- お役立ち記事
- Approach for successful outsourcing of maintenance work for valve drive devices and other equipment
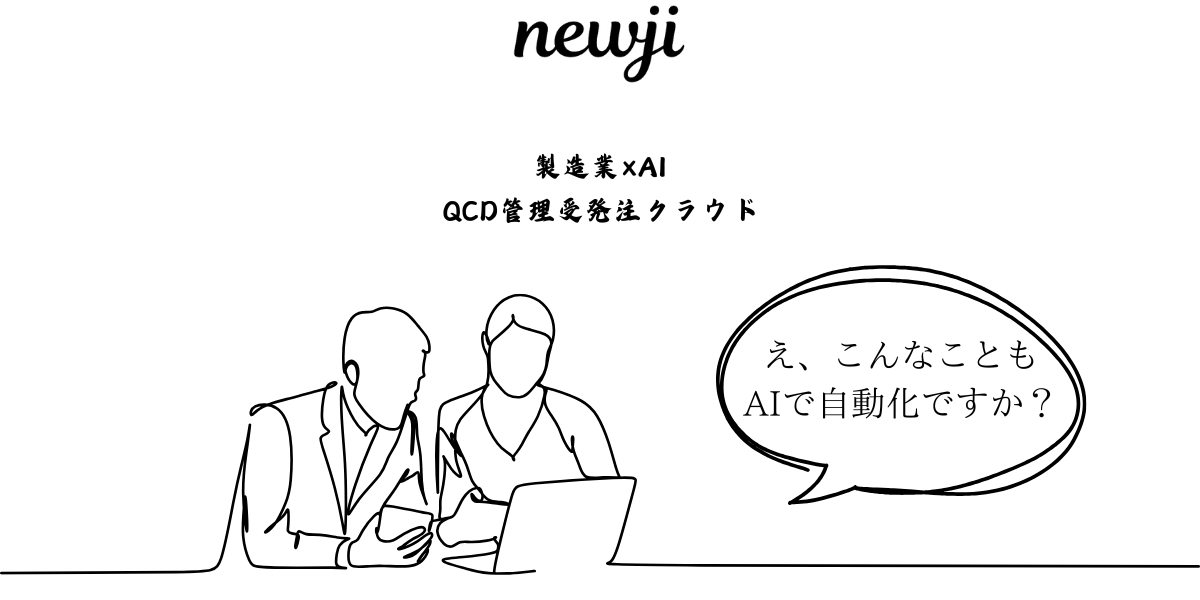
Approach for successful outsourcing of maintenance work for valve drive devices and other equipment
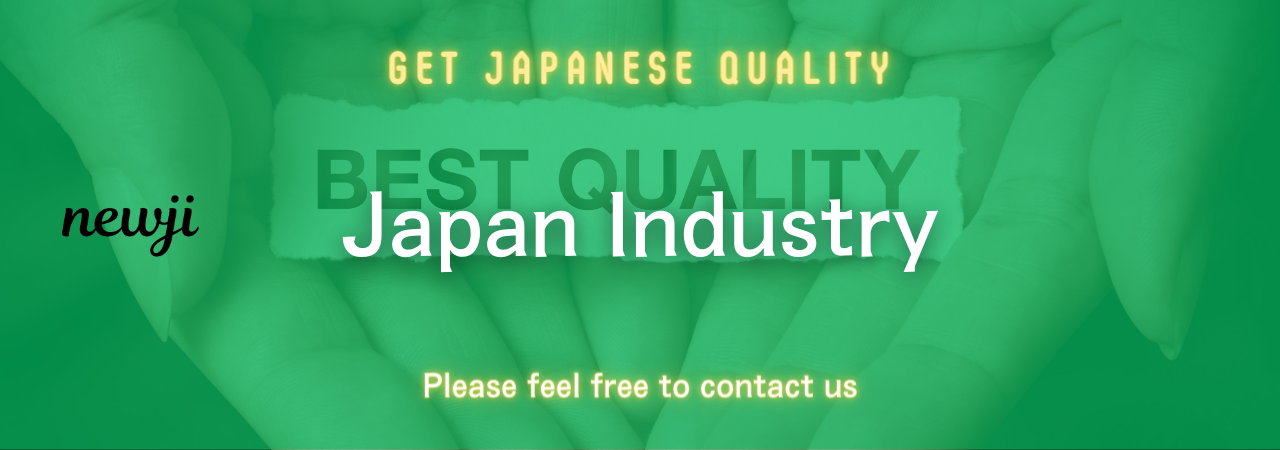
目次
Understanding the Basics of Outsourcing
Outsourcing can be an effective way to handle valve drive devices and other equipment maintenance work.
It involves hiring external organizations to perform tasks that might otherwise be executed internally.
The primary goal is to streamline operations, reduce costs, and leverage specialized expertise.
For businesses managing multiple types of machinery, outsourcing maintenance tasks can be an efficient strategy.
With the right outsourcing partner, companies can ensure that their equipment operates smoothly without the burden of maintaining an in-house team for every specialized task.
Identifying the Right Reasons to Outsource
Before deciding to outsource maintenance work, businesses must identify the specific reasons behind their decision.
Common reasons include cost reduction, lack of internal expertise, or the need for more scalable operations.
