- お役立ち記事
- Basics and practice of quality control at the prototype stage
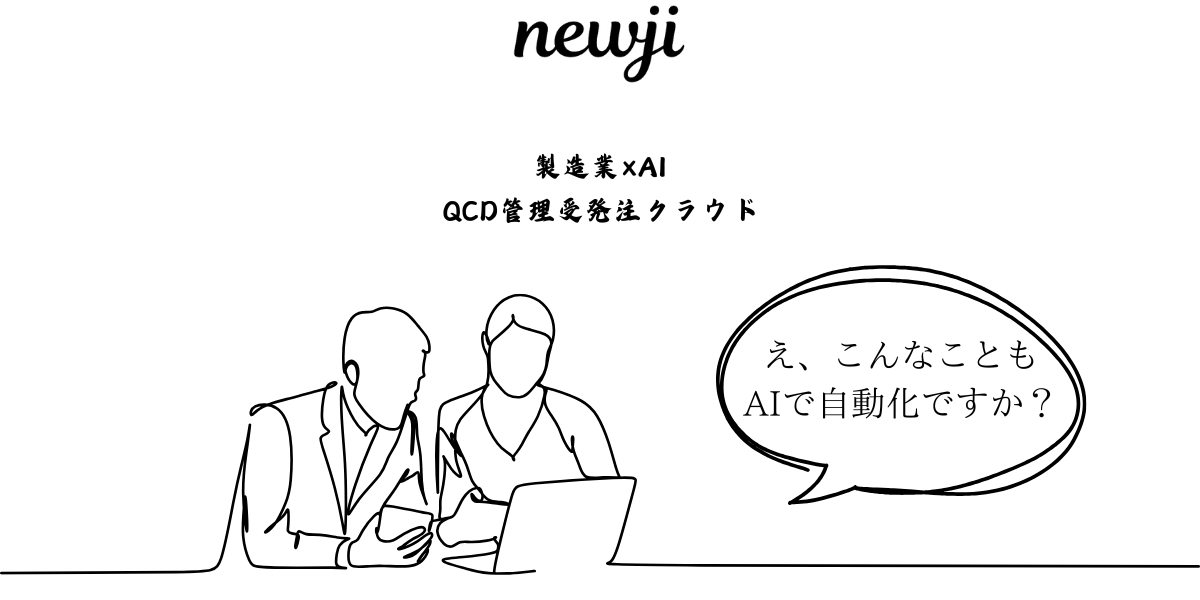
Basics and practice of quality control at the prototype stage
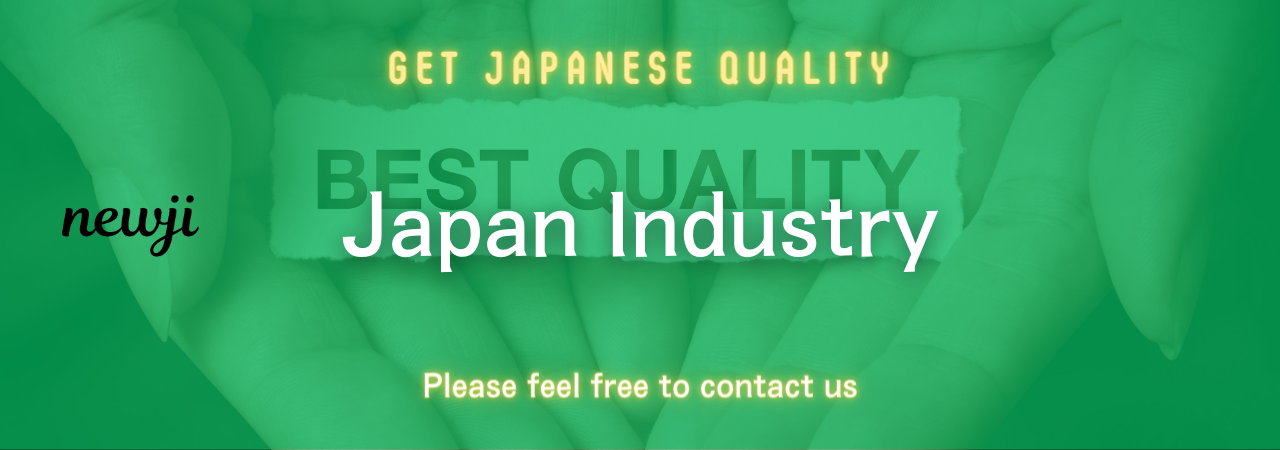
目次
Understanding Quality Control in the Prototype Stage
Quality control is a critical aspect of product development, especially during the prototype stage.
It ensures that the final product meets the desired standards of quality, reliability, and performance.
By implementing effective quality control measures early in the product development process, companies can save time, reduce costs, and prevent potential issues that may arise in later stages.
In this article, we will discuss the basics and practice of quality control during the prototype stage.
What is Quality Control?
Quality control refers to the process of ensuring that a product meets specified requirements and standards.
It involves checking and testing the product at various stages of development to identify and address any defects or issues.
