- お役立ち記事
- Unlocking Precision: The Role of 研磨機 (Grinders) in Japanese Manufacturing Excellence
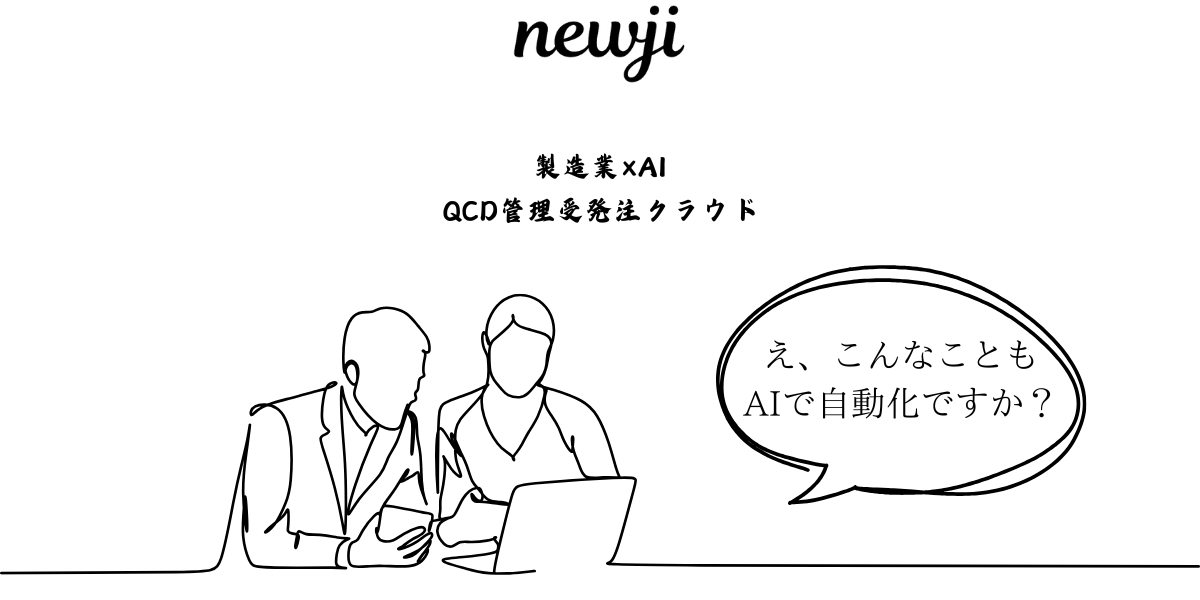
Unlocking Precision: The Role of 研磨機 (Grinders) in Japanese Manufacturing Excellence
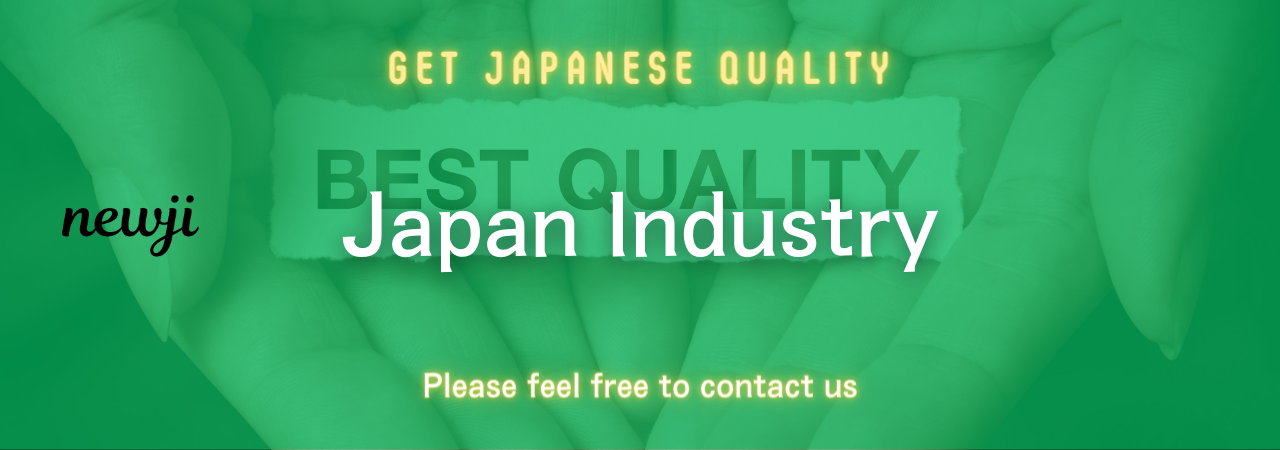
目次
Introduction to Grinders in Japanese Manufacturing
In the landscape of global manufacturing, Japan stands out for its dedication to precision and quality. A pivotal component contributing to this reputation is the use of **研磨機 (grinders)** in various manufacturing processes. Grinders are essential machines used to shape, finish, and refine materials to achieve the desired specifications. Their role in ensuring the excellence of Japanese manufacturing cannot be overstated. This article delves into the significance of grinders in Japanese manufacturing, exploring their advantages and disadvantages, procurement and purchasing strategies, supplier negotiation techniques, market conditions, and best practices.
The Importance of Grinders in Manufacturing Excellence
Grinders are fundamental in achieving high precision and surface finish in manufactured components. In Japanese manufacturing, where quality and precision are paramount, grinders play a crucial role in several aspects:
Precision and Accuracy
Japanese manufacturers prioritize precision engineering. Grinders enable the attainment of tight tolerances and smooth surface finishes, which are essential for high-performance components in industries such as automotive, aerospace, and electronics.
Material Versatility
Grinders can process a wide range of materials, including metals, ceramics, and composites. This versatility makes them indispensable in diverse manufacturing sectors, allowing manufacturers to produce components with varying material requirements.
Efficiency and Productivity
Advanced grinders equipped with automation and CNC (Computer Numerical Control) capabilities enhance production efficiency. Japanese manufacturers leverage these technologies to streamline operations, reduce production times, and maintain consistent quality levels.
Advantages of Utilizing Grinders in Japanese Manufacturing
Integrating grinders into manufacturing processes offers several advantages that align with the principles of Japanese manufacturing excellence.
Enhanced Surface Quality
