- お役立ち記事
- Strategy and optimal vendor selection for procuring materials and machinery in the semiconductor field
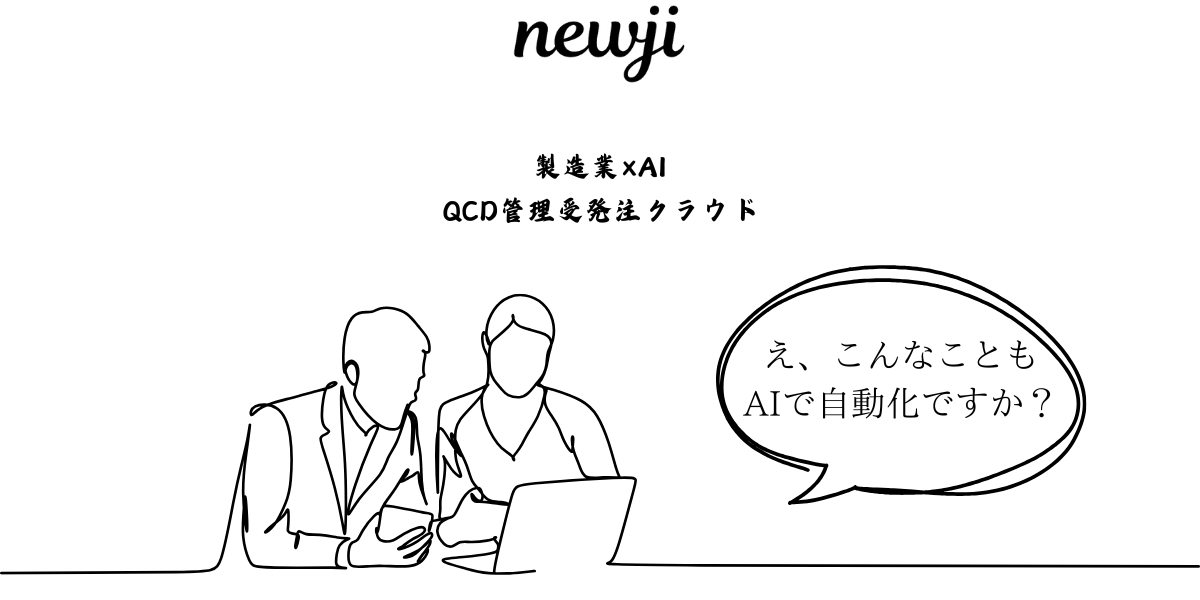
Strategy and optimal vendor selection for procuring materials and machinery in the semiconductor field
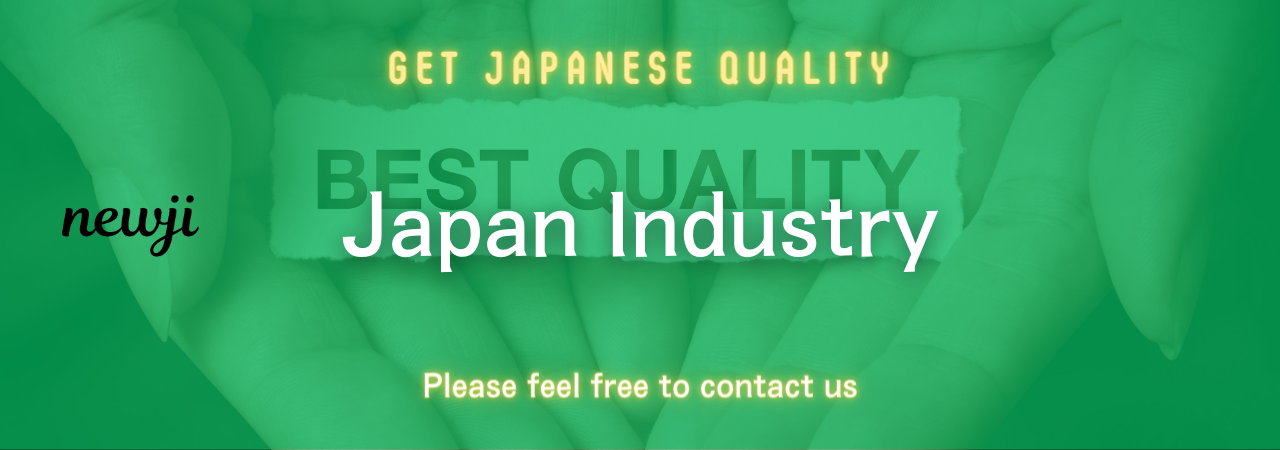
目次
Understanding the Importance of Vendor Selection
In the semiconductor field, procuring the right materials and machinery is crucial for maintaining efficient production processes and ensuring high-quality outputs.
The complexity of semiconductor manufacturing necessitates a careful strategy for choosing vendors who provide raw materials and machinery used in the production process.
Selecting the optimal vendor is more than just comparing prices.
It also involves assessing quality, reliability, service, and total cost of ownership.
By carefully evaluating vendors, companies can secure the best deals and maintain a competitive edge in the fast-evolving semiconductor industry.
