- お役立ち記事
- Practical example of cost allocation and optimization at the prototyping stage
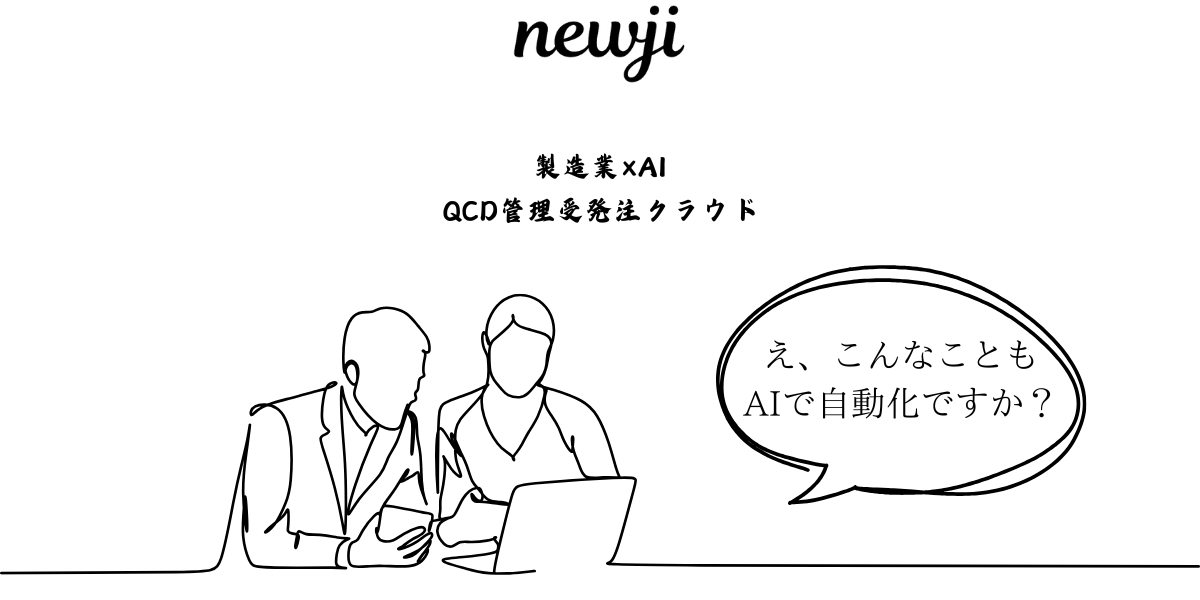
Practical example of cost allocation and optimization at the prototyping stage
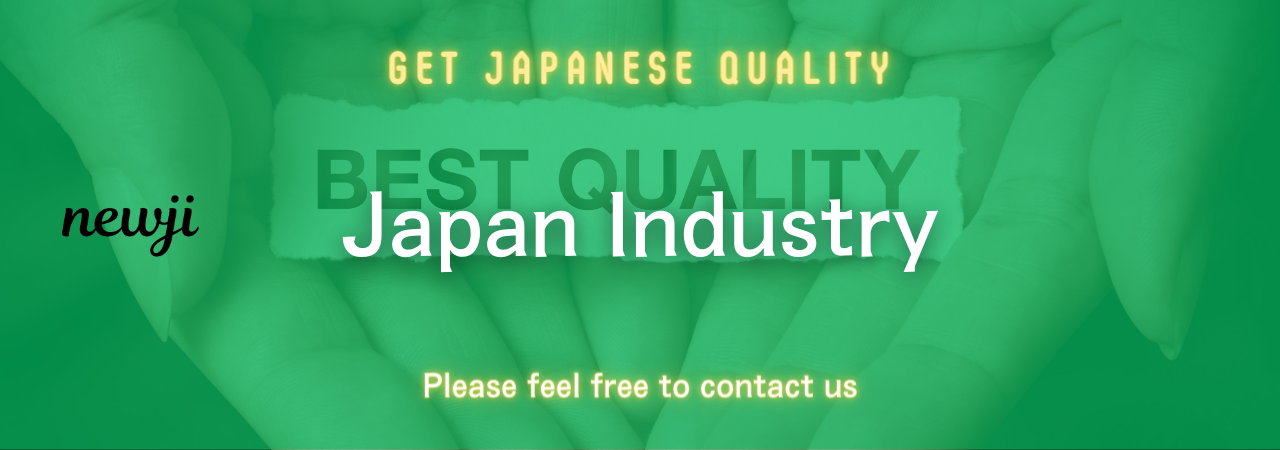
目次
Understanding Cost Allocation at the Prototyping Stage
When embarking on a new project, particularly in product development, managing costs effectively is crucial.
At the prototyping stage, strategic cost allocation helps ensure that resources are used efficiently and that projects remain financially viable.
The challenge lies in allocating these costs accurately and optimizing them for project success.
Cost allocation, in the context of prototyping, involves assigning the costs associated with developing a prototype to different components or activities.
This could include materials, labor, machinery, and overheads.
A clear understanding of these allocations is important because it directly impacts the company’s bottom line and strategic decision-making.
