- お役立ち記事
- Key points for cost reduction in the prototyping process
月間77,185名の
製造業ご担当者様が閲覧しています*
*2025年2月28日現在のGoogle Analyticsのデータより
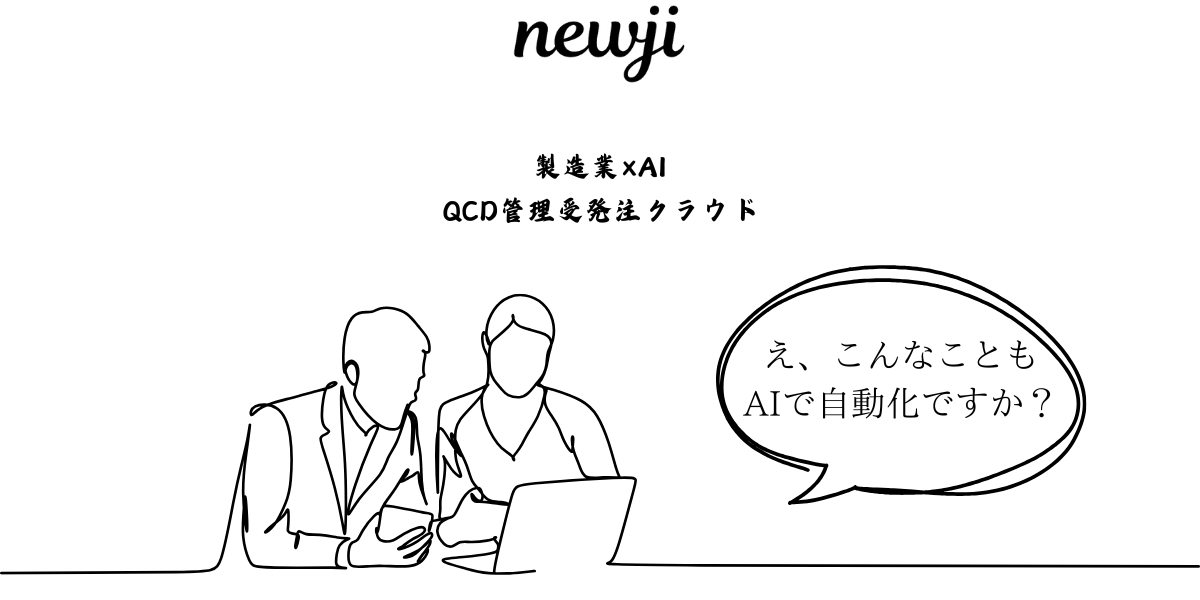
Key points for cost reduction in the prototyping process
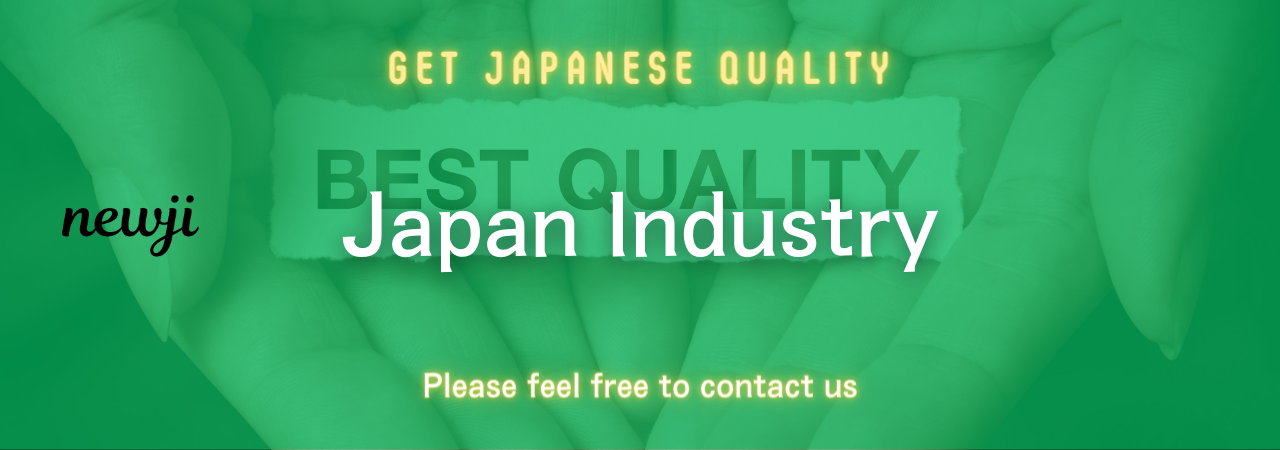
目次
Understanding the Importance of Prototyping
Prototyping is a crucial step in product development that allows companies to test, evaluate, and refine their ideas before they proceed to full-scale production.
It helps in identifying potential issues and making improvements early in the process.
However, the prototyping process can be costly.