Key Factors in Vendor Selection
When deciding on vendors, there are multiple factors that semiconductor companies must consider to ensure they are making the right choice.
Quality of Materials and Machinery
The quality of materials and machinery is paramount in the semiconductor field.
Inferior quality can lead to defects, reduced efficiency, and increased waste, all of which contribute to higher costs and potentially lower customer satisfaction.
Hence, selecting vendors who have a strong reputation for quality is essential.
Conduct thorough evaluations and inspections of material or machinery samples to assess their quality before making a decision.
Reliability and Consistency
Reliability in delivery and product consistency shape the backbone of successful vendor partnerships.
Evaluate a vendor’s track record in meeting delivery schedules, as delays can significantly impact production timelines and profitability.
Consistency in the quality of the supplied materials or machinery likewise ensures stable production conditions and helps mitigate risks associated with variability in inputs.
Cost Considerations
While cost should not be the sole factor in vendor selection, it is undeniably important.
A comprehensive cost analysis should include not just the purchase price, but also the total cost of ownership.
This includes maintenance expenses, energy consumption, and potential costs related to downtime or repairs.
Striking a balance between cost and quality will yield the best long-term value for semiconductor companies.
Strategic Approach to Vendor Selection
A strategic approach to vendor selection involves integrating various analytical methods and risk assessments to facilitate informed decision-making.
Vendor Evaluation and Rating
Develop a scoring model to evaluate and rate potential vendors based on key criteria, such as quality, cost, reliability, and service.
This model helps standardize the selection process and allows for objective comparison of vendors.
By weighting each criterion according to its importance to your specific manufacturing needs, you can better identify which vendors align most closely with your operational goals.
Building Long-term Partnerships
Establishing long-term partnerships with vendors can provide strategic advantages, such as better pricing, preferential treatment, and responsive service.
By fostering strong relationships, companies can work collaboratively with vendors to improve product development and address any supply chain challenges proactively.
These partnerships often lead to improved innovation and jointly developed solutions that cater specifically to the manufacturer’s needs.
Risk Management
Risk management is integral to vendor selection strategy.
Assess the risks associated with each vendor, including geopolitical stability, financial health, and dependency on single sources.
Diversifying your vendor base can reduce risks, while maintaining an active dialogue with vendors can help mitigate the impact of unforeseen disruptions.
Implementing an Effective Procurement Strategy
Implementing an effective procurement strategy involves a combination of careful planning, efficient execution, and continuous improvement.
Understanding Market Dynamics
Staying informed about market trends and technological advancements helps in making timely procurement decisions.
Understanding supply and demand dynamics, price fluctuations, and emerging technologies is essential for selecting vendors who are both current and future-ready.
Leverage industry reports and engage in networking activities to gain insights into market developments.
Continuous Process Improvement
Continuously examine and refine your procurement process.
Encourage feedback from production teams and vendors to identify areas for improvement and optimize supply chain efficiency.
By adopting Lean principles and technology tools, you can streamline procurement activities, reduce lead times, and enhance overall production performance.
Technology Integration
Integrate technology solutions such as procurement software and supply chain management tools.
These technologies improve procurement processes by automating routine tasks, enhancing transparency, and providing real-time data for better decision-making.
Furthermore, analytics tools can offer valuable insights, allowing companies to identify trends, predict future needs, and evaluate vendor performance accurately.
Conclusion
Selecting the optimal vendor for materials and machinery in the semiconductor field is a multifaceted endeavor that requires a strategic and comprehensive approach.
By considering key factors like quality, reliability, and cost, and by adopting a strategic, informed, and technology-driven procurement process, semiconductor companies can ensure they achieve optimal results.
Building strong vendor partnerships will not only ensure high-quality production but also position companies for long-term success in the competitive semiconductor market.
資料ダウンロード
QCD調達購買管理クラウド「newji」は、調達購買部門で必要なQCD管理全てを備えた、現場特化型兼クラウド型の今世紀最高の購買管理システムとなります。
ユーザー登録
調達購買業務の効率化だけでなく、システムを導入することで、コスト削減や製品・資材のステータス可視化のほか、属人化していた購買情報の共有化による内部不正防止や統制にも役立ちます。
NEWJI DX
製造業に特化したデジタルトランスフォーメーション(DX)の実現を目指す請負開発型のコンサルティングサービスです。AI、iPaaS、および先端の技術を駆使して、製造プロセスの効率化、業務効率化、チームワーク強化、コスト削減、品質向上を実現します。このサービスは、製造業の課題を深く理解し、それに対する最適なデジタルソリューションを提供することで、企業が持続的な成長とイノベーションを達成できるようサポートします。
オンライン講座
製造業、主に購買・調達部門にお勤めの方々に向けた情報を配信しております。
新任の方やベテランの方、管理職を対象とした幅広いコンテンツをご用意しております。
お問い合わせ
コストダウンが利益に直結する術だと理解していても、なかなか前に進めることができない状況。そんな時は、newjiのコストダウン自動化機能で大きく利益貢献しよう!
(Β版非公開)