- お役立ち記事
- Benefits of using digital twin in the prototyping process
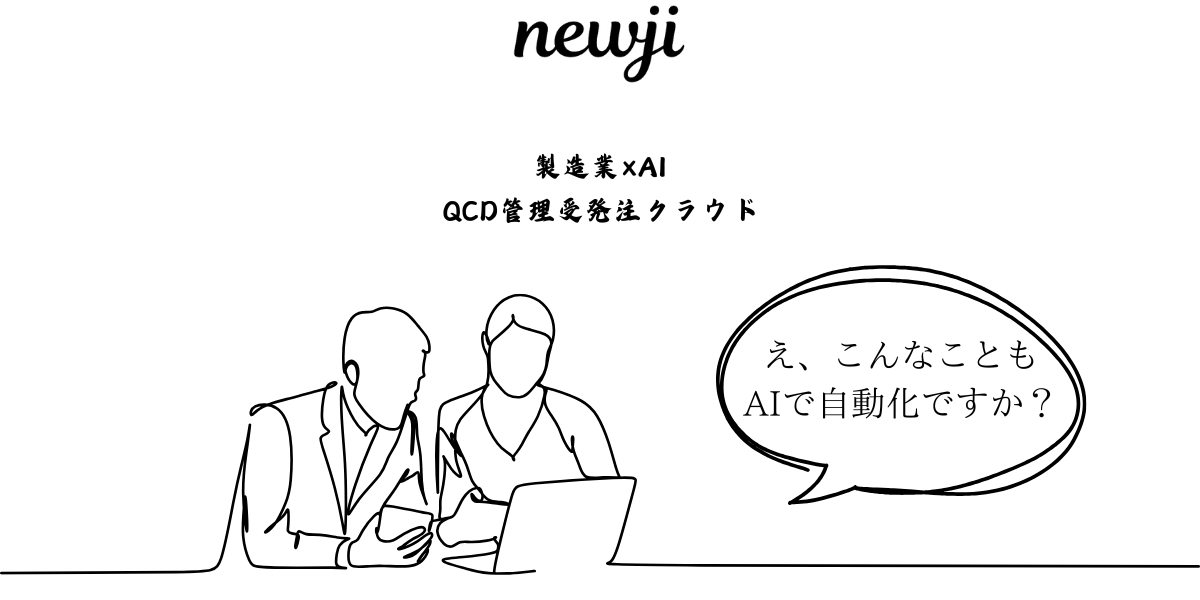
Benefits of using digital twin in the prototyping process
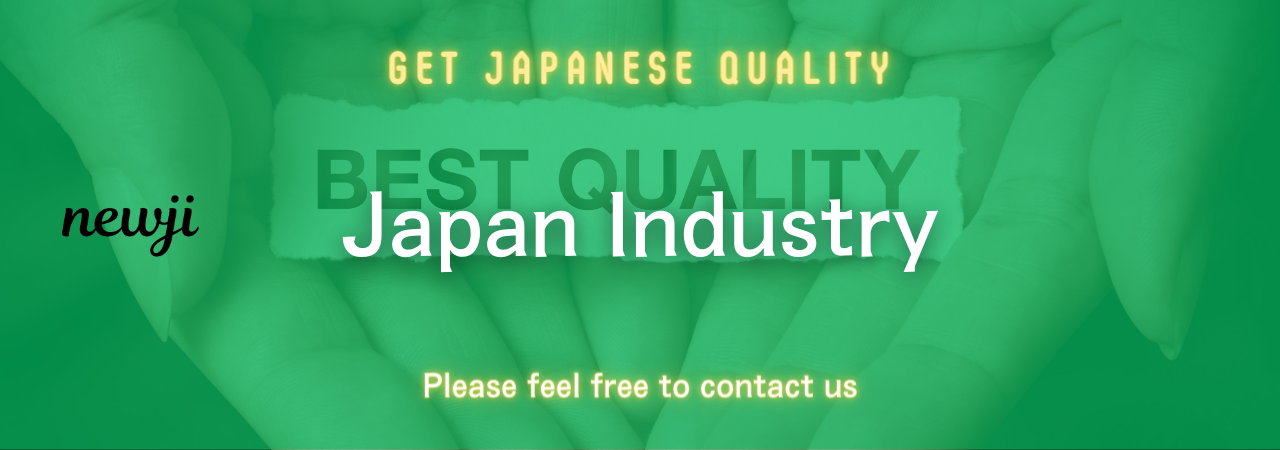
目次
Understanding Digital Twins
Digital Twins have emerged as an innovative concept in the realm of technology, particularly affecting how industries approach the prototyping process.
The term “Digital Twin” refers to a virtual model or simulation that represents a physical object or system.
This sophisticated technology creates an exact digital replica of a real-world item, enabling businesses and professionals to view and analyze various aspects of that object without interacting with the physical version.
By leveraging these digital replicas, companies can significantly enhance their prototyping processes to achieve better outcomes and efficiencies.
Streamlined Prototyping Process
One of the most significant benefits of using digital twins in the prototyping process is the potential for streamlining operations.
