- お役立ち記事
- Surface treatment technology for prototype parts and its quality evaluation criteria
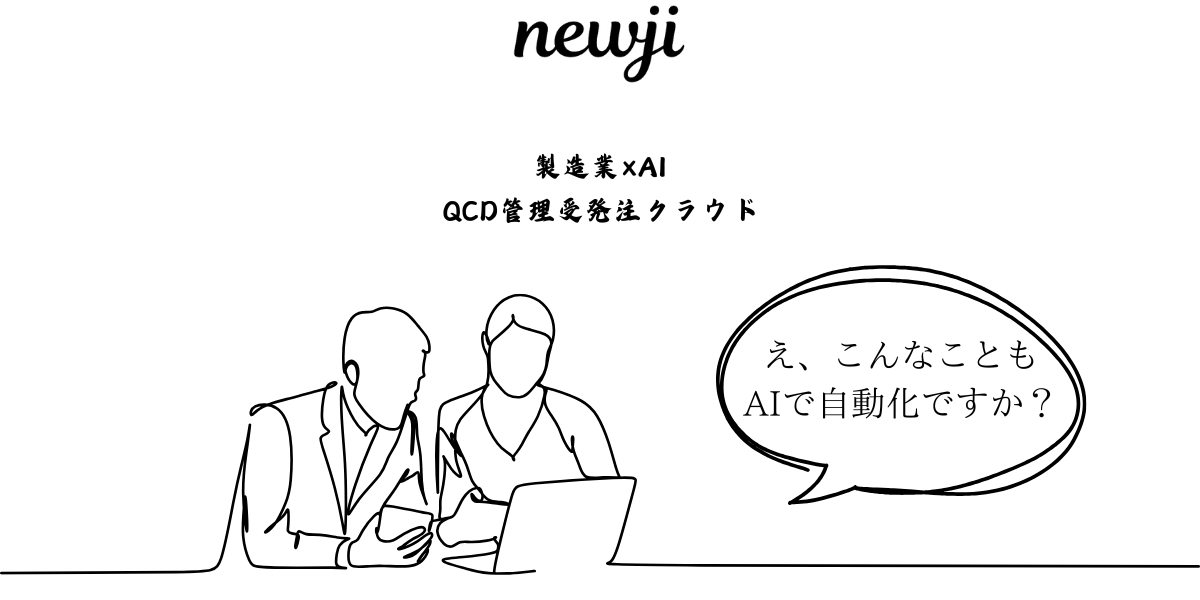
Surface treatment technology for prototype parts and its quality evaluation criteria
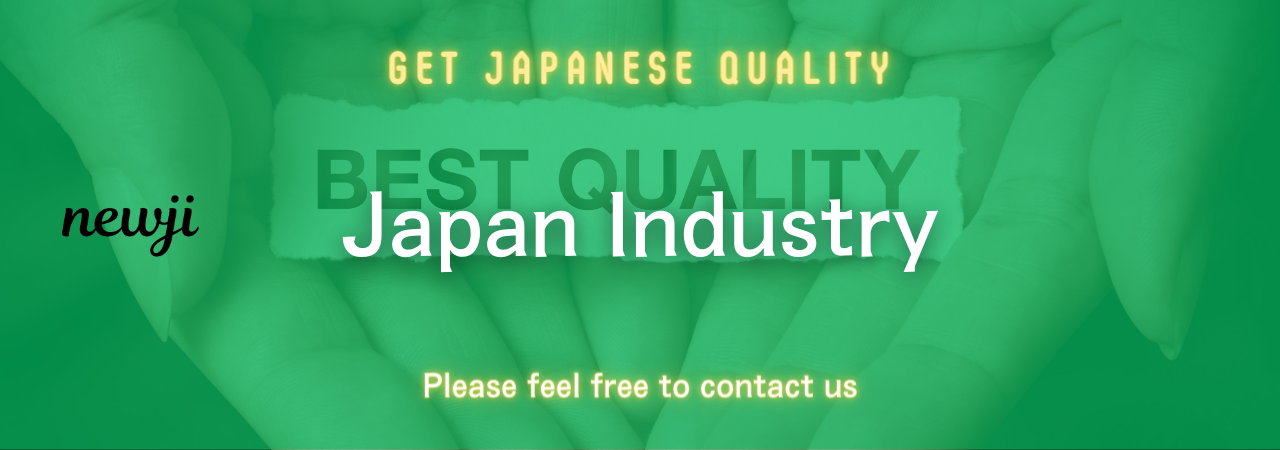
目次
Understanding Surface Treatment Technology
Surface treatment technology plays a crucial role in changing the surface properties of prototype parts to enhance their performance, appearance, and durability.
In various industries, surface treatment is essential as it offers protection against wear, corrosion, and other environmental factors.
This technology involves applying a different material onto the surface of a prototype to achieve desired characteristics.
The process begins with preparing the surface of the part by cleaning it to remove any contaminants.
This ensures a smoother and more effective treatment.
Once the part is clean, the surface is treated using methods such as coating, plating, anodizing, or painting, depending on the end-use requirements and material type.
Types of Surface Treatments
There are several types of surface treatment technologies used in the prototyping industry.
Here are some of the most common:
Coating
Coating involves applying a material in liquid or powder form to the surface of a part.
This protective or decorative layer can improve the prototype’s appearance, resistance to abrasion, and corrosion protection.
