- お役立ち記事
- Points to consider when choosing an SIer equipment manufacturer that can design and manufacture
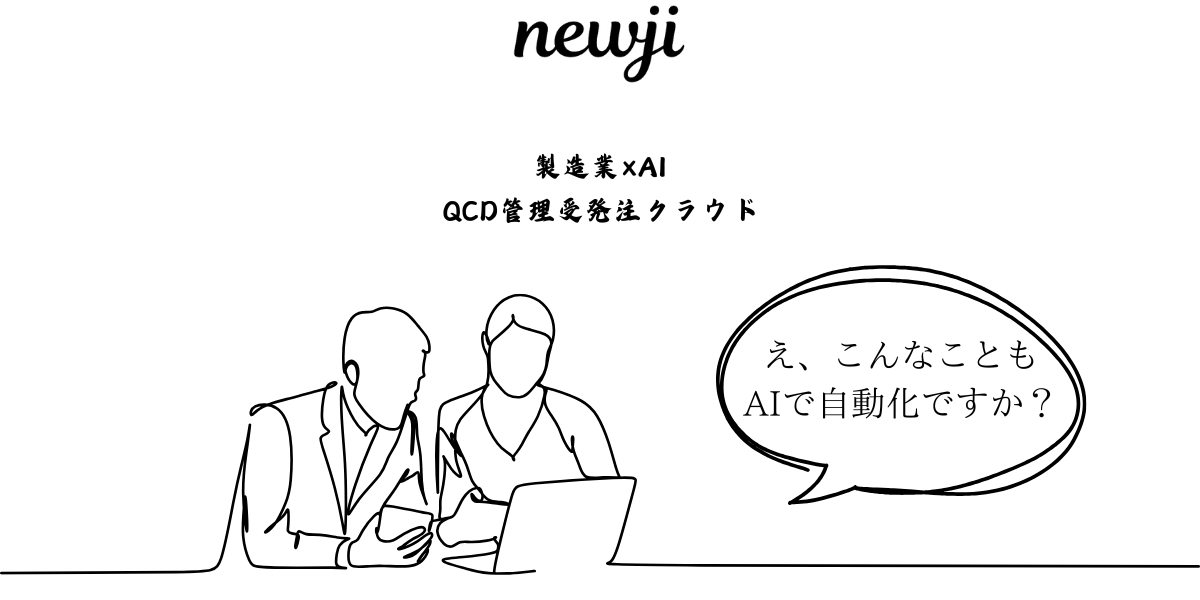
Points to consider when choosing an SIer equipment manufacturer that can design and manufacture
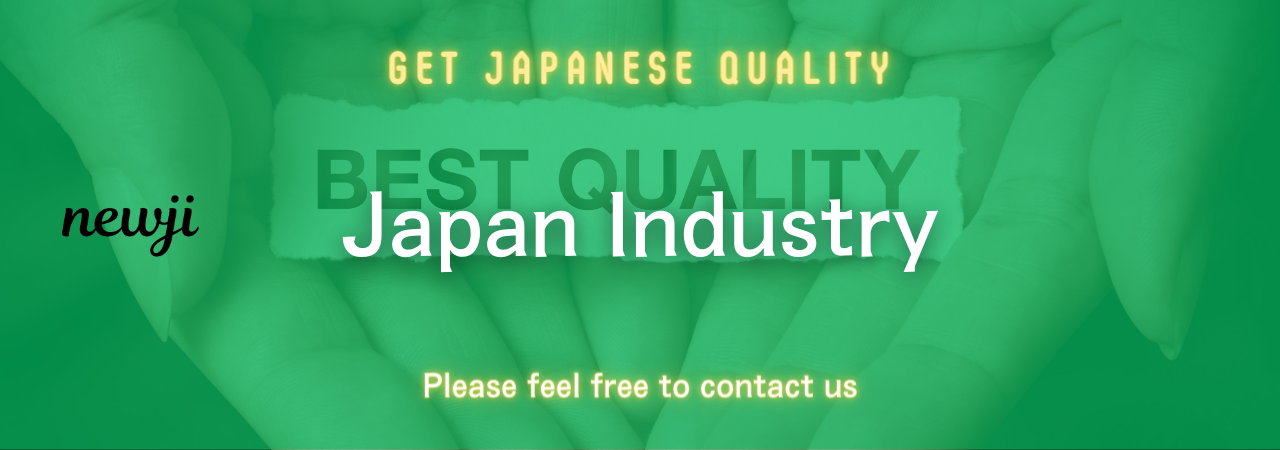
目次
Understanding the Role of an SIer Equipment Manufacturer
Choosing the right SIer (System Integrator) equipment manufacturer can profoundly impact the success of a project involving the design and manufacturing of specialized equipment.
An SIer plays a crucial role in integrating various systems and technologies to create efficient and effective workflows.
Their expertise ensures that different components work seamlessly together, ultimately boosting productivity and efficiency.
When selecting an SIer equipment manufacturer, several points must be considered to ensure they can meet your specific needs and enhance your operations effectively.
Identifying Your Needs and Requirements
Before diving into the search for an SIer equipment manufacturer, it’s essential to clearly identify your project needs and requirements.
Understanding what you need will help streamline your decision-making process.
