- お役立ち記事
- Practical example of reducing lead time in the prototyping process
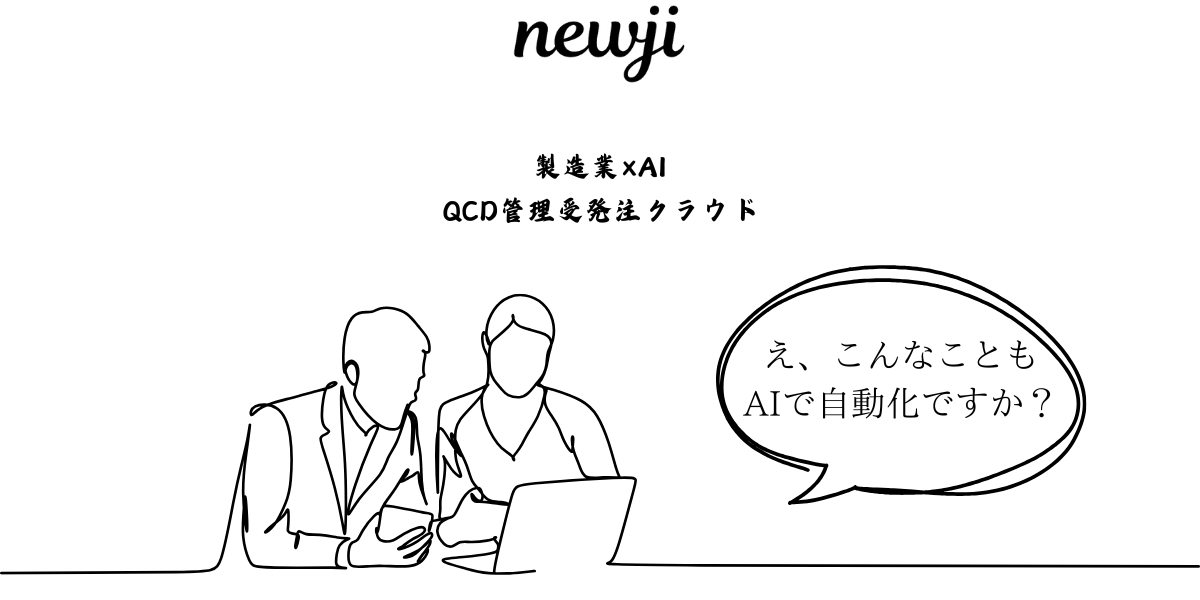
Practical example of reducing lead time in the prototyping process
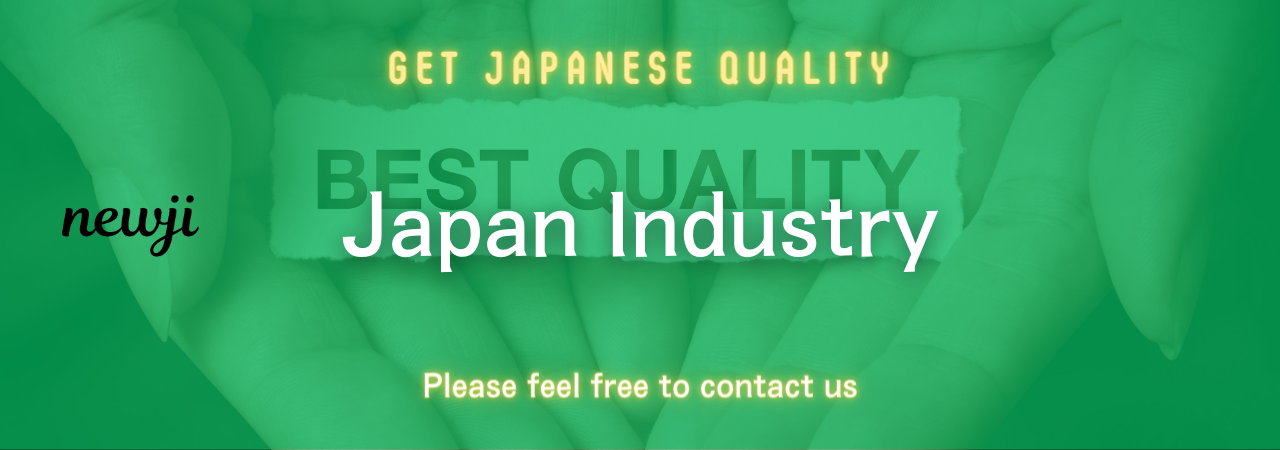
目次
Understanding Lead Time in the Prototyping Process
Lead time refers to the duration taken from the initial concept of a product to its deployment or market release.
In prototyping, reducing lead time is essential because it allows companies to innovate and respond to market needs swiftly.
When companies can speed up their prototyping process, they gain a competitive edge by bringing products to market faster and potentially lowering costs.
The Importance of Reducing Lead Time
Reducing lead time is crucial for several reasons.
Firstly, it enables companies to quickly adapt to evolving market trends and customer demands.
This agility can make the difference between leading a market or lagging behind competitors.
Secondly, by minimizing lead time, businesses can test and iterate on their designs more effectively.
