- お役立ち記事
- Key points for successful high-precision metal die-casting prototype production in Hirakawa City
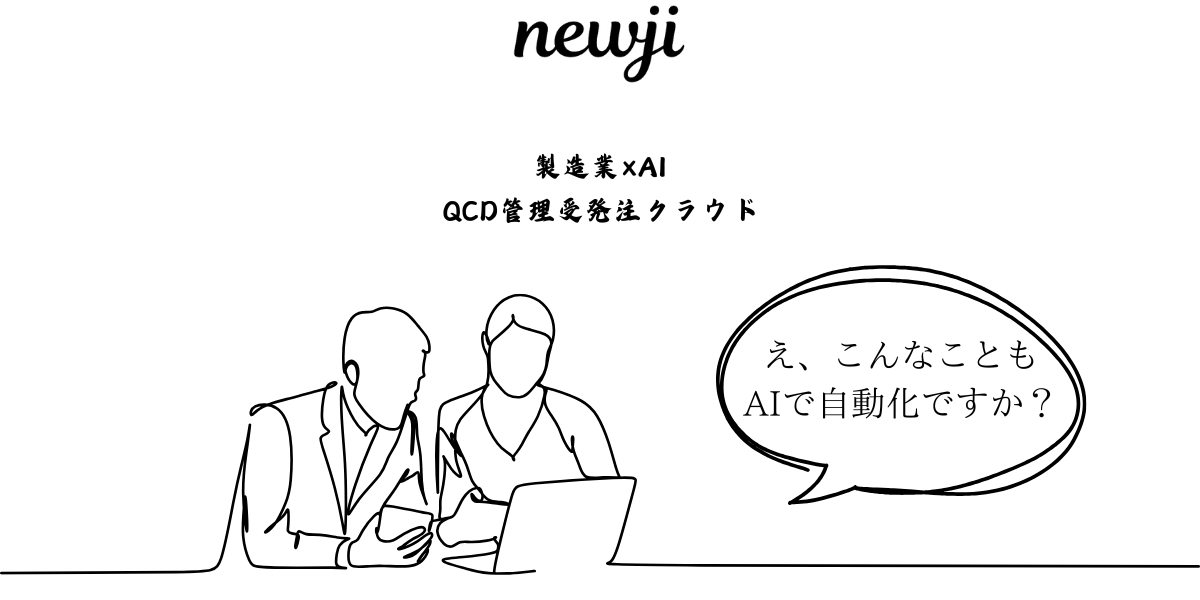
Key points for successful high-precision metal die-casting prototype production in Hirakawa City
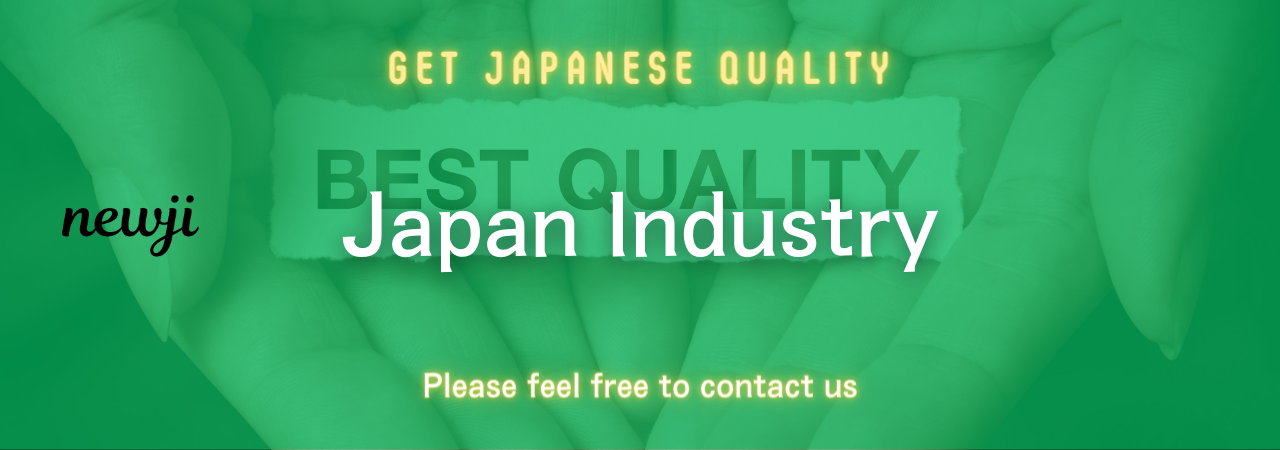
目次
Understanding High-Precision Metal Die-Casting
High-precision metal die-casting is a manufacturing process where molten metal is poured into molds to create intricately shaped components.
It’s widely used in various industries, including automotive, aerospace, and electronics, due to its ability to produce components with exceptional accuracy and surface finish.
In Hirakawa City, known for its excellence in manufacturing, metal die-casting plays a crucial role in producing prototypes that meet stringent industry standards.
Achieving success in this field depends on several key factors that manufacturers must pay special attention to during production.
The Importance of Material Selection
One of the first steps in the die-casting process is selecting the appropriate material.
In Hirakawa City, manufacturers often choose between aluminum, magnesium, and zinc alloys, based on the specific needs of the prototype.
