- お役立ち記事
- Examples of IoT usage in the prototyping process in the manufacturing industry
月間77,185名の
製造業ご担当者様が閲覧しています*
*2025年2月28日現在のGoogle Analyticsのデータより
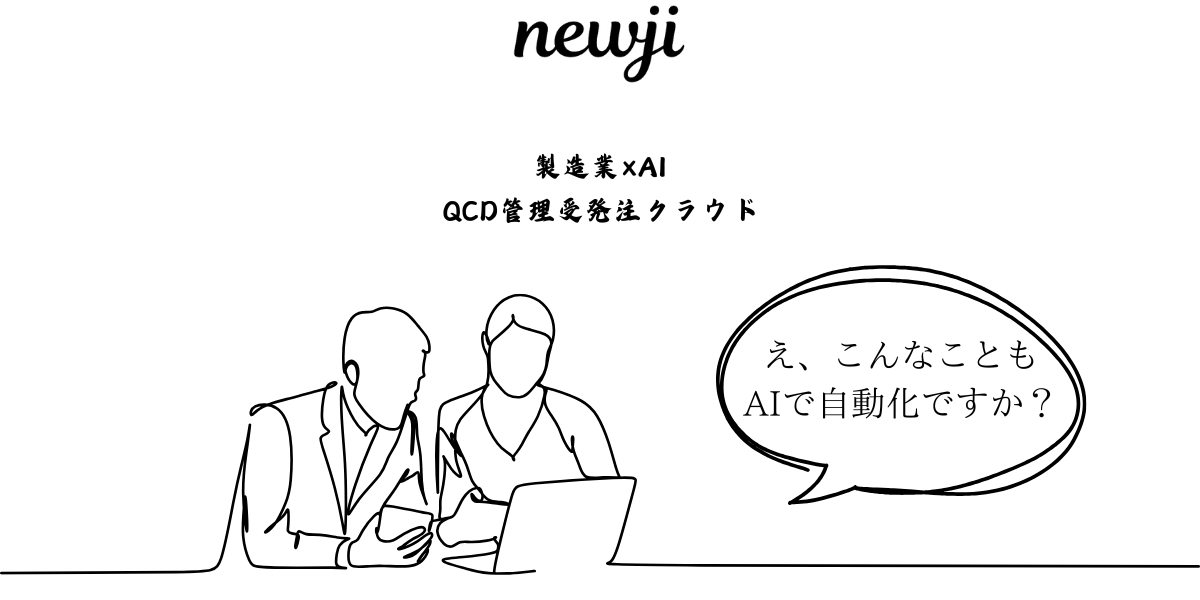
Examples of IoT usage in the prototyping process in the manufacturing industry
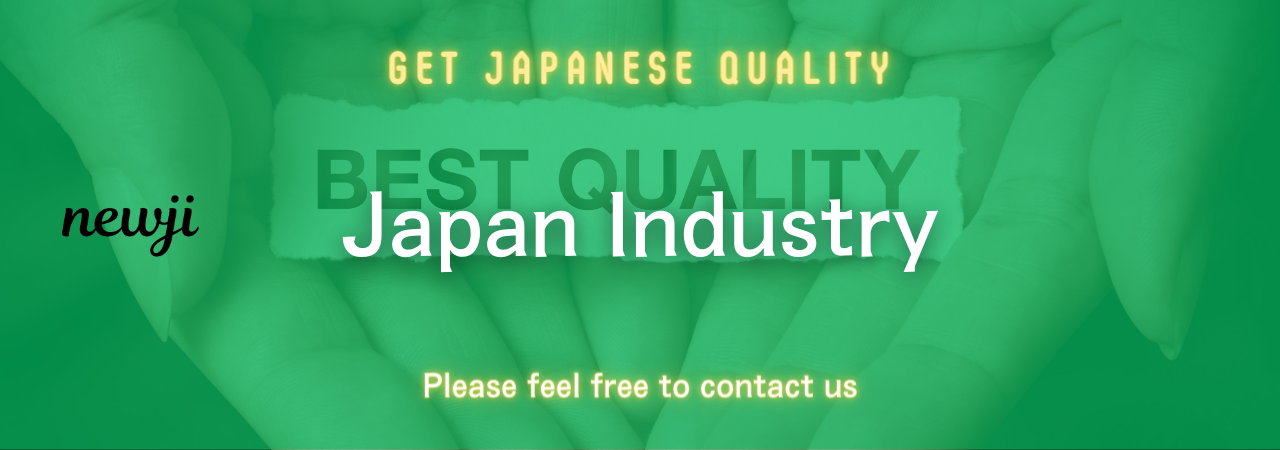
目次
Introduction to IoT in Manufacturing
The Internet of Things (IoT) is making waves across various industries, and manufacturing is no exception.
Its ability to interconnect devices, processes, and systems provides unprecedented opportunities to enhance efficiency, reduce costs, and foster innovation.
In the manufacturing industry, IoT is particularly valuable during the prototyping process, where quick iterations and data-driven insights are essential.