Grinders provide superior surface finishes compared to other machining methods. This enhancement is critical for components that require minimal friction, improved wear resistance, or specific aesthetic qualities.
Improved Dimensional Accuracy
The precision of grinders ensures that components meet exact dimensional specifications. This accuracy is vital for parts that must fit seamlessly into larger assemblies without the need for extensive post-processing.
Increased Tool Life
Grinders can extend the life of cutting tools by reducing the wear and tear associated with other machining processes. This extension results in lower tool replacement costs and less downtime for tool maintenance.
Automation and Integration
Modern grinders can be easily integrated into automated manufacturing systems. This integration supports just-in-time production, reduces human error, and enhances overall factory efficiency.
Disadvantages and Challenges of Using Grinders
While grinders offer significant benefits, their implementation comes with certain challenges that manufacturers must address.
High Initial Investment
Advanced grinding machines, especially those with CNC capabilities, can be costly. The high upfront investment may be a barrier for smaller manufacturers or those looking to upgrade their existing equipment.
Complex Operation and Maintenance
Operating grinders requires specialized knowledge and training. Additionally, maintaining these machines to ensure optimal performance can be labor-intensive and demanding.
Energy Consumption
Grinders, particularly high-precision models, can consume substantial amounts of energy. Manufacturers must consider energy costs and sustainability when incorporating grinders into their operations.
Limitations on Material Thickness
Grinders are best suited for finishing operations and may have limitations when working with thick materials or requiring significant material removal. Manufacturers may need to supplement grinding with other machining processes to achieve desired results.
Procurement and Purchasing Strategies for Grinders
Effective procurement and purchasing strategies are essential for acquiring grinders that meet the specific needs of Japanese manufacturing operations. These strategies ensure that manufacturers obtain high-quality machines that align with their production requirements and budget constraints.
