- お役立ち記事
- Practical use of parts manufacturing traceability system at the prototyping stage
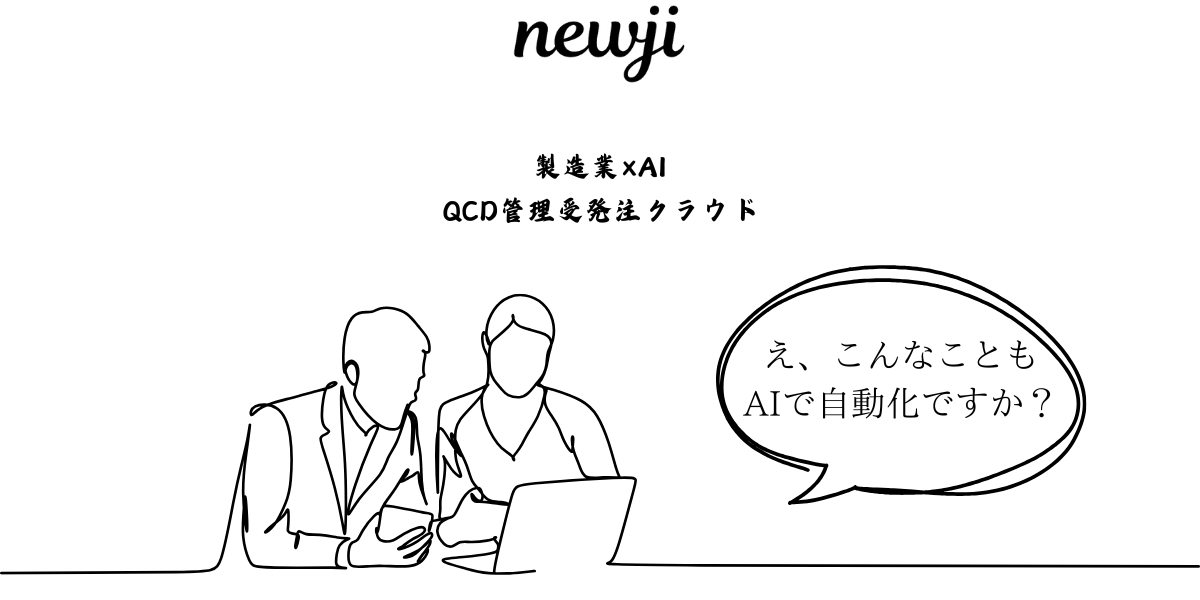
Practical use of parts manufacturing traceability system at the prototyping stage
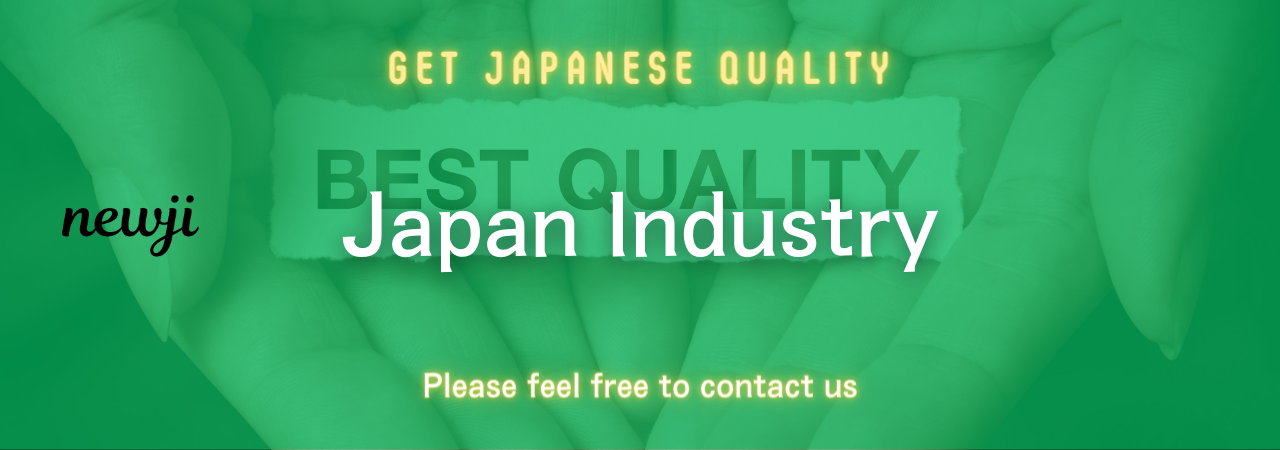
目次
Understanding Parts Manufacturing Traceability
In today’s rapidly evolving manufacturing landscape, keeping track of parts and components is essential.
This is where the concept of parts manufacturing traceability comes into play.
Traceability systems are designed to monitor and record the journey of a component from its raw material stage to its final product placement.
