- お役立ち記事
- Structure and principles of permanent magnet synchronous motors, basics of vector control technology, and points of inverter design
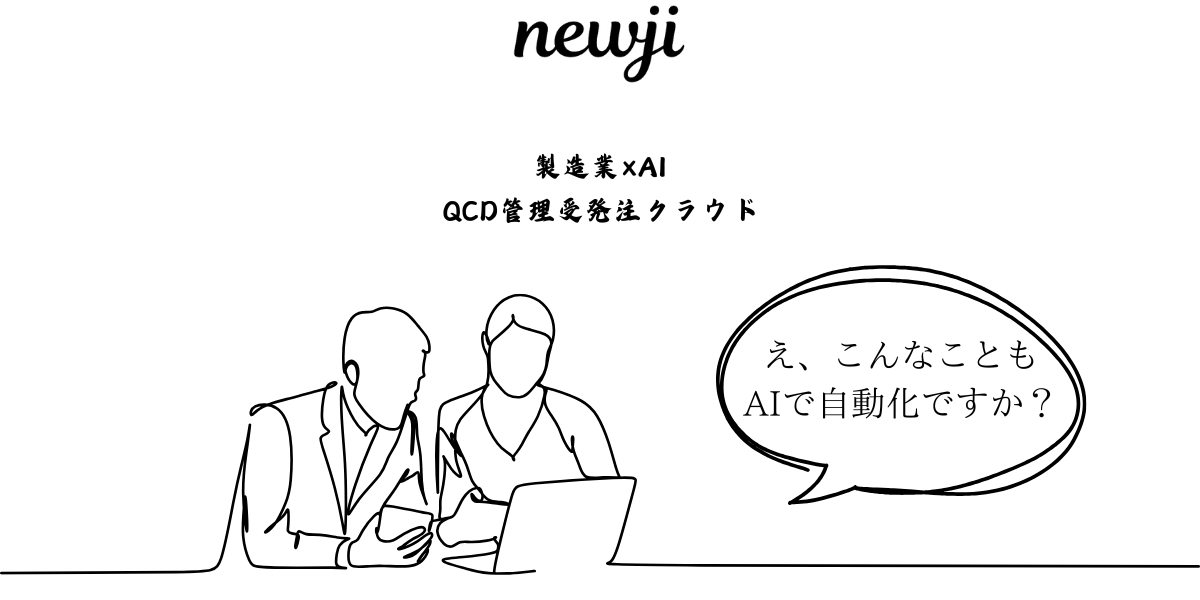
Structure and principles of permanent magnet synchronous motors, basics of vector control technology, and points of inverter design
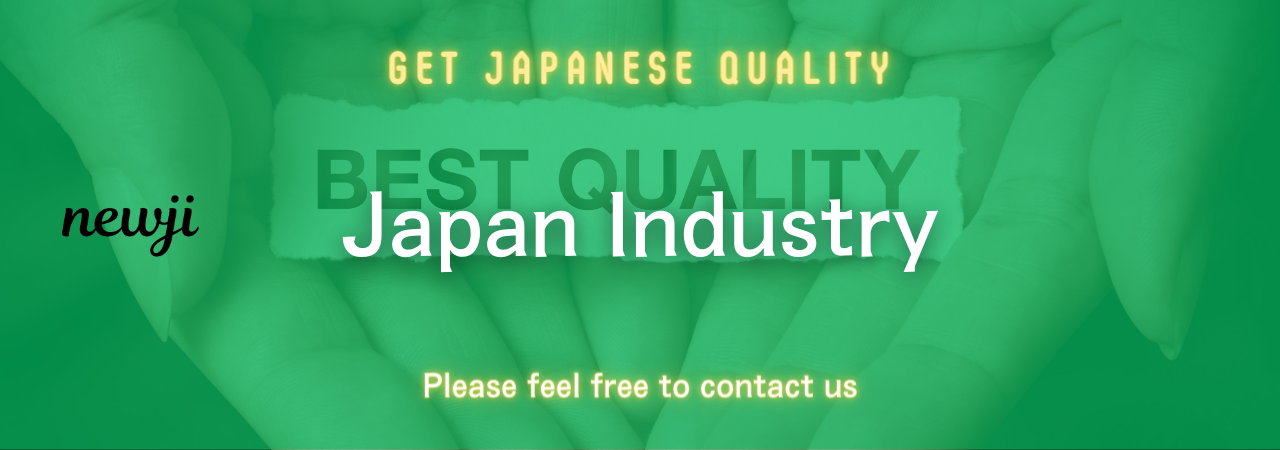
目次
Understanding Permanent Magnet Synchronous Motors
Permanent Magnet Synchronous Motors, often abbreviated as PMSMs, are a type of motor that has gained popularity due to their efficiency and performance in various applications.
These motors use permanent magnets embedded in the steel rotor to create a constant magnetic field.
This unique characteristic distinguishes them from other types of motors, such as induction motors or brushed DC motors.
Basic Structure of PMSMs
The main components of a PMSM include a stator, rotor, and housing.
