- お役立ち記事
- Tips for developing automation and labor-saving equipment and outsourcing manufacturing
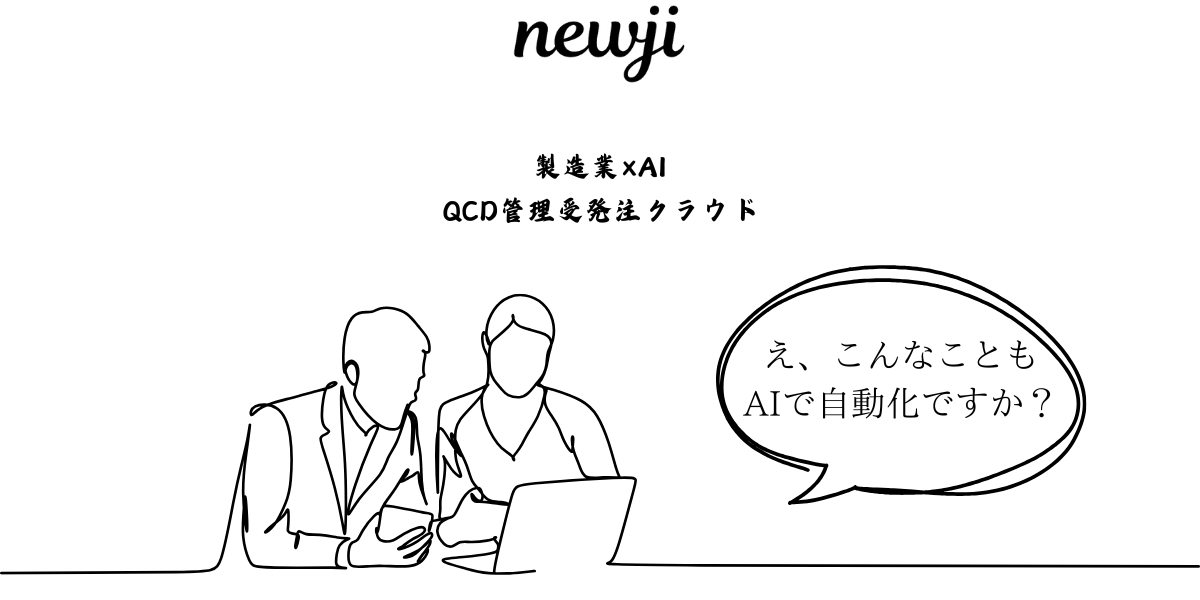
Tips for developing automation and labor-saving equipment and outsourcing manufacturing
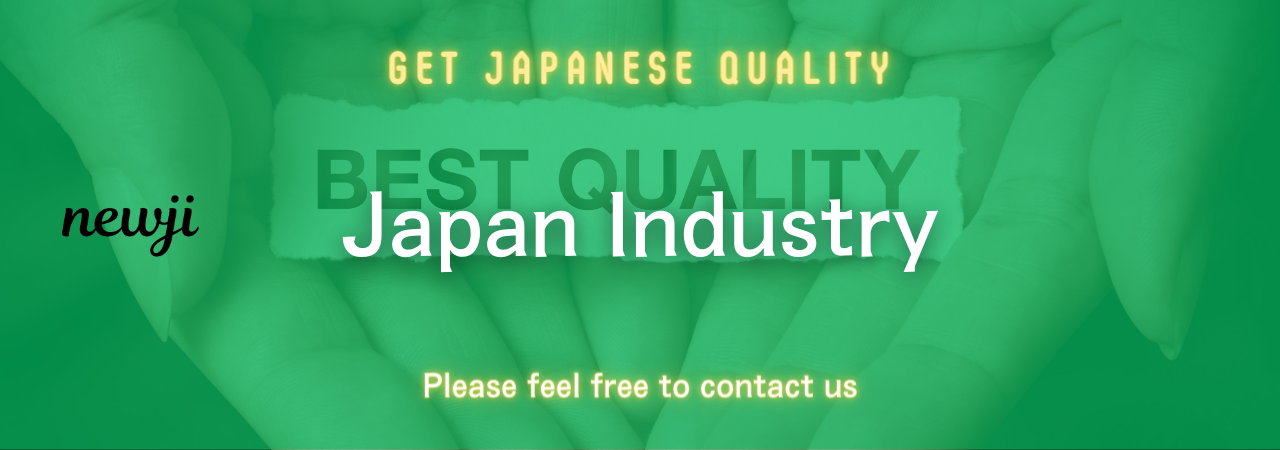
目次
Understanding Automation and Labor-Saving Equipment
Automation and labor-saving equipment have revolutionized the way industries operate today.
These innovations help businesses increase efficiency, reduce costs, and improve productivity.
Automation involves the use of technologies to perform tasks with minimal human intervention.
Labor-saving equipment, on the other hand, assists in reducing the amount of human labor required to complete a specific job.
Industries ranging from manufacturing to agriculture have benefited significantly from these technologies.
For businesses looking to grow and innovate, understanding how to develop and implement such equipment is crucial.
Alongside development, outsourcing manufacturing can be a strategic move to enhance business operations.
The Importance of Automation and Labor-Saving Equipment
The primary advantage of automation and labor-saving equipment is the increase in efficiency.
Tasks that once took hours can now be completed in a fraction of the time, allowing businesses to meet their objectives faster.