Therefore, understanding how to reduce costs without compromising quality is essential for businesses aiming to remain competitive.
Planning and Budgeting Wisely
One of the most effective ways to reduce costs in the prototyping process is by planning and budgeting wisely.
Begin by clearly defining the scope of your project and what you aim to achieve with your prototype.
This will help in allocating resources effectively and avoiding unnecessary expenditures.
Set a realistic budget and timeline, considering all possible costs, such as materials, labor, and testing.
Using Cost-Effective Materials
Selecting the right materials can significantly influence the cost of prototyping.
Opt for materials that balance price and quality to ensure that the prototype functions correctly without overspending.
It might also be beneficial to use alternative materials that are less expensive but still meet the required standards for testing and evaluation.
Leveraging Technology and Tools
Incorporating modern technology and tools into the prototyping process can lead to substantial cost reductions.
Utilizing computer-aided design (CAD) software can help in creating detailed and accurate designs before the physical prototype is made, minimizing the risk of costly errors.
Additionally, 3D printing is a powerful tool in prototyping, allowing for rapid and inexpensive production of parts and components.
Emphasizing Virtual Prototyping
Virtual prototyping is another technological advance that can help reduce costs.
By creating digital models, companies can simulate and analyze the performance of their designs in various environments without having to construct physical models for every test.
This not only saves money but also accelerates the development process.
Outsourcing and Partnering
Outsourcing certain aspects of the prototyping process can be a cost-effective strategy.
Collaborating with specialized firms or partners who have the necessary expertise and equipment can lead to better quality and reduced costs.
However, it is important to ensure that the selected partners are reliable and provide value for the investment.
Pooling Resources and Sharing Costs
Pooling resources with other companies or sharing costs with partners in joint development projects can offer significant savings.
This collaborative approach allows businesses to access technologies and expertise that might otherwise be too costly on their own.
Iterative Testing and Feedback
Cost reduction can also be achieved through iterative testing and receiving feedback from stakeholders at every stage of the prototyping process.
Instead of producing multiple complete prototypes, create minimal viable products (MVPs) and test them iteratively.
This approach allows you to make adjustments early, preventing expensive redesigns later.
Engaging with End-Users
Incorporating feedback from end-users during the prototyping phase is invaluable in refining the product and ensuring it meets customer needs.
This engagement can prevent costly mistakes and oversights, ultimately resulting in a more successful product and reduced prototyping costs.
Minimizing Waste
Efficient use of materials and resources is key to reducing costs in prototyping.
Implement practices that minimize waste, such as reusing materials where possible and recycling any leftover materials.
This not only helps in reducing expenses but also promotes sustainable environmental practices.
Optimizing Design for Manufacturing
Design for manufacturability (DFM) is a strategy that involves designing with the manufacturing process in mind.
By considering how your prototype will ultimately be manufactured at scale, you can make design decisions that simplify the process and reduce costs.
This includes choosing standard components and minimizing complex geometries.
Continuous Process Improvement
Adopting a mindset of continuous improvement can drive down costs in the long run.
Regularly evaluate the prototyping process and look for opportunities to increase efficiency and reduce unnecessary steps.
Investing in training for your team can also help, as skilled professionals are more likely to identify and implement cost-saving measures.
Learning from Past Prototypes
Use insights and lessons learned from previous prototyping projects to improve future processes.
Analyze what worked well and what didn’t, and apply this knowledge to prevent similar issues and optimize costs in upcoming projects.
By focusing on these key points, businesses can successfully reduce costs in the prototyping process while maintaining the quality and effectiveness of their products.
Implementing these strategies not only leads to cost savings but also supports innovation and competitiveness in the marketplace.
資料ダウンロード
QCD管理受発注クラウド「newji」は、受発注部門で必要なQCD管理全てを備えた、現場特化型兼クラウド型の今世紀最高の受発注管理システムとなります。
ユーザー登録
受発注業務の効率化だけでなく、システムを導入することで、コスト削減や製品・資材のステータス可視化のほか、属人化していた受発注情報の共有化による内部不正防止や統制にも役立ちます。
NEWJI DX
製造業に特化したデジタルトランスフォーメーション(DX)の実現を目指す請負開発型のコンサルティングサービスです。AI、iPaaS、および先端の技術を駆使して、製造プロセスの効率化、業務効率化、チームワーク強化、コスト削減、品質向上を実現します。このサービスは、製造業の課題を深く理解し、それに対する最適なデジタルソリューションを提供することで、企業が持続的な成長とイノベーションを達成できるようサポートします。
製造業ニュース解説
製造業、主に購買・調達部門にお勤めの方々に向けた情報を配信しております。
新任の方やベテランの方、管理職を対象とした幅広いコンテンツをご用意しております。
お問い合わせ
コストダウンが利益に直結する術だと理解していても、なかなか前に進めることができない状況。そんな時は、newjiのコストダウン自動化機能で大きく利益貢献しよう!
(β版非公開)