- お役立ち記事
- Leaf spring prototype production: Points to consider when choosing the best partner for design and manufacturing
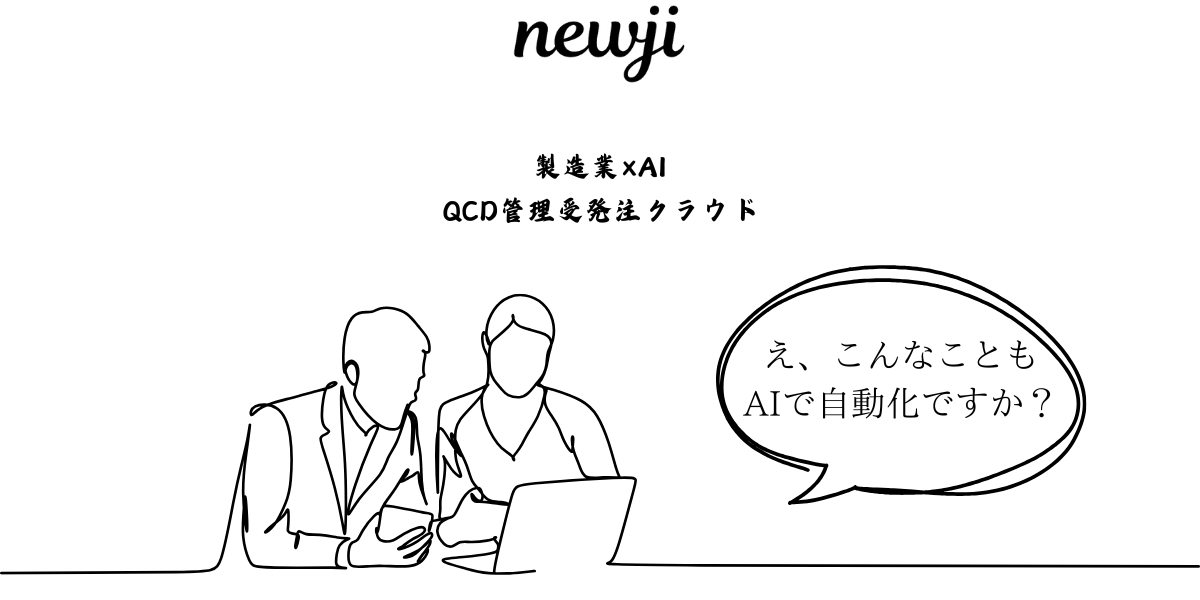
Leaf spring prototype production: Points to consider when choosing the best partner for design and manufacturing
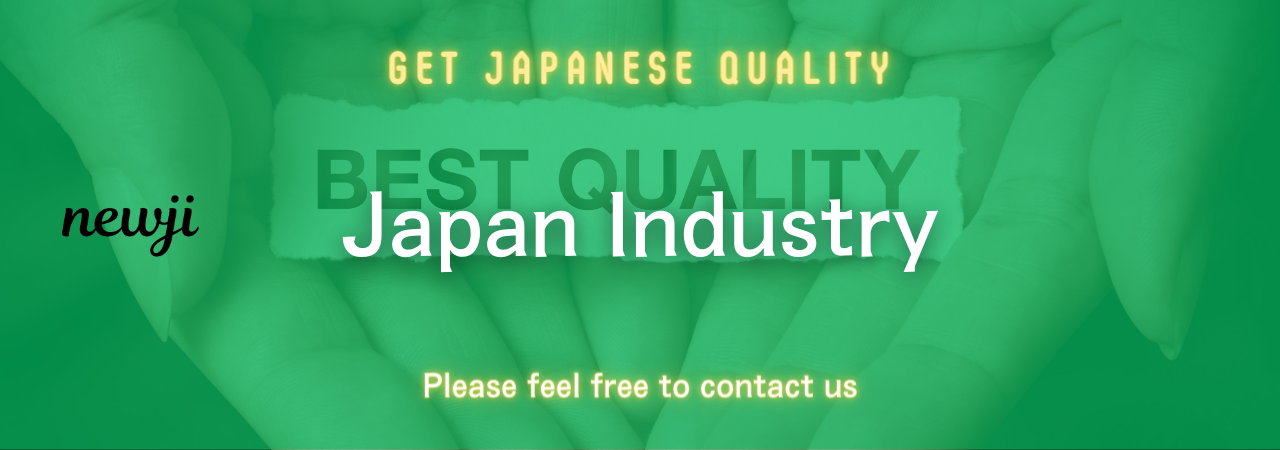
目次
Understanding Leaf Spring Prototype Production
Leaf springs are a crucial component in vehicle suspension systems, and their design and manufacturing play a significant role in the performance and safety of the vehicle.
In prototype production, leaf springs are created to test designs before full-scale manufacturing.
This process allows engineers and designers to refine and adjust specifications, ensuring optimal functionality and efficiency.
Choosing the right partner for leaf spring prototype production can significantly impact the outcome of your project.
The Importance of a Reliable Partner
A reliable partner in leaf spring prototype production offers several benefits.
