- お役立ち記事
- Unlocking Success: How Japanese Manufacturing Thrives with Close-Up Improvement Strategies
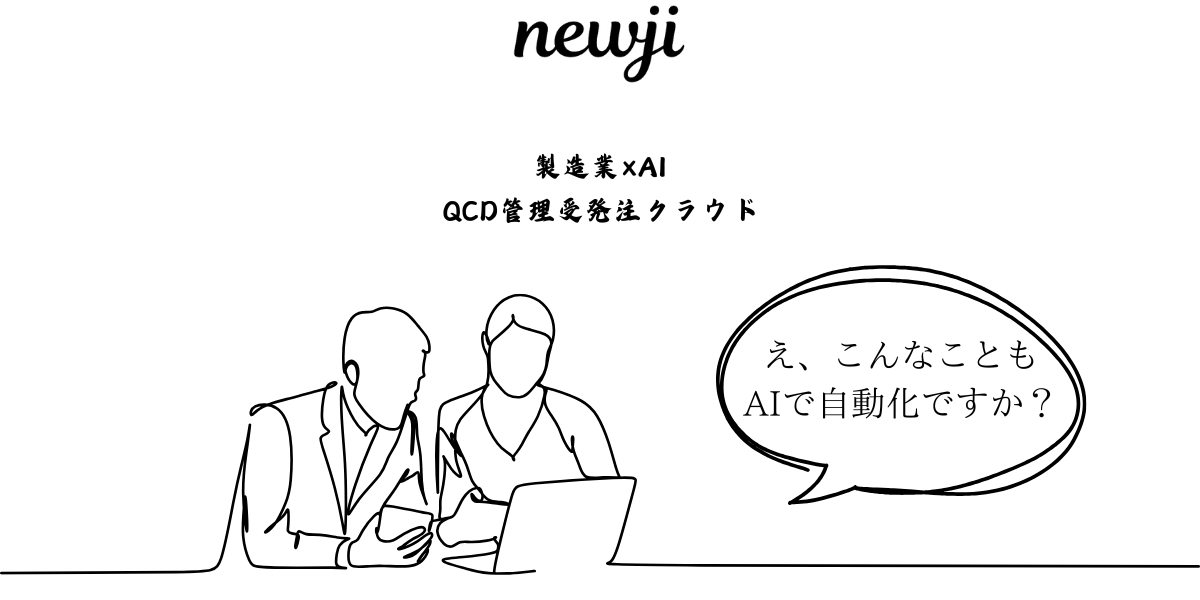
Unlocking Success: How Japanese Manufacturing Thrives with Close-Up Improvement Strategies
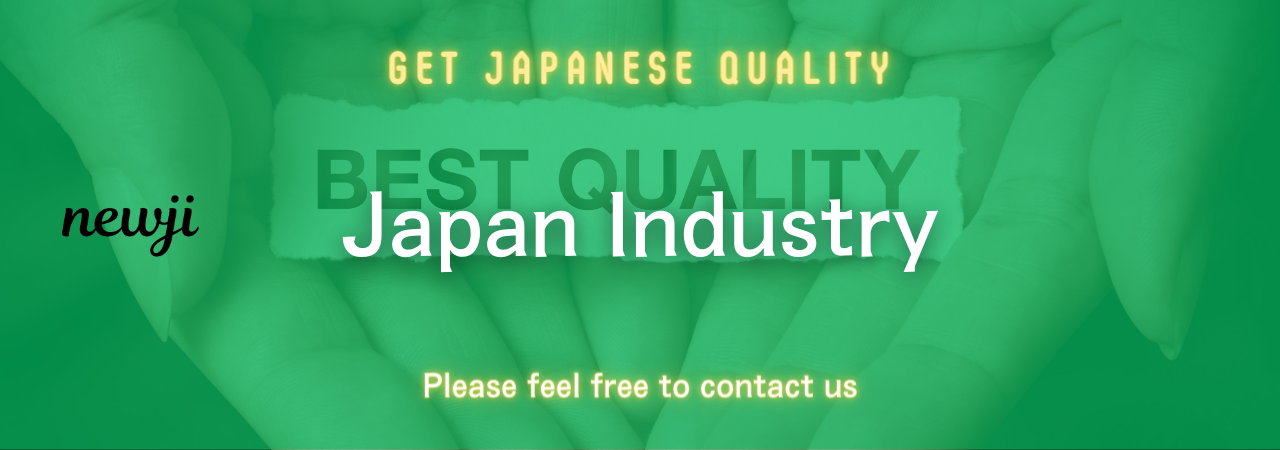
目次
Introduction to Japanese Manufacturing Excellence
Japanese manufacturing has long been synonymous with quality, efficiency, and innovation. This reputation is not a product of chance but the result of deliberate strategies focused on continuous improvement and meticulous attention to detail. In the competitive landscape of global manufacturing, Japanese companies have successfully navigated challenges by implementing close-up improvement strategies that enhance every facet of their operations. This article delves into the essence of these strategies, exploring their impact on procurement and purchasing, supplier negotiations, market conditions, and best practices that drive sustained success.
