- お役立ち記事
- Dynamic testing of prototype parts and durability performance evaluation methods
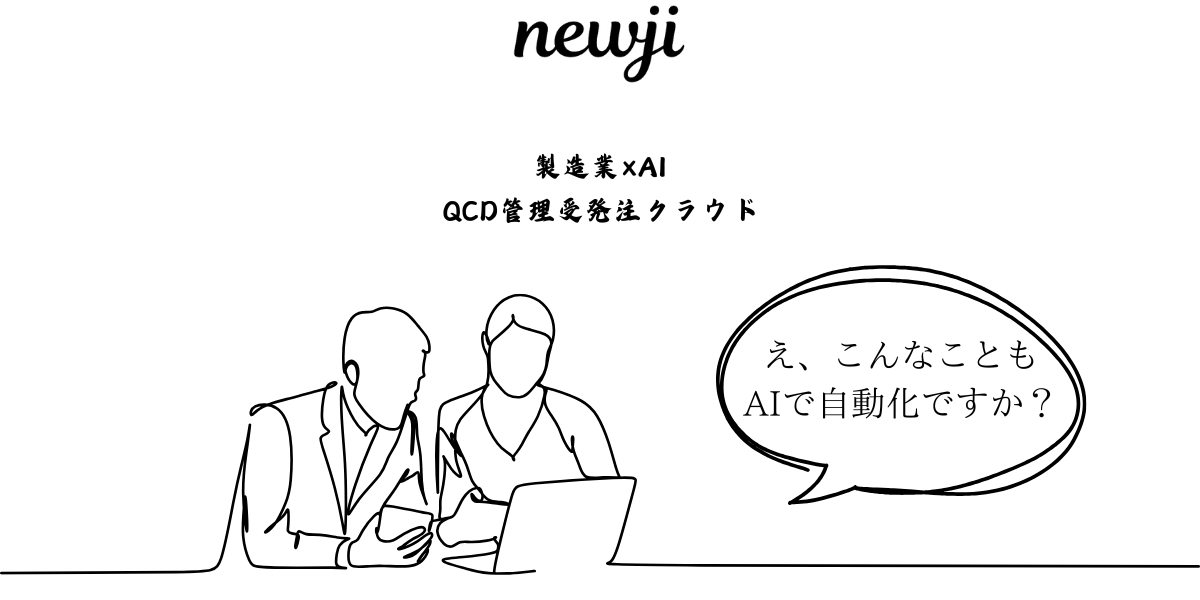
Dynamic testing of prototype parts and durability performance evaluation methods
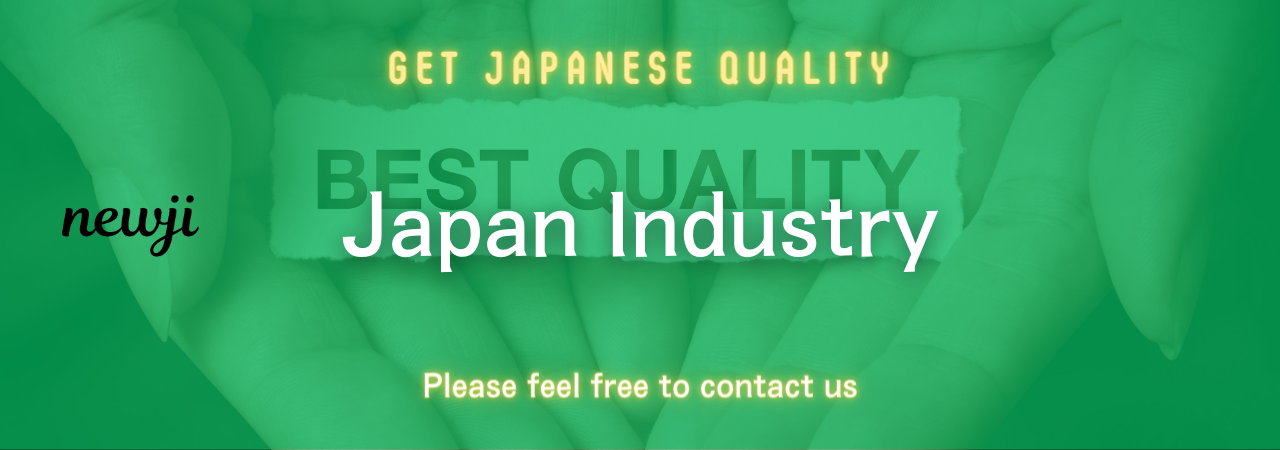
目次
Introduction to Dynamic Testing
Dynamic testing is a critical process in evaluating prototype parts.
It involves assessing the behavior of these parts under various conditions to ensure they meet the required specifications and performance standards.
This type of testing allows engineers to identify potential issues that can affect the functionality and durability of a product.
