- お役立ち記事
- Human error prevention measures and implementation examples in the prototyping process
月間76,176名の
製造業ご担当者様が閲覧しています*
*2025年3月31日現在のGoogle Analyticsのデータより
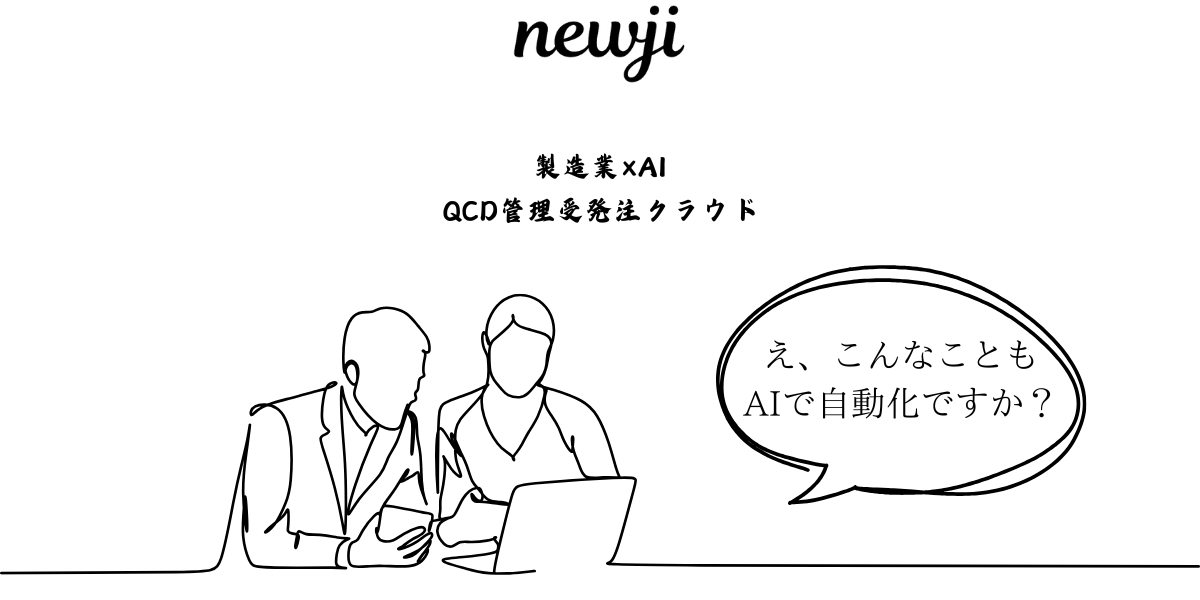
Human error prevention measures and implementation examples in the prototyping process
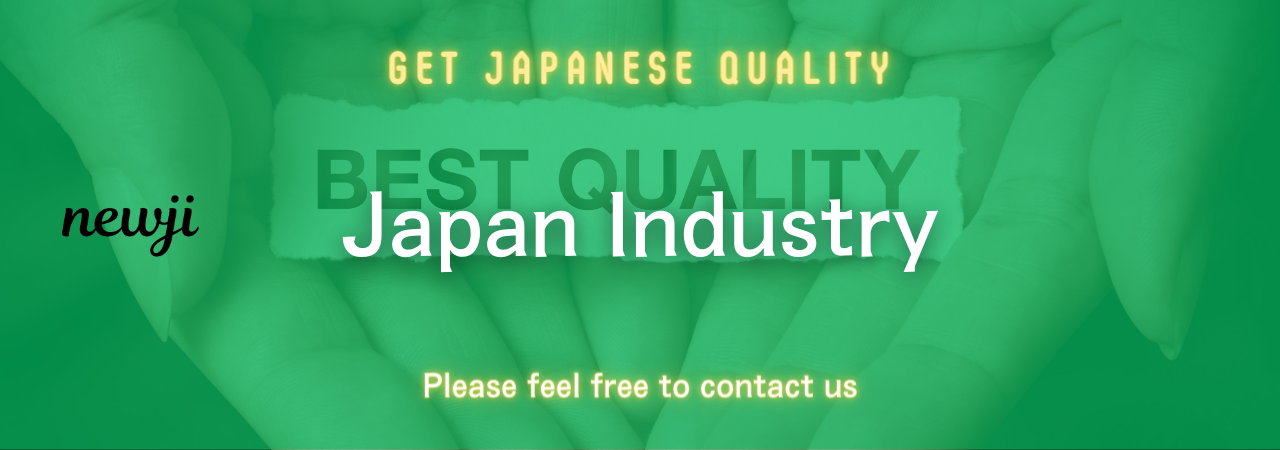
目次
Understanding Human Error in Prototyping
The process of creating prototypes is an essential part of product development.
It allows designers and engineers to test concepts, identify issues, and refine their ideas before mass production.
However, even in the controlled environment of prototyping, human errors can occur, leading to setbacks or potentially costly mistakes.
Human error refers to any unintended action or decision that deviates from what was intended or expected.
In prototyping, these can range from simple mistakes in measurements or materials to more complex miscommunications among team members.
