- お役立ち記事
- Specific measures to optimize cost allocation in prototyping
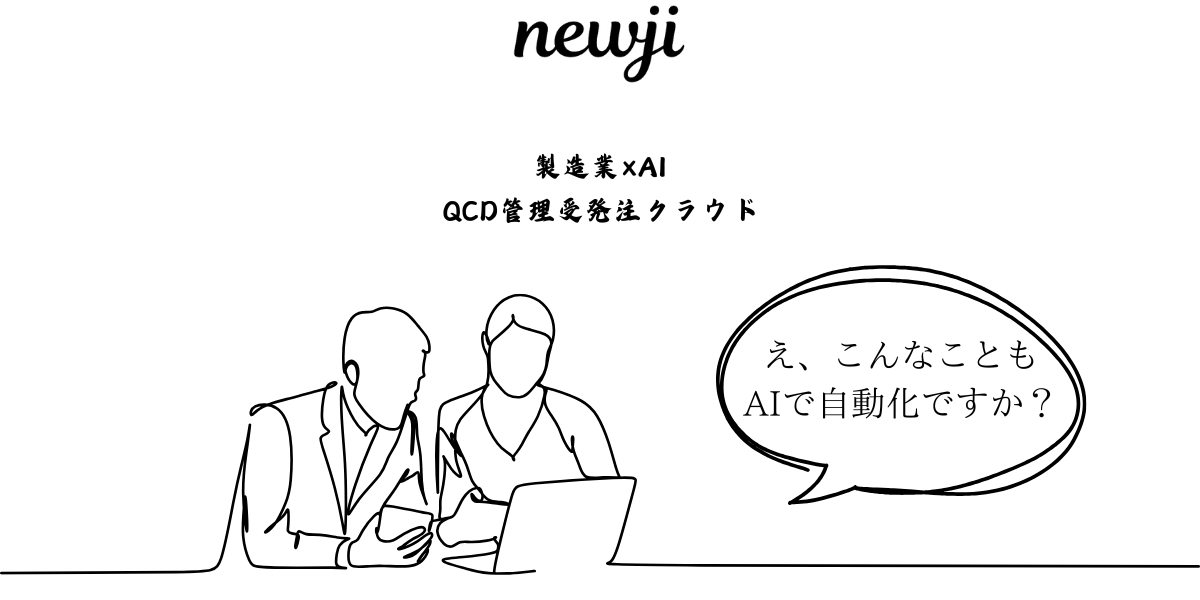
Specific measures to optimize cost allocation in prototyping
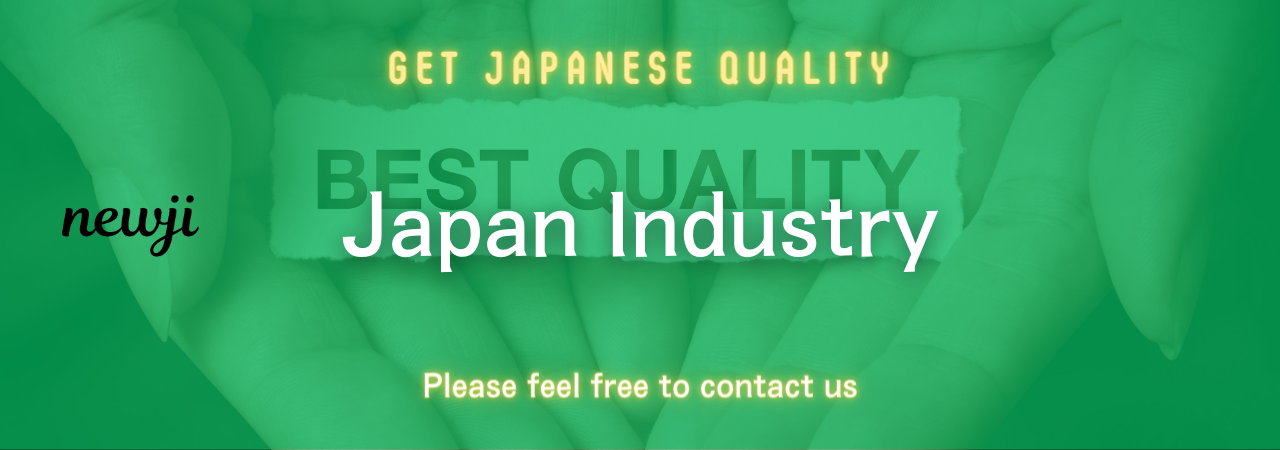
Understanding Cost Allocation in Prototyping
Prototyping is a crucial stage in product development, where ideas are transformed into tangible forms that stakeholders can evaluate and improve.
However, one significant challenge in this phase is managing and optimizing cost allocation.
Understanding the components involved and the implications of each expense is essential for ensuring that resources are used effectively.