Understanding Close-Up Improvement Strategies
Close-up improvement, often associated with methodologies like Kaizen, involves making small, incremental changes continuously to improve processes. Unlike large-scale overhauls, close-up improvements focus on detailed, day-to-day enhancements that accumulate over time, leading to significant overall performance gains.
The Kaizen Philosophy
Kaizen, a Japanese term meaning “change for better,” embodies the spirit of close-up improvement. It encourages every employee, from top management to frontline workers, to identify areas for improvement and implement solutions. This collective effort fosters a culture of continuous advancement and responsiveness to change.
Lean Manufacturing Principles
Lean manufacturing complements close-up improvement by emphasizing waste reduction, efficiency, and value creation. By streamlining processes and eliminating non-value-added activities, Japanese manufacturers can optimize their operations, resulting in higher quality products and reduced costs.
Impact on Procurement and Purchasing
Effective procurement and purchasing are critical to the success of any manufacturing operation. Japanese close-up improvement strategies have a profound impact on these areas, ensuring that supply chains are robust, cost-effective, and aligned with the company’s quality standards.
Strategic Sourcing
Japanese companies prioritize strategic sourcing, identifying and partnering with suppliers who share their commitment to quality and innovation. This approach involves thorough market analysis and supplier assessments to ensure that the selected partners can meet the company’s stringent requirements.
Supplier Relationship Management
Building strong relationships with suppliers is a cornerstone of Japanese procurement practices. Regular communication, collaborative problem-solving, and mutual trust enable seamless integration of suppliers into the manufacturing process. This synergy ensures consistent quality and timely delivery of materials.
Cost Management
Close-up improvement strategies emphasize cost management without compromising quality. By continuously analyzing and optimizing procurement processes, Japanese manufacturers can reduce costs through efficient sourcing, bulk purchasing, and negotiating favorable terms with suppliers.
Advantages of Japanese Close-Up Improvement Strategies
The implementation of close-up improvement strategies offers numerous advantages that contribute to the sustained success of Japanese manufacturing.
Enhanced Quality Control
Continuous improvement ensures that quality control is maintained at every stage of the manufacturing process. By identifying and addressing potential issues early, Japanese companies can produce high-quality products that meet or exceed customer expectations.
Increased Efficiency
Incremental improvements streamline operations, reduce waste, and optimize resource utilization. This increased efficiency translates to faster production cycles, lower operational costs, and improved overall productivity.
Flexibility and Responsiveness
Japanese manufacturers can quickly adapt to changing market conditions and customer demands. The culture of continuous improvement fosters a proactive approach to problem-solving, enabling companies to respond swiftly to new challenges and opportunities.
Employee Engagement and Morale
Involving employees in the improvement process enhances their sense of ownership and responsibility. This engagement leads to higher morale, increased job satisfaction, and a motivated workforce committed to the company’s success.
Challenges and Disadvantages
While close-up improvement strategies offer significant benefits, they also present certain challenges that Japanese manufacturers must navigate to achieve optimal results.