Recognizing how these errors occur and implementing prevention measures is crucial to improving the efficiency and outcomes of the prototyping process.
Common Causes of Human Error in Prototyping
Lack of Communication
One of the most prevalent causes of human error in prototyping is poor communication.
The prototyping process often involves multiple team members, including designers, engineers, and manufacturers, who must work together seamlessly.
Miscommunications or misunderstandings between these parties can lead to incorrect specifications or improperly executed designs.
Inadequate Training
Another common cause of errors is inadequate training or lack of experience among team members.
When individuals are not properly trained in the tools or practices necessary for prototyping, the likelihood of mistakes increases significantly.
Complexity of Processes
Prototyping can involve complex processes and numerous steps, each requiring careful attention.
As the complexity increases, so does the potential for oversight or mistakes.
Simplifying these processes can often help minimize errors.
Strategies for Preventing Human Error in Prototyping
Enhancing Communication
Improving communication within the team is essential to reducing the risk of errors.
This can be achieved by setting up regular meetings, utilizing collaborative tools, and establishing clear, open lines of communication.
Encouraging questions and feedback can also prevent misunderstandings before they lead to errors.
Providing Proper Training
Ensuring that all team members receive adequate training is vital.
This includes both initial training for new employees and ongoing development for existing team members to keep them up-to-date with the latest tools and methods.
By building a knowledgeable team, the likelihood of errors can be significantly reduced.
Simplifying Processes
Streamlining and simplifying processes can also help mitigate the risk of mistakes.
This might involve breaking down complex tasks into smaller, more manageable steps or using standardized procedures whenever possible.
The aim is to make the prototyping process as clear and straightforward as possible.
Implementation Examples of Error Prevention in Prototyping
Utilizing Checklists
One practical example of human error prevention is the use of checklists.
By developing detailed and comprehensive checklists for each stage of the prototyping process, teams can ensure that all necessary steps are completed correctly.
Checklists act as reminders and help maintain consistency across projects.
Fostering a Collaborative Environment
Creating a culture that fosters collaboration and teamwork can help in reducing errors.
Encouraging team members to work together and share insights can often lead to the discovery of potential errors before they occur.
Collaboration tools like shared documents and project management software aid significantly in this regard.
Implementing Automation
Automation of repetitive or mundane tasks can significantly reduce human error.
In prototyping, automation tools can be used for precise measurements, data entry, or even some manufacturing processes.
These tools not only reduce the risk of error but also free up human resources for more complex tasks.
Continuous Improvement and Monitoring
An essential part of error prevention is ongoing improvement and monitoring.
After implementing various measures, it’s crucial to continuously assess their effectiveness and make any necessary adjustments.
Regular feedback sessions, audits, and performance reviews are integral to maintaining a high standard of error prevention.
Learning from Mistakes
It’s important to view errors as learning opportunities.
Analyzing errors to understand why they occurred and how they can be prevented in the future is a valuable practice.
This proactive approach helps teams evolve and improve their processes over time.
Adapting to Technological Advances
Prototyping is a field that is constantly evolving with technological advancements.
Staying abreast of new techniques, tools, and technologies can help teams prevent errors by adopting more reliable and efficient practices.
Regularly incorporating new technologies is essential to maintaining a competitive edge and reducing potential for error.
Conclusion
Human error in the prototyping process is an inevitable challenge that every team faces.
However, by understanding the common causes of these errors and implementing strategic prevention measures, teams can significantly reduce their occurrence.
Ensuring effective communication, providing proper training, simplifying processes, and leveraging technology are all critical components of an error-resistant prototyping process.
Through continuous improvement and adaptation, teams can enhance their efficiency, produce higher quality prototypes, and ultimately achieve greater success in product development.
資料ダウンロード
QCD管理受発注クラウド「newji」は、受発注部門で必要なQCD管理全てを備えた、現場特化型兼クラウド型の今世紀最高の受発注管理システムとなります。
ユーザー登録
受発注業務の効率化だけでなく、システムを導入することで、コスト削減や製品・資材のステータス可視化のほか、属人化していた受発注情報の共有化による内部不正防止や統制にも役立ちます。
NEWJI DX
製造業に特化したデジタルトランスフォーメーション(DX)の実現を目指す請負開発型のコンサルティングサービスです。AI、iPaaS、および先端の技術を駆使して、製造プロセスの効率化、業務効率化、チームワーク強化、コスト削減、品質向上を実現します。このサービスは、製造業の課題を深く理解し、それに対する最適なデジタルソリューションを提供することで、企業が持続的な成長とイノベーションを達成できるようサポートします。
製造業ニュース解説
製造業、主に購買・調達部門にお勤めの方々に向けた情報を配信しております。
新任の方やベテランの方、管理職を対象とした幅広いコンテンツをご用意しております。
お問い合わせ
コストダウンが利益に直結する術だと理解していても、なかなか前に進めることができない状況。そんな時は、newjiのコストダウン自動化機能で大きく利益貢献しよう!
(β版非公開)