- お役立ち記事
- Utilization and case studies of multi-objective optimization technology in the prototyping process
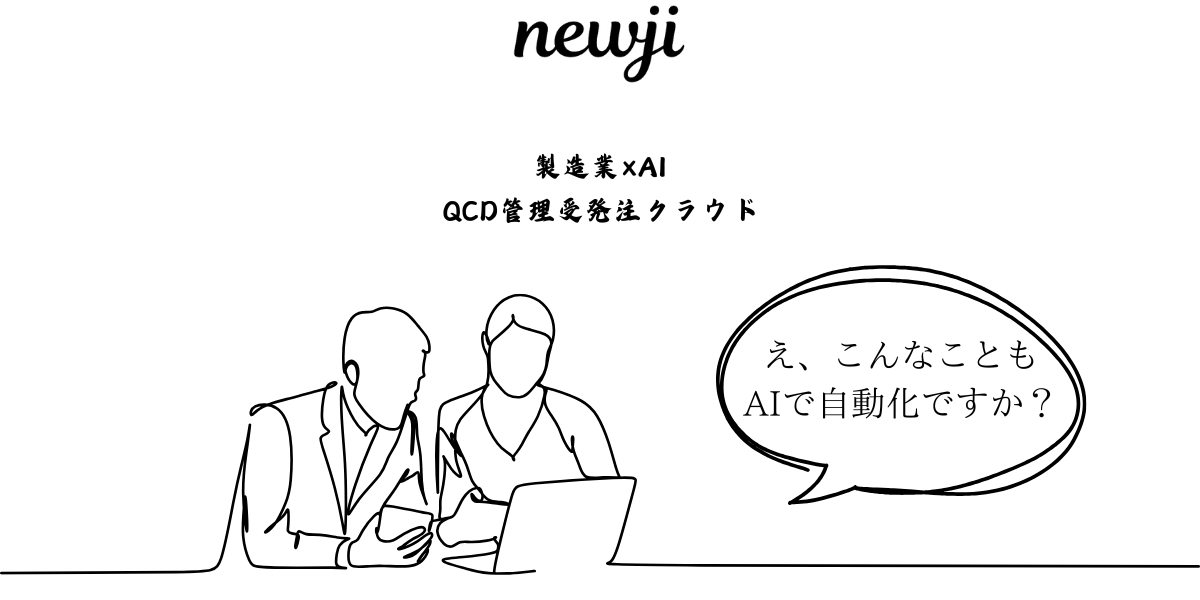
Utilization and case studies of multi-objective optimization technology in the prototyping process
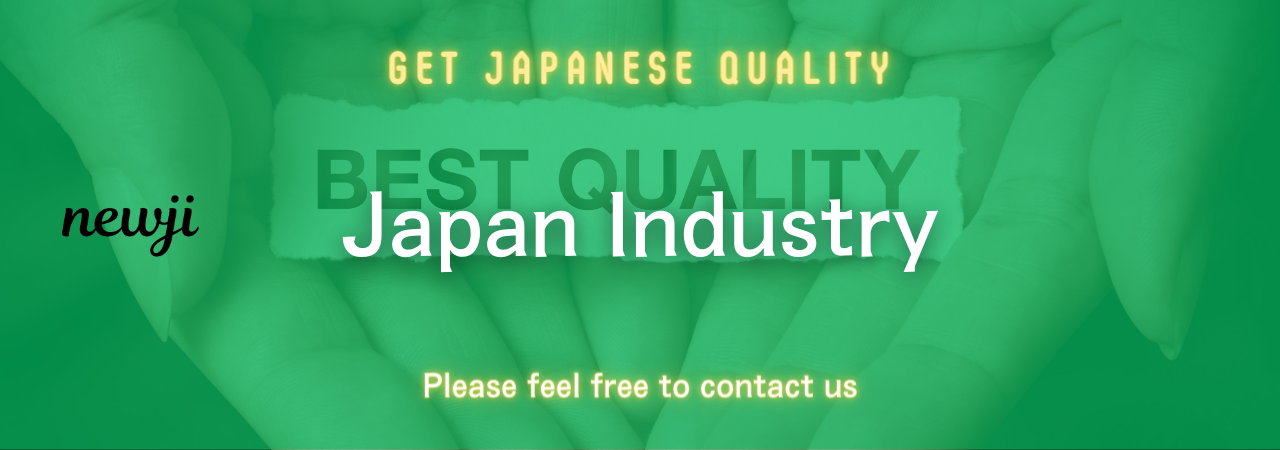
目次
Understanding Multi-Objective Optimization
Multi-objective optimization is a powerful technique used in various fields to tackle problems with multiple conflicting objectives.
In the prototyping process, it allows designers and engineers to balance different goals such as cost, performance, and sustainability.
The essence of this technology is to identify the best trade-offs among the competing objectives, providing a set of optimal solutions.
These solutions are often visualized as a Pareto front, a curve that represents the best possible compromises.
Multi-objective optimization doesn’t lead to a single “best” solution but offers a spectrum of options, enabling decision-makers to choose based on preference and context.
Importance in the Prototyping Process
In the prototyping stage, designers often face numerous decisions with various competing factors.
For instance, they must consider the balance between cost and performance, or the trade-off between speed and accuracy.
With multi-objective optimization, it’s possible to systematically evaluate these factors and identify the optimal balance.
This approach leads to more informed decision-making, reducing the time and resources spent on iterations.
It improves the efficiency of the prototyping process by allowing engineers to pinpoint areas where they can afford to compromise and where they need to maximize performance.
