- お役立ち記事
- Measures to improve production traceability in the prototyping process
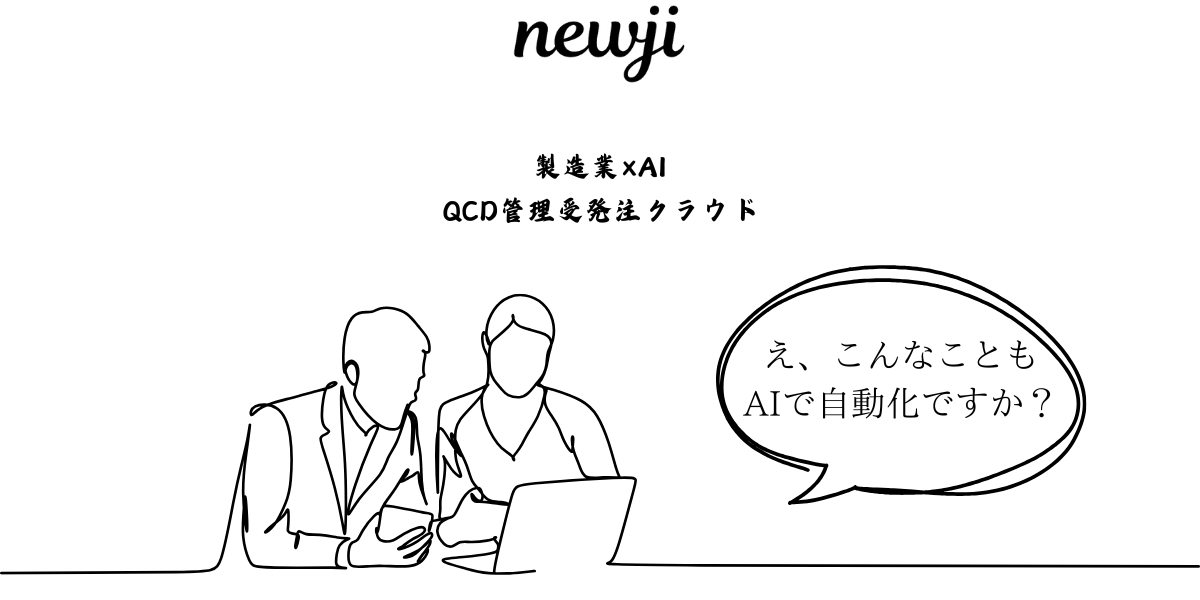
Measures to improve production traceability in the prototyping process
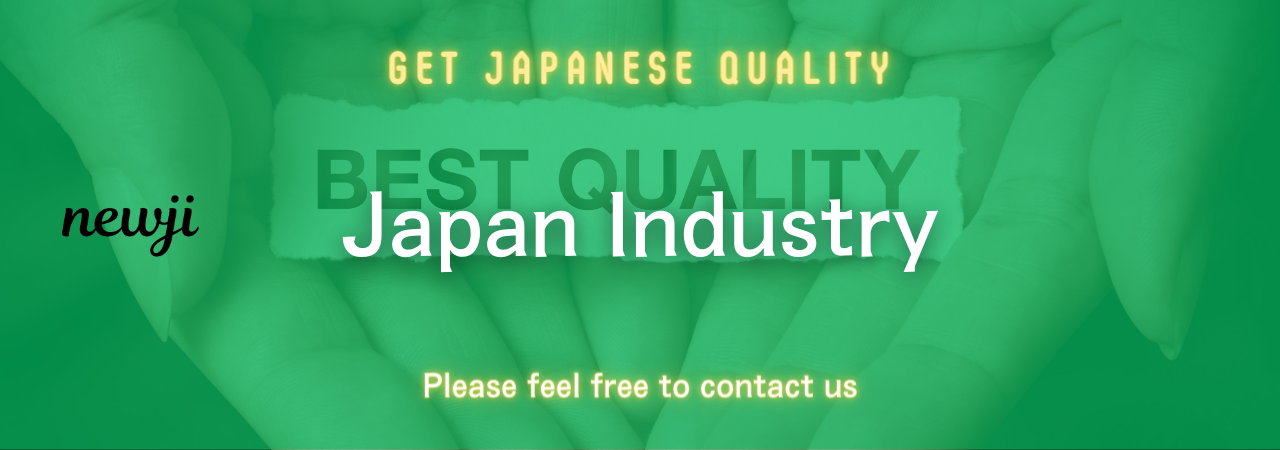
目次
Understanding Production Traceability
Production traceability refers to the ability to track and trace the history, location, and application of parts and products throughout the manufacturing process.
In the context of prototyping, ensuring traceability is crucial as it allows designers and manufacturers to monitor the evolution of a product from conception to completion.
Traceability enhances accountability, helps identify errors or issues in the manufacturing process, and improves the overall quality control of the prototype.
Prototyping serves as a critical stage in product development, where ideas transition from concepts to tangible forms.
The Importance of Traceability in Prototyping
Traceability in prototyping offers numerous benefits, which collectively contribute to a more efficient and reliable production process.
Firstly, it enables effective communication among all stakeholders involved, from designers to production teams.
Each party can access crucial information about the prototype stages, making collaboration seamless and reducing the chance for miscommunications.
Additionally, traceability allows for comprehensive documentation, enabling teams to keep records of materials used, processes applied, and any modifications made.