This is crucial in ensuring quality control, efficient inventory management, and compliance with regulations.
Why Traceability Matters in Prototyping
Prototyping is a critical phase in product development.
It is where ideas are transformed into tangible products for the first time.
During this stage, maintaining traceability of parts can lead to significant advantages.
Firstly, it allows manufacturers to track any defects or faults back to their origins.
This is vital for making improvements and adjustments to the prototype.
Additionally, traceability provides a comprehensive history of each part’s journey.
This becomes particularly crucial when dealing with complex products that include a multitude of components from various suppliers.
Benefits of a Traceability System
Implementing a traceability system in the prototyping stage offers numerous benefits.
Quality Control and Assurance
With a traceability system in place, manufacturers can ensure consistent quality across all prototypes.
Any discrepancies or deviations from the expected quality can be quickly identified and resolved, minimizing risks.
Enhanced Efficiency
Traceability aids in streamlining processes.
By efficiently tracking parts throughout their lifecycle, manufacturers can better estimate delivery times and resource allocation.
This results in reduced downtime and increased productivity.
Regulatory Compliance
Many industries are governed by strict regulations regarding the safety and quality of products.
A comprehensive traceability system supports compliance with these regulations by providing accurate records of a component’s history.
This is especially important for industries such as automotive, aerospace, and pharmaceuticals.
Implementing a Traceability System
Deploying a traceability system might initially seem daunting, but breaking it down into manageable steps can simplify the process.
Identify Components and Data Points
Start by identifying which components need to be tracked.
Then, determine the data points that are necessary for effective traceability.
These may include supplier details, manufacturing dates, and quality control checks.
Choose the Right Technology
There are several technologies available for implementing traceability systems.
Barcoding, RFID (Radio Frequency Identification), and IoT (Internet of Things) sensors are common options.
Selecting the right technology depends on your specific needs, scale of production, and budget.
Integrate with Existing Systems
Once you’ve selected a traceability technology, integrate it with your current manufacturing systems.
This ensures seamless data flow and easier access to traceability information.
Train Your Team
Training your staff is crucial for the successful adoption of a traceability system.
Ensure that everyone involved understands how to use the system effectively and the importance of maintaining accurate records.
Challenges and Solutions
While the advantages of a traceability system are clear, manufacturers may face certain challenges during implementation.
Data Overload
Collecting extensive data can lead to overload, making it difficult to extract meaningful insights.
To tackle this, focus on collecting key data points and use data management tools to organize and analyze information efficiently.
System Integration Issues
Integrating a new traceability system with existing processes may present challenges.
To mitigate this, work closely with your IT department or external experts to ensure compatibility and smooth integration.
Cost and Resources
The initial setup of a traceability system can be costly.
However, consider it an investment that will lead to long-term savings through improved efficiency and reduced waste.
Seek solutions that offer scalability so your system can grow with your manufacturing needs.
Future Trends in Traceability
As technology advances, so too will the capabilities of traceability systems.
Artificial intelligence and machine learning are expected to play significant roles in enhancing traceability.
These technologies offer predictive insights, helping manufacturers anticipate potential issues before they arise.
Blockchain is another emerging trend that promises to revolutionize traceability by providing an immutable and transparent ledger of a component’s journey.
This can increase trust and streamline audits.
Conclusion
The practical use of a parts manufacturing traceability system at the prototyping stage is a strategic decision that offers a competitive advantage.
From improving quality control to ensuring regulatory compliance, the benefits are substantial.
While challenges exist, careful planning and the right technology can help manufacturers overcome these hurdles and reap the rewards of a well-implemented traceability system.
資料ダウンロード
QCD調達購買管理クラウド「newji」は、調達購買部門で必要なQCD管理全てを備えた、現場特化型兼クラウド型の今世紀最高の購買管理システムとなります。
ユーザー登録
調達購買業務の効率化だけでなく、システムを導入することで、コスト削減や製品・資材のステータス可視化のほか、属人化していた購買情報の共有化による内部不正防止や統制にも役立ちます。
NEWJI DX
製造業に特化したデジタルトランスフォーメーション(DX)の実現を目指す請負開発型のコンサルティングサービスです。AI、iPaaS、および先端の技術を駆使して、製造プロセスの効率化、業務効率化、チームワーク強化、コスト削減、品質向上を実現します。このサービスは、製造業の課題を深く理解し、それに対する最適なデジタルソリューションを提供することで、企業が持続的な成長とイノベーションを達成できるようサポートします。
オンライン講座
製造業、主に購買・調達部門にお勤めの方々に向けた情報を配信しております。
新任の方やベテランの方、管理職を対象とした幅広いコンテンツをご用意しております。
お問い合わせ
コストダウンが利益に直結する術だと理解していても、なかなか前に進めることができない状況。そんな時は、newjiのコストダウン自動化機能で大きく利益貢献しよう!
(Β版非公開)