Additionally, these technologies can operate continuously without fatigue, ensuring consistent output.
Cost reduction is another significant benefit.
While the initial investment in automation technologies might be high, the long-term savings in labor costs, reduction of waste, and improved energy efficiency can outweigh these expenses.
This return on investment makes automation a viable option for companies looking to enhance their bottom line.
Furthermore, automation helps improve workplace safety.
By handling hazardous or repetitive tasks, machines protect human workers from potential injuries.
This not only ensures a safer working environment but also leads to savings on medical and insurance costs for the business.
Steps to Develop Automation and Labor-Saving Equipment
The process of developing automation and labor-saving equipment involves several critical steps.
1. Needs Assessment
Before investing in automation, businesses should conduct a thorough needs assessment.
This assessment involves identifying tasks that are repetitive or dangerous and determining which processes can benefit the most from automation.
Understanding these needs helps in making informed decisions about which equipment or technology should be developed or acquired.
2. Research and Development
Once the needs are identified, the next step is research and development.
This stage involves exploring existing technologies, potential innovations, and the current market landscape.
Collaborating with experts in the field and conducting pilot tests may be necessary to ensure the equipment developed meets the required standards and offers the desired benefits.
3. Prototype Development
After thorough research, businesses should move on to developing a prototype.
A prototype allows companies to test the functionality of the equipment in a controlled environment.
It is crucial to gather feedback during this phase and make necessary adjustments before the final production.
4. Implementation and Testing
Once the prototype is successful, the next step is full-scale implementation.
During this stage, continuous testing is essential to ensure that the equipment operates as intended in real-world conditions.
Monitoring and adjustments should be made as necessary to fine-tune operations.
5. Employee Training and Integration
Successful integration of automation technology requires training employees to work alongside new equipment.
Workers need to understand how to operate, maintain, and troubleshoot the machinery.
Fostering a culture open to technological adaptation can help ease the transition.
Outsourcing Manufacturing: A Strategic Move
For companies that have successfully developed automation and labor-saving equipment, outsourcing manufacturing can be a strategic decision.
Outsourcing allows businesses to benefit from expertise, reduce costs, and focus on core competencies.
Advantages of Outsourcing
One of the primary benefits of outsourcing manufacturing is access to specialized expertise.
Manufacturing firms have the resources and experience to produce high-quality products efficiently.
By leveraging their capabilities, businesses can ensure their equipment is produced to the highest standards.
Cost reduction is another significant advantage.
Outsourcing can save money by avoiding the expenses associated with setting up and maintaining a manufacturing facility.
By working with established manufacturers, businesses can take advantage of economies of scale, which can result in lower production costs.
Outsourcing also allows companies to focus on their core competencies.
Instead of worrying about manufacturing processes, businesses can concentrate on innovation, marketing, and customer service, leading to competitive advantages in their respective markets.
Considerations When Outsourcing
While outsourcing can offer numerous benefits, it’s essential to consider several factors before making the leap.
1. Selecting the Right Partner
Choosing the right manufacturing partner is crucial.
Businesses should assess potential partners based on their reputation, expertise, and capacity to meet specifications.
Conducting thorough background checks and seeking references can provide valuable insights.
2. Quality Control
Ensuring quality control is critical when outsourcing manufacturing.
Companies should establish clear standards and regular audit processes to verify that production meets the expected quality.
Maintaining open communication with manufacturing partners helps in addressing any quality issues promptly.
3. Intellectual Property Protection
Protecting intellectual property is a significant concern when outsourcing.
It’s essential to have clear agreements in place regarding the use and protection of proprietary technologies and designs.
Legal counsel may be necessary to ensure adequate protection measures are implemented.
Conclusion
In today’s rapidly evolving business landscape, automation and labor-saving equipment, coupled with strategic outsourcing, offer opportunities for growth and innovation.
By understanding the development process and the benefits of manufacturing partnerships, businesses can enhance their operations and stay competitive in the marketplace.
Embracing these advancements can lead to increased efficiency, cost savings, and improved safety, setting the stage for long-term success.
資料ダウンロード
QCD調達購買管理クラウド「newji」は、調達購買部門で必要なQCD管理全てを備えた、現場特化型兼クラウド型の今世紀最高の購買管理システムとなります。
ユーザー登録
調達購買業務の効率化だけでなく、システムを導入することで、コスト削減や製品・資材のステータス可視化のほか、属人化していた購買情報の共有化による内部不正防止や統制にも役立ちます。
NEWJI DX
製造業に特化したデジタルトランスフォーメーション(DX)の実現を目指す請負開発型のコンサルティングサービスです。AI、iPaaS、および先端の技術を駆使して、製造プロセスの効率化、業務効率化、チームワーク強化、コスト削減、品質向上を実現します。このサービスは、製造業の課題を深く理解し、それに対する最適なデジタルソリューションを提供することで、企業が持続的な成長とイノベーションを達成できるようサポートします。
オンライン講座
製造業、主に購買・調達部門にお勤めの方々に向けた情報を配信しております。
新任の方やベテランの方、管理職を対象とした幅広いコンテンツをご用意しております。
お問い合わせ
コストダウンが利益に直結する術だと理解していても、なかなか前に進めることができない状況。そんな時は、newjiのコストダウン自動化機能で大きく利益貢献しよう!
(Β版非公開)