- お役立ち記事
- Importance of QMS and its Implementation Effectiveness: Quality Management System for Strengthening Quality Control System and Improving Product Quality
Importance of QMS and its Implementation Effectiveness: Quality Management System for Strengthening Quality Control System and Improving Product Quality
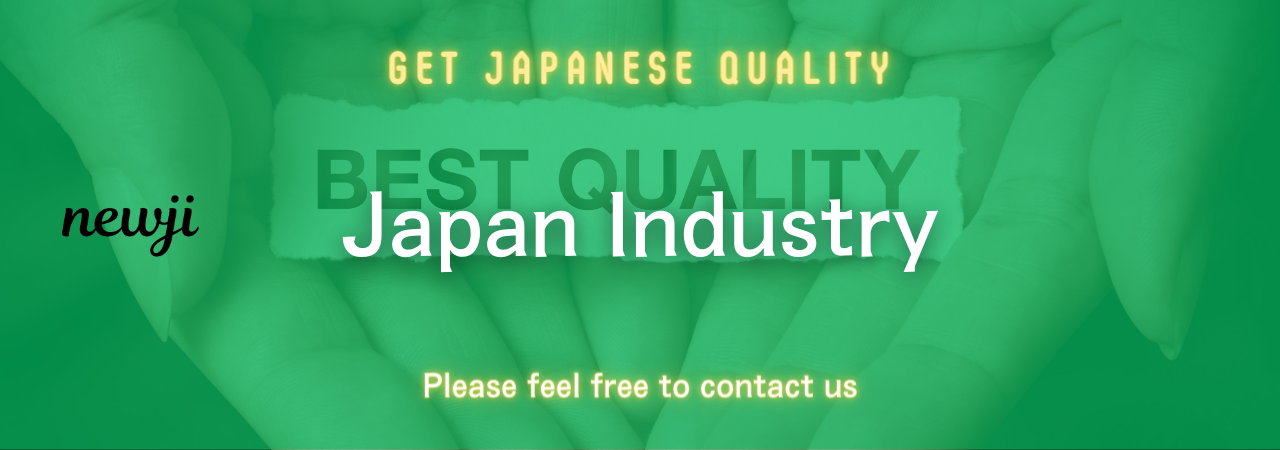
Implementing a Quality Management System (QMS) plays a pivotal role in enhancing the effectiveness of quality control and boosting product quality in any industry. Organizations that prioritize a strong QMS not only meet customer expectations but also gain competitive advantages in a dynamic market environment. The importance of QMS can’t be overstated, and its effective implementation can lead to significant improvements in process efficiency, risk management, and overall product quality.
A Quality Management System is a structured framework designed to oversee and manage the quality of products and services within an organization. This system encompasses all aspects of the production process, from initial design and development to final delivery and customer feedback. By establishing well-defined procedures, consistent documentation, and comprehensive monitoring, a QMS ensures that every output meets pre-determined quality standards.
One of the key benefits of implementing a QMS is the enhancement of quality control. Quality control refers to the techniques and activities used to fulfill quality requirements. Through a QMS, organizations can set specific criteria for product quality and systematically monitor compliance with these standards. This proactive approach helps identify discrepancies early in the process, allowing for timely corrective actions and preventing defective products from reaching consumers.
Moreover, a QMS boosts product quality by encouraging a culture of continuous improvement. By regularly evaluating processes and outcomes, organizations can pinpoint areas that require enhancement and adapt their practices accordingly. This iterative approach not only leads to more reliable products but also fosters innovation, as teams are constantly on the lookout for methods to optimize productivity and quality.
The effectiveness of QMS implementation hinges on several critical factors:
1. **Leadership Commitment**: Successful QMS implementation begins with strong leadership commitment. Top management must establish a clear vision and allocate necessary resources for the QMS. Their active involvement in quality initiatives demonstrates the importance of the system and motivates staff to embrace it.
2. **Employee Engagement**: Involving employees at all levels is crucial for effective QMS implementation. Staff should be well-informed about the QMS objectives, processes, and their roles within the system. Training programs can enhance their understanding and equip them with the skills needed to uphold quality standards.
