- お役立ち記事
- Optimization of aluminum corner louver processing and painting process
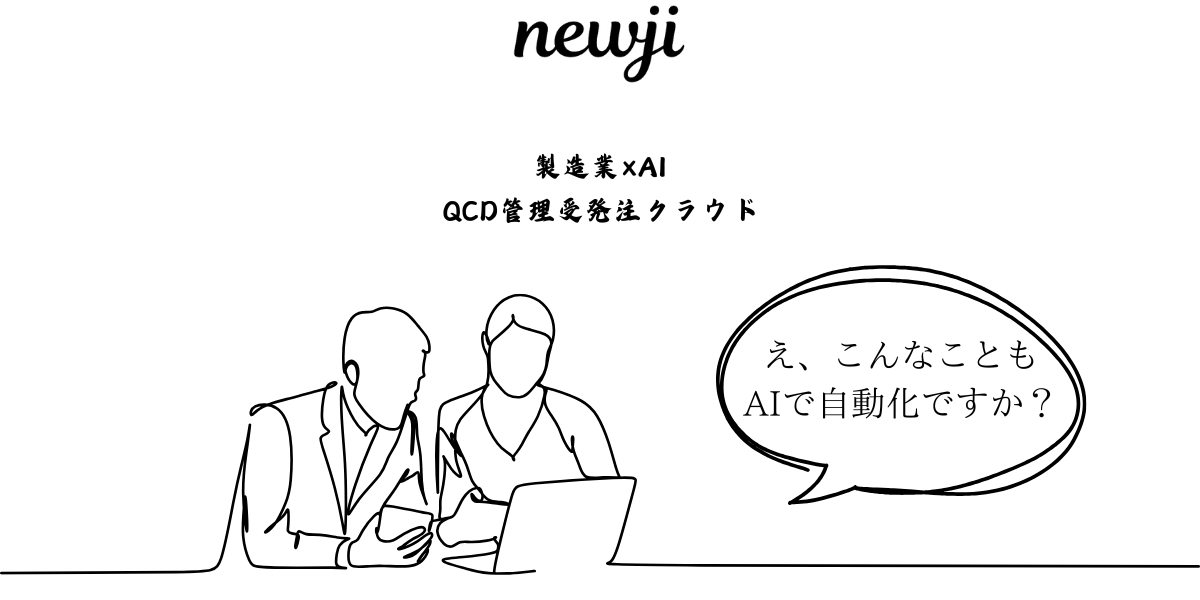
Optimization of aluminum corner louver processing and painting process
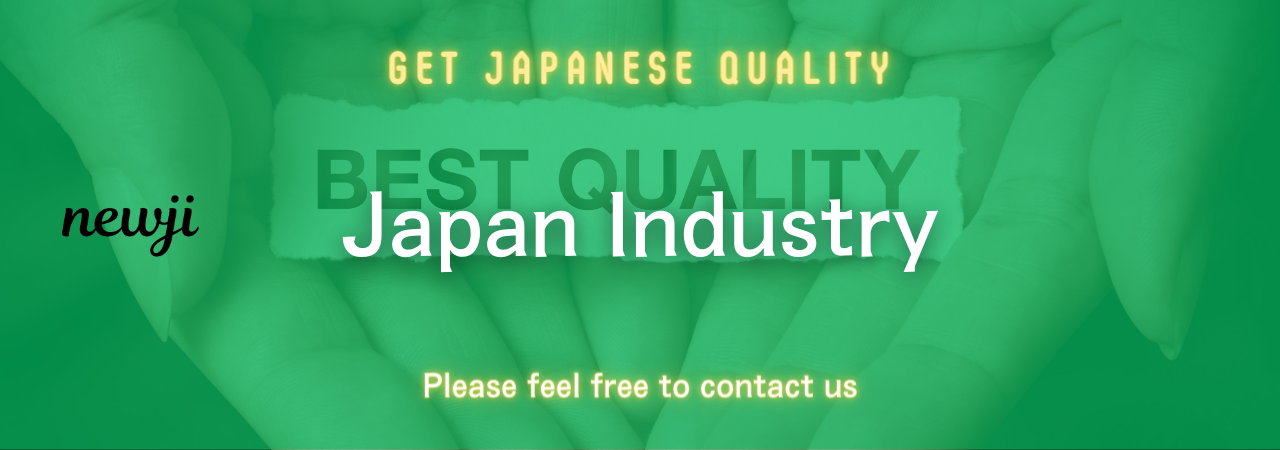
目次
Understanding Aluminum Corner Louvers
Aluminum corner louvers are essential components in various architectural and industrial applications.
They are primarily used for ventilation, sun shading, and adding aesthetic value to buildings.
These structures are made from lightweight, durable aluminum, which is resistant to corrosion.
The manufacturing and processing of aluminum corner louvers require careful attention to detail, especially during the optimization of cutting, assembling, and painting processes.
Properly optimized production processes ensure that these louvers meet quality standards and perform their intended functions effectively.
The Importance of Optimizing the Process
Optimization of the aluminum corner louver processing and painting process is crucial for several reasons.
Firstly, it enhances the quality of the finished product.
By adjusting the process parameters, manufacturers can improve the louver’s durability, appearance, and overall functionality.
Secondly, process optimization reduces production costs.
Efficient use of resources, such as aluminum sheets and paint, minimizes waste, saving both materials and money.
Additionally, optimized processes often lead to faster production times, which helps in meeting customer deadlines without compromising quality.
Lastly, optimizing these processes contributes to environmental sustainability.
