- お役立ち記事
- How to use a parts management system in the prototyping process
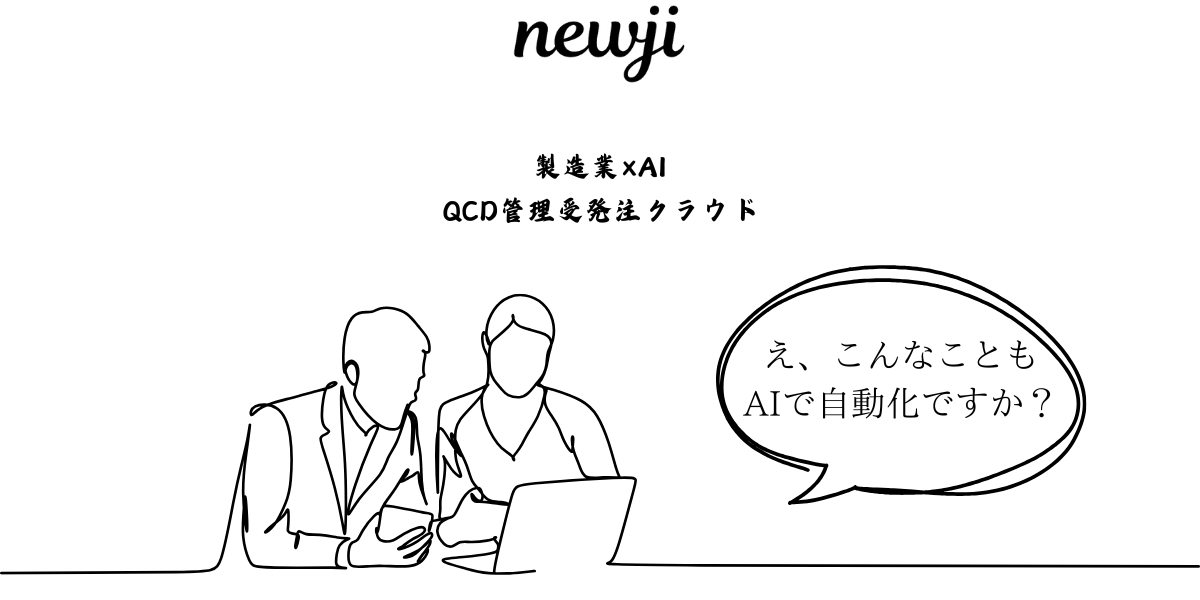
How to use a parts management system in the prototyping process
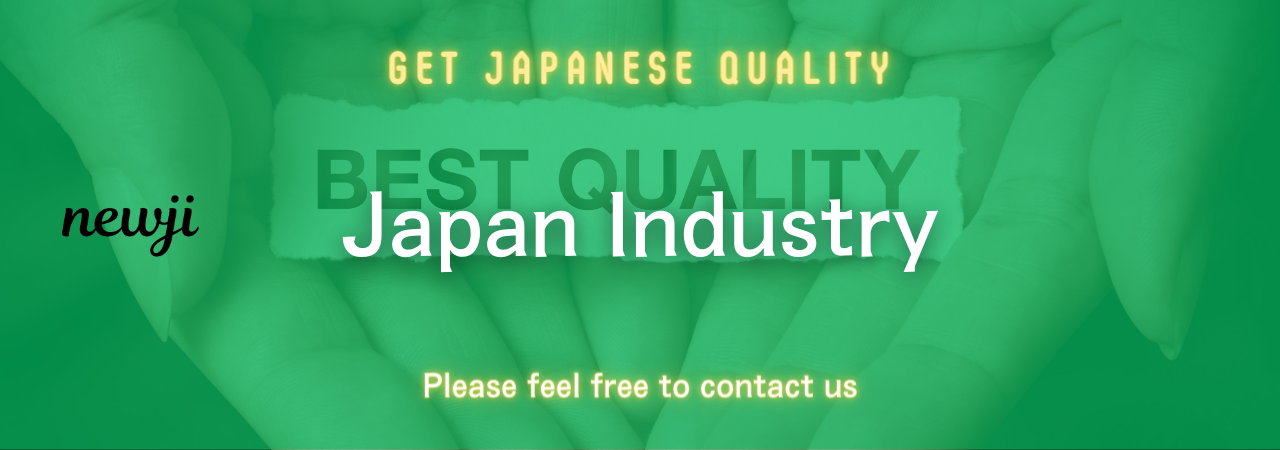
目次
Understanding the Parts Management System
In the realm of product development, especially during the prototyping stage, managing parts efficiently becomes crucial.
A parts management system is a tool designed to organize, track, and manage components and materials used in product prototyping.
It ensures that all necessary parts are available when needed, reducing delays and improving the overall process efficiency.
These systems can range from simple spreadsheets to complex software solutions, depending on the scale and need of your project.
They provide an overview of what parts are required, where they can be sourced from, and how much inventory is currently available.
