- お役立ち記事
- How to find a company that can assemble jigs for auto parts
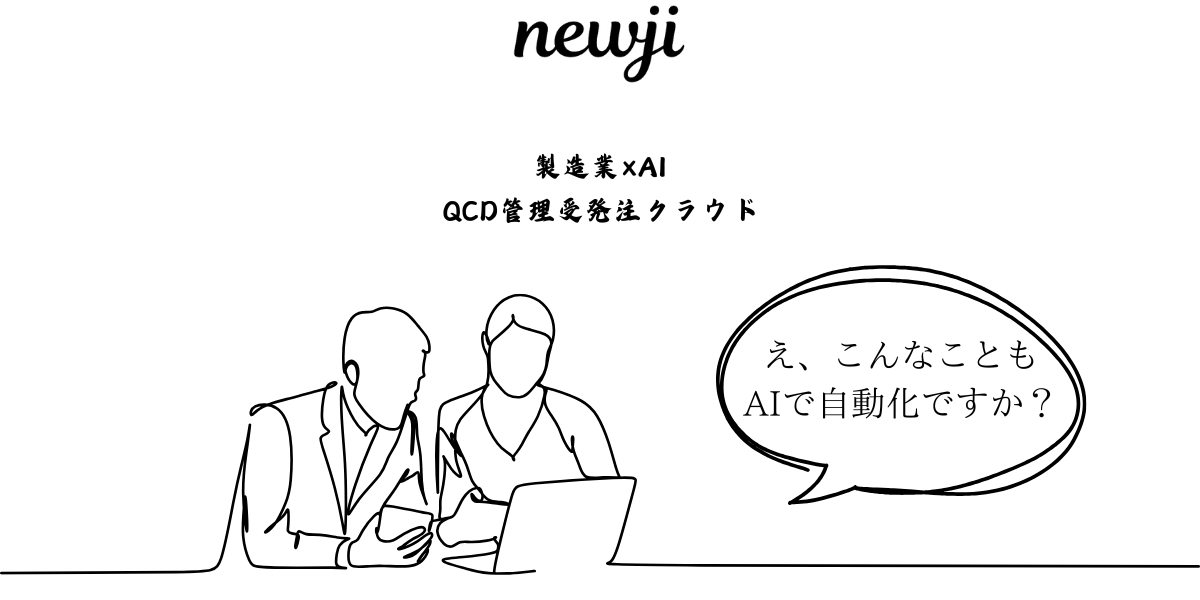
How to find a company that can assemble jigs for auto parts
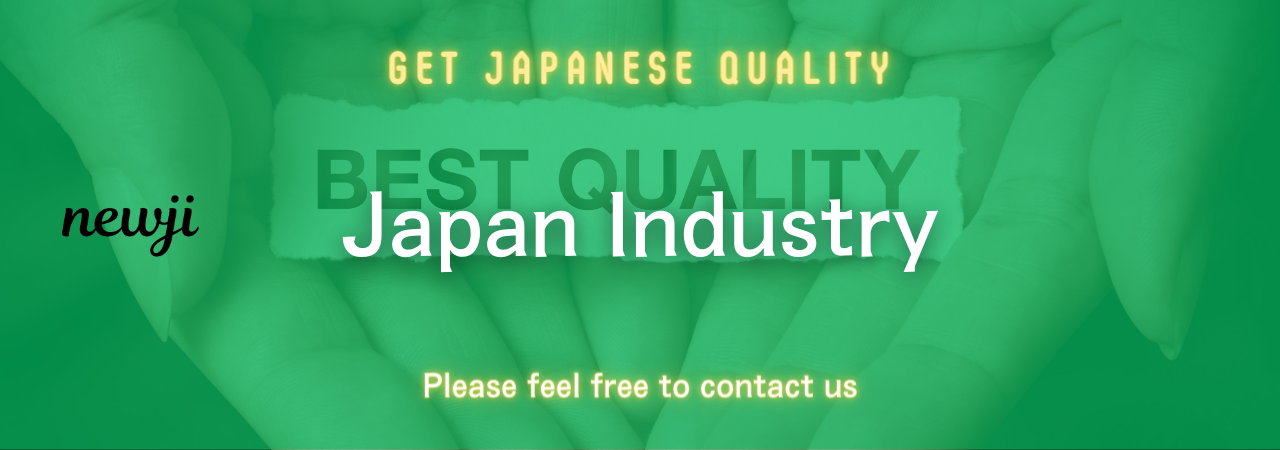
目次
Understanding Jigs for Auto Parts
Before diving into the search for a company that can assemble jigs, it’s essential to understand what jigs are in the context of auto parts.
Jigs are custom-made tools used to control the location and/or motion of parts or other tools during manufacturing.
In the automotive industry, jigs play a crucial role in ensuring that parts are produced with precision and consistency.
They help in assembling parts accurately, thus enhancing the overall quality of the final product.
Having the right company to assemble jigs means ensuring quality and efficiency in the manufacture of auto parts.
Importance of Choosing the Right Company
Selecting a company to assemble jigs for auto parts is an important decision that can impact production quality, efficiency, and cost.