3. **Documented Procedures**: Consistent documentation is a cornerstone of an effective QMS. Well-documented procedures provide a reference point for staff, ensuring that tasks are performed correctly and uniformly. This standardization minimizes variability, enhances efficiency, and facilitates compliance with regulatory requirements.
4. **Performance Measurement**: Regular monitoring and measurement of quality performance are essential for assessing the effectiveness of a QMS. Key performance indicators (KPIs) should be established to track progress and identify areas for improvement. Analyzing data from audits, inspections, and customer feedback helps refine processes and enhance product quality.
5. **Customer Focus**: A robust QMS prioritizes customer satisfaction. By understanding and addressing customer needs and expectations, organizations can tailor their products and services accordingly. Gathering feedback from customers and using it to drive improvements ensures that the end product aligns with market demands, ultimately enhancing customer loyalty and trust.
The successful implementation of QMS also involves integrating it seamlessly into the organization’s existing operations. This can be achieved through careful planning and phased implementation, where each stage is meticulously executed and evaluated. The main phases of QMS implementation are:
1. **Planning**: In the planning phase, the organization outlines the scope and objectives of the QMS. A comprehensive assessment of current processes and practices provides insights into areas requiring improvement. Setting clear goals and defining the roles and responsibilities of team members is essential for a structured implementation.
2. **Design and Development**: During this phase, the organization designs the framework for the QMS. This includes developing policies, procedures, and templates that align with quality objectives. Documenting the processes, control measures, and performance metrics helps create a blueprint for consistent quality management.
3. **Implementation**: The implementation phase involves rolling out the QMS across the organization. Training sessions and workshops ensure that employees understand the system and their contributions. Communication is key during this stage to address any concerns and promote acceptance among staff.
4. **Evaluation**: Once the QMS is in place, continuous evaluation is necessary to ensure its effectiveness. Regular audits and reviews help identify deviations and areas for improvement. Feedback loops encourage staff to share their experiences, providing valuable insights for refining the system.
5. **Improvement**: The final phase focuses on continuous improvement. Based on feedback and performance data, organizations can make informed adjustments to the QMS. This iterative approach helps address emerging challenges, incorporate new best practices, and maintain high-quality standards.
In conclusion, the importance of Quality Management Systems and their effective implementation cannot be overstated. A well-implemented QMS strengthens quality control processes, leading to improved product quality and customer satisfaction. Leadership commitment, employee engagement, documented procedures, performance measurement, and customer focus are pivotal factors influencing the success of QMS implementation. By following a systematic approach involving planning, design, development, implementation, evaluation, and improvement, organizations can establish a robust QMS that drives continuous quality enhancement and operational excellence.
資料ダウンロード
QCD調達購買管理クラウド「newji」は、調達購買部門で必要なQCD管理全てを備えた、現場特化型兼クラウド型の今世紀最高の購買管理システムとなります。
ユーザー登録
調達購買業務の効率化だけでなく、システムを導入することで、コスト削減や製品・資材のステータス可視化のほか、属人化していた購買情報の共有化による内部不正防止や統制にも役立ちます。
NEWJI DX
製造業に特化したデジタルトランスフォーメーション(DX)の実現を目指す請負開発型のコンサルティングサービスです。AI、iPaaS、および先端の技術を駆使して、製造プロセスの効率化、業務効率化、チームワーク強化、コスト削減、品質向上を実現します。このサービスは、製造業の課題を深く理解し、それに対する最適なデジタルソリューションを提供することで、企業が持続的な成長とイノベーションを達成できるようサポートします。
オンライン講座
製造業、主に購買・調達部門にお勤めの方々に向けた情報を配信しております。
新任の方やベテランの方、管理職を対象とした幅広いコンテンツをご用意しております。
お問い合わせ
コストダウンが利益に直結する術だと理解していても、なかなか前に進めることができない状況。そんな時は、newjiのコストダウン自動化機能で大きく利益貢献しよう!
(Β版非公開)