The goal is to deliver a product that is not only functional but also reliable and safe for use.
In the prototype stage, quality control allows developers to identify potential problems and make necessary improvements before moving on to mass production.
This stage is crucial because it sets the foundation for the quality of the final product.
The Basics of Quality Control During the Prototype Stage
To implement quality control effectively at the prototype stage, it is important to understand the basic principles involved.
These include setting clear quality standards, conducting thorough testing, and making data-driven improvements.
Setting Quality Standards
Setting quality standards is the first step in the quality control process.
These standards serve as benchmarks that the prototype must meet to ensure it meets customer expectations.
Quality standards typically cover aspects such as design, functionality, reliability, and safety.
To determine these standards, a company should consider:
– Customer needs and expectations
– Industry regulations and standards
– Company goals and objectives
Once these standards have been established, they should be communicated clearly to all members of the development team.
Conducting Testing and Inspections
Testing is a critical component of quality control during the prototype stage.
It involves evaluating the prototype against set standards to identify any deviations or issues.
There are several testing methods that can be used, including:
– Functional testing: This type of testing assesses whether the prototype performs its intended function correctly.
– Stress testing: This evaluates the prototype’s performance under extreme conditions to identify any weaknesses or potential failures.
– Usability testing: This focuses on the user experience and usability of the prototype, ensuring it is easy to use and meets user expectations.
Regular inspections should also be conducted throughout the prototype development process to ensure all components are being manufactured according to quality standards.
Making Data-Driven Improvements
Quality control is not just about identifying defects; it also involves making improvements based on data gathered through testing and inspections.
This requires analyzing the results from testing and inspections to understand the root causes of any issues.
Once the causes have been identified, potential solutions can be developed and implemented to address the problems.
This could involve redesigning certain components, changing materials, or modifying manufacturing processes.
Best Practices for Quality Control in the Prototype Stage
Implementing best practices for quality control can enhance the effectiveness of your efforts during the prototype stage.
Here are some key practices to consider:
Involve Cross-Functional Teams
Quality control should not be the responsibility of one individual or department alone.
It is important to involve cross-functional teams from areas such as engineering, design, manufacturing, and marketing.
This ensures diverse perspectives are considered and that potential quality issues are identified and addressed early.
Document and Monitor Progress
Maintaining accurate documentation of the quality control process is essential.
All tests, inspections, and modifications should be recorded and monitored regularly.
This ensures that progress is tracked, and any issues are addressed promptly.
Having a documented history also provides valuable insights for future projects and can help prevent similar issues from arising.
Engage with Customers and Feedback
Customer feedback is invaluable when it comes to quality control.
It provides insights into how well the prototype meets customer expectations and can highlight areas of improvement.
Engage with customers during the prototype stage by collecting their feedback and implementing their suggestions where feasible.
This practice demonstrates a commitment to delivering a high-quality product that meets their needs.
The Importance of Quality Control in the Prototype Stage
The importance of quality control during the prototype stage cannot be overstated.
By implementing effective quality control measures, companies can ensure that their final product is of the highest quality.
This not only enhances the reputation of the company but also ensures customer satisfaction and loyalty.
Without proper quality control, defects and issues may go unnoticed until mass production, leading to costly recalls and lost revenue.
Investing in quality control during the prototype stage is essential for long-term success in the competitive market.
Conclusion
Quality control at the prototype stage is a foundational element of successful product development.
By following the steps outlined in this article, including setting quality standards, conducting thorough testing, and making data-driven improvements, companies can identify and address issues early, ensuring a high-quality final product.
By adopting best practices, such as involving cross-functional teams, documenting progress, and engaging with customers, companies can further enhance their quality control processes.
In doing so, they can deliver products that meet – and exceed – customer expectations.
資料ダウンロード
QCD調達購買管理クラウド「newji」は、調達購買部門で必要なQCD管理全てを備えた、現場特化型兼クラウド型の今世紀最高の購買管理システムとなります。
ユーザー登録
調達購買業務の効率化だけでなく、システムを導入することで、コスト削減や製品・資材のステータス可視化のほか、属人化していた購買情報の共有化による内部不正防止や統制にも役立ちます。
NEWJI DX
製造業に特化したデジタルトランスフォーメーション(DX)の実現を目指す請負開発型のコンサルティングサービスです。AI、iPaaS、および先端の技術を駆使して、製造プロセスの効率化、業務効率化、チームワーク強化、コスト削減、品質向上を実現します。このサービスは、製造業の課題を深く理解し、それに対する最適なデジタルソリューションを提供することで、企業が持続的な成長とイノベーションを達成できるようサポートします。
オンライン講座
製造業、主に購買・調達部門にお勤めの方々に向けた情報を配信しております。
新任の方やベテランの方、管理職を対象とした幅広いコンテンツをご用意しております。
お問い合わせ
コストダウンが利益に直結する術だと理解していても、なかなか前に進めることができない状況。そんな時は、newjiのコストダウン自動化機能で大きく利益貢献しよう!
(Β版非公開)