Cultural Resistance
Implementing continuous improvement requires a cultural shift that may face resistance from employees accustomed to traditional ways of working. Overcoming this resistance involves consistent communication, training, and leadership commitment to foster a culture of change.
Initial Investment
Although close-up improvements focus on incremental changes, initial investments in training, process reengineering, and technology may be necessary. These upfront costs can be a barrier, especially for smaller companies with limited resources.
Maintaining Momentum
Sustaining the momentum of continuous improvement can be challenging. Companies must ensure that improvement initiatives remain a priority and that long-term commitment is maintained to prevent stagnation.
Balancing Standardization and Flexibility
While standardization is essential for quality and efficiency, too much rigidity can stifle innovation and flexibility. Japanese manufacturers must strike a balance between maintaining standardized processes and allowing room for creative problem-solving and adaptation.
Supplier Negotiation Techniques
Effective supplier negotiation is vital for securing favorable terms and ensuring a reliable supply chain. Japanese manufacturers employ specialized techniques that reflect their commitment to mutual benefit and long-term partnerships.
Win-Win Approach
Japanese negotiations focus on creating value for both parties. By understanding the supplier’s needs and constraints, manufacturers can develop agreements that benefit both sides, fostering trust and collaboration.
Long-Term Relationship Focus
Rather than seeking short-term gains, Japanese companies prioritize long-term relationships with suppliers. This approach encourages suppliers to invest in quality and reliability, knowing that a stable partnership is assured.
Information Sharing
Transparent communication and information sharing are key components of Japanese negotiation tactics. By openly discussing goals, challenges, and expectations, both parties can work towards solutions that satisfy mutual interests.
Problem-Solving Mindset
Japanese negotiators approach challenges with a problem-solving mindset, seeking creative solutions rather than adopting an adversarial stance. This cooperative approach helps overcome obstacles and find mutually acceptable outcomes.
Market Conditions and Adaptability
The ability to adapt to changing market conditions is crucial for maintaining a competitive edge. Japanese manufacturers leverage close-up improvement strategies to navigate dynamic environments and sustain growth.
Market Analysis and Forecasting
Continuous improvement involves regularly analyzing market trends and forecasting future demands. By staying informed about industry developments, Japanese companies can anticipate changes and adjust their strategies accordingly.
Innovation and R&D
Investment in research and development is integral to Japanese manufacturing excellence. By fostering innovation, companies can introduce new products, improve existing offerings, and stay ahead of competitors in a rapidly evolving market.
Supply Chain Resilience
Close-up improvement strategies enhance supply chain resilience by diversifying suppliers, optimizing logistics, and implementing risk management practices. This resilience ensures that manufacturers can maintain operations even in the face of disruptions.
Customer-Centric Approach
Japanese manufacturers prioritize understanding and meeting customer needs. By focusing on customer satisfaction, companies can tailor their products and services to better align with market demands, driving sales and loyalty.
Best Practices in Japanese Manufacturing
Adopting best practices from Japanese manufacturing can provide valuable insights and actionable strategies for companies aiming to enhance their own operations.
Just-In-Time (JIT) Manufacturing
JIT manufacturing minimizes inventory levels by synchronizing production schedules with demand. This practice reduces storage costs, minimizes waste, and ensures that resources are used efficiently.
Total Quality Management (TQM)
TQM emphasizes continuous quality improvement across all organizational processes. By integrating quality into every aspect of operations, Japanese manufacturers achieve consistent excellence and customer satisfaction.
5S Methodology
The 5S methodology—Sort, Set in order, Shine, Standardize, and Sustain—promotes workplace organization and efficiency. Implementing 5S helps maintain a clean, orderly, and productive work environment.
Continuous Training and Development
Investing in employee training and development ensures that the workforce remains skilled and knowledgeable. Continuous learning fosters a culture of innovation and adaptability, essential for sustained improvement.
Case Studies: Success Stories of Japanese Manufacturing
Examining real-world examples of Japanese manufacturing success illustrates the practical application of close-up improvement strategies and their impact on business outcomes.