Identifying Requirements
Before initiating the procurement process, it is crucial to clearly define the requirements:
- Type of materials to be processed
- Desired precision and surface finish
- Production volume and capacity needs
- Automation and integration capabilities
- Budget and financial constraints
Supplier Evaluation and Selection
Selecting the right supplier involves assessing their capabilities, reputation, and reliability. Key factors include:
- Technical expertise and product range
- Quality certifications and compliance
- After-sales support and service offerings
- Customer reviews and references
- Pricing and payment terms
Quality Assurance and Standards
Ensuring that the grinders meet international quality standards is paramount. Manufacturers should verify that suppliers adhere to standards such as ISO 9001 and industry-specific certifications. Additionally, requesting product samples or conducting factory audits can provide insights into the supplier’s quality control processes.
Cost Management
Balancing cost with quality is a critical aspect of procurement. Manufacturers should conduct a total cost of ownership (TCO) analysis, considering not only the initial purchase price but also maintenance costs, energy consumption, and expected lifespan.
Supplier Negotiation Techniques
Negotiating with suppliers effectively can lead to favorable terms and conditions, enhancing the overall value of the procurement process.
Building Relationships
Establishing strong relationships with suppliers fosters trust and collaboration. Japanese business culture emphasizes long-term partnerships, which can lead to better negotiation outcomes and ongoing support.
Leveraging Volume and Commitment
Offering commitments for larger volumes or long-term purchases can provide leverage in negotiations. Suppliers may be more willing to offer discounts or favorable terms in exchange for guaranteed business.
Understanding Supplier Constraints
Gaining insight into the supplier’s cost structure, production capabilities, and market conditions enables more informed negotiations. Understanding their constraints allows for more realistic and mutually beneficial agreements.
Flexible Terms and Conditions
Negotiating flexible terms, such as payment schedules, warranty periods, and service agreements, can enhance the overall value proposition. Flexibility in these areas can mitigate risks and align the supplier’s offerings with the manufacturer’s operational needs.
Market Conditions for Grinders in Japan
The market for grinders in Japan is influenced by various factors, including technological advancements, economic trends, and global demand.
Technological Innovations
Continuous advancements in grinding technology, such as the integration of AI and IoT, are shaping the market. These innovations enhance machine capabilities, improve efficiency, and provide manufacturers with better data for process optimization.
Economic Factors
Economic stability and growth in Japan support investment in manufacturing equipment. However, fluctuations in the global economy can impact demand for Japanese-made grinders, influencing pricing and availability.
Global Competition
Japanese grinder manufacturers face competition from global players offering similar technologies. To maintain their market position, Japanese firms focus on innovation, quality, and customer service.
Supply Chain Dynamics
Global supply chain disruptions, such as those caused by geopolitical tensions or pandemics, can affect the availability of grinding machines. Japanese manufacturers must develop resilient supply chains to ensure consistent access to necessary equipment.
Best Practices for Procuring Grinders in Japanese Manufacturing
Adhering to best practices in procurement and purchasing can optimize the acquisition of grinders, ensuring alignment with manufacturing goals and operational efficiency.
Conducting Comprehensive Needs Assessment
A thorough needs assessment helps identify the specific requirements for grinders, ensuring that the selected machines align with production processes and quality standards.
Engaging in Strategic Sourcing
Strategic sourcing involves identifying and evaluating potential suppliers to select those that offer the best combination of quality, cost, and reliability. This approach minimizes risks and enhances procurement outcomes.
Implementing Effective Contract Management
Clear and well-defined contracts are essential to outline the terms of purchase, responsibilities, and expectations. Effective contract management ensures compliance and facilitates the resolution of any disputes.
Ensuring Continuous Improvement
Regularly reviewing and assessing the performance of grinders and suppliers allows manufacturers to identify areas for improvement. Implementing feedback loops and fostering a culture of continuous improvement contribute to long-term manufacturing excellence.
