- お役立ち記事
- Latest examples in automotive parts prototyping
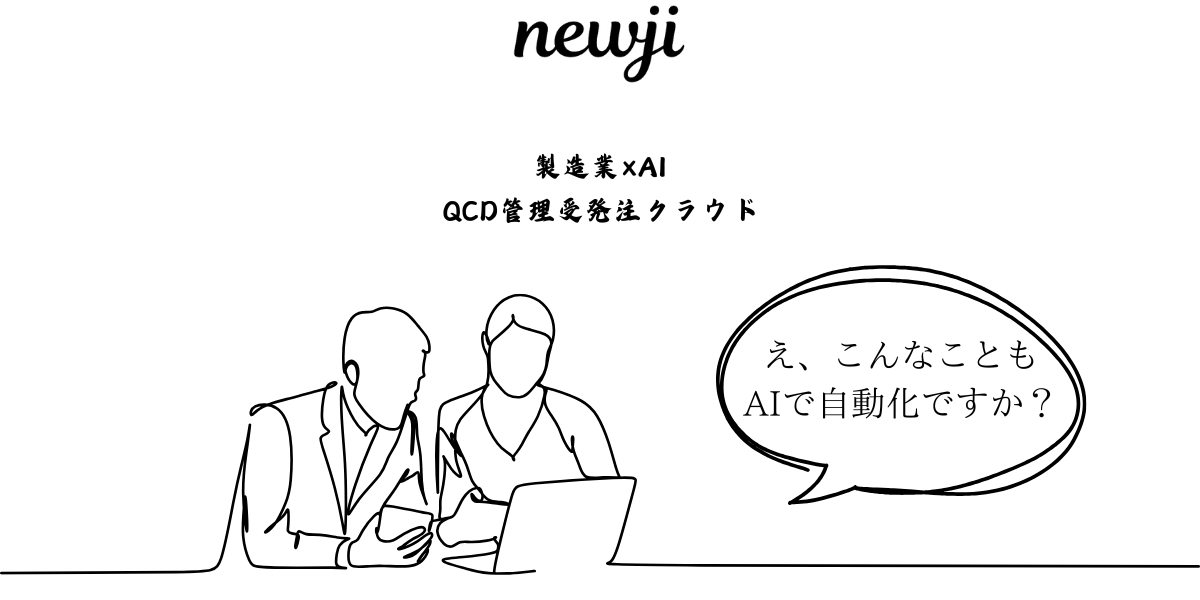
Latest examples in automotive parts prototyping
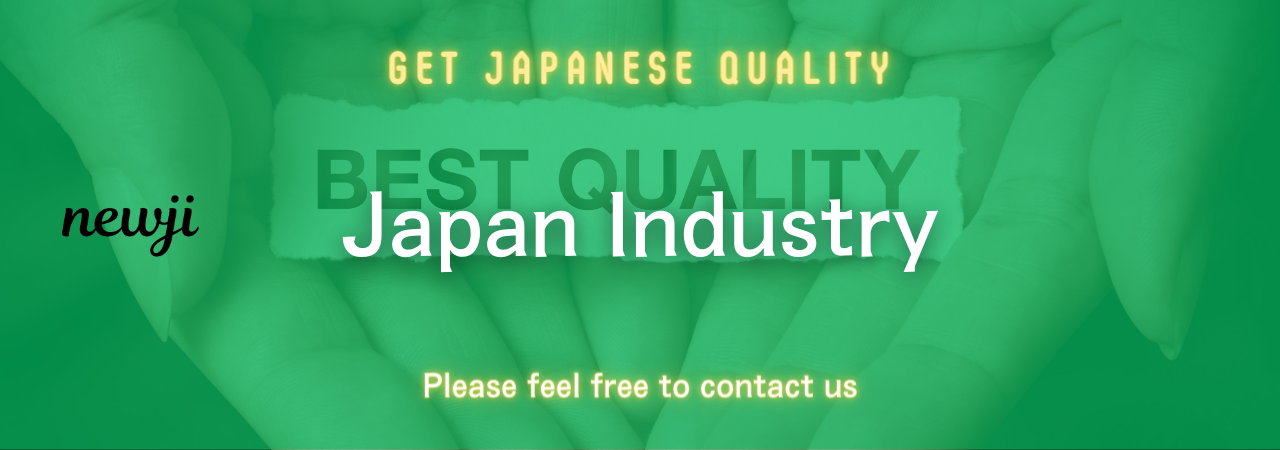
目次
Understanding Automotive Parts Prototyping
Automotive parts prototyping plays a vital role in the development and manufacturing of vehicles.
Prototyping is an essential process that allows manufacturers to create models for testing and evaluation before mass production.
Through this process, automakers can identify potential issues, assess functionality, and make necessary improvements to parts and designs.
There are various methods and techniques employed in automotive parts prototyping.
Each has its benefits and specific applications.
Some of the most commonly used methods include 3D printing, CNC machining, and injection molding.
These techniques enable the creation of prototypes with varying degrees of complexity and material properties.
As the automotive industry evolves, manufacturers continuously seek innovative ways to enhance the prototyping process.
Recent advancements have led to more efficient techniques, allowing for faster production and reduced costs.
3D Printing: A Revolutionary Approach
3D printing, also known as additive manufacturing, has revolutionized the prototyping process in the automotive industry.
