- お役立ち記事
- Hydrodynamic simulation of prototype parts and efficient design methods
月間77,185名の
製造業ご担当者様が閲覧しています*
*2025年2月28日現在のGoogle Analyticsのデータより
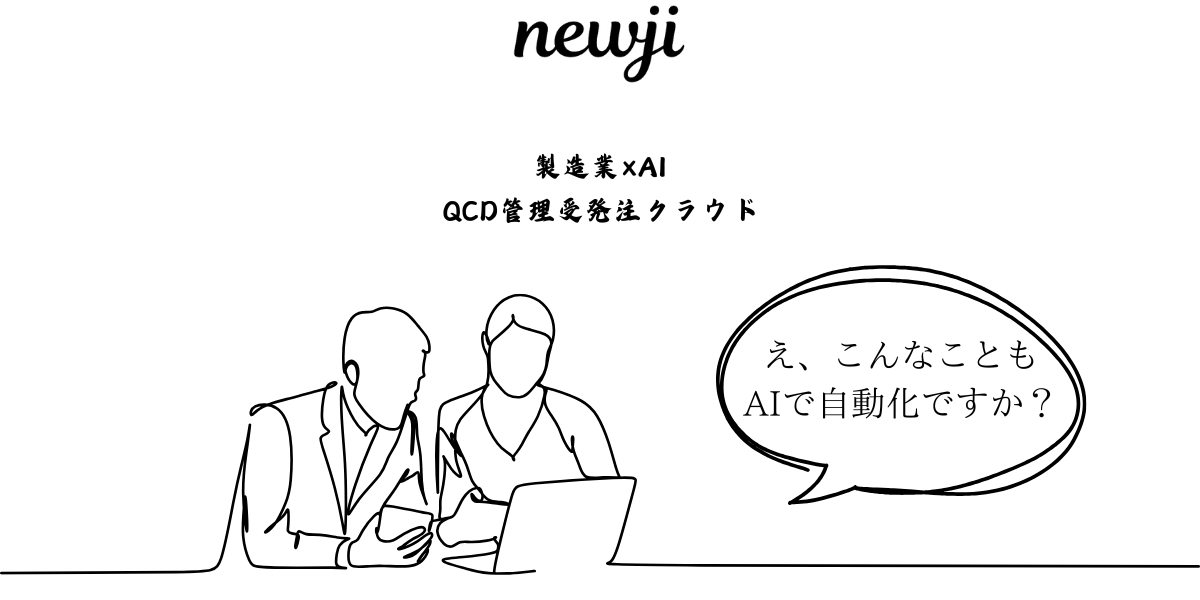
Hydrodynamic simulation of prototype parts and efficient design methods
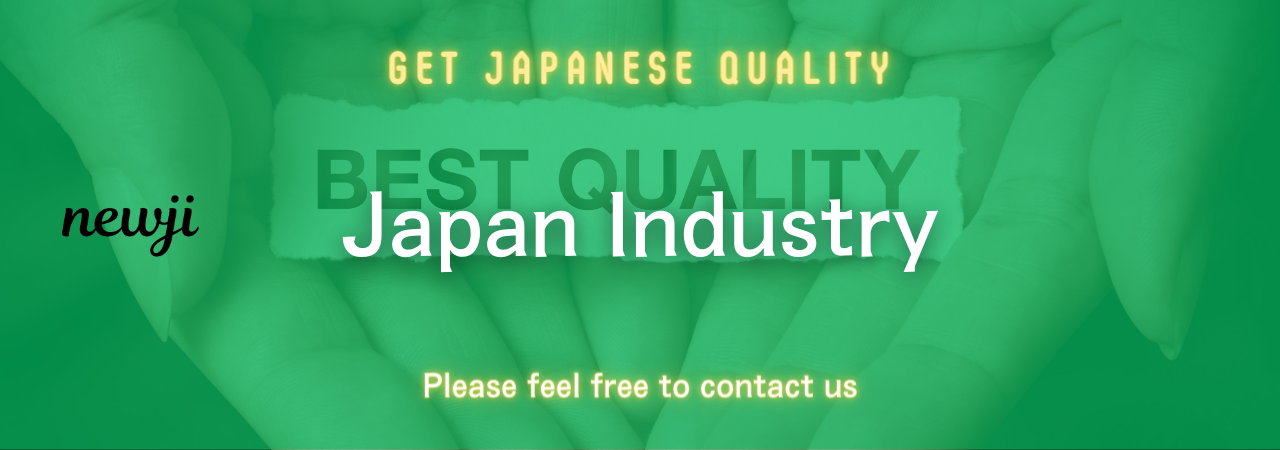
目次
Introduction to Hydrodynamic Simulations
Hydrodynamic simulations are crucial tools in modern engineering, providing insights into how fluids interact with different structures and components.
These simulations help engineers design and test parts before physical prototypes are created, saving time and resources.
Understanding the flow and behavior of fluids—including air and water—around various parts enables engineers to anticipate performance, identify potential issues, and improve design efficiency.
The Role of Hydrodynamic Simulations in Engineering
In the field of engineering, fluid dynamics plays a vital role in the design and optimization of products.
Whether it is the aerodynamic shape of a car, the hull design of a ship, or the piping in industrial processes, understanding fluid behavior is essential.
Hydrodynamic simulations use computational methods to model and predict how fluids interact with surfaces and materials.
By simulating these interactions, engineers can observe phenomena such as turbulence, drag, and lift, allowing for precise adjustments to enhance performance.
