- お役立ち記事
- Basics of BOM (Bill of Materials), how to use it, and key points for successful construction
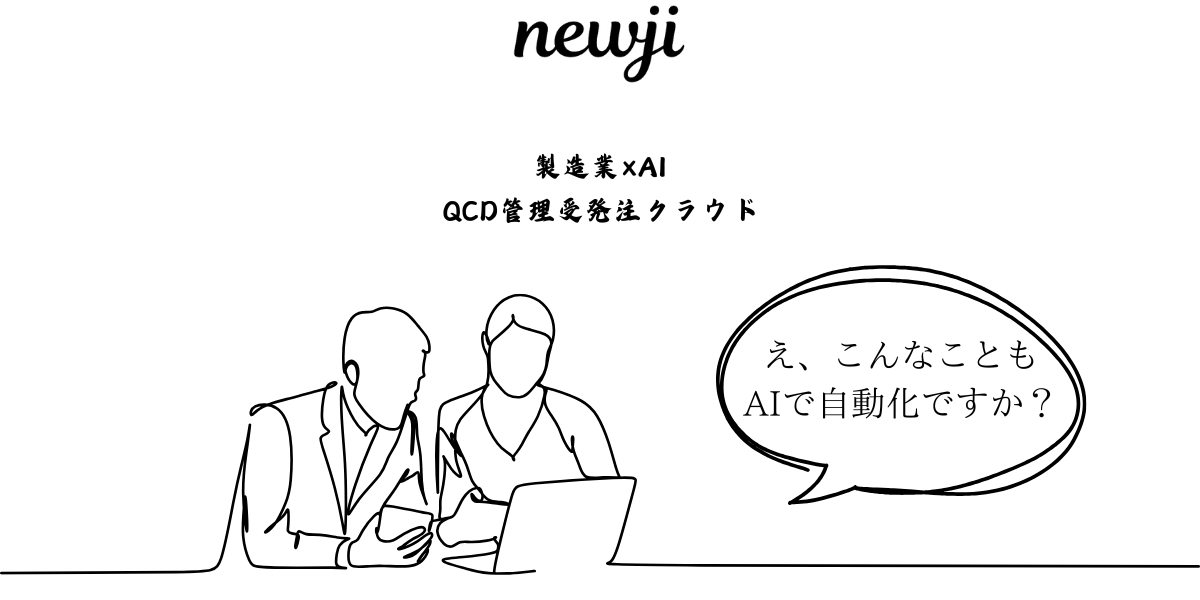
Basics of BOM (Bill of Materials), how to use it, and key points for successful construction
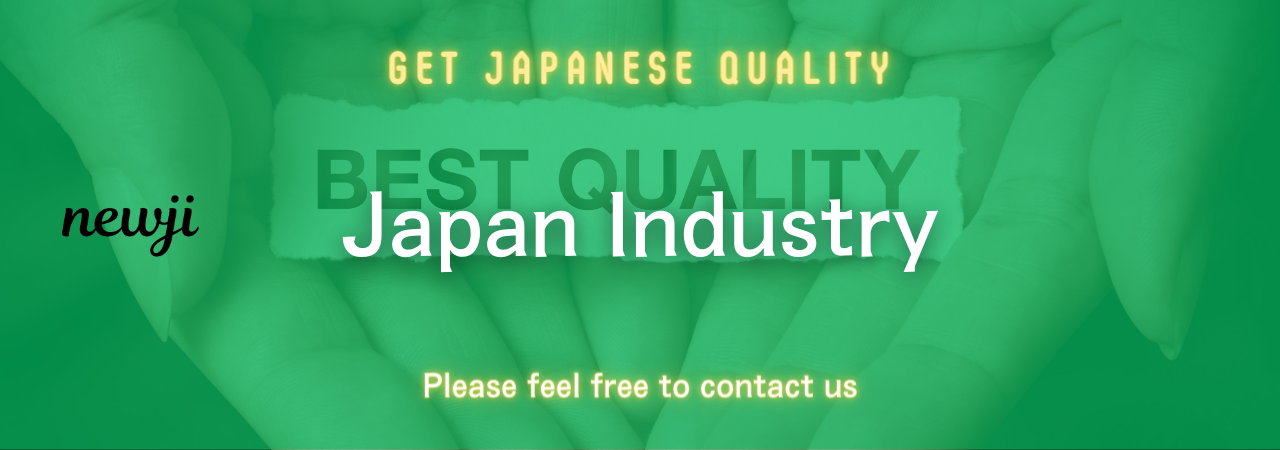
Understanding the Basics of BOM (Bill of Materials)
目次
What is a Bill of Materials (BOM)?
A Bill of Materials, commonly referred to as BOM, is a detailed list that outlines all the components, parts, and materials required to construct or manufacture a product.
Think of it as a recipe for a product, similar to a list of ingredients you need to prepare your favorite dish.
Each item in a BOM is crucial to ensure that the final product is assembled correctly and efficiently.
BOMs are used extensively across various industries, including manufacturing, engineering, and construction.
They serve as a guide, ensuring that all the necessary materials are available, and help streamline the production process.
