- お役立ち記事
- Evolution of spherical fillers that achieve high thermal conductivity and low dielectric constant
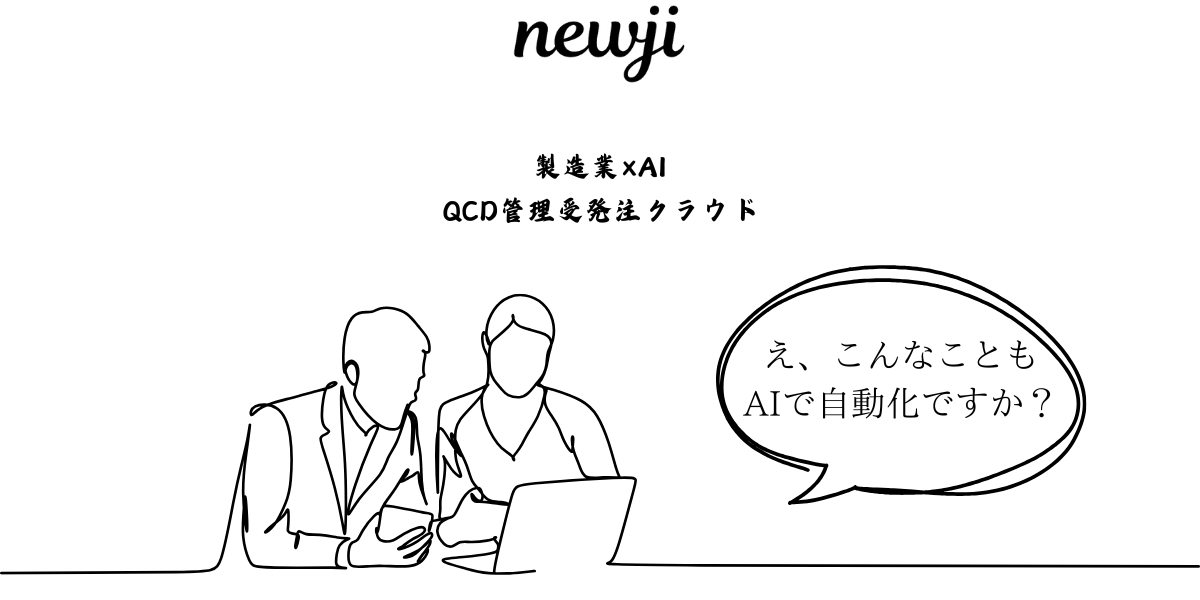
Evolution of spherical fillers that achieve high thermal conductivity and low dielectric constant
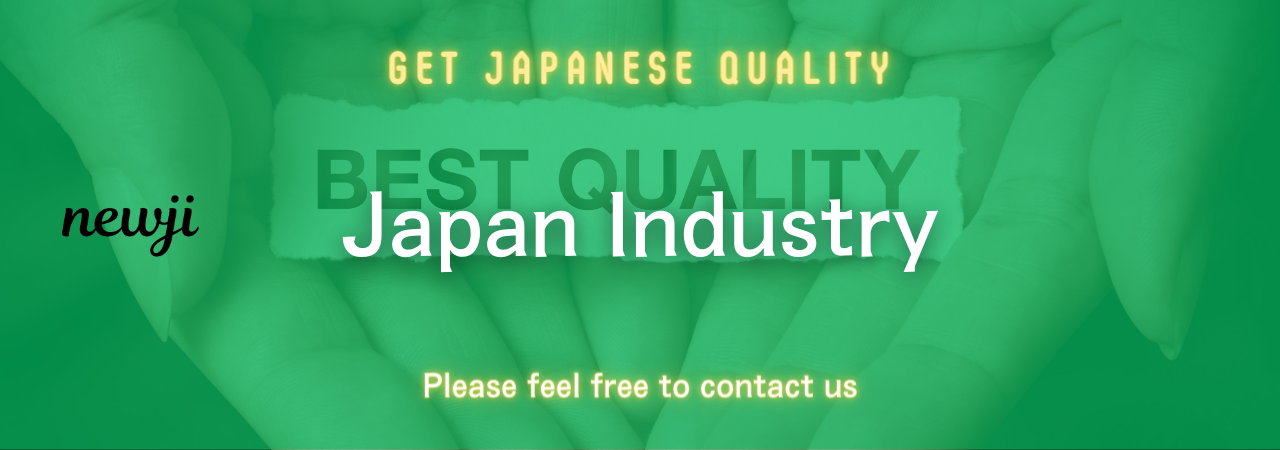
目次
Understanding Spherical Fillers
Spherical fillers have become a crucial component in various industries, especially in the development of materials with specific thermal and electrical properties.
In simple terms, these are small round particles added to materials to enhance their performance.
The goal is to achieve high thermal conductivity while maintaining a low dielectric constant, which is essential in many applications like electronics, automotive, and aerospace industries.
Thermal conductivity refers to a material’s ability to conduct heat, whereas the dielectric constant quantifies its ability to store electrical energy.
The Need for High Thermal Conductivity
High thermal conductivity in materials is essential to efficiently dissipate heat.
Devices and machinery often heat up during operation, and managing this heat is crucial to ensure optimal performance and longevity.