How Hydrodynamic Simulations Work
Hydrodynamic simulations are primarily based on numerical calculation methods such as computational fluid dynamics (CFD).
CFD uses algorithms to solve fluid flow equations, generating virtual models that predict how fluids behave in real-world scenarios.
These simulations require sophisticated software that incorporates physics, mathematics, and computer science principles.
Typically, a simulation begins with defining the parameters of the fluid flow problem, including the geometry of the part, the properties of the fluid, and the boundary conditions.
The software then discretizes the equations governing fluid motion and solves them iteratively to predict fluid behavior over time.
Steps in Conducting a Hydrodynamic Simulation
Conducting a hydrodynamic simulation involves several critical steps:
1. **Geometry Creation:** Engineers create a digital model of the prototype part, which serves as the simulation’s foundation.
2. **Mesh Generation:** The digital model is divided into smaller elements, known as a mesh, to ensure that the fluid flow can be accurately calculated across the entire surface.
3. **Setting Boundary Conditions:** Engineers specify the initial and boundary conditions, such as fluid velocity, pressure, and temperature, to guide the simulation.
4. **Solving:** The simulation software computes the interaction between the fluid and the prototype by solving the governing equations.
5. **Post-Processing and Analysis:** Engineers analyze the results to interpret fluid behavior, visualize flow patterns, and assess the part’s performance.
Advantages of Using Hydrodynamic Simulations
Hydrodynamic simulations offer numerous benefits over traditional testing methods, making them indispensable to modern design processes.
– **Cost-Efficiency:** By simulating and optimizing designs virtually, development costs associated with prototyping and testing are significantly reduced.
– **Time Savings:** Engineers can evaluate and refine different design iterations rapidly, speeding up the development cycle.
– **Enhanced Performance:** Simulations allow for more comprehensive exploration of design options, leading to superior performance and efficiency of the final product.
– **Risk Reduction:** Potential design flaws and performance issues can be identified early, minimizing the risk of failure in the final product.
Applications in Various Industries
Hydrodynamic simulations are used across a wide array of industries:
– **Automotive:** Designing aerodynamic bodies to reduce drag, enhance fuel efficiency, and improve stability at high speeds.
– **Aerospace:** Optimizing wing and fuselage shapes for better lift, control, and fuel efficiency.
– **Marine:** Designing efficient hulls for ships to reduce resistance and increase speed.
– **Oil and Gas:** Ensuring efficient design of pipelines and equipment to handle complex fluid flows under varying conditions.
– **Manufacturing:** Optimizing fluid flow in HVAC systems, chemical processes, and cooling systems in electronics.
Efficient Design Methods Using Simulations
Hydrodynamic simulations play a pivotal role in developing efficient design methods, guiding engineers toward sustainable and innovative solutions.
– **Iterative Design Process:** By integrating simulations into the design process, engineers can adopt an iterative approach, refining prototypes quickly and efficiently.
– **Multi-Disciplinary Optimization:** Simulations allow for the consideration of multiple factors simultaneously, such as fluid dynamics, structural integrity, and thermodynamics, leading to holistic design solutions.
– **Customizable Simulations:** Engineers can tailor simulations to specific applications, reusing models and settings to streamline future projects, enhancing design efficiency.
– **Predictive Analytics:** Simulations provide a predictive capability, enabling informed decision-making and strategic planning in the early stages of design.
Challenges and Future Directions
Despite their advantages, hydrodynamic simulations face certain challenges:
– **Computational Demands:** Simulations require significant computing power and resources, particularly for complex or large-scale systems.
– **Accuracy of Models:** The precision of a simulation depends on the quality of the input data, including mesh quality and choice of computational models.
– **User Expertise:** Efficient use of simulation tools requires skilled professionals who understand both the technical and theoretical aspects of fluid dynamics.
The future of hydrodynamic simulations looks promising, with advancements in AI, machine learning, and high-performance computing poised to further enhance their accuracy and applicability.
Conclusion
Hydrodynamic simulation has revolutionized prototype design, providing powerful insights into fluid behavior around components.
By embracing this technology, engineers across various industries can develop products that are efficient, cost-effective, and high-performing.
As computational capabilities continue to advance, the potential of hydrodynamic simulations will only grow, offering exciting opportunities for innovation and discovery in design and engineering.
資料ダウンロード
QCD管理受発注クラウド「newji」は、受発注部門で必要なQCD管理全てを備えた、現場特化型兼クラウド型の今世紀最高の受発注管理システムとなります。
ユーザー登録
受発注業務の効率化だけでなく、システムを導入することで、コスト削減や製品・資材のステータス可視化のほか、属人化していた受発注情報の共有化による内部不正防止や統制にも役立ちます。
NEWJI DX
製造業に特化したデジタルトランスフォーメーション(DX)の実現を目指す請負開発型のコンサルティングサービスです。AI、iPaaS、および先端の技術を駆使して、製造プロセスの効率化、業務効率化、チームワーク強化、コスト削減、品質向上を実現します。このサービスは、製造業の課題を深く理解し、それに対する最適なデジタルソリューションを提供することで、企業が持続的な成長とイノベーションを達成できるようサポートします。
製造業ニュース解説
製造業、主に購買・調達部門にお勤めの方々に向けた情報を配信しております。
新任の方やベテランの方、管理職を対象とした幅広いコンテンツをご用意しております。
お問い合わせ
コストダウンが利益に直結する術だと理解していても、なかなか前に進めることができない状況。そんな時は、newjiのコストダウン自動化機能で大きく利益貢献しよう!
(β版非公開)