- お役立ち記事
- How to use the technology of laminating PPS resin 100mm square plates by vibration welding
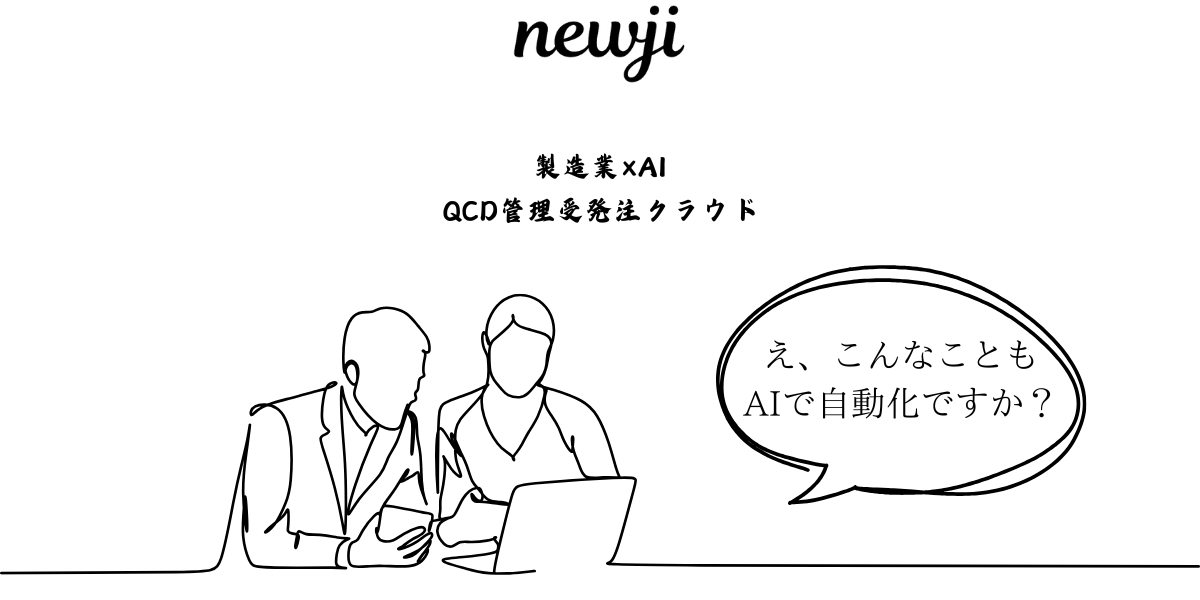
How to use the technology of laminating PPS resin 100mm square plates by vibration welding
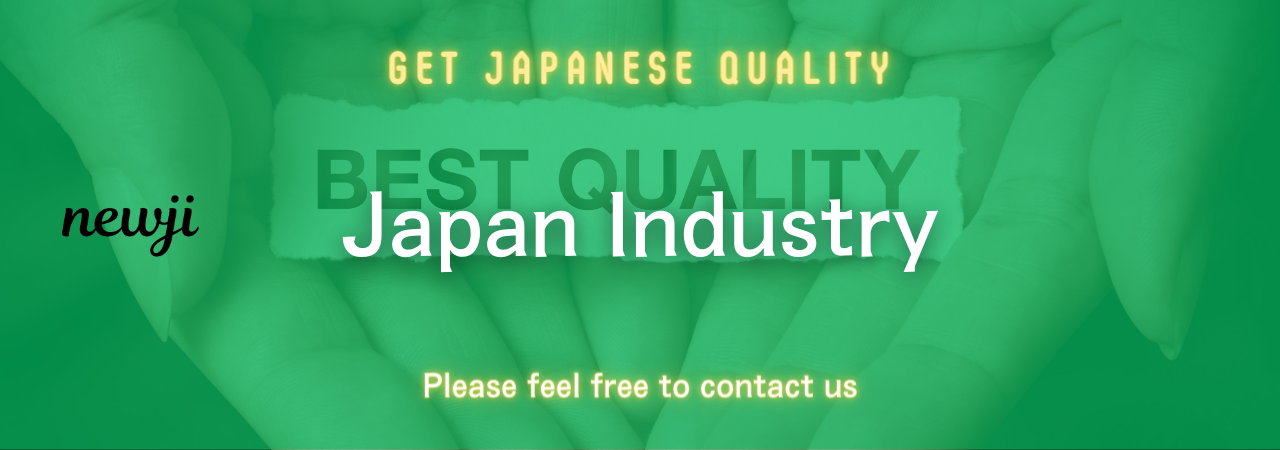
目次
Understanding Vibration Welding
Vibration welding is an advanced technology often used for joining thermoplastic materials.
This process involves placing two pieces of material together, applying pressure, and causing one part to vibrate.
The friction generated by these vibrations causes the materials to fuse together without the need for adhesives or external heat sources.
In the case of laminating PPS (polyphenylene sulfide) resin 100mm square plates, vibration welding is a favored method due to its precision and reliability.
