座
製造業、主に購買・調達部門にお勤めの方々に向けた情報を配信しております。
新任の方やベテランの方、管理職を対象とした幅広いコンテンツをご用意しております。
お問い合わせ
コストダウンが利益に直結する術だと理解していても、なかなか前に進めることができない状況。そんな時は、newjiのコストダウン自動化機能で大きく利益貢献しよう!
(Β版非公開)