Cost allocation in prototyping involves distributing expenses across various aspects of the process, such as materials, labor, and equipment.
Each of these categories has its own set of variables that can impact the overall budget.
By analyzing these factors, businesses can identify areas where cost savings are possible without sacrificing quality or slowing down development.
Breaking Down the Costs
To optimize cost allocation, it’s important to know where money is being spent.
Common cost components in prototyping include:
Material Costs
Materials make up a significant portion of prototyping expenses.
Depending on the complexity and requirements of a prototype, costs can vary greatly.
For instance, 3D printing materials such as resins or filaments might be cheaper than using metals or specialized composites.
Conducting an initial assessment to determine the least expensive yet effective materials can help reduce costs.
Labor Costs
Labor is another critical area where costs can quickly accumulate.
This includes not just the physical building of the prototype but also the design and engineering processes.
Investing in skilled workers might seem costly upfront, but their expertise can lead to more efficient production and fewer errors, potentially saving money in the long run.
Equipment Costs
Prototyping often requires specialized machinery, such as 3D printers or CNC machines.
These can be expensive to purchase and maintain.
Businesses may consider leasing equipment or using outsourcing services as cost-effective alternatives, especially if prototyping needs are infrequent or variable.
Strategies for Optimizing Cost Allocation
Once the cost components are identified, several strategies can be applied to optimize allocation and reduce overall expenses effectively.
Leveraging Technology
Advancements in technology offer ways to reduce prototyping costs significantly.
For example, simulation software can reduce the number of physical prototypes needed by allowing virtual testing and modification of designs.
This technology can avoid errors and improve designs before any physical model is created.
3D printing is another technology that can streamline the prototyping process, allowing for rapid production and reducing material waste.
By adopting these technologies, businesses can optimize the cost allocation more efficiently.
Outsourcing and Collaboration
Partnering with external prototyping firms can also be a cost-effective strategy.
This approach can reduce the need for investing in costly equipment and also provide access to specialized expertise.
Additionally, collaborating with other companies on projects can help share costs and resources.
It’s important to choose partners who align with your project goals to ensure a successful collaboration.
Iterative Design Process
Implementing an iterative design process can significantly reduce prototyping costs.
This method involves creating multiple small-scale prototypes and testing them before finalizing the design.
By refining designs progressively, businesses can identify and correct errors early, reducing the need for costly modifications later on.
An iterative process allows teams to make informed decisions about design improvements and ensures a more efficient allocation of resources.
Assessing Prototype Necessity
Not every component of a design requires a prototype.
Careful evaluation of design elements can help determine which aspects are most critical for physical prototyping and which can be assessed virtually or skipped altogether.
This prioritization ensures that resources are allocated to the most necessary areas, maximizing the value of the prototyping phase.
Integrating Cost Control Measures
Implementing cost control measures is another significant step in optimizing cost allocation.
This includes setting a budget cap for prototyping expenses and regularly reviewing costs to identify any deviations from the budget.
Businesses should establish a clear process for approving expenses to ensure that all costs are necessary and justified.
Regular audits can help identify areas where costs can be reduced or where there may be potential for over-expenditure.
Conclusion
Optimizing cost allocation in prototyping is essential for staying within budget and ensuring effective resource use.
By understanding the main cost components—materials, labor, and equipment—and applying various strategies, businesses can significantly reduce expenses without compromising the quality or speed of development.
Employing technology, outsourcing, adopting an iterative process, and implementing robust cost control measures are all effective ways to optimize cost allocation in prototyping.
Ultimately, strategic cost allocation helps in achieving a more efficient and impactful prototyping phase, paving the way for successful product development.
資料ダウンロード
QCD調達購買管理クラウド「newji」は、調達購買部門で必要なQCD管理全てを備えた、現場特化型兼クラウド型の今世紀最高の購買管理システムとなります。
ユーザー登録
調達購買業務の効率化だけでなく、システムを導入することで、コスト削減や製品・資材のステータス可視化のほか、属人化していた購買情報の共有化による内部不正防止や統制にも役立ちます。
NEWJI DX
製造業に特化したデジタルトランスフォーメーション(DX)の実現を目指す請負開発型のコンサルティングサービスです。AI、iPaaS、および先端の技術を駆使して、製造プロセスの効率化、業務効率化、チームワーク強化、コスト削減、品質向上を実現します。このサービスは、製造業の課題を深く理解し、それに対する最適なデジタルソリューションを提供することで、企業が持続的な成長とイノベーションを達成できるようサポートします。
オンライン講座
製造業、主に購買・調達部門にお勤めの方々に向けた情報を配信しております。
新任の方やベテランの方、管理職を対象とした幅広いコンテンツをご用意しております。
お問い合わせ
コストダウンが利益に直結する術だと理解していても、なかなか前に進めることができない状況。そんな時は、newjiのコストダウン自動化機能で大きく利益貢献しよう!
(Β版非公開)