PPS is a high-performance thermoplastic known for its toughness, chemical resistance, and ability to withstand high temperatures.
These physical traits make it an ideal candidate for use in various industrial and automotive applications.
By understanding the nuances of vibration welding, manufacturers can achieve optimal results when laminating these PPS plates.
Preparing for the Welding Process
Before beginning the vibration welding process, proper preparation is crucial.
First, ensure the PPS resin plates are clean and free of any contaminants.
Particles, dust, or grease on the surface can negatively impact the quality of the weld, leading to weak or inconsistent bonds between the plates.
Next, precisely align the 100mm square plates to ensure uniform distribution of pressure and vibration during the welding process.
Accurate alignment is critical because any deviation can result in an ineffective weld, which could compromise the integrity of the final product.
Determining the optimal weld parameters is also important.
This includes setting the appropriate frequency, amplitude, and pressure for the specific PPS resin being used.
These parameters can vary depending on the thickness of the plates, the type of PPS resin, and the final application requirements.
Consulting with a material specialist or referencing technical datasheets can provide valuable insights into these critical settings.
Executing the Vibration Welding Process
Once the preparation steps are completed, the actual vibration welding process can begin.
Place the aligned PPS plates in the vibration welder, ensuring they are secured firmly but not excessively clamped, which can alter the final weld quality.
The vibration welder generates vibrations that are transmitted through the plates.
Typically, a frequency ranging from 100 to 240 Hz is used for PPS resin, but fine-tuning may be required to achieve the best results.
The vibrational energy converts to heat at the interface of the plates, softening the material and allowing it to meld together.
Maintaining consistent pressure during this phase is essential.
Pressure ensures that the molten material between the plates flows to fill any voids and forms a strong, cohesive bond upon cooling.
Unsteady or inadequate pressure can lead to defects such as gaps or weak joins in the laminate.
Monitoring and Quality Control
Throughout the welding process, monitoring is key to ensuring successful lamination.
Equipment should be regularly checked to confirm that it operates at the correct parameters.
Any fluctuations in settings could affect the weld’s quality and may necessitate adjustments.
Perform visual inspections of the welds to detect any visual defects immediately.
Look for signs of porosity, uneven joins, or misalignment, as these can indicate areas of improvement.
For critical applications, additional non-destructive testing methods like ultrasonic inspection may be employed to assess bond integrity further.
Post-Welding Considerations
Once the vibration welding is complete, allow the laminated PPS plates to cool naturally.
This cooling phase is vital as it ensures the material solidifies, forming a strong and durable bond.
Premature handling or forced cooling can lead to warping or residual stresses within the material.
After cooling, clean the surface of the laminated plates if necessary to remove any debris that may have accumulated during the welding process.
This is particularly important if the laminated plates are to undergo further processing or assembly into larger components.
Optimizing the Welding Process
Continuous improvement efforts can help optimize the vibration welding process over time.
Review production results and feedback from quality control to identify areas where the process may be enhanced.
Factors such as reducing cycle time, minimizing material waste, and improving bond strength are all worthy of consideration.
Engaging with material suppliers or industry experts can also provide insights into the latest advancements and techniques that could be applied to your vibration welding procedures.
Staying informed about new technologies or materials can give your production processes a competitive edge.
Conclusion
Incorporating vibration welding for laminating PPS resin 100mm square plates offers numerous benefits, including high precision and strong adhesive-free bonds.
When properly executed, this technology ensures that the final laminated products maintain the desirable attributes of PPS while meeting application-specific requirements.
By adhering to thorough preparation, diligent process execution, and continuous optimization, manufacturers can leverage vibration welding to produce superior laminated components suited for a wide range of industries.
As technology advances, staying informed and adaptable will be key to maintaining efficiency and quality in the vibration welding process.
資料ダウンロード
QCD調達購買管理クラウド「newji」は、調達購買部門で必要なQCD管理全てを備えた、現場特化型兼クラウド型の今世紀最高の購買管理システムとなります。
ユーザー登録
調達購買業務の効率化だけでなく、システムを導入することで、コスト削減や製品・資材のステータス可視化のほか、属人化していた購買情報の共有化による内部不正防止や統制にも役立ちます。
NEWJI DX
製造業に特化したデジタルトランスフォーメーション(DX)の実現を目指す請負開発型のコンサルティングサービスです。AI、iPaaS、および先端の技術を駆使して、製造プロセスの効率化、業務効率化、チームワーク強化、コスト削減、品質向上を実現します。このサービスは、製造業の課題を深く理解し、それに対する最適なデジタルソリューションを提供することで、企業が持続的な成長とイノベーションを達成できるようサポートします。
オンライン講座
製造業、主に購買・調達部門にお勤めの方々に向けた情報を配信しております。
新任の方やベテランの方、管理職を対象とした幅広いコンテンツをご用意しております。
お問い合わせ
コストダウンが利益に直結する術だと理解していても、なかなか前に進めることができない状況。そんな時は、newjiのコストダウン自動化機能で大きく利益貢献しよう!
(Β版非公開)