By implementing such a system, teams can significantly reduce waste and lower the costs associated with over-ordering or losing track of parts.
Setting Up a Parts Management System
Before diving into using a parts management system, it’s essential to set it up correctly.
First, compile a comprehensive list of all parts and materials used in your prototyping process.
Classify these parts into categories based on their function, material type, or any other relevant criteria that suit your project’s needs.
Next, choose a parts management tool that fits your project’s scale.
If you’re working on a small prototype, a spreadsheet might suffice.
However, for larger projects with multiple team members, consider using dedicated software designed for parts management.
Upload your parts list into the chosen system, ensuring that each item has a detailed description, part number, supplier information, and any other attributes necessary for easy identification.
Having a robust setup from the start will allow for smooth operation as the project progresses.
Optimizing Inventory Management
One of the key benefits of a parts management system is its ability to optimize inventory control.
With real-time updates on part availability, you can avoid overstocking and understocking, ensuring that you maintain the right balance of parts on hand.
Implementing just-in-time ordering can significantly reduce the storage costs and minimize waste.
It involves ordering only what you need when you need it, based on the project’s requirements indicated in the parts management system.
Additionally, by analyzing inventory data such as usage rates and lead times, you can predict future needs more accurately.
This proactive approach helps in mitigating risks associated with part shortages or excess inventory.
Regular Inventory Audits
Conduct regular audits of your inventory to verify the accuracy of your parts management system.
This will help you identify discrepancies between the system’s data and physical inventory, enabling you to correct any errors promptly.
Regular audits also assist in identifying obsolete or slow-moving parts.
Removing unnecessary stock not only frees up valuable storage space but also ensures that your parts list remains relevant and easy to manage.
Streamlining the Procurement Process
A parts management system simplifies the procurement process by centralizing all necessary information.
With supplier details and order history readily available, placing orders becomes a more straightforward and efficient task.
Automating parts reordering based on predefined thresholds can save your team time and prevent interruptions in the prototyping process.
For example, if a part’s inventory falls below a certain level, the system can automatically trigger a reorder to keep stock levels consistent.
Furthermore, maintaining a list of preferred suppliers helps in achieving better pricing through bulk purchases or long-term collaborations.
It also streamlines communications, ensuring that you always have access to the parts you need in a timely manner.
Facilitating Cross-Department Collaboration
Effective prototyping often requires collaboration across multiple departments, including design, engineering, and purchasing.
A parts management system serves as a central hub where all stakeholders can access up-to-date information.
By providing transparency and visibility into parts availability and project timelines, teams can coordinate more effectively.
This leads to fewer misunderstandings and a more streamlined workflow.
Sharing access to the parts management system with external vendors or contractors can also improve collaboration.
It enables them to view necessary specifications and availability, ensuring that they are aligned with your project needs.
Improving Quality Control
Quality control is a critical aspect of product prototyping, and a parts management system can aid in maintaining high standards.
By tracking the origins and specifications of each part, teams can ensure that only quality materials are used in the prototype.
The system can also be used to document any quality issues encountered and their resolutions.
This information can be valuable for future reference, helping to avoid previous mistakes in subsequent projects or iterations.
Conducting regular quality checks is easier with a well-organized parts management system, as it allows for efficient tracking and auditing of all parts involved in the prototyping process.
Conclusion
Incorporating a parts management system into your prototyping process offers numerous benefits, from improved inventory control to enhanced collaboration.
By setting up an effective system, you can streamline operations, reduce waste, and ensure that your prototypes are completed on time and to the highest quality.
Whether opting for a simple spreadsheet or a complex software solution, tailoring the system to your specific needs is key.
By doing so, you provide your team with the tools necessary to navigate the challenges of prototyping efficiently and successfully.
資料ダウンロード
QCD調達購買管理クラウド「newji」は、調達購買部門で必要なQCD管理全てを備えた、現場特化型兼クラウド型の今世紀最高の購買管理システムとなります。
ユーザー登録
調達購買業務の効率化だけでなく、システムを導入することで、コスト削減や製品・資材のステータス可視化のほか、属人化していた購買情報の共有化による内部不正防止や統制にも役立ちます。
NEWJI DX
製造業に特化したデジタルトランスフォーメーション(DX)の実現を目指す請負開発型のコンサルティングサービスです。AI、iPaaS、および先端の技術を駆使して、製造プロセスの効率化、業務効率化、チームワーク強化、コスト削減、品質向上を実現します。このサービスは、製造業の課題を深く理解し、それに対する最適なデジタルソリューションを提供することで、企業が持続的な成長とイノベーションを達成できるようサポートします。
オンライン講座
製造業、主に購買・調達部門にお勤めの方々に向けた情報を配信しております。
新任の方やベテランの方、管理職を対象とした幅広いコンテンツをご用意しております。
お問い合わせ
コストダウンが利益に直結する術だと理解していても、なかなか前に進めることができない状況。そんな時は、newjiのコストダウン自動化機能で大きく利益貢献しよう!
(Β版非公開)