The right company will have the expertise, technology, and experience to deliver jigs that meet specific requirements and standards.
An accurate jig helps reduce errors in the manufacturing process, saving time and resources in the long run.
Thus, investing time and effort in finding the best company is crucial for the success of your production line.
Research Companies with Experience
The first step in finding a company to assemble jigs for auto parts is conducting thorough research.
Look for companies with proven experience in creating jigs for the automotive industry.
This is crucial as the intricacies of auto parts require specialized knowledge and skills.
A company with a track record of providing high-quality jigs will likely meet your expectations and requirements.
Check Their Portfolio
By reviewing a company’s portfolio, you can gain insights into their expertise and the types of projects they have handled in the past.
An impressive portfolio indicates that the company has diverse experience and capabilities in producing jigs for various auto parts.
This not only assures you of their proficiency but also helps to understand the quality of their work.
Read Client Testimonials
Client testimonials and reviews are valuable resources when assessing a company’s reliability and efficiency.
Feedback from previous clients provides a realistic picture of what it’s like to work with the company.
Pay attention to comments about the quality of the jigs, the company’s customer service, and their ability to meet deadlines.
Evaluate the Company’s Technology and Equipment
The technology and equipment used in profiling and assembling jigs are critical factors to consider.
A company with modern and advanced technology is more likely to produce high-quality jigs that meet precise specifications.
Ensure the company has the latest machinery and tools required for the production of automotive jigs.
Up-to-date equipment not only increases accuracy but also boosts production efficiency.
Consider Their Engineering Team
The engineering team is the backbone of any company specializing in jig assembly.
It’s essential to verify that the company has a team of skilled and experienced engineers capable of designing and assembling custom jigs.
A competent engineering team will understand the complexities involved in auto part manufacturing and offer solutions tailored to your specific needs.
Certifications and Training
Check whether the engineering team holds relevant certifications and undergoes regular training.
Certifications indicate a certain level of proficiency and commitment to maintaining industry standards.
Regular training ensures that the team is updated with the latest trends and technologies in jig manufacturing.
Assess Their Quality Control Processes
Ensuring high-quality standards is crucial in jig assembly, especially in the automotive sector where precision is key.
Look for a company that implements stringent quality control measures throughout the jig assembly process.
This includes testing the jigs for durability, accuracy, and performance before delivery.
A company with a robust quality control process is likely to provide jigs that enhance the production process and reduce the chances of manufacturing defects.
Inquire About Production Capacity and Lead Times
Understanding a company’s production capacity is important to ensure that they can meet your demands without compromising quality.
Inquire about their lead times to ensure that they align with your project timelines.
A company with a flexible production capacity can adapt to your needs and help prevent production delays.
Discuss Pricing and Value
While cost is an important factor, it should not be the sole determinant in choosing a jig assembly company.
Discuss pricing in detail to understand what is included and what additional costs might arise.
It’s important to consider the value provided, such as quality of workmanship, customer service, and after-sales support, rather than focusing solely on the cost.
Request Quotations and Compare
Obtain detailed quotations from multiple companies to compare pricing and services offered.
Ensure that the quotations clearly state the costs involved and the scope of the work to avoid any hidden charges.
This comparison helps in making an informed decision when selecting a company that offers the best value for money.
Evaluate Their After-Sales Support
After-sales support is crucial in maintaining the functionality and longevity of the jigs.
Choose a company that offers comprehensive after-sales service, including maintenance, repairs, and technical support.
Reliable after-sales support helps in addressing any issues quickly, minimizing disruptions in the production process.
Conclusion
Finding the right company to assemble jigs for auto parts involves thorough research, evaluation of their expertise, technology, and services.
By assessing their portfolio, quality control measures, production capacity, and after-sales support, you can select a company that best suits your needs.
Remember, the aim is to establish a long-term partnership that ensures efficiency and high-quality production of auto parts.
資料ダウンロード
QCD調達購買管理クラウド「newji」は、調達購買部門で必要なQCD管理全てを備えた、現場特化型兼クラウド型の今世紀最高の購買管理システムとなります。
ユーザー登録
調達購買業務の効率化だけでなく、システムを導入することで、コスト削減や製品・資材のステータス可視化のほか、属人化していた購買情報の共有化による内部不正防止や統制にも役立ちます。
NEWJI DX
製造業に特化したデジタルトランスフォーメーション(DX)の実現を目指す請負開発型のコンサルティングサービスです。AI、iPaaS、および先端の技術を駆使して、製造プロセスの効率化、業務効率化、チームワーク強化、コスト削減、品質向上を実現します。このサービスは、製造業の課題を深く理解し、それに対する最適なデジタルソリューションを提供することで、企業が持続的な成長とイノベーションを達成できるようサポートします。
オンライン講座
製造業、主に購買・調達部門にお勤めの方々に向けた情報を配信しております。
新任の方やベテランの方、管理職を対象とした幅広いコンテンツをご用意しております。
お問い合わせ
コストダウンが利益に直結する術だと理解していても、なかなか前に進めることができない状況。そんな時は、newjiのコストダウン自動化機能で大きく利益貢献しよう!
(Β版非公開)