- お役立ち記事
- Initiatives to improve the level of adjustment work for battery-related ASSY equipment
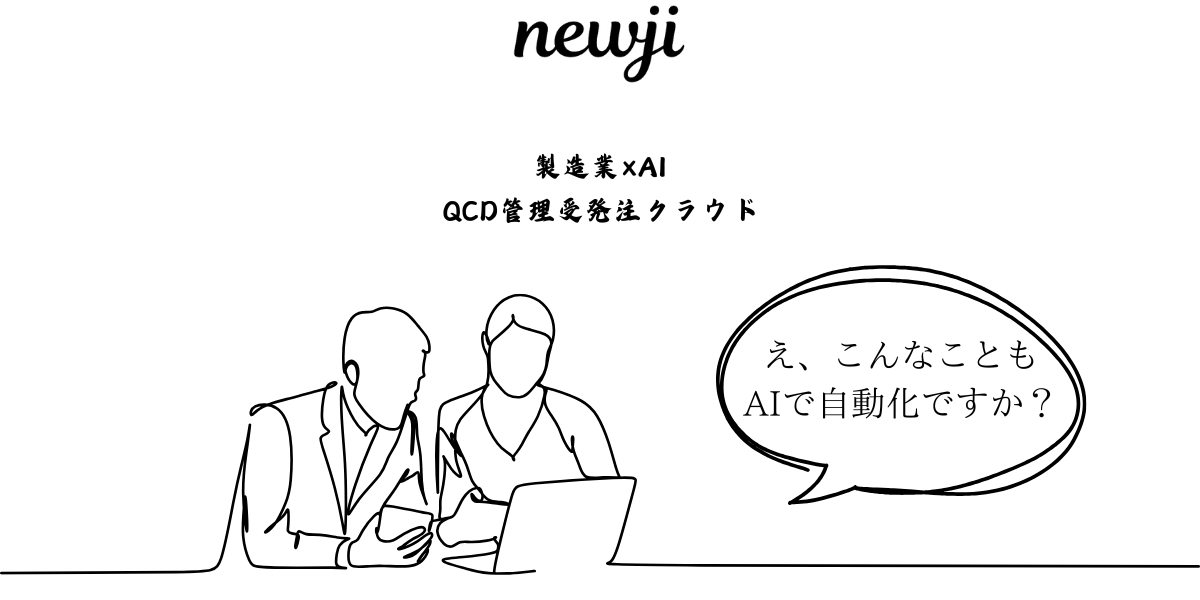
Initiatives to improve the level of adjustment work for battery-related ASSY equipment
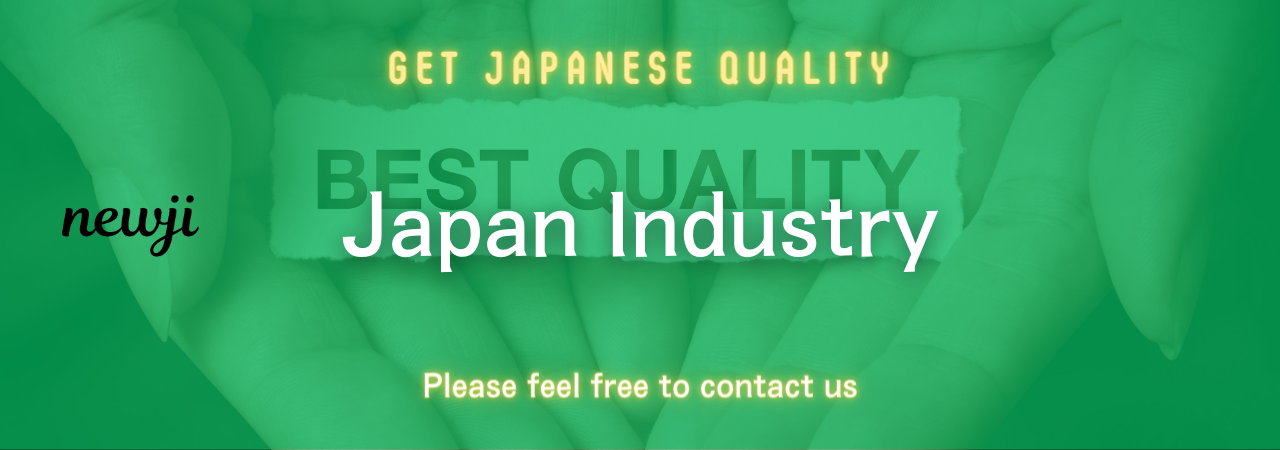
目次
Understanding ASSY Equipment in Battery Manufacturing
Battery-related ASSY equipment is critical in the manufacturing process of batteries.
These systems are responsible for assembling various components, ensuring the final product meets the performance and safety standards required for modern applications.
Given the complexity of batteries, from their chemical makeup to the precision needed in their assembly, adjusting and maintaining ASSY equipment is vital.
Manufacturers understand that the quality of the battery is as good as the weakest link in its manufacturing process.
Thus, improving the level of adjustment work for ASSY equipment directly translates to better-performing batteries.
As the demand for batteries increases, particularly with the rise of electric vehicles and renewable energy storage systems, manufacturers are focusing intensely on optimizing their ASSY processes.
The Importance of Precision in Battery Assembly
In battery manufacturing, each component must be precisely assembled to ensure safety and efficiency.