– **Stator**: The stator is the stationary part of the motor, containing coils of wire wound in specific patterns to create a magnetic field when an electric current passes through.
– **Rotor**: The rotor is the rotating component where the permanent magnets are mounted.
– **Housing**: The housing keeps all components secure and offers protection from external factors.
The interaction between the stator’s electromagnetic field and the rotor’s magnetic field allows the motor to produce torque and rotational motion.
Operating Principles
PMSMs operate based on the principle of synchronism with the applied frequency.
When an AC supply is provided to the stator windings, a rotating magnetic field is produced.
The rotor, featuring permanent magnets, aligns with this rotating field, thereby rotating synchronously with the stator’s magnetic field.
Unlike induction motors, PMSMs do not suffer from slip because the rotor speed is locked with the stator field speed.
This synchronism results in high efficiency and precision, making PMSMs suitable for applications demanding constant speed or position control.
Basics of Vector Control Technology
Vector control, also known as field-oriented control (FOC), is a powerful method used to achieve precise control of PMSMs.
It decouples the control of torque and flux, making it easier to manage motor performance across wide ranges.
Key Components of Vector Control
The vector control system involves several essential elements:
1. **Reference Frame Transformation**: This involves transforming three-phase stator currents into a rotating reference frame, simplifying the analysis and control of motor performance.
2. **PI Controllers**: Proportional-Integral controllers manage the d-axis and q-axis current components, representing flux and torque respectively.
3. **Pulse Width Modulation (PWM)**: PWM is used to vary the voltage sent to the motor, influencing its speed and torque in a controlled manner.
Benefits of Vector Control
By implementing vector control, PMSMs can achieve superior performance, including:
– **Improved Torque Control**: Decoupling torque and flux leads to precise torque regulation.
– **Wide Speed Range**: Enhanced control over speed, especially useful in dynamic applications.
– **Efficiency**: Vector control optimizes performance, reducing energy consumption.
Vector control is instrumental in applications such as electric vehicles, robotics, and high-performance drives where precision and efficiency are paramount.
Designing Inverters for PMSMs
Inverters are critical components in controlling the operation of PMSMs by converting direct current (DC) into alternating current (AC).
The design of an inverter for a PMSM must consider several factors to ensure optimal performance and longevity.
Factors in Inverter Design
1. **Switching Frequency**: Selecting an appropriate switching frequency is vital to balance efficiency and performance.
Lower frequencies may result in less control finesse, while higher frequencies can increase heat and losses.
2. **Thermal Management**: Inverters generate heat, and efficient thermal management is crucial to prevent damage and ensure stability.
3. **Control Algorithms**: Implementing advanced control algorithms like vector control necessitates a high-performance digital signal processor (DSP) or microcontroller.
4. **EMI/EMC Considerations**: Electromagnetic interference and compliance with standards are critical to prevent disruptions and ensure smooth operation.
Common Challenges
Designing inverters also presents certain challenges:
– **Harmonics**: Minimizing harmonic distortion improves motor performance and reduces losses.
– **Protection Circuits**: Ensuring the inverter can handle overloads and short circuits without failure is paramount.
Points to Consider in Inverter Design
Successful inverter design requires careful planning and attention to:
– **Component Selection**: Choosing durable components that can withstand the demands of PMSMs is crucial.
– **Reliability Testing**: Rigorous testing under various conditions anticipates failure points and enhances reliability.
Through thoughtful consideration and engineering, efficient inverter designs empower PMSMs to deliver optimized performance in diverse applications.
In conclusion, the integration of permanent magnet synchronous motors with vector control technology through well-designed inverters offers significant advantages.
These range from enhanced efficiency and precision control to applicability across various industries, paving the way for future innovations in motor technology.
資料ダウンロード
QCD調達購買管理クラウド「newji」は、調達購買部門で必要なQCD管理全てを備えた、現場特化型兼クラウド型の今世紀最高の購買管理システムとなります。
ユーザー登録
調達購買業務の効率化だけでなく、システムを導入することで、コスト削減や製品・資材のステータス可視化のほか、属人化していた購買情報の共有化による内部不正防止や統制にも役立ちます。
NEWJI DX
製造業に特化したデジタルトランスフォーメーション(DX)の実現を目指す請負開発型のコンサルティングサービスです。AI、iPaaS、および先端の技術を駆使して、製造プロセスの効率化、業務効率化、チームワーク強化、コスト削減、品質向上を実現します。このサービスは、製造業の課題を深く理解し、それに対する最適なデジタルソリューションを提供することで、企業が持続的な成長とイノベーションを達成できるようサポートします。
オンライン講座
製造業、主に購買・調達部門にお勤めの方々に向けた情報を配信しております。
新任の方やベテランの方、管理職を対象とした幅広いコンテンツをご用意しております。
お問い合わせ
コストダウンが利益に直結する術だと理解していても、なかなか前に進めることができない状況。そんな時は、newjiのコストダウン自動化機能で大きく利益貢献しよう!
(Β版非公開)