- お役立ち記事
- FMEA, efficient prevention practices and effective use for DR
月間77,185名の
製造業ご担当者様が閲覧しています*
*2025年2月28日現在のGoogle Analyticsのデータより
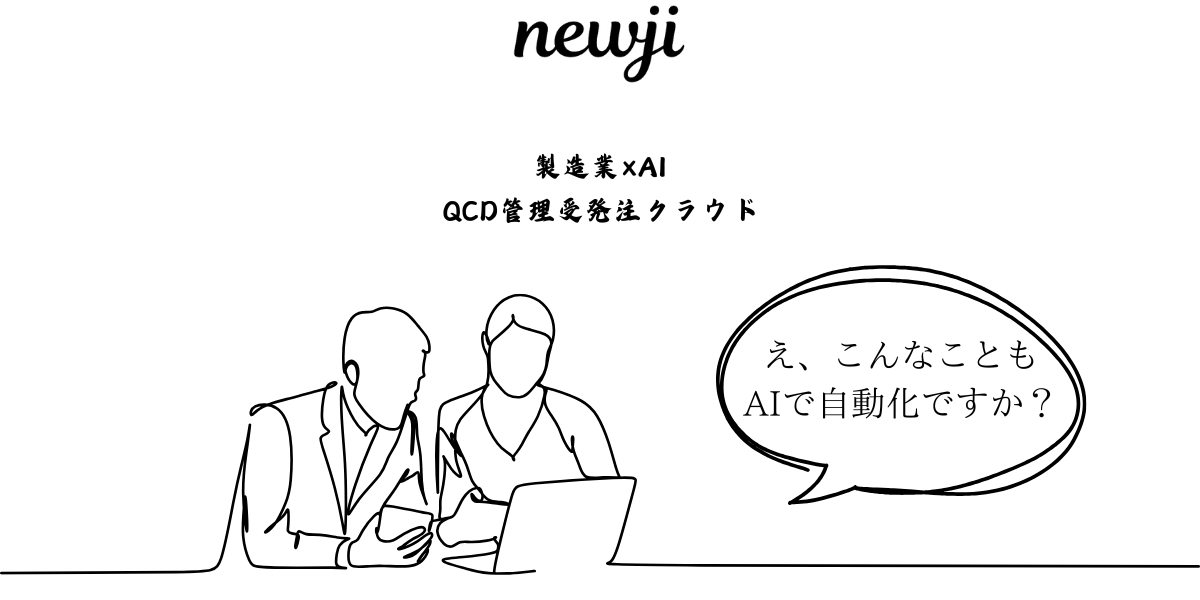
FMEA, efficient prevention practices and effective use for DR
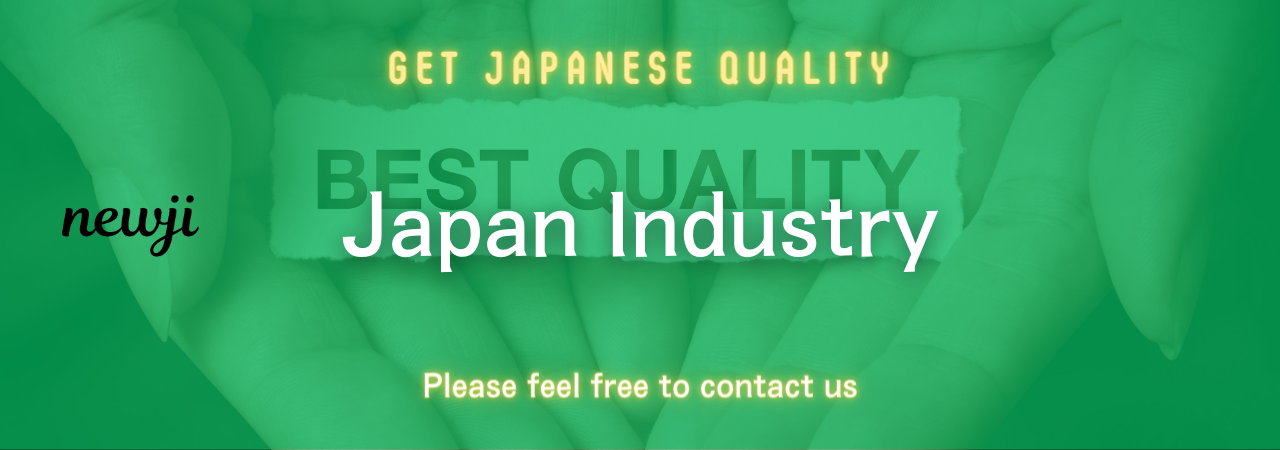
FMEA, or Failure Mode and Effects Analysis, is a systematic method used by organizations to identify and prevent potential failures in a product or process before they occur.
By understanding and addressing these potential issues early, companies can improve the quality and reliability of their products.
Let’s explore the concept of FMEA, efficient prevention practices, and how it can be effectively used for Design Review (DR).