Start by analyzing the nature of the equipment you intend to have designed and manufactured.
Consider the technical specifications, the scale of manufacturing, and the intended use of the equipment.
Having a clear picture of your requirements will guide you in evaluating potential manufacturers who have the capacity and expertise to meet these needs.
Assessing Technical Proficiency
Technical proficiency is a critical factor in choosing an SIer equipment manufacturer.
You’ll want a partner who understands the intricacies of designing and manufacturing technical equipment.
Investigate their portfolio to see past projects and assess whether they have successfully executed projects similar to yours.
Look for their ability to incorporate the latest technologies and innovations, as this will ensure your equipment remains up-to-date and competitive.
Evaluating Experience and Reputation
Experience often correlates with reliability.
An SIer equipment manufacturer with a long history in the industry is likely to have honed their processes and developed a keen understanding of industry standards and regulations.
Beyond the number of years in business, investigate the reputation of the manufacturer.
Check reviews and testimonials from previous clients.
A manufacturer with consistently high ratings is usually a safer choice as they have a proven track record of delivering quality products and great customer service.
Ensuring Quality Control and Compliance
Quality control is crucial when designing and manufacturing complex equipment.
Ask potential manufacturers about their quality assurance processes and the standards they adhere to.
They should be able to provide detailed information on how they ensure each piece of equipment meets predefined standards.
Additionally, ensure they comply with all relevant industry regulations and certifications.
Compliance is not only about legality but also guarantees that the equipment manufactured is safe and effective for use.
Exploring Customization Capabilities
Every project is unique, and therefore, customization is often necessary.
Consider whether the SIer equipment manufacturer offers the flexibility to customize and modify designs according to your specific needs.
The ability to tailor equipment ensures it closely aligns with your operational requirements, contributing to enhanced efficiency.
Discuss the extent to which they can modify existing designs or create new ones to meet unique specifications.
Considering Cost and Budget
While cost should not be the sole determining factor, it is undeniably important.
Come up with a realistic budget for your project before approaching manufacturers.
Once you have shortlisted potential partners, request detailed quotes and compare them against your budget.
Beware of quotes that are significantly lower than the average, as they may indicate compromises on quality or service.
The ideal manufacturer offers a reasonable price while not undermining quality.
Assessing Project Management and Support
Effective project management is crucial for the timely and successful completion of any project.
Evaluate the manufacturer’s ability to manage complex projects efficiently.
Look for their approach to project management, timelines, and communication methods.
Equally important is their after-sales support and maintenance services.
Your relationship with the manufacturer shouldn’t end at delivery.
Ensure they offer robust post-installation support to assist with any issues that may arise.
Cultural Fit and Communication
Working with an SIer equipment manufacturer often means a long-term partnership.
Thus, it’s important that they align with your organizational culture and values.
Consider the ease of communication and the level of transparency they provide.
A manufacturer that is open, communicative, and genuinely interested in understanding your objectives is more likely to be a beneficial partner.
Merging Technological Insights and Human Expertise
Incorporating both technological insights and human expertise is key to harnessing the full potential of equipment design and manufacturing.
Choose an SIer equipment manufacturer that demonstrates innovation and a clear understanding of technology trends, ensuring your equipment is forward-thinking.
Simultaneously, they should value customer relationships and tailor their expertise to deliver on client expectations.
This combined approach is more likely to yield equipment that surpasses functional performance and delivers strategic value.
Conclusion
In conclusion, selecting an SIer equipment manufacturer involves a multifaceted evaluation of their capabilities, experience, and approach to your specific requirements.
By focusing on technical proficiency, reputation, customization abilities, and project management, you can establish a successful partnership.
This careful selection is instrumental in achieving efficient design and production processes that effectively support your goals.
As you explore potential manufacturers, prioritize those who are not only technologically adept but also capable of robust client support and relationship management.
Doing so will ensure that your investment in equipment design and manufacturing yields substantial, long-term benefits for your organization.
資料ダウンロード
QCD調達購買管理クラウド「newji」は、調達購買部門で必要なQCD管理全てを備えた、現場特化型兼クラウド型の今世紀最高の購買管理システムとなります。
ユーザー登録
調達購買業務の効率化だけでなく、システムを導入することで、コスト削減や製品・資材のステータス可視化のほか、属人化していた購買情報の共有化による内部不正防止や統制にも役立ちます。
NEWJI DX
製造業に特化したデジタルトランスフォーメーション(DX)の実現を目指す請負開発型のコンサルティングサービスです。AI、iPaaS、および先端の技術を駆使して、製造プロセスの効率化、業務効率化、チームワーク強化、コスト削減、品質向上を実現します。このサービスは、製造業の課題を深く理解し、それに対する最適なデジタルソリューションを提供することで、企業が持続的な成長とイノベーションを達成できるようサポートします。
オンライン講座
製造業、主に購買・調達部門にお勤めの方々に向けた情報を配信しております。
新任の方やベテランの方、管理職を対象とした幅広いコンテンツをご用意しております。
お問い合わせ
コストダウンが利益に直結する術だと理解していても、なかなか前に進めることができない状況。そんな時は、newjiのコストダウン自動化機能で大きく利益貢献しよう!
(Β版非公開)