- お役立ち記事
- Clean room basics, cleaning technology, optimal management methods and their key points
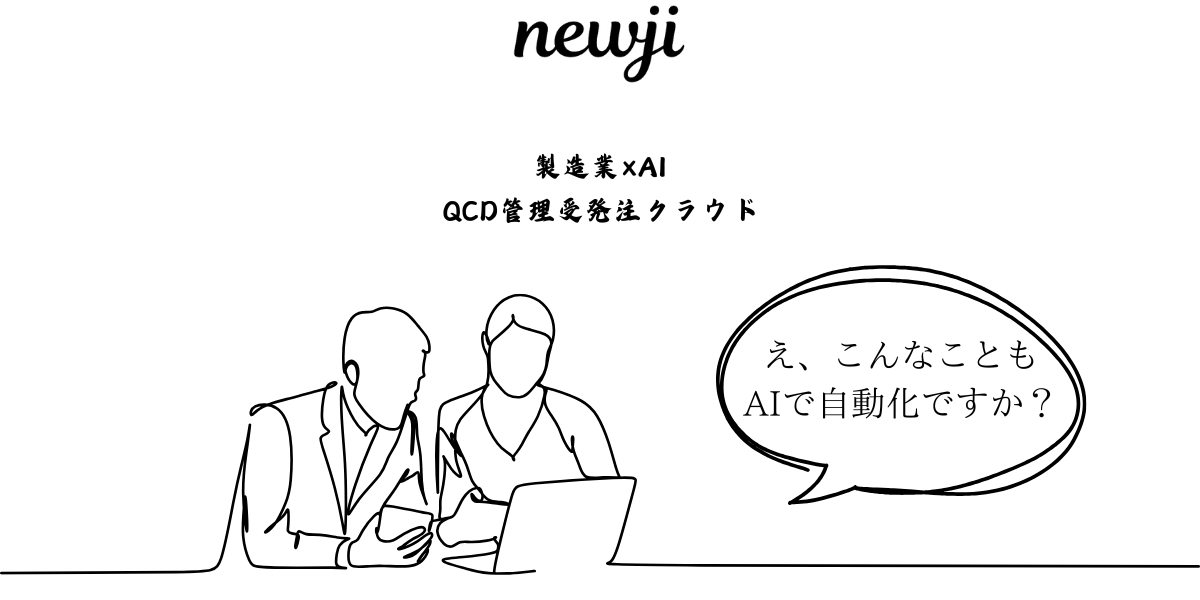
Clean room basics, cleaning technology, optimal management methods and their key points
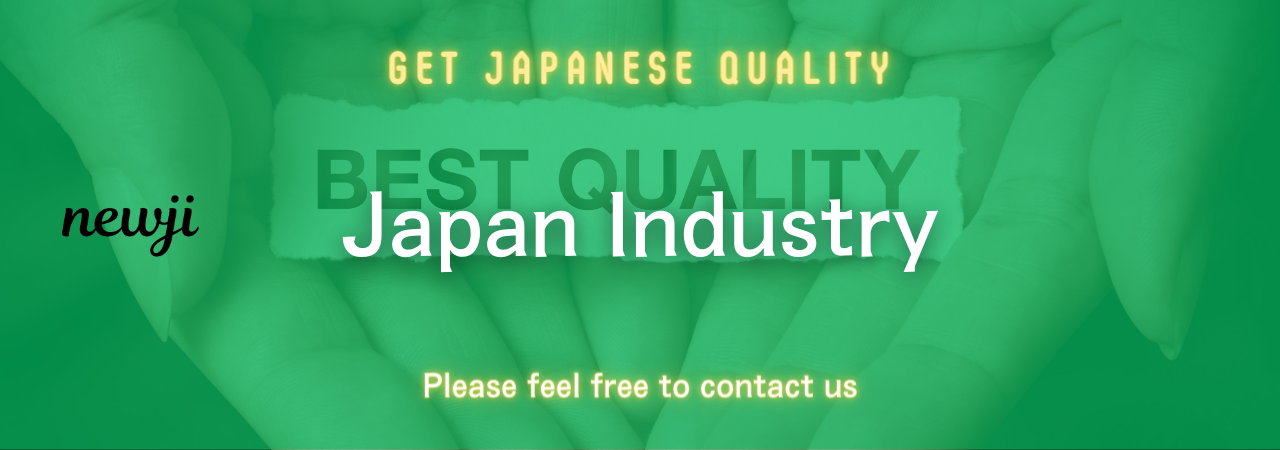
目次
Understanding Clean Rooms
A clean room is a controlled environment where pollutants like dust, airborne microbes, and chemical vapors are filtered out to provide the cleanest area possible.
The goal is to minimize the introduction, generation, and retention of particles within the room.
Clean rooms are essential in manufacturing industries such as pharmaceuticals, semiconductors, and biotechnology, where a particle-free atmosphere is crucial.
Clean rooms vary in size and complexity and are used extensively in industries where small particles can adversely affect the manufacturing process.
To ensure a clean environment, all aspects of the room, from the air quality to the surfaces and equipment, are strictly controlled through advanced cleaning technologies and optimal management methods.
Key Concepts in Clean Room Technology
Air Quality Management
Air quality in a clean room is maintained using specialized filtration systems that remove contaminants.
High-Efficiency Particulate Air (HEPA) filters are commonly used to trap particulate matter, while Ultra-Low Penetration Air (ULPA) filters offer even higher efficiency for capturing smaller particles.
