- お役立ち記事
- How to make food manufacturing production lines more efficient with DX (robotization/automation)
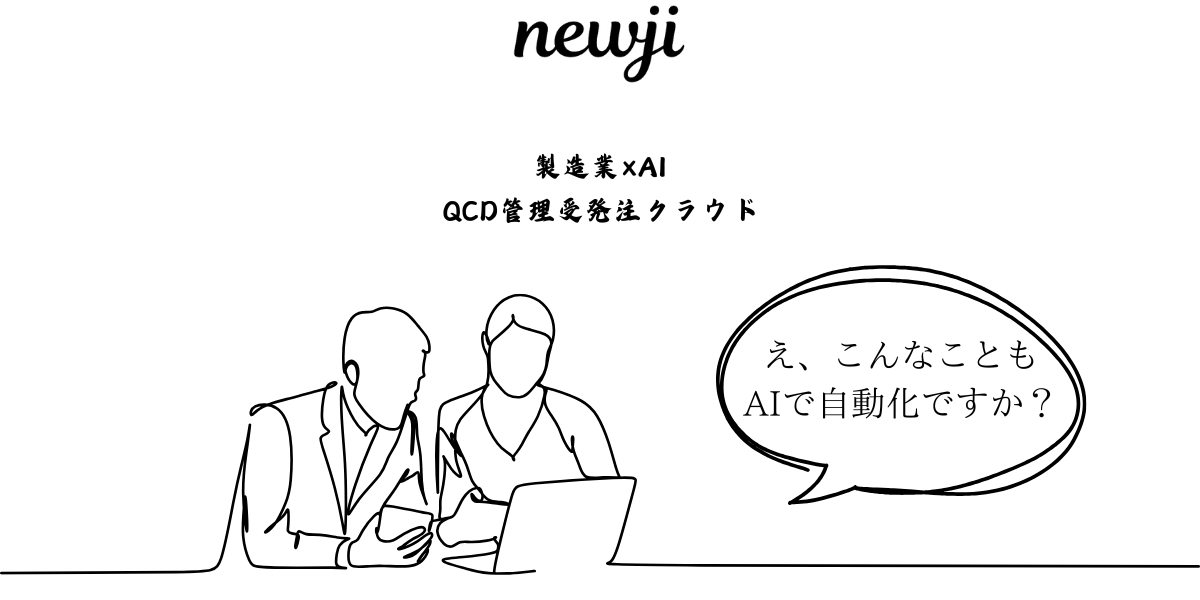
How to make food manufacturing production lines more efficient with DX (robotization/automation)
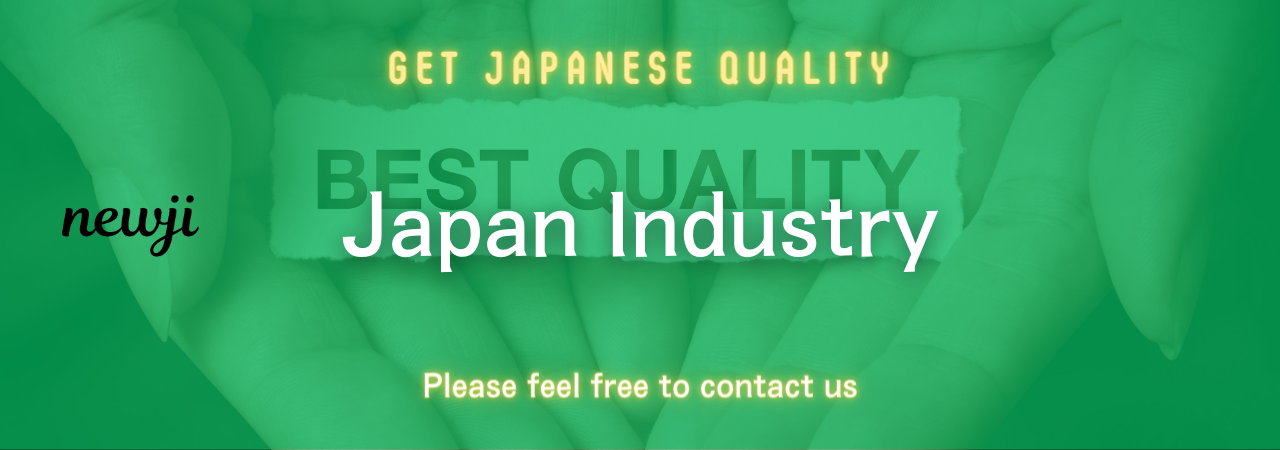
目次
Understanding the Basics of DX in Food Manufacturing
Digital transformation, often referred to as DX, is transforming industries worldwide, and food manufacturing is no exception.
The objective is to enhance efficiency, reduce operational costs, and improve product quality by implementing advanced technologies such as robotization and automation.
DX in the food industry can involve using smart sensors, advanced robotic systems, and AI-driven analytics to automate and optimize production lines.