By simulating real-world conditions, dynamic testing offers valuable insights into how a part will perform during its lifecycle.
Why Dynamic Testing is Important
Dynamic testing is essential because it helps verify the reliability and safety of prototype parts.
Without this testing, products may fail to perform adequately, leading to customer dissatisfaction or safety hazards.
Additionally, it helps in optimizing the design by revealing weaknesses that may not be apparent in static tests.
This allows for improvements before mass production, saving time and resources.
Methods of Dynamic Testing
Several methodologies are utilized to conduct dynamic tests on prototype parts, each serving a unique purpose.
Some of the most common methods include vibration testing, fatigue testing, and thermal cycling.
Understanding these methods helps in selecting the appropriate test for a specific part and its application.
Vibration Testing
Vibration testing involves subjecting a prototype part to vibrations similar to those it will experience in its operational environment.
This test helps identify how the part responds to forces that can cause it to fail.
Engineers can detect issues like resonance, which can lead to structural failures or undue stress on components.
Through this testing, adjustments can be made to the prototype to enhance its vibration resistance.
Fatigue Testing
Fatigue testing examines how a part withstands repeated cycles of stress.
It is crucial for parts expected to endure repetitive loading and unloading during their service life.
This testing is aimed at determining the lifecycle of a component and identifying when it might fail due to material fatigue.
It helps manufacturers ensure that their products remain safe and effective over time.
Thermal Cycling
Thermal cycling involves exposing a part to extreme temperature changes to test its thermal tolerance and resistance.
This is important for parts likely to undergo frequent temperature fluctuations in their usage environment.
Thermal cycling can reveal issues such as thermal expansion and contraction, which may cause cracks or other forms of deterioration over time.
Making necessary design enhancements based on thermal testing is critical for durability.
Evaluating Durability Performance
Durability performance evaluation focuses on how long a prototype part can maintain its functionality under expected use conditions.
This involves several tests and methods to simulate long-term wear and tear.
By doing so, manufacturers can predict the lifespan of the part and ensure it meets or exceeds expectations.
Significance of Durability Testing
Durability testing is significant because it directly influences product reliability and consumer trust.
Products that fail prematurely can result in costly recalls and damage to a brand’s reputation.
Manufacturers strive to produce durable products to avoid these outcomes and ensure customer satisfaction.
Common Durability Tests
Durability tests often include stress testing, environmental exposure tests, and lifecycle testing.
Each of these tests has a specific role in assessing a prototype’s ability to withstand different scenarios over time.
Stress Testing
Stress testing involves applying forces to a part to understand its strength limits.
This method identifies how much load a prototype can endure before it breaks or deforms.
Stress testing is essential for ensuring that parts can withstand the maximum expected operational loads.
Environmental Exposure Tests
These tests assess how a prototype part performs under various environmental conditions, such as humidity, salt spray, or UV light exposure.
This testing helps ensure that a product remains functional and stable in different climates and conditions it may face.
Lifecycle Testing
Lifecycle testing simulates the entire operational life of a part within a condensed timeframe.
It helps to identify any failure modes that could occur over time, allowing engineers to make design tweaks for enhanced durability.
Conclusion
Dynamic testing and durability performance evaluation are vital for developing reliable and successful prototype parts.
By accurately simulating real-world scenarios, these tests ensure that parts meet safety, quality, and performance standards.
Manufacturers can optimize product design, avoid costly failures, and enhance customer satisfaction by investing in comprehensive testing methods.
Ensuring that a prototype undergoes thorough testing is crucial for its success in the marketplace.
資料ダウンロード
QCD調達購買管理クラウド「newji」は、調達購買部門で必要なQCD管理全てを備えた、現場特化型兼クラウド型の今世紀最高の購買管理システムとなります。
ユーザー登録
調達購買業務の効率化だけでなく、システムを導入することで、コスト削減や製品・資材のステータス可視化のほか、属人化していた購買情報の共有化による内部不正防止や統制にも役立ちます。
NEWJI DX
製造業に特化したデジタルトランスフォーメーション(DX)の実現を目指す請負開発型のコンサルティングサービスです。AI、iPaaS、および先端の技術を駆使して、製造プロセスの効率化、業務効率化、チームワーク強化、コスト削減、品質向上を実現します。このサービスは、製造業の課題を深く理解し、それに対する最適なデジタルソリューションを提供することで、企業が持続的な成長とイノベーションを達成できるようサポートします。
オンライン講座
製造業、主に購買・調達部門にお勤めの方々に向けた情報を配信しております。
新任の方やベテランの方、管理職を対象とした幅広いコンテンツをご用意しております。
お問い合わせ
コストダウンが利益に直結する術だと理解していても、なかなか前に進めることができない状況。そんな時は、newjiのコストダウン自動化機能で大きく利益貢献しよう!
(Β版非公開)