Toyota Motor Corporation
Toyota is renowned for its Toyota Production System (TPS), which integrates lean manufacturing and Just-In-Time principles. TPS emphasizes waste reduction, continuous improvement, and employee involvement, setting the standard for manufacturing excellence worldwide.
Canon Inc.
Canon has leveraged close-up improvement strategies to excel in the imaging and optical products industry. Through meticulous quality control, innovation in product design, and strong supplier partnerships, Canon maintains its position as a market leader.
Panasonic Corporation
Panasonic’s commitment to continuous improvement and customer-centric innovation has enabled the company to thrive in the competitive electronics market. By focusing on product quality, operational efficiency, and sustainable practices, Panasonic continues to meet evolving consumer demands.
Implementing Close-Up Improvement in Your Organization
Adopting Japanese close-up improvement strategies requires a comprehensive approach that aligns with your organization’s goals and culture. Below are key steps to successfully implement these strategies.
Assess Current Processes
Begin by evaluating existing processes to identify areas for improvement. Use tools like value stream mapping and process flow analysis to understand workflows and pinpoint inefficiencies.
Foster a Culture of Continuous Improvement
Cultivate an organizational culture that values and encourages continuous improvement. Empower employees at all levels to contribute ideas and take ownership of improvement initiatives.
Set Clear, Achievable Goals
Define specific, measurable, attainable, relevant, and time-bound (SMART) goals for your improvement efforts. Clear objectives provide direction and enable progress tracking.
Provide Training and Resources
Equip your workforce with the necessary skills and knowledge to implement improvement strategies. Offer training programs, workshops, and resources that support ongoing development.
Implement Incremental Changes
Start with small, manageable changes that can be easily implemented and monitored. Incremental improvements reduce risk and make it easier to sustain long-term enhancements.
Monitor and Measure Progress
Regularly assess the impact of improvement initiatives through key performance indicators (KPIs) and metrics. Use data-driven insights to refine strategies and ensure continuous progress.
Encourage Collaboration and Communication
Promote open communication and collaboration across departments and with suppliers. Effective teamwork enhances problem-solving and fosters a unified approach to improvement.
Celebrate Successes
Recognize and celebrate achievements to reinforce the importance of continuous improvement. Celebrating successes boosts morale and motivates employees to maintain their commitment to excellence.
Conclusion
Japanese manufacturing’s sustained success is a testament to the power of close-up improvement strategies. By focusing on continuous, incremental enhancements, fostering strong supplier relationships, and maintaining a culture of quality and efficiency, Japanese companies have set a benchmark for excellence in the global marketplace. Adopting these strategies can help organizations across industries unlock their potential, achieve operational excellence, and thrive in an ever-evolving business environment.
資料ダウンロード
QCD調達購買管理クラウド「newji」は、調達購買部門で必要なQCD管理全てを備えた、現場特化型兼クラウド型の今世紀最高の購買管理システムとなります。
ユーザー登録
調達購買業務の効率化だけでなく、システムを導入することで、コスト削減や製品・資材のステータス可視化のほか、属人化していた購買情報の共有化による内部不正防止や統制にも役立ちます。
NEWJI DX
製造業に特化したデジタルトランスフォーメーション(DX)の実現を目指す請負開発型のコンサルティングサービスです。AI、iPaaS、および先端の技術を駆使して、製造プロセスの効率化、業務効率化、チームワーク強化、コスト削減、品質向上を実現します。このサービスは、製造業の課題を深く理解し、それに対する最適なデジタルソリューションを提供することで、企業が持続的な成長とイノベーションを達成できるようサポートします。
オンライン講座
製造業、主に購買・調達部門にお勤めの方々に向けた情報を配信しております。
新任の方やベテランの方、管理職を対象とした幅広いコンテンツをご用意しております。
お問い合わせ
コストダウンが利益に直結する術だと理解していても、なかなか前に進めることができない状況。そんな時は、newjiのコストダウン自動化機能で大きく利益貢献しよう!
(Β版非公開)