Materials with high thermal conductivity allow heat to pass through quickly, preventing the buildup that can lead to component damage or reduced efficiency.
This is especially important in electronics where overheating can shorten the lifespan of components or even cause failure.
Importance of Low Dielectric Constant
A low dielectric constant is equally significant, particularly in applications related to electronics and telecommunications.
Materials with a low dielectric constant reduce signal loss and improve the speed and efficiency of transmissions.
This is because fewer electrical charges are stored, decreasing the energy lost as heat.
Thus, by minimizing these losses, devices can operate faster and more effectively, making materials with these properties highly desirable.
Evolution of Spherical Fillers
The development of spherical fillers has made remarkable strides, driven by the continuous evolution of technology and the increasing demand for new material properties.
Early Spherical Fillers
Initially, spherical fillers were quite simplistic, often made from materials like glass or simple ceramics.
Their primary function was to improve material stability and provide mechanical strength.
However, they did not significantly address the need for enhanced thermal and electrical properties, which limited their application in high-tech industries.
Modern Spherical Fillers
Today’s spherical fillers are far more sophisticated.
Advanced materials like silicon carbide and boron nitride have been incorporated into filler designs, enhancing their ability to conduct heat.
Moreover, the manufacturing processes have improved significantly, allowing for the production of fillers with precise size and shape.
This precision ensures consistent performance across a range of applications.
Furthermore, modern fillers have been engineered to maintain a low dielectric constant alongside high thermal conductivity, a feat that was not attainable with earlier designs.
Innovative Composites
Composites made with spherical fillers offer versatile solutions to complex material challenges.
By combining fillers with polymers and other base materials, manufacturers can tailor the properties of the final product to meet specific needs.
This customization is vital in industries where precise material specifications are required.
Researchers continue to experiment with hybrid fillers combining different materials to achieve even greater performance enhancements, such as combining metallic and ceramic fillers to balance electrical and thermal properties effectively.
Applications in Modern Technology
The evolution of spherical fillers has paved the way for their utilization in various cutting-edge technologies.
Electronics
In the electronics industry, high thermal conductivity and low dielectric constant materials are essential.
Smartphones, tablets, and laptops all benefit from these materials, ensuring devices operate efficiently without overheating.
Filler-enhanced composites are used in circuit boards and chip packaging, vital components that require robust thermal management.
Automotive and Aerospace Industries
Cars and aircraft are becoming more reliant on sophisticated electronics and materials.
In these sectors, weight reduction without sacrificing performance is critical.
Spherical fillers contribute by providing lightweight materials with the thermal and electrical properties needed for applications such as battery cooling systems in electric vehicles or thermal barriers in airplane engines.
Telecommunication
The expansion of telecommunications technology, including 5G networks, has increased the need for materials that maintain signal integrity.
Spherical fillers help create materials that are suitable for antennas and other components, balancing thermal management with minimal signal interference.
Future Directions and Innovations
The continuous pursuit of more efficient materials drives ongoing research and innovation in spherical fillers.
Nano-Fillers
The future may see an increased use of nano-scale spherical fillers that offer even greater precision in modifying material properties.
These tiny fillers can lead to more refined control of thermal and dielectric characteristics, enhancing applications in all current domains.
Eco-Friendly Solutions
As environmental concerns grow, there is an emerging push towards developing fillers made from sustainable materials.
Bio-based fillers or those that are easier to recycle may become more prominent, helping to reduce the environmental impact of high-tech industries.
Integrated Systems
Advancements in smart manufacturing could lead to integrated systems where spherical fillers are precisely applied during the production process.
Such systems could drastically reduce material wastage and improve overall production efficiency while ensuring consistency in product quality.
In conclusion, the continued evolution and application of spherical fillers exemplify the ever-growing demand for materials that can meet specific performance criteria.
These advancements enable the high-tech solutions of today and promise an exciting potential for future innovations in material science and industrial applications.
資料ダウンロード
QCD調達購買管理クラウド「newji」は、調達購買部門で必要なQCD管理全てを備えた、現場特化型兼クラウド型の今世紀最高の購買管理システムとなります。
ユーザー登録
調達購買業務の効率化だけでなく、システムを導入することで、コスト削減や製品・資材のステータス可視化のほか、属人化していた購買情報の共有化による内部不正防止や統制にも役立ちます。
NEWJI DX
製造業に特化したデジタルトランスフォーメーション(DX)の実現を目指す請負開発型のコンサルティングサービスです。AI、iPaaS、および先端の技術を駆使して、製造プロセスの効率化、業務効率化、チームワーク強化、コスト削減、品質向上を実現します。このサービスは、製造業の課題を深く理解し、それに対する最適なデジタルソリューションを提供することで、企業が持続的な成長とイノベーションを達成できるようサポートします。
オンライン講座
製造業、主に購買・調達部門にお勤めの方々に向けた情報を配信しております。
新任の方やベテランの方、管理職を対象とした幅広いコンテンツをご用意しております。
お問い合わせ
コストダウンが利益に直結する術だと理解していても、なかなか前に進めることができない状況。そんな時は、newjiのコストダウン自動化機能で大きく利益貢献しよう!
(Β版非公開)