Consider if the current maintenance processes are meeting the expectations concerning efficiency and cost-effectiveness.
If your internal team lacks expertise with certain technical equipment, outsourcing may fill the gaps.
It can often save costs associated with recruitment, training, and maintaining specialist staff.
Choosing the Right Outsourcing Partner
Once the decision to outsource is made, the next step is selecting the right partner.
The selection process should be methodical and thorough to ensure quality and reliability.
Assess Expertise and Experience
It is crucial to evaluate the expertise and experience of potential outsourcing partners.
Look for firms with a proven track record in maintaining valve drive devices and similar equipment.
Examine case studies or client testimonials to understand their capabilities and success stories.
Additionally, check if they have handled equipment similar to what your business operates.
Doing so ensures that they are well-versed in the specific needs and challenges related to the machinery.
Verify Credentials and Certifications
Ensure that the potential partner possesses the necessary certifications and credentials, which are vital in maintenance work.
These certifications often indicate a level of commitment to quality and standards compliance.
They can also provide assurance that the partner is updated on the latest industry practices and technologies.
Evaluate Communication and Support
Effective communication is the bedrock of successful outsourcing relationships.
Assess the responsiveness and support provided by the outsourcing partner.
Determine if they have a dedicated support team ready to handle queries or emergencies at all times.
Regular updates and feedback sessions should be part of their service offerings to keep you informed about the maintenance work progress.
Establishing Clear Contracts and SLAs
To ensure a smooth outsourcing relationship, it’s crucial to establish clear contracts and Service Level Agreements (SLAs).
These documents set the foundation for expectations, deliverables, and responsibilities.
Define Scope and Objectives
Clearly outline the scope of the outsourced maintenance work and set specific objectives.
This clarity helps in avoiding any ambiguities and ensures that both parties have a mutual understanding of the task at hand.
Specify the types of maintenance services required, whether it’s routine checks, emergency repairs, or comprehensive overhauls.
The more detailed the scope, the less room there is for misunderstandings.
Set Performance Metrics
Incorporate performance metrics into the contract to measure the outsourcing partner’s effectiveness.
Metrics might include equipment downtime, response time for repairs, and overall maintenance costs.
These key performance indicators (KPIs) will serve as benchmarks to evaluate the success of the maintenance services provided.
Include Contingency Plans
Every outsourcing agreement should have contingency plans for unforeseen circumstances.
These could involve alternative arrangements if the primary outsourcing partner fails to deliver as expected.
Planning for contingencies ensures that maintenance work can continue without major disruptions.
Monitoring and Managing the Outsourcing Relationship
After selecting an outsourcing partner and setting up contracts, it is essential to continuously monitor and manage the relationship.
Regular Performance Reviews
Conduct regular performance reviews to assess if the maintenance work aligns with the agreed-upon KPIs and objectives.
These reviews offer opportunities to provide feedback, address concerns, and make necessary adjustments.
Ensure open lines of communication during these reviews to foster a collaborative and transparent partnership.
Foster an Ongoing Partnership
Successful outsourcing relationships thrive on building long-term partnerships rather than short-term transactions.
Cultivate an environment that encourages mutual growth and understanding.
Regularly engage with the outsourcing partner and involve them in strategic discussions about equipment maintenance and innovations.
By doing so, both parties can work together towards continuous improvement.
The Benefits of Successful Outsourcing
When executed correctly, outsourcing maintenance work can bring various benefits.
These include cost savings, access to specialized skills, improved focus on core business functions, and enhanced maintenance quality.
By partnering with experts, businesses can reduce operational risks associated with equipment failure.
It also accelerates the time-to-solution for complex maintenance issues, keeping the business operation smooth and effective.
Ultimately, successful outsourcing requires careful planning, selecting the right partner, and maintaining an open, collaborative relationship.
When these elements are addressed properly, outsourcing can be a powerful tool to maintain your equipment with efficiency and expertise.
資料ダウンロード
QCD調達購買管理クラウド「newji」は、調達購買部門で必要なQCD管理全てを備えた、現場特化型兼クラウド型の今世紀最高の購買管理システムとなります。
ユーザー登録
調達購買業務の効率化だけでなく、システムを導入することで、コスト削減や製品・資材のステータス可視化のほか、属人化していた購買情報の共有化による内部不正防止や統制にも役立ちます。
NEWJI DX
製造業に特化したデジタルトランスフォーメーション(DX)の実現を目指す請負開発型のコンサルティングサービスです。AI、iPaaS、および先端の技術を駆使して、製造プロセスの効率化、業務効率化、チームワーク強化、コスト削減、品質向上を実現します。このサービスは、製造業の課題を深く理解し、それに対する最適なデジタルソリューションを提供することで、企業が持続的な成長とイノベーションを達成できるようサポートします。
オンライン講座
製造業、主に購買・調達部門にお勤めの方々に向けた情報を配信しております。
新任の方やベテランの方、管理職を対象とした幅広いコンテンツをご用意しております。
お問い合わせ
コストダウンが利益に直結する術だと理解していても、なかなか前に進めることができない状況。そんな時は、newjiのコストダウン自動化機能で大きく利益貢献しよう!
(Β版非公開)