Popular coating methods include powder coating, which offers a durable finish, and wet painting, which adds color and aesthetic appeal.
Plating
Plating, such as electroplating, involves depositing a metal layer onto the surface of the part, providing enhanced wear resistance and conductivity.
Common plating metals include nickel, chrome, and gold.
Electroless plating is another method where a chemical reaction deposits the metal layer without an electric current.
Anodizing
Anodizing is an electrolytic process that increases the thickness of the natural oxide layer on metal surfaces, typically aluminum.
This treatment enhances the part’s resistance to corrosion and wear while providing a range of color options for aesthetic enhancement.
Heat Treatment
Heat treatment involves heating and cooling prototype parts in a controlled way to change their physical and mechanical properties.
Processes like case hardening and tempering improve hardness and toughness.
Evaluating the Quality of Surface Treatments
Quality evaluation of surface treatments is critical to ensure the performance standards of prototype parts are met.
Several criteria are used to assess the quality of surface treatments:
Adhesion
Adhesion tests assess how well a coating or treatment bonds to the substrate.
A strong bond is essential to prevent peeling and ensure durability.
Common tests for adhesion include the cross-cut test and pull-off test.
Thickness
Measuring the thickness of the applied surface treatment helps determine if it meets the required specifications.
Inaccurate thickness can affect the functionality and longevity of the part.
Hardness
Surface hardness tests evaluate resistance to deformation or wear.
Hardness testing methods include the Vickers and Rockwell tests, which determine the treatment’s effectiveness in improving durability.
Corrosion Resistance
Corrosion resistance tests, such as salt spray tests, help evaluate a material’s ability to withstand corrosive environments.
This is essential for parts exposed to harsh conditions that could degrade over time.
Visual Inspections
Visual inspections check for surface defects such as cracks, blisters, or uneven finishes.
This step ensures that the surface treatment enhances the part’s aesthetic appeal.
Applications of Surface Treatment Technology
Surface treatment technologies are applied across various industries to ensure products meet desired functionalities.
Some key industries include:
Automotive
In the automotive industry, surface treatment technologies are used to protect parts from wear and corrosion.
This enhances the longevity of vehicle components like engine parts and body panels.
Aerospace
Aerospace applications use surface treatments to improve the performance and safety of components by providing heat and corrosion resistance.
These treatments help maintain the integrity of aerospace structures under extreme conditions.
Electronics
For electronic devices, surface treatments are used to enhance conductivity and protect sensitive parts.
These treatments are crucial for the functionality and longevity of electronic components.
Medical Devices
Surface treatments in medical devices help ensure biocompatibility and sterility.
Treatments improve the surfaces of implants and surgical tools for better performance and safety.
Challenges in Surface Treatment Technology
Despite the advantages, surface treatment technology faces challenges that need addressing:
Compatibility
Ensuring compatibility between the treatment and the material is crucial to avoid adverse reactions.
Incompatible treatments can lead to weak adhesion and reduced effectiveness.
Environmental Concerns
Some surface treatment processes can be detrimental to the environment.
The industry is shifting towards eco-friendly methods that reduce waste and hazardous emissions.
Cost
The cost of surface treatments can be significant, especially for high-quality or specialized processes.
Balancing cost with required performance is often a challenge for manufacturers.
The Future of Surface Treatment Technology
The future of surface treatment technology looks promising with ongoing advancements and innovations:
Nanotechnology
Nanotechnology offers more precise surface treatments at the molecular level.
This leads to improved performance and new functionalities.
Smart Coatings
Smart coatings that interact with their environment offer potential to provide self-healing and self-cleaning properties.
These innovations can extend the lifespan and performance of prototype parts.
Sustainable Solutions
The industry is moving towards sustainable solutions, prioritizing eco-friendly processes and materials to reduce environmental impact.
In conclusion, surface treatment technology is vital for enhancing the performance and durability of prototype parts.
By understanding various methods and quality evaluation criteria, industries can ensure their products meet high-performance standards.
With ongoing technological advancements, the future of surface treatment holds exciting possibilities for improved functionality and sustainability.
資料ダウンロード
QCD調達購買管理クラウド「newji」は、調達購買部門で必要なQCD管理全てを備えた、現場特化型兼クラウド型の今世紀最高の購買管理システムとなります。
ユーザー登録
調達購買業務の効率化だけでなく、システムを導入することで、コスト削減や製品・資材のステータス可視化のほか、属人化していた購買情報の共有化による内部不正防止や統制にも役立ちます。
NEWJI DX
製造業に特化したデジタルトランスフォーメーション(DX)の実現を目指す請負開発型のコンサルティングサービスです。AI、iPaaS、および先端の技術を駆使して、製造プロセスの効率化、業務効率化、チームワーク強化、コスト削減、品質向上を実現します。このサービスは、製造業の課題を深く理解し、それに対する最適なデジタルソリューションを提供することで、企業が持続的な成長とイノベーションを達成できるようサポートします。
オンライン講座
製造業、主に購買・調達部門にお勤めの方々に向けた情報を配信しております。
新任の方やベテランの方、管理職を対象とした幅広いコンテンツをご用意しております。
お問い合わせ
コストダウンが利益に直結する術だと理解していても、なかなか前に進めることができない状況。そんな時は、newjiのコストダウン自動化機能で大きく利益貢献しよう!
(Β版非公開)