- お役立ち記事
- Solder resist dispenser application prototype technology
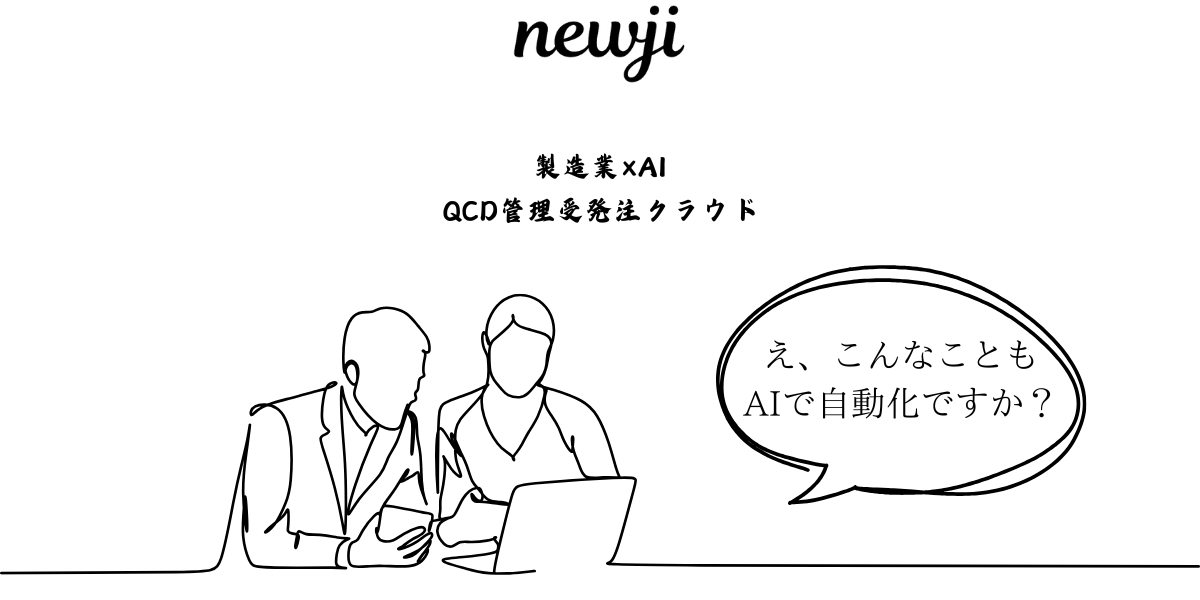
Solder resist dispenser application prototype technology
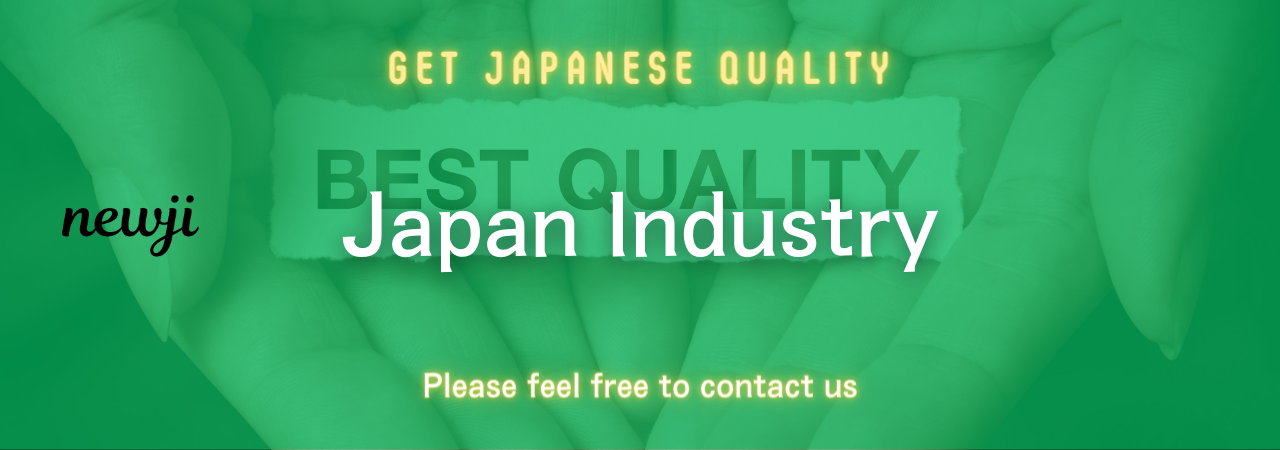
目次
What is Solder Resist?
Solder resist, also known as solder mask, is a crucial material in the manufacturing of printed circuit boards (PCBs).
It is a thin layer that is applied to the copper traces on a PCB to prevent solder from bridging between conductors during soldering.
Essentially, it acts as a protective film that ensures the integrity and functionality of electronic circuits.
Solder resist is typically green but can also come in other colors such as blue, red, or white.
The material offers a range of benefits, including protection against oxidation, prevention of short circuits, and improved aesthetic appearance.
Understanding the process of applying solder resist and the technology behind it is vital for anyone interested in electronics manufacturing.
How is Solder Resist Applied?
The application process of solder resist involves several steps to ensure uniformity and effectiveness.
The method includes cleaning the PCB surface, applying a layer of resist, and curing it to achieve the desired properties.
1. Cleaning the PCB
Before applying solder resist, it’s essential to clean the PCB thoroughly.
A clean surface ensures proper adhesion of the solder resist layer.
Any contaminants left on the surface can jeopardize the application, leading to defects or operational failures.