Prototyping is inherently about experimentation and testing hypotheses.
Shorter cycles mean that teams can learn from mistakes and make necessary adjustments without significant delays.
Lastly, reducing lead time often correlates with cost savings.
Less time spent in development can equate to fewer resources allocated to any given project phase, resulting in more efficient use of budgets.
Strategies for Reducing Lead Time
There are several strategies companies can implement to reduce lead time in their prototyping process.
These strategies focus on streamlining workflows, enhancing communication, and leveraging technology.
1. Implement Agile Methodologies
Adopting agile practices can significantly impact the prototyping lead time.
This approach emphasizes flexibility, collaboration, and customer feedback, allowing teams to work in incremental steps and continuously improve the product.
Instead of following a linear approach, agile methodologies encourage multi-disciplinary teams to work concurrently, accelerating the overall process.
2. Leverage Rapid Prototyping Technologies
Rapid prototyping technologies, such as 3D printing, can drastically reduce the time needed to create physical prototypes.
These technologies allow designers and engineers to quickly produce and test models, leading to faster feedback loops and adjustments.
With the ability to create complex models directly from digital files, teams can iterate designs much more swiftly than traditional manufacturing methods allow.
3. Enhance Communication and Collaboration
Effective communication is vital for reducing lead time.
Ensuring that all team members, stakeholders, and departments are aligned from the start can prevent misunderstandings and misalignments that often lead to delays.
Using collaborative tools, real-time data sharing, and regular updates helps keep everyone on the same page.
Moreover, fostering a culture of open communication encourages team members to voice concerns or suggest improvements, which can lead to more efficient processes.
4. Utilize Concurrent Engineering
Concurrent engineering involves parallelizing tasks rather than performing them sequentially.
By overlapping phases of development, such as design, testing, and manufacturing planning, teams can shorten the overall project time.
This method requires a coordinated effort and robust project management but can significantly trim lead times if executed effectively.
5. Invest in Advanced Software Solutions
Software solutions, such as computer-aided design (CAD) and project management tools, can streamline the prototyping process.
These applications help automate repetitive tasks, manage resources efficiently, and track progress in real-time.
By integrating these technologies, teams can reduce the time spent on administrative tasks and focus more on innovation and testing.
Real-World Examples of Reduced Lead Time
To illustrate the impact of reducing lead time, let’s look at real-world examples where companies have effectively implemented strategies to accelerate their prototyping processes.
Ford’s Use of 3D Printing
Ford has been a pioneer in using 3D printing technology to reduce lead time in its prototyping processes.
By creating parts and components using additive manufacturing, Ford’s engineers can produce prototypes in hours rather than weeks.
This rapid feedback loop allows for more iterations and improvements, ultimately speeding up the development of new vehicles.
Google’s Agile Approach
Google’s product development teams often embrace agile methodologies, focusing on collaboration and iterative improvements.
By breaking down projects into smaller, manageable sprints, they can test ideas, gather user feedback, and refine designs rapidly.
This process not only reduces lead time but also ensures that products meet user expectations and needs more effectively.
Tesla’s Concurrent Engineering
Tesla is renowned for its ability to bring products to market quickly, partly due to its concurrent engineering practices.
By running design, testing, and production planning simultaneously, Tesla compresses its development timelines significantly.
This approach has enabled Tesla to innovate quickly in the competitive automotive industry.
Conclusion
Reducing lead time in the prototyping process is crucial for staying competitive and meeting consumer demands in today’s fast-paced market.
By adopting strategies such as agile methodologies, rapid prototyping technologies, and concurrent engineering, companies can bring products to market faster and more efficiently.
Real-world examples from Ford, Google, and Tesla demonstrate the tangible benefits of these approaches, highlighting the potential for innovation and success when lead times are minimized.
資料ダウンロード
QCD調達購買管理クラウド「newji」は、調達購買部門で必要なQCD管理全てを備えた、現場特化型兼クラウド型の今世紀最高の購買管理システムとなります。
ユーザー登録
調達購買業務の効率化だけでなく、システムを導入することで、コスト削減や製品・資材のステータス可視化のほか、属人化していた購買情報の共有化による内部不正防止や統制にも役立ちます。
NEWJI DX
製造業に特化したデジタルトランスフォーメーション(DX)の実現を目指す請負開発型のコンサルティングサービスです。AI、iPaaS、および先端の技術を駆使して、製造プロセスの効率化、業務効率化、チームワーク強化、コスト削減、品質向上を実現します。このサービスは、製造業の課題を深く理解し、それに対する最適なデジタルソリューションを提供することで、企業が持続的な成長とイノベーションを達成できるようサポートします。
オンライン講座
製造業、主に購買・調達部門にお勤めの方々に向けた情報を配信しております。
新任の方やベテランの方、管理職を対象とした幅広いコンテンツをご用意しております。
お問い合わせ
コストダウンが利益に直結する術だと理解していても、なかなか前に進めることができない状況。そんな時は、newjiのコストダウン自動化機能で大きく利益貢献しよう!
(Β版非公開)