Investing in Training and Development
Providing training for staff on the operation and maintenance of grinders ensures that the equipment is used effectively and maintained properly. Skilled personnel can maximize the benefits of advanced grinding technology.
Case Studies: Successful Integration of Grinders in Japanese Manufacturing
Examining real-world examples of Japanese manufacturers successfully integrating grinders illuminates best practices and strategies that others can emulate.
Case Study 1: Automotive Component Manufacturing
A leading automotive parts manufacturer integrated high-precision grinders into their production line to produce engine components with exacting tolerances. By investing in CNC grinders, the company reduced production times by 20% and increased component accuracy, resulting in fewer defects and higher customer satisfaction.
Case Study 2: Aerospace Industry Applications
An aerospace manufacturer employed advanced grinding technology to produce turbine blades with intricate geometries and surface finishes. The implementation of automated grinders enhanced production efficiency and ensured compliance with stringent industry standards, contributing to the company’s reputation for reliability and quality.
Case Study 3: Electronics Manufacturing
A Japanese electronics company utilized specialized grinders to achieve the necessary surface finishes for microelectronics components. The precision provided by the grinders was critical in enabling the company to meet the high-performance requirements of their products, leading to increased market competitiveness.
Future Trends in Grinding Technology
The future of grinding technology in Japanese manufacturing is poised for significant advancements, driven by emerging trends and evolving industry demands.
Integration of Artificial Intelligence
AI is set to revolutionize grinding processes by enabling predictive maintenance, optimizing grinding parameters, and enhancing process control. These capabilities will further improve efficiency and reduce downtime.
Advancements in Materials and Coatings
Innovations in grinding wheel materials and coatings will enhance the performance and lifespan of grinders. These advancements will allow for improved material removal rates and better adaptability to different workpiece materials.
Enhanced Automation and Robotics
The continued integration of automation and robotics in grinding operations will lead to higher precision, increased production rates, and reduced labor costs. Automated systems will also facilitate real-time monitoring and quality control.
Sustainability and Energy Efficiency
As environmental concerns grow, there is a push towards more energy-efficient grinding technologies. Future grinders are expected to incorporate energy-saving features and sustainable materials, aligning with global sustainability initiatives.
Conclusion
Grinders are integral to the fabric of Japanese manufacturing excellence, underpinning the precision, quality, and efficiency that define the industry. By understanding the advantages and challenges of grinders, implementing strategic procurement and purchasing practices, and staying abreast of market conditions and technological advancements, manufacturers can harness the full potential of grinding technology. Embracing best practices and fostering strong supplier relationships further ensure that grinders contribute effectively to the sustained success and global competitiveness of Japanese manufacturing operations.
資料ダウンロード
QCD調達購買管理クラウド「newji」は、調達購買部門で必要なQCD管理全てを備えた、現場特化型兼クラウド型の今世紀最高の購買管理システムとなります。
ユーザー登録
調達購買業務の効率化だけでなく、システムを導入することで、コスト削減や製品・資材のステータス可視化のほか、属人化していた購買情報の共有化による内部不正防止や統制にも役立ちます。
NEWJI DX
製造業に特化したデジタルトランスフォーメーション(DX)の実現を目指す請負開発型のコンサルティングサービスです。AI、iPaaS、および先端の技術を駆使して、製造プロセスの効率化、業務効率化、チームワーク強化、コスト削減、品質向上を実現します。このサービスは、製造業の課題を深く理解し、それに対する最適なデジタルソリューションを提供することで、企業が持続的な成長とイノベーションを達成できるようサポートします。
オンライン講座
製造業、主に購買・調達部門にお勤めの方々に向けた情報を配信しております。
新任の方やベテランの方、管理職を対象とした幅広いコンテンツをご用意しております。
お問い合わせ
コストダウンが利益に直結する術だと理解していても、なかなか前に進めることができない状況。そんな時は、newjiのコストダウン自動化機能で大きく利益貢献しよう!
(Β版非公開)