Reducing waste and energy consumption during manufacturing processes lessens the environmental impact, an essential consideration in today’s eco-conscious world.
Steps in Aluminum Corner Louver Manufacturing
The production of aluminum corner louvers involves several critical steps, each of which can be optimized for better efficiency and quality.
1. Designing the Louvers
The first step in the manufacturing process is designing the louvers according to specific requirements.
This may involve creating detailed blueprints that outline dimensions, shapes, and other essential features.
Advanced software tools can assist in optimizing this design process by providing accurate simulations of how the louvers will perform in real-world conditions.
By using such tools, designers can identify potential issues early and make necessary adjustments before production begins.
2. Cutting and Shaping Aluminum Sheets
Once the design is finalized, the next step is cutting and shaping aluminum sheets to match the design specifications.
The quality of the louvers largely depends on precision during this stage.
Using state-of-the-art machinery and computer numerical control (CNC) technology ensures that each cut is made precisely as intended.
Optimization here can also involve selecting the right cutting tools and parameters to maximize efficiency and minimize material wastage.
3. Assembling the Louvers
Following the cutting process, the individual components are assembled to form the final louver structure.
This step requires precise alignment and joining techniques to ensure that the assembled louvers are strong and stable.
Advanced techniques like robotic assembly systems and automated welding processes can enhance the efficiency and accuracy of assembly.
Optimizing this phase includes ensuring that assembly lines are well-coordinated and flexible to accommodate different product designs.
4. Surface Preparation and Painting
Painting is a critical part of the aluminum corner louver manufacturing process, not only for aesthetic reasons but also to add an extra layer of protection against environmental factors.
Prior to painting, the louvers must undergo thorough surface preparation.
This involves cleaning and sometimes, pretreating the surface to ensure the paint adheres properly.
Optimizing the painting process typically involves selecting the right type of paint and application technique, such as powder coating or anodizing.
These methods provide long-lasting finishes and can be optimized to reduce paint waste and enhance coverage efficiency.
Strategies for Optimizing the Processes
Improving the efficiency and quality of aluminum corner louver processing and painting can be accomplished through several strategies.
1. Embrace Technological Advancements
Incorporating the latest technological advancements is one of the most effective ways to optimize manufacturing processes.
Automated systems, like robotic cutting and assembly lines, can significantly reduce errors and increase production speed.
Additionally, Internet of Things (IoT) solutions can provide real-time data monitoring, allowing manufacturers to make informed decisions on process enhancements.
2. Continuous Employee Training
The skills and expertise of workers play a vital role in producing high-quality louvers efficiently.
Regular training and development programs can ensure that employees are well-versed in the latest manufacturing techniques and safety protocols.
Educating workers on process optimization technologies and methods will empower them to contribute effectively to ongoing process improvements.
3. Lean Manufacturing Principles
Applying lean manufacturing principles can help eliminate waste and enhance process efficiency.
By focusing on continuous improvement and streamlining workflows, manufacturers can reduce downtime and optimize resource utilization.
Implementing practices such as Just-in-Time (JIT) production and Total Quality Management (TQM) ensures that production processes remain agile and responsive to changes.
Benefits of Process Optimization
Optimizing the processing and painting of aluminum corner louvers yields numerous benefits across various facets of the manufacturing process.
1. Improved Product Quality
Process optimization directly leads to higher product quality by ensuring consistency and precision in every step of production.
The result is a durable, high-performing louver that meets customer expectations and industry standards.
2. Cost Efficiency
Reducing waste and improving resource management through optimization translates to significant cost savings.
Lower production costs make it possible for manufacturers to offer competitive pricing while maintaining profitability.
3. Reduced Environmental Impact
By optimizing processes to minimize energy consumption and material waste, manufacturers contribute positively to environmental sustainability efforts.
This not only helps preserve natural resources but also enhances the company’s brand image as an eco-conscious entity.
Conclusion
Optimizing the aluminum corner louver processing and painting process is vital for manufacturers aiming to stay competitive and meet consumer demands.
By investing in technology, training, and lean practices, companies can produce high-quality louvers efficiently and sustainably.
The benefits of such optimizations extend beyond product quality and cost savings, contributing to a more environmentally friendly industry.
Ultimately, a well-optimized manufacturing process is a win-win for both producers and consumers.
資料ダウンロード
QCD調達購買管理クラウド「newji」は、調達購買部門で必要なQCD管理全てを備えた、現場特化型兼クラウド型の今世紀最高の購買管理システムとなります。
ユーザー登録
調達購買業務の効率化だけでなく、システムを導入することで、コスト削減や製品・資材のステータス可視化のほか、属人化していた購買情報の共有化による内部不正防止や統制にも役立ちます。
NEWJI DX
製造業に特化したデジタルトランスフォーメーション(DX)の実現を目指す請負開発型のコンサルティングサービスです。AI、iPaaS、および先端の技術を駆使して、製造プロセスの効率化、業務効率化、チームワーク強化、コスト削減、品質向上を実現します。このサービスは、製造業の課題を深く理解し、それに対する最適なデジタルソリューションを提供することで、企業が持続的な成長とイノベーションを達成できるようサポートします。
オンライン講座
製造業、主に購買・調達部門にお勤めの方々に向けた情報を配信しております。
新任の方やベテランの方、管理職を対象とした幅広いコンテンツをご用意しております。
お問い合わせ
コストダウンが利益に直結する術だと理解していても、なかなか前に進めることができない状況。そんな時は、newjiのコストダウン自動化機能で大きく利益貢献しよう!
(Β版非公開)