The Importance of Accurate Cost Allocation
Accurate cost allocation during prototyping provides numerous benefits.
Firstly, it aids in budgeting and forecasting, allowing management to make informed decisions about future projects.
Accurate data sheds light on which areas of the prototype are cost-intensive and which are more efficient.
Secondly, it provides a basis for setting realistic timelines.
Understanding the cost dynamics can inform how long a prototype should take to develop, allowing for better scheduling and resource allocation.
Thirdly, accurate cost allocation forms the foundation for pricing strategies.
Knowing the exact cost of prototyping helps with setting a price point for the final product that covers all expenses and drives profit.
Prototyping Cost Components
At the prototyping stage, several key components contribute to the overall cost.
Categorizing and understanding these components allows for meticulous management and optimization.
Material Costs
Material costs are a major expense during prototyping.
They include raw materials directly used in creating the prototype.
Selecting the appropriate materials, ensuring minimal waste, and looking for cost-effective alternatives are pivotal in managing these costs.
Labor Costs
Labor is another significant factor.
It encompasses the wages of the engineering team, designers, and any other personnel involved in the prototype’s assembly.
Optimizing labor costs involves ensuring that the team is not only adequately skilled but also efficiently utilized.
Machinery and Equipment
Machinery used in prototyping can often be expensive.
The costs associated with machinery include not only purchase or leasing expenses but also maintenance costs.
Effective scheduling of machinery use and considering outsourcing certain aspects are strategies to manage these expenses.
Overheads
Overheads include various indirect costs associated with prototyping.
These might be costs related to utilities, administrative expenses, or rent for the space used for the development.
While not directly tied to the prototype’s creation, they still need to be allocated accurately to understand the full cost picture.
Strategies for Cost Optimization
Cost optimization involves identifying areas where expenses can be reduced and efficiencies improved, without compromising the quality or progress of the prototype.
Efficient Resource Planning
By forecasting the resources required for a project, companies can reduce overspending.
Planning involves understanding resource load, availability, and the time each resource needs to complete their task.
Lean Prototyping
Lean prototyping emphasizes reducing waste and improving process efficiencies.
It involves a methodology that focuses on delivering just what’s needed for a given stage of product development, thus reducing overhead costs and preventing unnecessary work.
Utilizing Advanced Software Tools
The use of advanced planning and management software can streamline the entire prototyping process.
Such tools help in tracking progress, monitoring costs, and predicting future expenses.
They provide valuable insights and data that can be used to make quick, data-driven decisions.
Collaboration and Communication
Effective collaboration between departments involved in prototyping can ensure resources are allocated optimally.
Regular meetings and updates can also identify potential problems early, allowing for quick resolutions that minimize cost impacts.
Real-World Applications of Cost Allocation and Optimization
Companies across industries leverage cost allocation and optimization strategies to enhance their prototyping efforts.
For example, a tech firm developing a new gadget will focus on using software simulations to test prototypes before physical creation, saving on material and labor costs.
Similarly, automotive companies investing in electric vehicles are streamlining parts sourcing by switching to local suppliers to cut transportation costs, hence optimizing overall production even at the prototype level.
In the pharmaceutical industry, prototyping new drug formulas involves significant R&D expenditure.
By optimizing these costs through advanced biotechnology and data analysis tools, companies can reduce the time and expense associated with such innovations.
Conclusion: A Path to Successful Prototyping
Effective cost allocation and optimization at the prototyping stage are instrumental in any project’s success.
As products become increasingly complex and markets more competitive, these financial strategies become essential in ensuring that companies can deliver quality prototypes without exceeding their budgets.
By understanding the intricacies of cost components and employing thoughtful optimization strategies, businesses can transform their prototyping challenges into strategic advantages.
Ultimately, the ability to manage costs effectively not only aids in successful prototyping but also strengthens the foundation for launching successful products into the market.
資料ダウンロード
QCD調達購買管理クラウド「newji」は、調達購買部門で必要なQCD管理全てを備えた、現場特化型兼クラウド型の今世紀最高の購買管理システムとなります。
ユーザー登録
調達購買業務の効率化だけでなく、システムを導入することで、コスト削減や製品・資材のステータス可視化のほか、属人化していた購買情報の共有化による内部不正防止や統制にも役立ちます。
NEWJI DX
製造業に特化したデジタルトランスフォーメーション(DX)の実現を目指す請負開発型のコンサルティングサービスです。AI、iPaaS、および先端の技術を駆使して、製造プロセスの効率化、業務効率化、チームワーク強化、コスト削減、品質向上を実現します。このサービスは、製造業の課題を深く理解し、それに対する最適なデジタルソリューションを提供することで、企業が持続的な成長とイノベーションを達成できるようサポートします。
オンライン講座
製造業、主に購買・調達部門にお勤めの方々に向けた情報を配信しております。
新任の方やベテランの方、管理職を対象とした幅広いコンテンツをご用意しております。
お問い合わせ
コストダウンが利益に直結する術だと理解していても、なかなか前に進めることができない状況。そんな時は、newjiのコストダウン自動化機能で大きく利益貢献しよう!
(Β版非公開)