By creating a digital model of a product or system, engineers and designers can easily simulate different aspects and tweak designs without the cost, time, and resource use needed for physical prototypes.
This means that changes to the design can be assessed almost instantly, without the need to construct multiple physical iterations.
As a result, what once took weeks or even months can now often be accomplished in a fraction of the time.
Cost Reduction
Another considerable advantage of digital twins in the prototyping process is the potential to reduce costs.
Building physical prototypes is not only time-consuming but can also be quite costly.
Materials can be expensive, and the labor required to produce each iteration adds up quickly.
Digital twins eliminate much of this financial burden since changes and improvements can be made in a virtual environment.
The cost savings realized can then be redirected into further development, enabling businesses to improve their product offerings and remain competitive in their field.
Improved Accuracy and Precision
Digital twins also provide improved accuracy and precision in the prototyping process.
These virtual models allow engineers and designers to simulate complex systems under different conditions, providing them with valuable insights that might not be possible with physical prototypes.
Understanding how a product or system will behave in real-world scenarios helps pinpoint potential problems before they arise, promoting higher quality and more reliable final products.
This level of accuracy also ensures that digital twins keep companies at the forefront of innovation by continually refining and optimizing designs.
Increased Flexibility
The use of digital twins provides significant flexibility when modifying designs.
In traditional prototyping processes, each change required a new physical product build, which could be cumbersome and inflexible.
Digital twins, however, allow for easy modifications to be made in real-time.
These changes can quickly be tested and evaluated, meaning that the design phase becomes far more flexible.
By adapting swiftly to new trends, expectations, and technological advancements, businesses can maintain a competitive edge.
Such flexibility opens up numerous possibilities regarding experimentation and innovation, further enhancing the value of the prototyping process.
Enhancement in Collaboration
Digital twins facilitate global collaboration between teams, designers, and stakeholders.
With a digital model, everyone involved in the project’s development can interact with the prototype regardless of their geographic location.
This accessibility allows for real-time feedback and input, fostering stronger collaboration and teamwork throughout the prototyping process.
Teams can work together seamlessly, sharing insights, suggestions, and data, making the prototyping process more inclusive and innovative.
The enhanced collaboration facilitates more creative solutions, accelerates problem-solving, and helps meet project deadlines more efficiently.
Comprehensive Data Analysis
One of the most powerful advantages of digital twins in the prototyping process is their ability to provide comprehensive data analysis.
Through simulation and data collection, they offer valuable insights into a product’s performance under different conditions.
This precise data empowers companies to make informed design decisions based on predictive analytics.
Understanding how a prototype performs in various scenarios allows companies to optimize its functionality before finalizing the design.
The predictive insights obtained from digital twins can also aid in risk management by identifying potential issues before mass production.
Challenges to Consider
While digital twins present numerous benefits, there are challenges businesses must consider to deploy them effectively.
For instance, setting up digital twin systems can involve significant initial costs in terms of time, technology, and skilled personnel.
Data security is also a concern, as the sensitive data represented by digital twins must be carefully protected.
Additionally, ensuring the digital twin remains accurately calibrated with the physical object requires diligence and ongoing attention.
The Future of Prototyping
As technology continues to evolve, so will the applications of digital twins in the prototyping process.
From smaller start-ups to large corporations, entities across the board are poised to benefit greatly from adopting this technology.
With continuous innovations, digital twins will likely become even more powerful and integral in product development cycles.
The increasing integration of artificial intelligence and the Internet of Things (IoT) suggests even more dynamic and responsive digital twin models in the future.
In conclusion, the advantages of using digital twins in the prototyping process cannot be overstated.
From reducing costs to improving accuracy and enhancing collaboration, digital twins are transforming how products are developed and tested.
By embracing this technology, industries can not only optimize their prototypes but also pave the way for groundbreaking innovations in the years to come.
資料ダウンロード
QCD調達購買管理クラウド「newji」は、調達購買部門で必要なQCD管理全てを備えた、現場特化型兼クラウド型の今世紀最高の購買管理システムとなります。
ユーザー登録
調達購買業務の効率化だけでなく、システムを導入することで、コスト削減や製品・資材のステータス可視化のほか、属人化していた購買情報の共有化による内部不正防止や統制にも役立ちます。
NEWJI DX
製造業に特化したデジタルトランスフォーメーション(DX)の実現を目指す請負開発型のコンサルティングサービスです。AI、iPaaS、および先端の技術を駆使して、製造プロセスの効率化、業務効率化、チームワーク強化、コスト削減、品質向上を実現します。このサービスは、製造業の課題を深く理解し、それに対する最適なデジタルソリューションを提供することで、企業が持続的な成長とイノベーションを達成できるようサポートします。
オンライン講座
製造業、主に購買・調達部門にお勤めの方々に向けた情報を配信しております。
新任の方やベテランの方、管理職を対象とした幅広いコンテンツをご用意しております。
お問い合わせ
コストダウンが利益に直結する術だと理解していても、なかなか前に進めることができない状況。そんな時は、newjiのコストダウン自動化機能で大きく利益貢献しよう!
(Β版非公開)