The food manufacturing sector is inherently complex, with a need for precision, consistency, and compliance with strict health and safety standards.
By applying digital technologies, companies can streamline operations and stay competitive in an increasingly demanding market.
Benefits of Robotization and Automation
Automation in food manufacturing refers to the use of machines and technologies to replicate or improve production processes that were traditionally performed manually.
Robots and automated systems can take over tasks such as sorting, packaging, quality control, and even cooking.
One of the primary benefits of automation is the enhancement of productivity.
Robots can operate 24/7 without breaks, leading to increased output and faster turnaround times.
Additionally, automation reduces the risk of human error, ensuring a higher degree of consistency and quality in the final product.
Robotization can also lead to cost savings in the long run.
Though the initial investment might be significant, the reduction in labor costs and the minimization of waste due to accurate, efficient production pay off over time.
Another vital advantage is the ability to ensure a safe and hygienic production environment.
Robotic systems can handle materials without direct human contact, significantly reducing the risk of contamination—a critical factor in food manufacturing.
Implementing DX: Key Considerations
When considering introducing DX through robotization and automation, manufacturers must assess several factors to ensure a successful transition.
Assessing the Current Workflow
Before automating, it’s essential to analyze existing processes to identify areas that could benefit most from automation.
This involves understanding the current workflow, identifying bottlenecks, and assessing where human labor is inefficient or could be better utilized.
Selecting the Right Technology
Not all automation technologies are suited for every type of food production.
Manufacturers must select technology that meets their specific needs, considering factors such as product type, production volume, and compliance requirements.
This might include choosing between different types of robots—articulated, delta, or SCARA robots—based on tasks and spatial constraints.
Ensuring Employee Buy-In
The transition to automation can be challenging for employees.
It’s crucial to communicate the benefits of DX and provide training to help them adapt to new roles.
This might involve reskilling workers to manage and maintain automated systems, ensuring they remain valuable to the company.
Maintaining Compliance and Safety
Food manufacturers must comply with stringent regulatory standards, and automation projects are no exception.
It’s essential to ensure that all systems adhere to food safety regulations and industry standards at every step of the automation process.
Real-Life Examples of DX in Food Manufacturing
Several companies have successfully integrated DX into their production lines, creating case studies that serve as blueprints for others.
Case Study 1: Automated Quality Control
A leading snack manufacturer integrated AI-driven visual inspection systems that could automatically detect defects in products with high precision.
This automation reduced waste, improved quality, and freed up skilled employees to focus on more complex tasks, leading to increased productivity and product satisfaction.
Case Study 2: Robotic Packaging Systems
Another manufacturer invested in robotic packaging solutions.
Automated packing systems adapted to various product shapes and sizes, responding to changes in production volume efficiently.
The result was a dramatic reduction in packaging errors and material wastage, while also accelerating the overall process.
Case Study 3: Predictive Maintenance
Implementing IoT-enabled sensors throughout their production line, a dairy manufacturer could monitor equipment in real-time.
These sensors predict when maintenance is needed, avoiding costly downtime.
This proactive approach helped maintain continuous production and reduced repair costs substantially.
Embracing the Future of Food Manufacturing
Digital transformation is not just a choice but a necessity for food manufacturers who wish to thrive in the modern market.
By embracing robotization and automation, they can meet the growing demands for quality, efficiency, and safety.
However, successful implementation requires careful planning, selecting appropriate technologies, and fostering an adaptive workforce culture.
Those that manage this transition will find themselves well-positioned to offer better products, foster innovation, and ensure sustainable growth in the competitive landscape of food manufacturing.
資料ダウンロード
QCD調達購買管理クラウド「newji」は、調達購買部門で必要なQCD管理全てを備えた、現場特化型兼クラウド型の今世紀最高の購買管理システムとなります。
ユーザー登録
調達購買業務の効率化だけでなく、システムを導入することで、コスト削減や製品・資材のステータス可視化のほか、属人化していた購買情報の共有化による内部不正防止や統制にも役立ちます。
NEWJI DX
製造業に特化したデジタルトランスフォーメーション(DX)の実現を目指す請負開発型のコンサルティングサービスです。AI、iPaaS、および先端の技術を駆使して、製造プロセスの効率化、業務効率化、チームワーク強化、コスト削減、品質向上を実現します。このサービスは、製造業の課題を深く理解し、それに対する最適なデジタルソリューションを提供することで、企業が持続的な成長とイノベーションを達成できるようサポートします。
オンライン講座
製造業、主に購買・調達部門にお勤めの方々に向けた情報を配信しております。
新任の方やベテランの方、管理職を対象とした幅広いコンテンツをご用意しております。
お問い合わせ
コストダウンが利益に直結する術だと理解していても、なかなか前に進めることができない状況。そんな時は、newjiのコストダウン自動化機能で大きく利益貢献しよう!
(Β版非公開)