This cleaning process typically involves mechanical and chemical cleaning methods to ensure a spotless copper surface.
2. Coating with Solder Resist
Once clean, the PCB is coated with solder resist.
Several methods exist for solder resist application, including screen printing, curtain coating, and spray coating.
In screen printing, a fine mesh is used to apply the solder resist to specific areas of the board.
Curtain coating involves passing the PCB under a continuous curtain of solder resist to achieve an even layer.
Spray coating uses a spray gun to deposit the material, offering precise control over the thickness and coverage.
3. Curing the Solder Resist
After the application, the solder resist is cured to set it in place.
The curing process typically involves thermal or UV curing methods.
Thermal curing involves baking the PCB at a high temperature, while UV curing uses ultraviolet light to harden the material quickly.
The choice of curing method depends on the type of solder resist being used and the specific requirements of the PCB.
The Role of Dispensers in Solder Resist Application
Dispensers play a significant role in the application of solder resist, particularly in prototyping and small-scale production.
Dispensers offer precision and control, allowing for consistent application and minimizing the risk of human error.
1. Precision and Control
Solder resist dispensers are designed to provide accurate control over the amount of material being applied.
This precision is vital in ensuring that only the desired areas are covered, avoiding any unwanted coverage that could interfere with the PCB’s functions.
By using dispensers, manufacturers can fine-tune the application process, adjusting the speed, pressure, and volume of the solder resist as needed.
This customization is particularly useful during prototyping, where variations in design are common.
2. Versatility in Application
Dispensers offer versatility in the application of solder resist, adapting easily to various PCB sizes and designs.
This flexibility makes it easier for manufacturers to accommodate different prototypes without the need for extensive retooling or adjustments.
The ability to quickly change settings or use different nozzle sizes helps manufacturers meet specific project requirements efficiently.
As a result, dispensers facilitate faster turnaround times and enhance productivity in PCB fabrication.
3. Reduction of Waste
Using dispensers also contributes to reducing material waste during solder resist application.
By ensuring precise application, dispensers minimize excess material usage, leading to cost savings and minimizing environmental impact.
The precise control provided by dispensers means less material is used, and fewer mistakes are made.
This not only conserves resources but also helps in maintaining a sustainable manufacturing process.
Advancements in Solder Resist Dispenser Technology
The technology behind solder resist dispensers continues to evolve, driven by innovations aimed at improving efficiency and effectiveness.
Recent advancements have led to the development of more sophisticated dispensing systems, incorporating automation and smart technology.
1. Automated Dispensing Systems
Automation has transformed solder resist dispensers, making them more efficient and capable of handling high-volume production with minimal oversight.
Automated systems can operate continuously, reducing human intervention and the potential for errors.
These systems are equipped with advanced software that allows for precise control over the application process.
Features such as programmable patterns and automatic adjustment to environmental conditions ensure consistent results.
2. Smart Dispensing Technology
Smart technology is making its way into the world of solder resist dispensers, introducing features like real-time monitoring and feedback capabilities.
These features allow operators to track the application process and make adjustments on the fly, ensuring optimal results.
Smart dispensers can also integrate with other manufacturing systems, promoting seamless communication and coordination in the production line.
This connectivity leads to improved process efficiency and quality control.
3. Enhanced Applicator Design
The design of dispensers continues to evolve, focusing on improving ergonomics and ease of use.
Enhanced designs include user-friendly interfaces and interchangeable nozzles that facilitate quick changes and adjustments.
The improvements in applicator design contribute to reducing operator fatigue and increasing productivity.
Better ergonomics lead to more precise operation and ensure that the application process is efficient and effective.
Conclusion
Solder resist dispensers are an essential tool in the production of printed circuit boards, particularly in prototyping and small-scale manufacturing.
Their precision, versatility, and efficiency make them indispensable in the application of solder resist, contributing to the reliability and functionality of electronic products.
With ongoing advancements in dispenser technology, the future of solder resist application looks promising.
As automation and smart technology become more integrated into manufacturing processes, we can expect even greater gains in productivity and quality in PCB production.
Understanding the nuances of solder resist dispensers and their application can significantly enhance manufacturing processes, ensuring better outcomes and paving the way for innovative electronic solutions.
資料ダウンロード
QCD調達購買管理クラウド「newji」は、調達購買部門で必要なQCD管理全てを備えた、現場特化型兼クラウド型の今世紀最高の購買管理システムとなります。
ユーザー登録
調達購買業務の効率化だけでなく、システムを導入することで、コスト削減や製品・資材のステータス可視化のほか、属人化していた購買情報の共有化による内部不正防止や統制にも役立ちます。
NEWJI DX
製造業に特化したデジタルトランスフォーメーション(DX)の実現を目指す請負開発型のコンサルティングサービスです。AI、iPaaS、および先端の技術を駆使して、製造プロセスの効率化、業務効率化、チームワーク強化、コスト削減、品質向上を実現します。このサービスは、製造業の課題を深く理解し、それに対する最適なデジタルソリューションを提供することで、企業が持続的な成長とイノベーションを達成できるようサポートします。
オンライン講座
製造業、主に購買・調達部門にお勤めの方々に向けた情報を配信しております。
新任の方やベテランの方、管理職を対象とした幅広いコンテンツをご用意しております。
お問い合わせ
コストダウンが利益に直結する術だと理解していても、なかなか前に進めることができない状況。そんな時は、newjiのコストダウン自動化機能で大きく利益貢献しよう!
(Β版非公開)