目次
Understanding FMEA
Failure Mode and Effects Analysis is a step-by-step approach that helps industries identify potential failure modes in a system.
These can range from defects in a product to inefficiencies in a process.
By analyzing these modes, FMEA allows organizations to prioritize their responses based on the potential impact of the failure.
The fundamental goal of FMEA is to reduce risk and improve the reliability of products or processes.
The analysis involves three primary components: potential failure modes, potential effects of failure, and potential causes of failure.
Each of these components is assessed to determine its significance and the best course of action to prevent the failure from occurring.
Efficient Prevention Practices
To make the most of FMEA, it’s important to implement efficient prevention practices.
Here are some practices that can enhance the effectiveness of FMEA:
Early Integration in the Design Process
Integrating FMEA early in the design process allows for the identification of potential failure modes before they become ingrained in the final design.
This proactive approach is cost-effective and increases the likelihood of resolving issues efficiently.
Cross-Functional Teams
FMEA should be conducted by a cross-functional team composed of members from various departments such as design, engineering, manufacturing, and quality assurance.
This diverse expertise provides a comprehensive perspective on potential failures and their impacts, ensuring no aspect is overlooked.
Regular Updates and Reviews
FMEA is not a one-time task; it should be regularly updated and reviewed throughout the lifecycle of a product or process.
As new data becomes available or changes are made, revisiting the FMEA analysis ensures that new risks are identified and mitigated.
Utilizing FMEA Software
Incorporating FMEA-specific software tools can streamline the analysis process.
These tools provide structured templates, risk assessment matrices, and facilitation of collaboration, making it easier for teams to conduct thorough analyses.
Employee Training and Awareness
Educating employees about the importance of FMEA and how it applies to their roles encourages a culture of quality and risk-awareness throughout the organization.
Regular training sessions can help team members stay informed and engaged.
Effective Use of FMEA for Design Review (DR)
Design Review is a critical phase in the product development lifecycle where designs are systematically evaluated against specified requirements.
Using FMEA during DR can significantly enhance the review process by identifying potential risks and vulnerabilities early.
Identifying High-Risk Areas
FMEA assists in identifying high-risk areas within a design that might fail under specific conditions.
By highlighting these areas, design teams can focus their efforts on mitigating risks before the product reaches production.
Enhancing Communication and Collaboration
Incorporating FMEA in DR encourages communication between different departments.
Designers, engineers, and quality assurance professionals can collaborate more effectively to address potential issues and solve problems collaboratively.
Facilitating Decision-Making
With a well-documented FMEA, decision-makers have access to comprehensive data on potential failure modes and their impacts.
This information aids in making informed design changes and prioritizations based on quantified risk levels.
Embedding Risk Mitigation Strategies
During the DR phase, FMEA informs teams of the necessary risk mitigation strategies required to enhance product reliability.
Embedding these strategies into design specifications ensures that they are implemented throughout the development process.
Continuous Improvement Loop
Utilizing FMEA as a part of DR promotes a culture of continuous improvement.
Feedback from DR sessions can be utilized to update the FMEA and refine future risk assessments, leading to an iterative process of enhancement.
Conclusion
FMEA is a powerful tool for preventing failures and enhancing the quality of products and processes.
When integrated effectively with Design Review, it provides organizations with a structured approach to identifying and addressing potential risks.
By employing efficient prevention practices and utilizing FMEA for DR, businesses can ensure the reliability and success of their products.
Investing in proper training, tools, and cross-functional collaboration can significantly amplify the benefits of FMEA, paving the way for smoother operations and reduced costs in the long run.
資料ダウンロード
QCD管理受発注クラウド「newji」は、受発注部門で必要なQCD管理全てを備えた、現場特化型兼クラウド型の今世紀最高の受発注管理システムとなります。
ユーザー登録
受発注業務の効率化だけでなく、システムを導入することで、コスト削減や製品・資材のステータス可視化のほか、属人化していた受発注情報の共有化による内部不正防止や統制にも役立ちます。
NEWJI DX
製造業に特化したデジタルトランスフォーメーション(DX)の実現を目指す請負開発型のコンサルティングサービスです。AI、iPaaS、および先端の技術を駆使して、製造プロセスの効率化、業務効率化、チームワーク強化、コスト削減、品質向上を実現します。このサービスは、製造業の課題を深く理解し、それに対する最適なデジタルソリューションを提供することで、企業が持続的な成長とイノベーションを達成できるようサポートします。
製造業ニュース解説
製造業、主に購買・調達部門にお勤めの方々に向けた情報を配信しております。
新任の方やベテランの方、管理職を対象とした幅広いコンテンツをご用意しております。
お問い合わせ
コストダウンが利益に直結する術だと理解していても、なかなか前に進めることができない状況。そんな時は、newjiのコストダウン自動化機能で大きく利益貢献しよう!
(β版非公開)