- お役立ち記事
- Improving Efficiency in Press Forming by Optimizing Feeder System
Improving Efficiency in Press Forming by Optimizing Feeder System
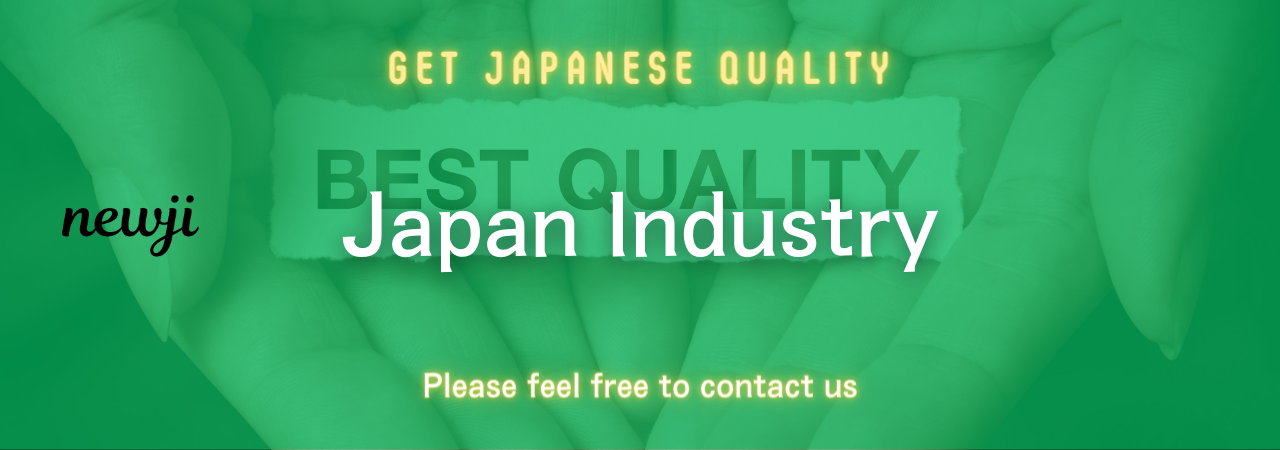
Press forming is a crucial process in many manufacturing industries, ranging from automotive to electronics. It involves shaping materials, usually metals, using a press machine and dies. One often overlooked but vital part of this process is the feeder system, which supplies material to the press. Optimizing this system can lead to a significant increase in efficiency and overall productivity. This article will guide you through practical steps to enhance your feeder system for better performance.
Understanding the Feeder System
A feeder system in press forming functions like a conveyor belt, ensuring that the material is reliably delivered to the press. It can include various components such as straighteners, uncoilers, and feeders. Each part plays a role in preparing and positioning the material correctly. Any shortcomings in these elements can slow down the process, leading to inefficiencies and increased costs.
Why Optimization Matters
Before diving into optimization strategies, it’s essential to understand why it matters. A well-optimized feeder system can:
– Increase production speed
– Reduce material waste
– Lower operational costs
– Improve product quality
Key Components to Optimize
1. Feed Rollers
Feed rollers help transport the material into the press. Ensuring these rollers are well-maintained and correctly aligned can significantly enhance the feeding accuracy. Regular inspections and replacements when necessary will keep the system running smoothly.
2. Straighteners
Straighteners help align the material before feeding it into the press. An effective straightener reduces the likelihood of jams and misfeeds. Invest in high-quality straighteners and ensure they are correctly calibrated for the specific material used.
3. Uncoilers
Uncoilers hold the material in coil form and feed it into the straightener and feeder. Automatic uncoilers can offer consistent material delivery and reduce manual interventions. Ensure that the uncoiler is compatible with the coil size and material type used in your process.
Practical Steps for Optimization
Regular Maintenance
Preventive maintenance is the first step in optimizing a feeder system. Regularly check for wear and tear, and replace components when necessary. Keeping the system clean and lubricated also helps in maintaining its efficiency.
Monitoring and Analysis
Use sensors and monitoring tools to track the performance of your feeder system. Data such as feeding speed, material thickness, and tension can provide valuable insights into areas needing improvement. Analyze this data periodically to make informed decisions about adjustments and upgrades.
Automation and Upgrades
Modernizing your feeder system with automation can drastically improve efficiency. Consider upgrading to a fully automatic feeder system capable of adjusting feed rate, tension, and alignment in real-time. While these systems require an upfront investment, the long-term savings and productivity gains can be substantial.
Staff Training
Even the most advanced systems are only as good as the operators using them. Investing in comprehensive training for your staff ensures they can troubleshoot issues, perform basic maintenance, and operate the system at peak efficiency.
Benefits of Optimization
Increased Speed and Productivity
An optimized feeder system reduces the time needed to load and align material, directly increasing the production speed. This allows you to produce more in less time, meeting higher demand without compromising quality.
Reduced Waste
Misfeeds and jams can lead to significant material wastage. An effective feeder system minimizes these issues, leading to better resource utilization. This not only reduces costs but also supports sustainability efforts.
Lower Operational Costs
While optimizing your feeder system requires an initial investment, the long-term benefits include reduced downtime, lower maintenance costs, and improved energy efficiency. These savings quickly add up, offering a substantial return on investment.
Case Study: Real-World Application
To illustrate the benefits of optimizing a feeder system, consider a case study of an automotive parts manufacturer. Before optimization, the company faced frequent downtimes due to material jams and misalignments, affecting their production schedules and increasing costs.
The Problems
– Frequent material jams
– High maintenance costs
– Significant material waste
The Solutions
– Upgraded to an automatic feeder system
– Implemented a preventive maintenance schedule
– Trained staff on the new system
The Results
– Production speed increased by 25%
– Material waste reduced by 30%
– Maintenance costs lowered by 20%
This example highlights how a strategic approach to feeder system optimization can lead to substantial improvements in overall efficiency and cost savings.
Optimizing the feeder system in press forming is not just about upgrading equipment; it’s about taking a holistic approach that includes maintenance, monitoring, automation, and staff training. By investing time and resources into these areas, you can significantly enhance your production efficiency, reduce waste, and lower operational costs. Whether you are a large manufacturing firm or a smaller operation, these improvements can provide you with a competitive edge in the market.
資料ダウンロード
QCD調達購買管理クラウド「newji」は、調達購買部門で必要なQCD管理全てを備えた、現場特化型兼クラウド型の今世紀最高の購買管理システムとなります。
ユーザー登録
調達購買業務の効率化だけでなく、システムを導入することで、コスト削減や製品・資材のステータス可視化のほか、属人化していた購買情報の共有化による内部不正防止や統制にも役立ちます。
NEWJI DX
製造業に特化したデジタルトランスフォーメーション(DX)の実現を目指す請負開発型のコンサルティングサービスです。AI、iPaaS、および先端の技術を駆使して、製造プロセスの効率化、業務効率化、チームワーク強化、コスト削減、品質向上を実現します。このサービスは、製造業の課題を深く理解し、それに対する最適なデジタルソリューションを提供することで、企業が持続的な成長とイノベーションを達成できるようサポートします。
オンライン講座
製造業、主に購買・調達部門にお勤めの方々に向けた情報を配信しております。
新任の方やベテランの方、管理職を対象とした幅広いコンテンツをご用意しております。
お問い合わせ
コストダウンが利益に直結する術だと理解していても、なかなか前に進めることができない状況。そんな時は、newjiのコストダウン自動化機能で大きく利益貢献しよう!
(Β版非公開)