The Role of IoT in Prototyping
Prototyping is a critical phase in the manufacturing process.
It involves creating preliminary models of a product to test concepts and validate designs.
This stage is crucial for identifying potential issues and making necessary improvements before full-scale production.
IoT enhances this process by providing real-time data and connectivity, allowing manufacturers to make informed decisions quickly.
Streamlining Prototyping with IoT
IoT devices can streamline the prototyping process by connecting various components and technologies into a cohesive system.
For example, sensors embedded in prototypes can collect valuable data on performance, which can then be analyzed to improve the design.
This data-driven approach allows for more precise iterations, reducing the time and cost traditionally associated with prototyping.
Enhanced Collaboration and Communication
IoT facilitates better collaboration and communication among different teams involved in the prototyping process.
With IoT, data collected from prototypes can be shared across departments in real-time.
Engineers, designers, and product managers can access the same information and collaborate more effectively.
This transparency ensures that everyone is aligned and working towards the same goals, speeding up the entire process.
Examples of IoT Usage in Prototyping
To understand how IoT is utilized in the prototyping phase, let’s look at some practical examples.
Smart Sensors and Data Collection
One of the most common uses of IoT in prototyping is through smart sensors.
These sensors can be integrated into prototype models to collect data on various parameters—such as temperature, pressure, and vibration—during testing.
This real-time data collection helps in assessing the prototype’s performance under different conditions.
By analyzing this data, manufacturers can identify weaknesses and make necessary modifications to enhance the product design.
Remote Monitoring and Control
IoT enables remote monitoring and control of prototype testing.
Manufacturers can track the performance and status of prototypes from any location.
This capability is particularly beneficial when testing is conducted in remote or hazardous environments.
Remote monitoring also allows for timely interventions, reducing the risk of damage or failure and ensuring that prototypes are functioning as intended.
Predictive Maintenance
Predictive maintenance is another area where IoT proves beneficial during prototyping.
By analyzing data from sensors, manufacturers can predict when a prototype component might fail or require maintenance.
This foresight allows for proactive measures, ensuring that prototypes are always in optimal condition for testing.
Predictive maintenance reduces downtime and extends the lifespan of prototype models.
Challenges and Considerations
While IoT offers numerous benefits in the prototyping process, it also presents its own set of challenges.
Manufacturers must address these to leverage IoT effectively.
Data Security and Privacy
With increased connectivity comes the risk of data breaches and unauthorized access.
Manufacturers must ensure that IoT systems are secure to protect sensitive information.
Implementing robust cybersecurity measures and adhering to industry standards is crucial for safeguarding data.
Integration with Existing Systems
Integrating IoT with existing manufacturing systems can be complex.
Manufacturers need to ensure compatibility and seamless communication between new IoT technologies and their current infrastructure.
This may require investment in new equipment or the modification of existing systems to fully realize the benefits of IoT.
Cost and Resource Implications
Implementing IoT solutions can involve significant upfront costs.
Manufacturers need to consider the financial and resource implications of deploying IoT devices and systems.
While the long-term benefits of IoT are substantial, careful planning and a clear understanding of the return on investment are essential.
Conclusion: The Future of IoT in Manufacturing
The adoption of IoT in the prototyping process is a game-changer for the manufacturing industry.
It offers numerous advantages, from faster iterations and improved collaboration to enhanced data collection and analysis.
Despite the challenges, the potential for increased efficiency, cost savings, and innovation make IoT a valuable tool in modern manufacturing.
As IoT technology continues to evolve and become more accessible, its role in the prototyping phase will only grow.
Manufacturers who embrace IoT stand to gain a competitive edge, leading to better products and faster time-to-market.
The future of manufacturing is interconnected, and IoT is paving the way.
資料ダウンロード
QCD管理受発注クラウド「newji」は、受発注部門で必要なQCD管理全てを備えた、現場特化型兼クラウド型の今世紀最高の受発注管理システムとなります。
ユーザー登録
受発注業務の効率化だけでなく、システムを導入することで、コスト削減や製品・資材のステータス可視化のほか、属人化していた受発注情報の共有化による内部不正防止や統制にも役立ちます。
NEWJI DX
製造業に特化したデジタルトランスフォーメーション(DX)の実現を目指す請負開発型のコンサルティングサービスです。AI、iPaaS、および先端の技術を駆使して、製造プロセスの効率化、業務効率化、チームワーク強化、コスト削減、品質向上を実現します。このサービスは、製造業の課題を深く理解し、それに対する最適なデジタルソリューションを提供することで、企業が持続的な成長とイノベーションを達成できるようサポートします。
製造業ニュース解説
製造業、主に購買・調達部門にお勤めの方々に向けた情報を配信しております。
新任の方やベテランの方、管理職を対象とした幅広いコンテンツをご用意しております。
お問い合わせ
コストダウンが利益に直結する術だと理解していても、なかなか前に進めることができない状況。そんな時は、newjiのコストダウン自動化機能で大きく利益貢献しよう!
(β版非公開)