Errors in assembly, even slight ones, can lead to suboptimal performance or, in worst-case scenarios, hazardous failures.
The ASSY equipment must be fine-tuned to handle these components, accommodating different battery types and sizes without compromising quality.
Precision in assembly affects the internal structure of the battery, influencing its overall efficiency.
For instance, misalignment of electrodes can decrease charge retention and reduce the battery’s lifespan.
Hence, constant improvement in adjustment works of ASSY equipment is not just an operational necessity but a quality mandate.
Challenges in Adjusting ASSY Equipment
Manufacturers face several challenges in adjusting equipment for optimum battery assembly.
First, the technological complexities involved require a deep understanding of both mechanical and electronic systems.
Battery-related ASSY equipment involves intricate processes, such as layering, tab welding, and final casing, each needing precise alignment.
Another challenge is the variation in battery designs.
With ongoing innovations, battery designs are frequently updated.
This necessitates frequent recalibration and adjustments to the ASSY machines to accommodate new specifications.
Additionally, the lack of skilled technicians trained in the nuances of ASSY equipment operation can slow adjustment work.
Consistent training and upskilling are required to ensure that personnel are capable of effectively managing the adjustments needed for optimal battery assembly.
Innovations in ASSY Equipment Adjustment
To mitigate these challenges, manufacturers are exploring a range of innovations aimed at improving adjustment work for ASSY equipment.
Automation technology is at the forefront of this transformation.
By integrating advanced robotics and AI, companies can enhance precision, reduce human error, and ensure consistent high-quality assembly.
Moreover, real-time monitoring systems are being increasingly utilized.
These systems provide instant feedback on the assembly process, helping technicians make necessary adjustments swiftly.
The integration of IoT devices allows for predictive maintenance, identifying potential issues before they affect the system’s performance.
Software advancements also play a crucial role.
Specialized software can simulate various assembly scenarios, allowing technicians to anticipate and prepare for potential issues during assembly.
This not only speeds up the adjustment process but also improves the overall efficiency of the equipment.
Strategies for Effective Adjustments
Developing effective strategies for adjustment begins with assessing the current capabilities of ASSY equipment.
Regular audits can identify components of the system that require regular updates or calibration.
With data-driven insights, manufacturers can prioritize areas that need attention and allocate resources effectively.
Training programs are essential for personnel involved in equipment operations.
Investing in continuous education and hands-on workshops ensures that technicians remain knowledgeable about the latest technological advancements.
This readiness enables them to handle adjustments swiftly and accurately.
Moreover, collaboration with equipment suppliers can be beneficial.
Since suppliers possess in-depth knowledge of their products, they can offer valuable insights into optimizing settings and improving equipment performance.
Collaborative Approaches Towards Optimization
The road to improved ASSY equipment adjustments requires a collaborative approach.
Engaging with industry experts, researchers, and other manufacturers can unlock new possibilities for innovation.
Industry partnerships can lead to the development of standardized practices and technologies that benefit all players in the field.
Additionally, feedback mechanisms from end-users can inform manufacturers about the real-world performance of their products.
This can guide further adjustments and innovations in both the equipment and the batteries being assembled.
The Future of Battery Manufacturing
As technology continues to advance, the outlook for battery manufacturing becomes increasingly promising.
ASSY equipment will likely evolve to handle more sophisticated tasks, backed by advancements in AI and machine learning.
These technologies will assist in predictive analytics, further optimizing assembly lines.
Environmental concerns are also shaping the future of battery manufacturing.
Manufacturers are starting to incorporate sustainable practices in assembly processes.
Adjustments and enhancements in ASSY equipment will likely focus on reducing waste and improving energy efficiency.
This progress is not only necessary but inevitable given the rapid growth of industries reliant on battery technology.
From consumer electronics to automotive innovations, efficient and reliable battery production is foundational.
By continuing to improve the adjustment work for battery-related ASSY equipment, manufacturers are setting a solid groundwork for a future powered by reliable and sustainable energy sources.
資料ダウンロード
QCD調達購買管理クラウド「newji」は、調達購買部門で必要なQCD管理全てを備えた、現場特化型兼クラウド型の今世紀最高の購買管理システムとなります。
ユーザー登録
調達購買業務の効率化だけでなく、システムを導入することで、コスト削減や製品・資材のステータス可視化のほか、属人化していた購買情報の共有化による内部不正防止や統制にも役立ちます。
NEWJI DX
製造業に特化したデジタルトランスフォーメーション(DX)の実現を目指す請負開発型のコンサルティングサービスです。AI、iPaaS、および先端の技術を駆使して、製造プロセスの効率化、業務効率化、チームワーク強化、コスト削減、品質向上を実現します。このサービスは、製造業の課題を深く理解し、それに対する最適なデジタルソリューションを提供することで、企業が持続的な成長とイノベーションを達成できるようサポートします。
オンライン講座
製造業、主に購買・調達部門にお勤めの方々に向けた情報を配信しております。
新任の方やベテランの方、管理職を対象とした幅広いコンテンツをご用意しております。
お問い合わせ
コストダウンが利益に直結する術だと理解していても、なかなか前に進めることができない状況。そんな時は、newjiのコストダウン自動化機能で大きく利益貢献しよう!
(Β版非公開)