Such documentation is essential for identifying sources of defects or deviations from the intended design, which can save time and resources when troubleshooting.
Furthermore, having a robust traceability system enhances accountability.
Teams can easily pinpoint when and where a problem occurred and take corrective action to prevent future incidents.
This accountability fosters continuous improvement, which is key to achieving high-quality prototypes and, eventually, successful products.
Challenges in Establishing Traceability
While the benefits of traceability are numerous, establishing a solid traceability framework in the prototyping process can be challenging.
One significant hurdle is the integration of disparate systems across the production lifecycle.
Each stage, from design to assembly, might utilize different tools, software, or documentation methods, making it hard to create a cohesive overview.
Moreover, rapid changes in design and production are common in prototyping.
These changes, if not properly documented, can lead to discrepancies and a loss of traceability.
Additionally, the fast-paced nature of prototyping may result in teams overlooking the importance of detailed record-keeping, which can compromise the traceability system.
Lastly, the cost and resources required to establish a comprehensive traceability system can be significant, especially for smaller companies or teams with limited budgets.
Investing in appropriate technology and training personnel to properly implement and maintain the system can be a daunting task.
Key Steps to Improve Traceability in Prototyping
Despite these challenges, several measures can enhance production traceability in the prototyping process.
These steps involve careful planning and the strategic application of tools and technologies that ensure every stage of production is well documented and traceable.
1. Implementing Digital Tracking Systems
One of the most effective ways to ensure traceability is through digital tracking systems.
These systems allow for real-time data collection and analysis, providing insights into each part of the production process.
By utilizing technologies such as barcoding, RFID tags, or QR codes, manufacturers can track components and materials with precision.
Such technology enables easy access to the history and location of parts, which is essential for traceability.
2. Centralized Data Management
A centralized data management system is crucial for recording all the changes and updates made during the prototyping phase.
This system acts as a single source of truth, where all team members can input and access information seamlessly.
A centralized approach prevents data silos and ensures that everyone has the most accurate and up-to-date information.
3. Standardized Documentation Practices
Establishing standardized documentation practices guarantees that all necessary data is recorded, clear, and consistent.
Developing templates and guidelines for documentation helps team members understand what information is critical and how to record it effectively.
This practice ensures that documentation is comprehensive and easy to follow, facilitating traceability.
4. Training and Awareness Programs
Education and awareness are crucial elements of improving traceability.
Training programs and workshops can help team members understand the importance of traceability and how to effectively implement it in their daily operations.
When everyone understands their role in maintaining traceability, the overall process becomes more efficient and effective.
Leveraging Technology for Better Traceability
Modern technology offers numerous solutions that can be leveraged to improve traceability in the prototyping process.
Cloud-based platforms, for example, provide a flexible and scalable solution for data management and sharing.
These platforms enable remote teams to access information in real time, improving collaboration and efficiency.
Additionally, the integration of the Internet of Things (IoT) devices in the manufacturing process can further enhance traceability.
IoT devices can collect and transmit data from various parts of the production line, offering valuable insights into each stage.
This data can be used for predictive analysis, identifying potential bottlenecks or areas for improvement.
Continuous Improvement and Future Trends
Achieving optimal traceability in prototyping is not a one-time effort but a continuous process.
Regular audits and evaluations of the traceability system help identify areas for improvement and ensure that the system evolves with technological advancements and industry standards.
Adjustments and updates should be made as needed to keep the process effective.
Looking to the future, the incorporation of artificial intelligence (AI) and machine learning promises to further enhance traceability.
These technologies can automate data collection and analysis, offering predictive insights and identifying potential issues before they become critical.
In conclusion, while establishing traceability in the prototyping process presents challenges, it is essential for improving quality, accountability, and efficiency.
By leveraging digital tools, centralizing data management, standardizing documentation, and providing comprehensive training, manufacturers can significantly improve their production traceability efforts.
Embracing this continuous improvement mindset will not only enhance the prototyping process but also pave the way for innovative, high-quality products.
資料ダウンロード
QCD調達購買管理クラウド「newji」は、調達購買部門で必要なQCD管理全てを備えた、現場特化型兼クラウド型の今世紀最高の購買管理システムとなります。
ユーザー登録
調達購買業務の効率化だけでなく、システムを導入することで、コスト削減や製品・資材のステータス可視化のほか、属人化していた購買情報の共有化による内部不正防止や統制にも役立ちます。
NEWJI DX
製造業に特化したデジタルトランスフォーメーション(DX)の実現を目指す請負開発型のコンサルティングサービスです。AI、iPaaS、および先端の技術を駆使して、製造プロセスの効率化、業務効率化、チームワーク強化、コスト削減、品質向上を実現します。このサービスは、製造業の課題を深く理解し、それに対する最適なデジタルソリューションを提供することで、企業が持続的な成長とイノベーションを達成できるようサポートします。
オンライン講座
製造業、主に購買・調達部門にお勤めの方々に向けた情報を配信しております。
新任の方やベテランの方、管理職を対象とした幅広いコンテンツをご用意しております。
お問い合わせ
コストダウンが利益に直結する術だと理解していても、なかなか前に進めることができない状況。そんな時は、newjiのコストダウン自動化機能で大きく利益貢献しよう!
(Β版非公開)