- お役立ち記事
- Prototype parts made with precision cutting
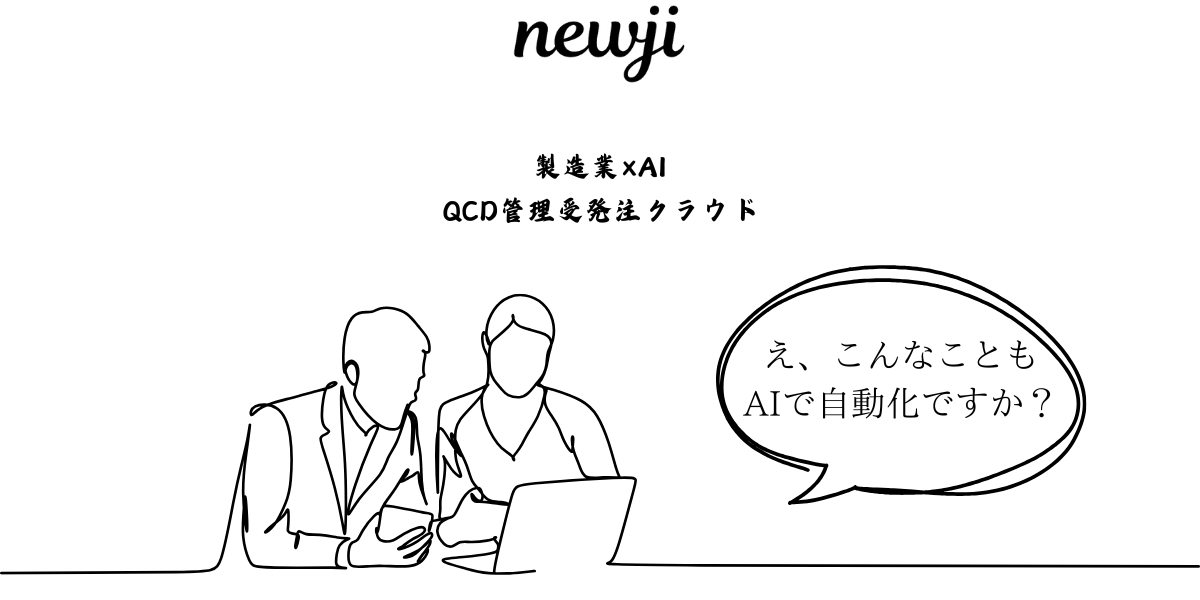
Prototype parts made with precision cutting
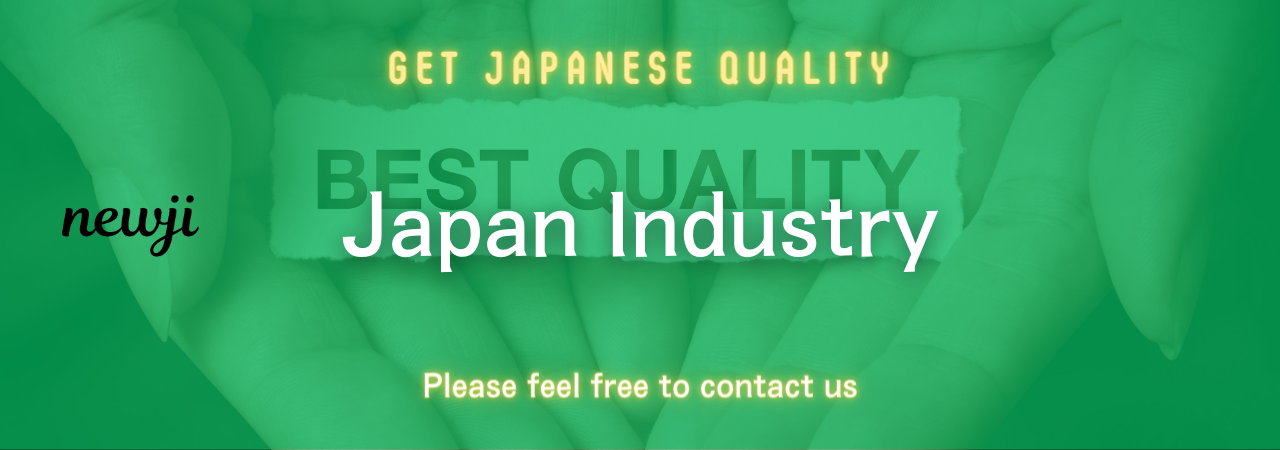
目次
Understanding Precision Cutting in Prototype Parts
Precision cutting is an essential process in the manufacturing of prototype parts.
It involves machining materials with a high degree of accuracy and complexity.
This process is utilized across various industries, including automotive, aerospace, electronics, and medical devices.
Understanding its significance and application can provide valuable insights into how products are developed and refined before they reach the market.
The Importance of Precision Cutting
When developing a prototype part, the accuracy of the initial model is crucial.
It must closely mirror the final product in order to identify and rectify any design flaws.
Precision cutting allows engineers to create parts to exact specifications, ensuring that each component fits seamlessly into the assembly.
This meticulous attention to detail helps prevent costly mistakes during mass production.