Applications of Multi-Objective Optimization
Automotive Industry
In the automotive industry, multi-objective optimization is crucial in designing vehicles that meet both performance and regulatory standards.
Designers must balance the power output, fuel efficiency, and environmental impact of new models.
This technology enables them to explore different design options and select those that offer the best trade-offs for their specific goals.
For example, optimizing the aerodynamics of a car can significantly improve fuel efficiency while maintaining aesthetic appeal.
Similarly, this technique helps minimize costs without compromising on safety or durability.
Aerospace
In aerospace, multi-objective optimization is key in developing aircraft that are both efficient and safe.
Engineers must consider multiple factors, such as weight, fuel consumption, and payload capacity.
By applying this technology, aerospace engineers can find the best configuration that balances these objectives.
For example, optimizing an aircraft’s weight distribution can improve its stability and fuel efficiency.
This approach also facilitates the integration of new technologies while ensuring compliance with safety standards.
Renewable Energy
The renewable energy sector benefits immensely from multi-objective optimization.
Energy systems must balance efficiency, cost, and environmental impact.
Optimization algorithms help in determining the most effective ways to distribute resources and manage energy output.
For instance, a wind farm’s design can be optimized for maximum energy production while minimizing environmental disruptions.
Moreover, this technique assists in predicting the best locations for renewable energy installations, taking into account factors like land use and ecological impact.
Manufacturing
In manufacturing, multi-objective optimization offers insights into process improvements and cost-saving opportunities.
Manufacturers must secure high-quality outputs while minimizing production costs and waste.
By optimizing design and manufacturing parameters, producers can achieve these goals more efficiently.
For example, in additive manufacturing, optimizing the layer thickness and orientation can significantly affect material usage and build time.
This advanced method helps manufacturers increase production efficiency and product quality, ultimately leading to better competitiveness in the market.
Challenges and Considerations
Despite its benefits, multi-objective optimization does come with challenges.
One primary challenge is the computational complexity involved in solving these problems.
The calculations needed to explore the trade-offs between different objectives can be intensive, requiring significant computing resources.
Another consideration is the decision-makers’ ability to interpret and use the outcomes effectively.
Additionally, identifying the most suitable algorithms for specific prototyping needs reduces trial and error, thus saving time and resources.
Finally, integrating multi-objective optimization into existing processes requires strategic planning and can be resource-intensive.
Real-World Case Studies
Case Study 1: Electric Vehicle Prototyping
A prominent electric vehicle manufacturer utilized multi-objective optimization to design a new battery system.
The objective was to maximize the battery life while minimizing the overall weight and cost.
Using optimization algorithms, they identified the best battery configurations that met these criteria, resulting in a more efficient and cost-effective model.
This approach also enabled quick adaptation to changing market and technology trends, streamlining the prototyping process.
Case Study 2: Airplane Wing Design
In aerospace, a major company used multi-objective optimization to improve the design of an airplane wing.
Their goals were to minimize the weight while maximizing strength and aerodynamic efficiency.
Through this process, they discovered innovative materials and design structures that provided the desired balance between the objectives.
The result was a wing design that enhanced overall aircraft performance and fuel efficiency.
Case Study 3: Solar Panel Layout
A solar energy company applied multi-objective optimization to optimize the layout of solar panels on a new solar farm.
Their objectives included maximizing energy output and minimizing land use.
The optimization process helped them find the optimal panel arrangement that provided the highest solar capture with minimal environmental impact.
This resulted in increased energy efficiency and reduced operational costs, benefiting both the company and the environment.
Future Directions
As technology continues to evolve, multi-objective optimization will become even more integrated into the prototyping process.
With advances in computational power and algorithms, the scope and scale of optimization will expand.
Emerging fields like artificial intelligence and machine learning offer new pathways for enhancing multi-objective optimization.
These advancements promise even more sophisticated methods for solving complex prototyping challenges.
The prototyping process, powered by multi-objective optimization, is set to drive innovation across industries.
By embracing this approach, companies will not only streamline their design processes but also create more competitive and sustainable products.
As multi-objective optimization becomes mainstream, its impact on product development and innovation will continue to grow, shaping the future of industries worldwide.
資料ダウンロード
QCD調達購買管理クラウド「newji」は、調達購買部門で必要なQCD管理全てを備えた、現場特化型兼クラウド型の今世紀最高の購買管理システムとなります。
ユーザー登録
調達購買業務の効率化だけでなく、システムを導入することで、コスト削減や製品・資材のステータス可視化のほか、属人化していた購買情報の共有化による内部不正防止や統制にも役立ちます。
NEWJI DX
製造業に特化したデジタルトランスフォーメーション(DX)の実現を目指す請負開発型のコンサルティングサービスです。AI、iPaaS、および先端の技術を駆使して、製造プロセスの効率化、業務効率化、チームワーク強化、コスト削減、品質向上を実現します。このサービスは、製造業の課題を深く理解し、それに対する最適なデジタルソリューションを提供することで、企業が持続的な成長とイノベーションを達成できるようサポートします。
オンライン講座
製造業、主に購買・調達部門にお勤めの方々に向けた情報を配信しております。
新任の方やベテランの方、管理職を対象とした幅広いコンテンツをご用意しております。
お問い合わせ
コストダウンが利益に直結する術だと理解していても、なかなか前に進めることができない状況。そんな時は、newjiのコストダウン自動化機能で大きく利益貢献しよう!
(Β版非公開)