This method allows for the creation of complex geometries and detailed designs with high precision.
It is particularly beneficial for creating intricate parts that would be challenging to produce using traditional methods.
One of the significant advantages of 3D printing is its flexibility.
Engineers can easily modify designs and produce multiple iterations with minimal effort and cost.
This makes it an ideal choice for prototyping in the early stages of design development.
In recent years, materials used in 3D printing have expanded beyond standard plastics to include metals, composites, and even ceramics.
This offers automotive manufacturers a broader range of options for prototyping various components, from engine parts to interior features.
Case Study: Rapid Prototyping with 3D Printing
A recent example of 3D printing’s impact on automotive prototyping is the development of a new air intake system for a high-performance sports car.
Using 3D printing, engineers were able to quickly produce multiple prototypes of the intricate design, allowing for rigorous testing and evaluation.
The rapid prototyping process enabled the team to identify and address potential issues early, enhancing the performance and efficiency of the final product.
As a result, the vehicle achieved better fuel efficiency and increased power output, demonstrating the effectiveness of 3D printing in automotive development.
CNC Machining: Precision and Speed
CNC machining is another essential technique used in automotive parts prototyping.
This subtractive manufacturing method involves using computer-controlled machines to precisely cut and shape materials into desired prototypes.
One of the main advantages of CNC machining is its ability to produce prototypes with high accuracy and smooth surface finishes.
This is particularly important for parts that require tight tolerances or specific mechanical properties.
CNC machining is ideal for creating prototypes from metal or high-strength materials, making it a popular choice for engine components, suspension parts, and structural elements.
Case Study: CNC Machining in Automotive Prototyping
A recent example of CNC machining’s application in automotive prototyping is seen in the development of a new suspension system for an electric vehicle.
The engineering team utilized CNC machining to create a series of prototypes from lightweight aluminum, which were then subjected to rigorous testing to assess their performance and durability.
By leveraging CNC machining, the team was able to quickly produce and refine their designs, ultimately resulting in an improved suspension system that enhanced the vehicle’s range and handling performance.
Injection Molding: Versatility and Mass Production
Injection molding is commonly used in the prototyping of automotive parts, particularly for plastic components.
This process involves injecting molten material into a mold cavity to shape it into the desired form.
One of the significant benefits of injection molding is its ability to produce prototypes that closely match the final production parts.
This makes it an invaluable tool for testing and validating designs before committing to mass production.
Injection molding is highly versatile and can be used with various materials, including thermoplastics, elastomers, and thermosetting polymers.
This versatility makes it suitable for manufacturing a wide range of automotive parts, from dashboard components to exterior trims.
Case Study: Injection Molding in Interior Component Prototyping
A recent example of injection molding in automotive prototyping is the development of a new dashboard panel for a luxury sedan.
The design team utilized injection molding to produce several iterations of the dashboard panel, experimenting with different materials and finishes to achieve the desired aesthetics and functionality.
The injection molding process allowed the team to test and refine their designs, ensuring the final product met both aesthetic and performance criteria.
This approach ultimately resulted in an innovative dashboard panel that enhanced the overall driving experience.
The Future of Automotive Parts Prototyping
As technology advances, the future of automotive parts prototyping looks promising, with new developments continually enhancing the design and manufacturing process.
Emerging technologies such as artificial intelligence and machine learning hold the potential to further streamline prototyping, enabling faster and more accurate designs.
In addition, the integration of virtual and augmented reality tools allows engineers to visualize and interact with prototypes in a digital environment.
This opens up new possibilities for evaluating designs and making informed decisions before physical prototyping begins.
Continued innovation in materials science will also play a crucial role in advancing prototyping techniques.
The development of new materials with enhanced properties will allow for more durable, lightweight, and sustainable automotive components.
Overall, the evolution of automotive parts prototyping promises to drive greater efficiencies, reduce costs, and foster innovation in the automotive industry, ultimately leading to the production of more advanced and reliable vehicles.
資料ダウンロード
QCD調達購買管理クラウド「newji」は、調達購買部門で必要なQCD管理全てを備えた、現場特化型兼クラウド型の今世紀最高の購買管理システムとなります。
ユーザー登録
調達購買業務の効率化だけでなく、システムを導入することで、コスト削減や製品・資材のステータス可視化のほか、属人化していた購買情報の共有化による内部不正防止や統制にも役立ちます。
NEWJI DX
製造業に特化したデジタルトランスフォーメーション(DX)の実現を目指す請負開発型のコンサルティングサービスです。AI、iPaaS、および先端の技術を駆使して、製造プロセスの効率化、業務効率化、チームワーク強化、コスト削減、品質向上を実現します。このサービスは、製造業の課題を深く理解し、それに対する最適なデジタルソリューションを提供することで、企業が持続的な成長とイノベーションを達成できるようサポートします。
オンライン講座
製造業、主に購買・調達部門にお勤めの方々に向けた情報を配信しております。
新任の方やベテランの方、管理職を対象とした幅広いコンテンツをご用意しております。
お問い合わせ
コストダウンが利益に直結する術だと理解していても、なかなか前に進めることができない状況。そんな時は、newjiのコストダウン自動化機能で大きく利益貢献しよう!
(Β版非公開)