Types of BOMs
There are different types of BOMs, each serving a unique purpose.
1. Engineering BOM
An Engineering BOM (EBOM) is often created by engineers during the product design phase.
It provides a detailed list of all the components, parts, and assemblies that are related to the design of a product.
EBOMs focus on the functional aspects and are mainly used to understand how a product is supposed to function.
2. Manufacturing BOM
The Manufacturing BOM (MBOM) offers a comprehensive view of all assemblies and components needed during the manufacturing process.
It includes packaging materials, sub-assemblies, and other essential items.
MBOMs are crucial for defining how a product will be both manufactured and assembled.
3. Service BOM
A Service BOM is used specifically for service and repair purposes.
It outlines the required spare parts and components needed to repair a product.
Service BOMs help ensure service technicians have the parts needed for maintenance or repair activities.
Key Components of a BOM
A well-structured BOM contains several vital elements that facilitate efficient production. Here are the main components:
1. Part Number
Each component in a BOM is assigned a unique part number, making it easy to identify and catalog items.
This aids in managing inventory and ensuring that there are no mix-ups in the production process.
2. Description
Descriptions provide detailed information about the components, such as their dimensions, material type, or other manufacturing specifications.
This detail helps ensure that the right parts are used in the assembly process.
3. Quantity
The quantity indicates how many units of each component are required for production.
Accurate quantities ensure that there is an adequate supply of parts to meet production needs without overstocking.
4. Unit of Measure
The unit of measure describes how the quantity is specified, whether it be in individual pieces, meters, liters, etc.
This ensures consistency across the production and inventory management processes.
5. BOM Level
BOM level designates the position of a part or assembly in the hierarchy of the BOM.
It often helps in understanding sub-assemblies and the structure of the product as a whole, especially when dealing with complex products.
How to Use a BOM Effectively
Using BOMs effectively requires understanding best practices and knowing how to leverage their full potential.
1. Maintain Updated BOMs
An up-to-date BOM is critical for successful product development and manufacturing.
Always update your BOMs to reflect any changes in product design, new components, or suppliers.
2. Incorporate Quality Checks
Quality checks ensure that the components listed in BOMs meet the necessary standards and specifications.
Incorporating quality checks at different stages of the manufacturing process can prevent costly errors and product recalls.
3. Use BOM Software
Utilizing BOM management software can significantly enhance efficiency.
These tools provide a centralized platform to manage and update BOMs, track changes, and ensure cross-functional collaboration.
They also integrate with other systems like ERP and PLM for seamless operations.
4. Collaborate Across Departments
Effective BOM management calls for collaboration between various teams, including engineering, procurement, and production.
Collaboration ensures that all stakeholders are on the same page and can prevent miscommunication and errors.
Key Points for Successful BOM Construction
Constructing a successful BOM requires attention to detail and strategic planning. Here are some key considerations:
1. Consistency in Naming Conventions
Adopt consistent naming conventions for parts and assemblies to reduce confusion and enhance clarity across the organization.
This will streamline communication and make it easier to refer to specific components.
2. Precisely Define Material Requirements
Accurately define material requirements to ensure the right materials are procured and available when needed.
Overspecifying or underspecifying can lead to inefficiencies, increased costs, or production delays.
3. Regular Audits and Revisions
Perform regular audits and revisions of BOMs to correct any errors and incorporate updates.
Periodic reviews help maintain accuracy and address any changes in design or supply chain dynamics.
4. Incorporate Supplier Information
Including supplier information can streamline the procurement process and ensure traceability of components.
Having supplier details at hand helps in managing supplier relationships and navigating supply chain disruptions effectively.
Understanding and leveraging the power of a Bill of Materials can greatly enhance the efficiency and accuracy of product development and manufacturing processes.
By mastering BOM creation and management techniques, businesses can ensure smoother production workflows, better inventory management, and improved communication across departments.
資料ダウンロード
QCD調達購買管理クラウド「newji」は、調達購買部門で必要なQCD管理全てを備えた、現場特化型兼クラウド型の今世紀最高の購買管理システムとなります。
ユーザー登録
調達購買業務の効率化だけでなく、システムを導入することで、コスト削減や製品・資材のステータス可視化のほか、属人化していた購買情報の共有化による内部不正防止や統制にも役立ちます。
NEWJI DX
製造業に特化したデジタルトランスフォーメーション(DX)の実現を目指す請負開発型のコンサルティングサービスです。AI、iPaaS、および先端の技術を駆使して、製造プロセスの効率化、業務効率化、チームワーク強化、コスト削減、品質向上を実現します。このサービスは、製造業の課題を深く理解し、それに対する最適なデジタルソリューションを提供することで、企業が持続的な成長とイノベーションを達成できるようサポートします。
オンライン講座
製造業、主に購買・調達部門にお勤めの方々に向けた情報を配信しております。
新任の方やベテランの方、管理職を対象とした幅広いコンテンツをご用意しております。
お問い合わせ
コストダウンが利益に直結する術だと理解していても、なかなか前に進めることができない状況。そんな時は、newjiのコストダウン自動化機能で大きく利益貢献しよう!
(Β版非公開)