Aluminum is popular for its lightweight properties and good corrosion resistance.
Magnesium stands out for its lower density, making it ideal for applications where weight reduction is a priority.
Zinc offers excellent electrical conductivity and is often used in electronic applications.
Choosing the wrong material can lead to issues in the final product, such as flaws, dimensional instability, or high production costs.
Therefore, careful assessment of material properties and client requirements is vital for a successful prototype.
Precision in Mold Design
Mold design is another critical factor in high-precision die-casting.
The design determines the prototype’s shape and dimensions, so it must be meticulously crafted to ensure accuracy.
In Hirakawa City, advanced CAD/CAM software and simulation tools are often employed to design and optimize molds.
These state-of-the-art technologies allow engineers to predict and avoid potential issues, such as material flow imbalances or thermal deformations, that might occur during production.
Moreover, incorporating draft angles, fillets, and ribs in the design is crucial.
These features facilitate the ejection of the cast part and improve its structural integrity.
Finely detailed molds lead to equally precise prototypes, making adherence to exact specifications indispensable.
The Role of Quality Control
Quality control is paramount in high-precision metal die-casting to ensure that prototypes meet established standards and client expectations.
In Hirakawa City, rigorous inspections and testing protocols are put in place throughout the production process.
Technicians conduct dimensional checks, using tools such as calipers and coordinate measuring machines (CMMs), to verify that each part conforms to the required specifications.
Non-destructive testing methods, like X-ray and ultrasonic testing, help detect hidden defects within the cast components without altering them.
These quality checks are vital for identifying any flaws early, allowing for corrective actions before mass production starts.
Optimizing the Production Process
For successful metal die-casting prototype production, optimizing the entire manufacturing process is essential.
Factors like machine setup, cycle time, and temperature control significantly impact the quality of the final product.
In Hirakawa City, manufacturers often employ advanced technologies, like computer-aided manufacturing (CAM) systems, to automate and streamline production.
This automation not only enhances efficiency but also minimizes human errors, further ensuring consistency and precision.
Moreover, maintaining strict control over variables such as injection speed, pressure, and temperature is crucial.
Deviations in these parameters can result in defects like porosity, shrinkage, or incomplete fills.
Therefore, constant monitoring and adjustments during production help in achieving high-quality prototypes and in minimizing waste.
Collaborative Design and Communication
Successful prototype production in Hirakawa City relies heavily on effective collaboration and communication throughout the entire process.
From initial design to the final cast, seamless cooperation between designers, engineers, and clients is vital.
Clear communication helps in aligning the design expectations with the manufacturing process.
It ensures that any potential issues are identified and addressed early, which can save time and resources.
Using collaborative tools and platforms, such as shared digital workspaces, allows all stakeholders to access, modify, and review designs and plans in real time.
This integrated approach not only helps in creating prototypes that meet client requirements but also strengthens relationships with clients.
Environmental and Sustainability Considerations
In modern manufacturing, including in Hirakawa City, environmental sustainability is becoming an increasingly significant aspect.
Manufacturers strive to reduce waste and energy consumption, aiming for eco-friendly production processes.
By using recycled materials and improving energy efficiency, companies contribute to environmental sustainability while also enhancing cost-effectiveness.
Furthermore, investing in innovative technologies, such as 3D printing and simulation software, helps minimize material waste by optimizing the design before production starts.
These practices not only benefit the environment but also build a positive reputation for the company, appealing to eco-conscious clients.
Conclusion
In summary, successful high-precision metal die-casting prototype production in Hirakawa City depends on several critical factors.
Careful material selection, precision in mold design, rigorous quality control, optimization of production processes, effective collaboration, and sustainability are all key elements.
By paying close attention to these aspects, manufacturers can produce high-quality prototypes that meet industry standards and client expectations.
In doing so, Hirakawa City’s reputation as a leader in manufacturing excellence continues to grow, paving the way for innovation and technological advancement in the field of metal die-casting.
資料ダウンロード
QCD調達購買管理クラウド「newji」は、調達購買部門で必要なQCD管理全てを備えた、現場特化型兼クラウド型の今世紀最高の購買管理システムとなります。
ユーザー登録
調達購買業務の効率化だけでなく、システムを導入することで、コスト削減や製品・資材のステータス可視化のほか、属人化していた購買情報の共有化による内部不正防止や統制にも役立ちます。
NEWJI DX
製造業に特化したデジタルトランスフォーメーション(DX)の実現を目指す請負開発型のコンサルティングサービスです。AI、iPaaS、および先端の技術を駆使して、製造プロセスの効率化、業務効率化、チームワーク強化、コスト削減、品質向上を実現します。このサービスは、製造業の課題を深く理解し、それに対する最適なデジタルソリューションを提供することで、企業が持続的な成長とイノベーションを達成できるようサポートします。
オンライン講座
製造業、主に購買・調達部門にお勤めの方々に向けた情報を配信しております。
新任の方やベテランの方、管理職を対象とした幅広いコンテンツをご用意しております。
お問い合わせ
コストダウンが利益に直結する術だと理解していても、なかなか前に進めることができない状況。そんな時は、newjiのコストダウン自動化機能で大きく利益貢献しよう!
(Β版非公開)