Firstly, they ensure timely delivery, helping to keep the project on schedule.
Secondly, they provide quality assurance, ensuring that each prototype meets your exact specifications.
Additionally, an experienced partner can offer valuable insights and suggestions for improvements, drawing from their expertise and industry knowledge.
Factors to Consider When Selecting a Partner
When selecting a partner for leaf spring prototype production, there are several essential factors to consider.
These factors will help ensure that you choose a company that aligns with your specific needs and project goals.
Experience and Expertise
One of the most crucial factors in selecting a partner is their experience and expertise in the field.
Look for a company that has a proven track record in designing and manufacturing leaf springs.
Their experience in working with various industries and applications can provide valuable insights into your project.
Check their portfolio and past projects to assess their capabilities and quality of work.
Technology and Equipment
The partner’s investment in modern technology and equipment is another critical consideration.
Advanced equipment allows for precision and accuracy in manufacturing, which is vital in prototype production.
It ensures that the prototypes accurately reflect the final product, verifying their design and functionality.
Additionally, check if the partner utilizes innovative technologies such as computer-aided design (CAD) and computer-aided manufacturing (CAM) systems.
Quality Control Processes
A partner’s commitment to quality control is essential in prototype production.
Look for a company that implements rigorous quality control processes at every stage of production.
Their ability to detect and correct errors early on will save time and resources.
Ask about their quality assurance certifications, such as ISO or other industry-specific standards, to ensure they adhere to recognized quality benchmarks.
Customization Capabilities
Every project is unique, and having a partner that offers customization capabilities can be a significant advantage.
They should be able to tailor their services to meet your specific design requirements and project goals.
This flexibility allows for adjustments and iterations during the prototype phase, ensuring the final product aligns with your expectations.
Communication and Collaboration
Effective communication and collaboration are crucial for a successful partnership.
Choose a partner that emphasizes clear and open lines of communication.
They should involve you in each step of the process, providing regular updates and seeking feedback.
This collaborative approach ensures that the prototype evolves according to your vision and requirements.
Cost and Budget Considerations
While it’s important to find a partner that meets your technical and quality requirements, cost considerations also play a crucial role.
Understanding the cost structure and pricing models of potential partners will help you make an informed decision.
Transparent Pricing
Seek a partner that offers transparent pricing and clear cost estimates up front.
They should provide detailed breakdowns of costs, including materials, labor, and any additional services.
This transparency helps avoid unexpected expenses and ensures the project stays within budget.
Value for Money
Rather than simply looking for the cheapest option, focus on finding a partner that offers value for money.
Evaluate their expertise, technology, and quality assurance in relation to their pricing.
A slightly higher initial cost might result in a more efficient and durable prototype, ultimately saving you money in the long run.
Conducting Research and Due Diligence
Before finalizing your decision, conduct thorough research and due diligence on potential partners.
This step ensures you choose a company that aligns with your project’s needs and expectations.
References and Reviews
Seek references from past clients and review testimonials on the partner’s website.
Additionally, consider consulting industry forums and review sites for unbiased opinions.
This feedback from other businesses can provide valuable insights into the partner’s reliability and service quality.
Site Visits
If possible, arrange a site visit to the partner’s facilities.
This visit allows you to assess their operations, equipment, and quality control processes firsthand.
Meeting their team also provides an opportunity to gauge their professionalism and expertise.
Conclusion
Selecting the best partner for leaf spring prototype production involves careful consideration of several factors.
From experience and expertise to technology, communication, and cost, each element plays a vital role in the success of your project.
By conducting thorough research, checking references, and evaluating their capabilities, you can choose a partner that aligns with your vision, ensuring a successful and efficient prototype production process.
Remember, the right partner not only provides the product but also adds value through insights and innovation, paving the way for the successful development of your final product.
資料ダウンロード
QCD調達購買管理クラウド「newji」は、調達購買部門で必要なQCD管理全てを備えた、現場特化型兼クラウド型の今世紀最高の購買管理システムとなります。
ユーザー登録
調達購買業務の効率化だけでなく、システムを導入することで、コスト削減や製品・資材のステータス可視化のほか、属人化していた購買情報の共有化による内部不正防止や統制にも役立ちます。
NEWJI DX
製造業に特化したデジタルトランスフォーメーション(DX)の実現を目指す請負開発型のコンサルティングサービスです。AI、iPaaS、および先端の技術を駆使して、製造プロセスの効率化、業務効率化、チームワーク強化、コスト削減、品質向上を実現します。このサービスは、製造業の課題を深く理解し、それに対する最適なデジタルソリューションを提供することで、企業が持続的な成長とイノベーションを達成できるようサポートします。
オンライン講座
製造業、主に購買・調達部門にお勤めの方々に向けた情報を配信しております。
新任の方やベテランの方、管理職を対象とした幅広いコンテンツをご用意しております。
お問い合わせ
コストダウンが利益に直結する術だと理解していても、なかなか前に進めることができない状況。そんな時は、newjiのコストダウン自動化機能で大きく利益貢献しよう!
(Β版非公開)