These filters work together with controlled air flow, typically provided by a unidirectional, laminar flow system, which directs air in a parallel stream vertically or horizontally across the room.
Contamination Control
Contaminant control involves minimizing the introduction of particles into the clean room.
Materials of construction, personnel, and equipment are all potential sources of contamination.
Personnel are required to wear special garments like coveralls, masks, gloves, and booties, which are made from materials that minimize shedding.
Equipment and materials brought into the clean room undergo strict decontamination procedures, including wiping with alcohol solutions and using sealed containers.
Environmental Monitoring
Continuous environmental monitoring is a crucial aspect of clean room technology, involving regular checks of particle counts, air temperature, humidity, and differential pressure.
These parameters are closely monitored through sophisticated digital systems to ensure that they comply with the specific requirements of the clean room’s application.
Any deviation from the set parameters triggers an immediate corrective action to prevent contamination.
Cleaning Protocols in Clean Rooms
Scheduled Cleaning
Regular cleaning schedules are a critical component of maintaining a clean room.
Daily cleaning tasks typically include wiping down surfaces, cleaning floors, and making sure that biohazardous waste is properly disposed of.
More thorough, weekly, or monthly cleaning includes disassembling equipment for detailed cleaning and replacing air filters as necessary.
This ensures a consistently clean environment that aligns with industry standards.
Proper Cleaning Agents
Choosing the appropriate cleaning agents is vital in controlling contamination without damaging surfaces or equipment.
Disinfectants and cleaning agents are selected based on their effectiveness against specific contaminants and their compatibility with clean room materials.
Solutions are usually applied using lint-free wipes or mops, followed by rinsing with distilled water to avoid any residue.
Training and Procedures
Personnel training is crucial for maintaining the integrity of a clean room.
Staff must be educated on effective cleaning procedures, the proper use of personal protective equipment, and the importance of maintaining strict cleanliness protocols.
Regular training updates ensure that all personnel are aware of the latest cleaning techniques and technologies.
Optimal Management Methods
Clean Room Design
The design of a clean room is fundamental to its efficiency.
An optimal clean room layout includes proper placement of filters, strategic air flow patterns, and selection of materials resistant to contamination and easy to clean.
The layout should also allow for easy movement and minimal disruption during maintenance and cleaning cycles.
Documentation and Compliance
Documentation and compliance are vital aspects of clean room management.
Regulatory bodies set standards to ensure clean rooms maintain specified cleanliness levels, and detailed records must be kept to demonstrate compliance with these standards.
Documenting procedures, cleaning schedules, material data, and training records is essential for quality assurance and audits.
Regular Maintenance and Inspection
Regular maintenance and inspection of clean room facilities and equipment ensure optimal functioning.
Scheduled checks include inspecting air filtration systems, validating environmental monitoring equipment, and verifying the integrity of the room’s structural components.
Timely maintenance prevents potential breaches in clean room protocols and ensures continuous compliance with industry standards.
Key Points for Maintaining Clean Rooms
Understanding Clean Room Standards
Clean room standards define the limits of allowable contamination.
ISO 14644-1 and Federal Standard 209E are internationally recognized standards that classify clean rooms based on their cleanliness level.
Understanding these standards helps in designing cleaning protocols and management practices tailored to specific industry requirements.
Adopting Advanced Technologies
Modern clean room technology continues to evolve, offering new solutions for contamination control and environmental monitoring.
Adopting advanced technologies such as automated cleaning robots, IoT for real-time monitoring, and data analytics for predictive maintenance can significantly enhance clean room management.
Promoting a Culture of Cleanliness
Promoting a culture of cleanliness within the organization is critical for maintaining clean rooms.
Encouraging all personnel to adhere to established protocols, report any contamination incidents, and participate in continuous improvement initiatives fosters a collective awareness and commitment to cleanliness.
By understanding clean room basics, implementing effective cleaning technologies, and adopting optimal management methods, industries can ensure that their clean rooms operate at peak efficiency.
This is crucial for producing high-quality products and fostering innovation in fields where precision and cleanliness are paramount.
資料ダウンロード
QCD調達購買管理クラウド「newji」は、調達購買部門で必要なQCD管理全てを備えた、現場特化型兼クラウド型の今世紀最高の購買管理システムとなります。
ユーザー登録
調達購買業務の効率化だけでなく、システムを導入することで、コスト削減や製品・資材のステータス可視化のほか、属人化していた購買情報の共有化による内部不正防止や統制にも役立ちます。
NEWJI DX
製造業に特化したデジタルトランスフォーメーション(DX)の実現を目指す請負開発型のコンサルティングサービスです。AI、iPaaS、および先端の技術を駆使して、製造プロセスの効率化、業務効率化、チームワーク強化、コスト削減、品質向上を実現します。このサービスは、製造業の課題を深く理解し、それに対する最適なデジタルソリューションを提供することで、企業が持続的な成長とイノベーションを達成できるようサポートします。
オンライン講座
製造業、主に購買・調達部門にお勤めの方々に向けた情報を配信しております。
新任の方やベテランの方、管理職を対象とした幅広いコンテンツをご用意しております。
お問い合わせ
コストダウンが利益に直結する術だと理解していても、なかなか前に進めることができない状況。そんな時は、newjiのコストダウン自動化機能で大きく利益貢献しよう!
(Β版非公開)