Precision cutting also plays a critical role in testing.
Prototypes are often subjected to rigorous conditions to assess their durability and performance.
If a part is not cut to precise measurements, it may not perform as expected during tests, leading to misleading results.
Precision ensures reliability, which is essential for making informed decisions about product designs.
Techniques Used in Precision Cutting
Several techniques are employed in precision cutting to achieve the desired results.
One of the most common methods is Computer Numerical Control (CNC) machining.
This cutting-edge technology uses computer-aided design (CAD) software to control the movement of machinery, resulting in highly accurate cuts.
CNC machines can handle complex geometries and produce intricate designs with minimal error.
Another popular technique is laser cutting.
This method uses a high-powered laser beam to cut through materials with exceptional precision.
Laser cutting is favored for its ability to handle detailed patterns and intricate cuts, making it ideal for small, delicate parts.
The focus of the laser allows for clean edges and a high-quality finish, reducing the need for additional processing.
Waterjet cutting is another option for precision cutting.
This technique involves using a high-pressure jet of water mixed with abrasive particles to cut materials.
Waterjet cutting is highly versatile, capable of slicing through a wide range of materials without producing heat, which can alter the properties of certain materials.
This makes it suitable for cutting sensitive materials, such as metals and composites, without compromising their structural integrity.
Applications of Precision Cutting in Prototyping
Precision cutting is used in a multitude of applications across different industries.
In the automotive sector, it is essential for creating components like engine parts, transmission systems, and interior features.
These parts must be precisely cut to ensure they work seamlessly with other components, contributing to the vehicle’s overall performance and safety.
The aerospace industry also heavily relies on precision cutting.
Aircraft structures, such as wings and fuselages, require finely detailed parts that can withstand extreme conditions and pressures.
Precision cutting ensures that each component is manufactured to exact tolerances, enhancing the aircraft’s performance and safety.
In electronics, precision cutting is crucial for developing small and intricate parts.
As technology becomes more advanced and compact, the demand for precision-cut components increases.
From circuit boards to connectors, precision in cutting ensures that the electrical parts fit together perfectly, ensuring reliable performance and reducing the risk of failure.
Precision cutting is also vital in the field of medical devices.
Medical instruments, implants, and prosthetics require meticulous craftsmanship and accuracy.
Precision cutting helps create components that meet the strict standards necessary for patient safety and effective performance.
This process allows for the creation of complex geometries and fine details required for life-saving medical equipment.
Advantages of Using Precision Cutting
Precision cutting offers numerous advantages over traditional manufacturing methods.
First, it provides unparalleled accuracy.
By using computer-controlled processes, manufacturers can achieve tolerances that are difficult to reach with manual techniques.
This accuracy helps reduce material waste and ensures consistent quality across all prototype parts.
Another advantage is flexibility.
Precision cutting can be applied to a wide variety of materials, including metals, plastics, and ceramics.
This versatility allows designers and engineers to experiment with different materials during the prototyping phase, leading to innovative solutions and improved product performance.
Precision cutting also speeds up the production process.
Automated techniques such as CNC machining and laser cutting enable rapid prototyping, reducing lead times and accelerating the development cycle.
This efficiency is crucial in industries where time-to-market is a competitive factor.
Finally, precision cutting enhances the overall quality of prototype parts.
With cleaner cuts and finer details, these parts often require less post-processing, such as polishing or sanding.
This not only saves time and resources but also contributes to a higher-quality final product.
Conclusion
Precision cutting is a fundamental process in the development of prototype parts.
Its importance spans various industries, ensuring that components are manufactured to high standards, reducing errors, and enhancing product performance.
By employing advanced techniques like CNC machining, laser cutting, and waterjet cutting, manufacturers can create intricate designs with accuracy and efficiency.
As technology continues to evolve, the role of precision cutting in prototyping will only become more critical, driving innovation and improving the quality of products across multiple sectors.
資料ダウンロード
QCD調達購買管理クラウド「newji」は、調達購買部門で必要なQCD管理全てを備えた、現場特化型兼クラウド型の今世紀最高の購買管理システムとなります。
ユーザー登録
調達購買業務の効率化だけでなく、システムを導入することで、コスト削減や製品・資材のステータス可視化のほか、属人化していた購買情報の共有化による内部不正防止や統制にも役立ちます。
NEWJI DX
製造業に特化したデジタルトランスフォーメーション(DX)の実現を目指す請負開発型のコンサルティングサービスです。AI、iPaaS、および先端の技術を駆使して、製造プロセスの効率化、業務効率化、チームワーク強化、コスト削減、品質向上を実現します。このサービスは、製造業の課題を深く理解し、それに対する最適なデジタルソリューションを提供することで、企業が持続的な成長とイノベーションを達成できるようサポートします。
オンライン講座
製造業、主に購買・調達部門にお勤めの方々に向けた情報を配信しております。
新任の方やベテランの方、管理職を対象とした幅広いコンテンツをご用意しております。
お問い合わせ
コストダウンが利益に直結する術だと理解していても、なかなか前に進めることができない状況。そんな時は、newjiのコストダウン自動化機能で大きく利益貢献しよう!
(Β版非公開)